- お役立ち記事
- For production engineers in the gas control valve manufacturing industry for semiconductor manufacturing! Design method that achieves both airtightness and corrosion resistance
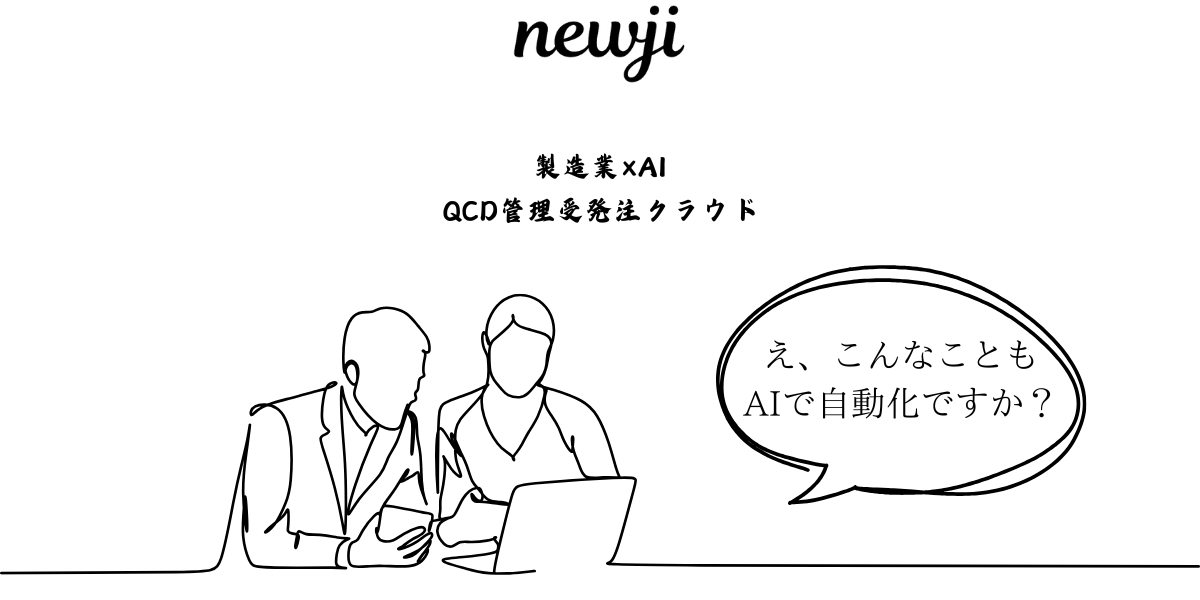
For production engineers in the gas control valve manufacturing industry for semiconductor manufacturing! Design method that achieves both airtightness and corrosion resistance
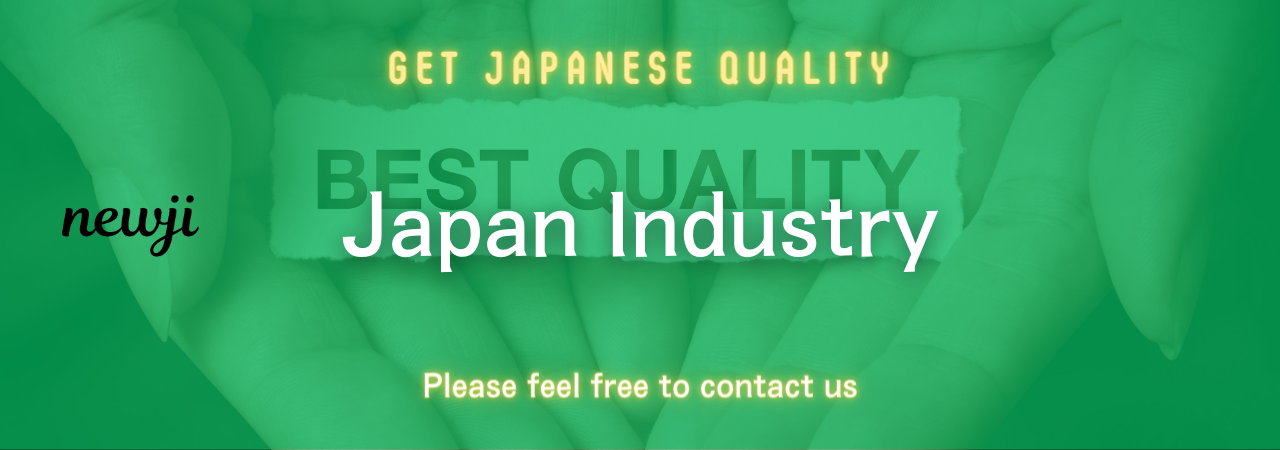
目次
Understanding the Importance of Gas Control Valves in Semiconductor Manufacturing
In the semiconductor manufacturing industry, precision and accuracy are paramount.
Gas control valves play a critical role in the production process by regulating the flow of gases used in various stages, such as etching, deposition, and cleaning.
These valves ensure that the exact amount of gas is delivered at the right pressure and temperature, maintaining the quality and efficiency of semiconductor production.
For production engineers, designing gas control valves that achieve both airtightness and corrosion resistance is crucial.
Airtightness ensures there are no leaks that could disrupt the delicate manufacturing process or cause safety hazards.
