- お役立ち記事
- For production engineers in the filter cartridge manufacturing industry for medical device manufacturing! Balancing precision filtration and chemical resistance
月間76,176名の
製造業ご担当者様が閲覧しています*
*2025年3月31日現在のGoogle Analyticsのデータより
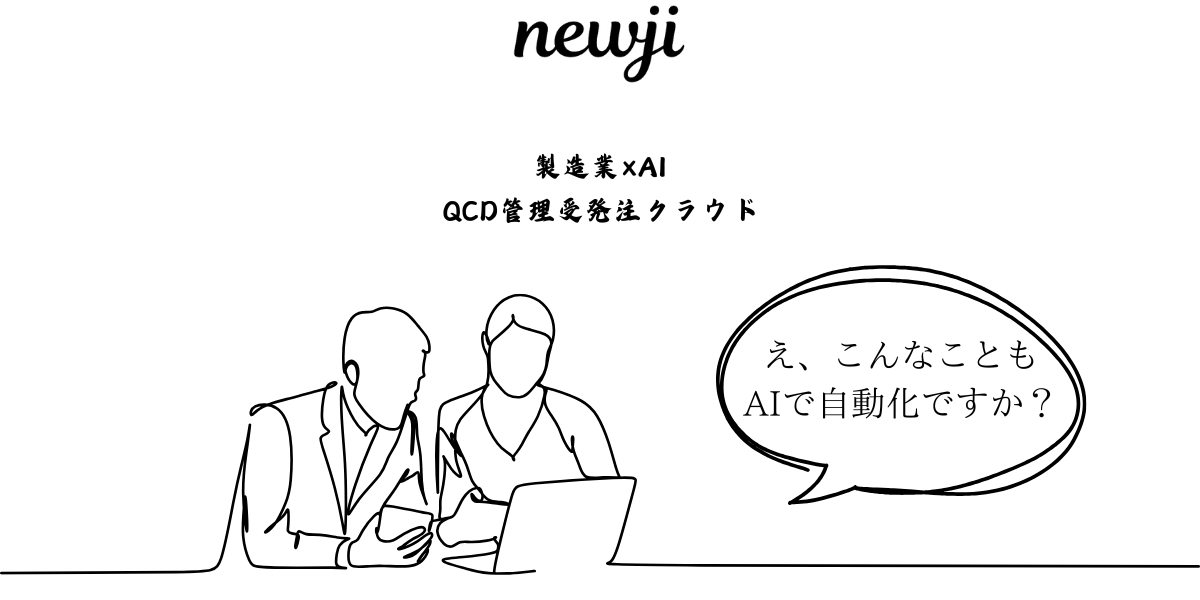
For production engineers in the filter cartridge manufacturing industry for medical device manufacturing! Balancing precision filtration and chemical resistance
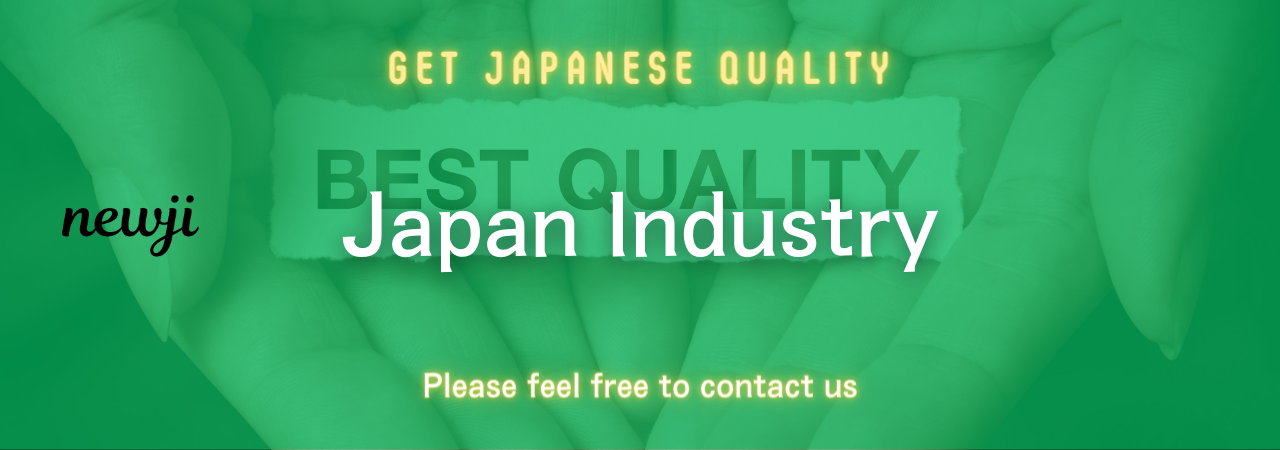
目次
Understanding the Role of Filter Cartridges in Medical Device Manufacturing
Filter cartridges play a crucial role in the medical device manufacturing process, particularly where precision filtration and chemical resistance are required.
These devices ensure that the medical products meet stringent quality standards, free from contaminants and suitable for safe use in various medical environments.
Production engineers need to have a thorough understanding of filter cartridges to enhance the quality and reliability of the manufactured medical devices.
The Importance of Precision Filtration
Precision filtration is vital in medical device manufacturing as it ensures the removal of unwanted particles and contaminants that could compromise the safety and efficacy of medical products.
Filter cartridges used in this field need to provide consistent filtrate quality, maintaining the integrity of the medical devices throughout the manufacturing process.
In applications where even the slightest contamination could have significant consequences, precision filtration helps prevent unwanted outcomes.
Engineers must choose filter cartridges with appropriate pore sizes and materials suitable for specific filtration needs.
Ensuring Chemical Resistance
Chemical resistance is another paramount factor for filter cartridges in medical device manufacturing.
During the production process, filter cartridges may come into contact with various chemicals that could potentially degrade the filter media and interfere with the filtration process.
To prevent degradation and ensure longevity, these filters must be constructed from materials that resist chemical reactions.
This necessity requires engineers to invest in high-quality materials that can withstand exposure to aggressive chemicals without affecting filtration efficiency.
Balancing Precision and Chemical Durability
Balancing precision filtration and chemical resistance is a formidable challenge for production engineers in filter cartridge manufacturing.
Selecting the appropriate filter media that can offer both properties is essential for achieving optimal performance in medical device production.
Engineers must analyze the types of substances encountered during filtration to make informed decisions about filter materials that are best suited for both precision and durability.
They need to consider factors like temperature, pressure, and compatibility with specific chemicals.
Choosing the Right Filter Media
Selection of the right filter media is crucial in ensuring the delicate balance between precision and chemical resistance.
There are several materials used in filter cartridges, each with its strengths and weaknesses.
Polypropylene filters are popular due to their excellent chemical resistance and cost-effectiveness.
However, in applications requiring high precision, engineers might opt for more advanced materials such as polytetrafluoroethylene (PTFE), which offers superior performance under challenging conditions.
In each case, engineers must conduct thorough assessments of the operational conditions to determine the most suitable filtration materials for specific medical device applications.
Enhancing Filtration Performance
Beyond selecting optimal materials, production engineers can take additional measures to enhance the performance of filter cartridges in medical device manufacturing.
Implementing regular maintenance and cleaning routines ensures that the filters remain operational and maintain their efficiency over time.
Routine inspections and replacements should be in place to prevent deterioration and possible disruptions in the manufacturing process.
Investing in advanced filtration technologies can also play a significant role in improving overall performance.
Innovations such as multi-layer filters or pleated cartridge designs can boost a filter’s longevity and filtration capacity, ensuring optimal outcomes without sacrificing precision or chemical resistance.
Testing and Validation
Testing and validation are crucial steps in filter cartridge manufacturing for medical devices.
Ensuring that the chosen filter cartridges perform adequately under working conditions is paramount to maintaining quality standards.
Production engineers must establish rigorous testing protocols to evaluate filter efficiency against expected contaminants and exposure to chemical environments.
Validation processes must be repeatable and consistent, offering confidence in the filter’s performance, ultimately ensuring the safety and effectiveness of medical devices.
Future Trends and Innovations
The ever-evolving landscape of medical device manufacturing continuously presents new challenges and opportunities for filter cartridge manufacturers.
Emerging trends and innovations in materials science and filtration technology offer exciting possibilities for enhancing precision and chemical resistance.
Nanotechnology is being explored to develop filters with incredibly fine pore structures, enabling the capture of even the smallest contaminants.
Similarly, advancements in sustainable materials are contributing to more environmentally friendly manufacturing solutions without compromising on performance.
The Role of Automation
Automation is playing an increasingly significant role in filter cartridge production.
Utilizing automated systems enhances precision and repeatability in manufacturing, reduces error rates, and increases overall efficiency.
With automated systems in place, production engineers can focus more on innovation and optimization, driving continuous improvement in filter performance for medical device applications.
Conclusion
Filter cartridges are vital components in the medical device manufacturing industry, where precision filtration and chemical resistance must be balanced to achieve exceptional product standards.
For production engineers, understanding the delicate equilibrium of these properties is crucial to ensuring the success and safety of medical devices.
By choosing the right filter materials, implementing robust testing protocols, and embracing innovative technologies, engineers can effectively contribute to advancements in medical device manufacturing, ultimately enhancing patient safety and improving healthcare outcomes worldwide.
資料ダウンロード
QCD管理受発注クラウド「newji」は、受発注部門で必要なQCD管理全てを備えた、現場特化型兼クラウド型の今世紀最高の受発注管理システムとなります。
ユーザー登録
受発注業務の効率化だけでなく、システムを導入することで、コスト削減や製品・資材のステータス可視化のほか、属人化していた受発注情報の共有化による内部不正防止や統制にも役立ちます。
NEWJI DX
製造業に特化したデジタルトランスフォーメーション(DX)の実現を目指す請負開発型のコンサルティングサービスです。AI、iPaaS、および先端の技術を駆使して、製造プロセスの効率化、業務効率化、チームワーク強化、コスト削減、品質向上を実現します。このサービスは、製造業の課題を深く理解し、それに対する最適なデジタルソリューションを提供することで、企業が持続的な成長とイノベーションを達成できるようサポートします。
製造業ニュース解説
製造業、主に購買・調達部門にお勤めの方々に向けた情報を配信しております。
新任の方やベテランの方、管理職を対象とした幅広いコンテンツをご用意しております。
お問い合わせ
コストダウンが利益に直結する術だと理解していても、なかなか前に進めることができない状況。そんな時は、newjiのコストダウン自動化機能で大きく利益貢献しよう!
(β版非公開)