Meanwhile, corrosion resistance is essential to prevent the deterioration of valve components due to the reactive and abrasive gases often used in semiconductor production.
Challenges in Designing Gas Control Valves
Designing gas control valves that meet the stringent requirements of the semiconductor industry presents several challenges.
Engineers must consider the chemical properties of the gases involved, the potential for pressure fluctuations, and the need for materials that can withstand harsh environments.
The choice of materials is particularly significant.
Valves must be constructed from materials that offer the necessary mechanical strength while resisting corrosion from chemicals like fluorine, chlorine, and other reactive gases.
In addition to material selection, engineers must focus on creating seals that prevent leaks and maintaining precision in valve operation.
Material Selection for Corrosion Resistance
Corrosion resistance begins with selecting the right materials.
Stainless steel is often a preferred choice due to its excellent resistance to corrosion and its durability under high-pressure conditions.
However, certain grades of stainless steel may not be suitable for all applications, especially when dealing with highly reactive gases.
In such cases, engineers may opt for materials like Monel, Hastelloy, or even ceramics, which provide higher resistance to specific chemical interactions.
Monel is known for its excellent resistance to fluorine, while Hastelloy can withstand harsh environments with varying acidity levels.
Ceramic materials are also gaining popularity due to their outstanding corrosion resistance and ability to maintain integrity at high temperatures.
The key is to choose materials that align best with the specific requirements of the semiconductor manufacturing process they are intended for.
Ensuring Airtightness in Gas Control Valves
Achieving airtightness in gas control valves is vital for maintaining the integrity of the semiconductor production process.
Leaks can lead to contamination, compromised product quality, and increased production costs.
To ensure airtightness, engineers must prioritize the design of seals and fittings within the valves.
One approach is to use high-performance elastomers and polymers for seals.
Materials like PTFE (polytetrafluoroethylene) and FKM (fluoroelastomer) offer excellent chemical resistance and maintain a good seal under various temperature ranges.
Moreover, valve designs can incorporate metal-to-metal sealing solutions, where precision machining ensures tight fits that minimize the risk of leaks.
Implementing double-seal mechanisms provides an additional layer of security against potential gas leaks.
Balancing Airtightness and Corrosion Resistance
While both airtightness and corrosion resistance are crucial, achieving the right balance between these two aspects can be challenging.
Focusing too much on airtightness may lead to compromises in material selection, whereas prioritizing corrosion resistance can sometimes affect the precision of seals.
Engineers can use simulation tools to model and predict how different materials and designs will perform under specific conditions.
These tools help optimize valve designs by analyzing stress points, potential leak paths, and the effects of chemical interactions over time.
Iterative testing is also essential in refining valve designs.
Prototypes can be subjected to rigorous testing processes to ensure they meet the required standards for both airtightness and corrosion resistance.
The Role of Coatings and Surface Treatments
In addition to selecting the right materials, coatings and surface treatments can enhance the performance of gas control valves.
Specialized coatings can provide an extra layer of protection against corrosion and wear while maintaining the necessary sealing properties.
For instance, applying a PTFE coating can offer additional chemical resistance and reduce friction in moving parts.
Electroless nickel plating is another option that provides a uniform, corrosion-resistant layer on valve components.
Surface treatments like passivation can enhance the natural oxide layer on stainless steel, further improving its corrosion resistance properties.
These techniques, when combined with careful material selection and design considerations, contribute to developing high-performance gas control valves.
Conclusion
For production engineers in the gas control valve manufacturing industry for semiconductor applications, designing valves that achieve both airtightness and corrosion resistance is a complex but essential task.
Success lies in understanding the unique challenges posed by the semiconductor manufacturing environment and selecting the materials and designs that best meet those needs.
Through thoughtful material selection, innovative design features, and the application of advanced coatings and surface treatments, engineers can enhance the performance and reliability of gas control valves.
Ultimately, these efforts will contribute to higher quality and efficiency in semiconductor manufacturing, supporting the advancement of technology and innovation in the industry.
資料ダウンロード
QCD調達購買管理クラウド「newji」は、調達購買部門で必要なQCD管理全てを備えた、現場特化型兼クラウド型の今世紀最高の購買管理システムとなります。
ユーザー登録
調達購買業務の効率化だけでなく、システムを導入することで、コスト削減や製品・資材のステータス可視化のほか、属人化していた購買情報の共有化による内部不正防止や統制にも役立ちます。
NEWJI DX
製造業に特化したデジタルトランスフォーメーション(DX)の実現を目指す請負開発型のコンサルティングサービスです。AI、iPaaS、および先端の技術を駆使して、製造プロセスの効率化、業務効率化、チームワーク強化、コスト削減、品質向上を実現します。このサービスは、製造業の課題を深く理解し、それに対する最適なデジタルソリューションを提供することで、企業が持続的な成長とイノベーションを達成できるようサポートします。
オンライン講座
製造業、主に購買・調達部門にお勤めの方々に向けた情報を配信しております。
新任の方やベテランの方、管理職を対象とした幅広いコンテンツをご用意しております。
お問い合わせ
コストダウンが利益に直結する術だと理解していても、なかなか前に進めることができない状況。そんな時は、newjiのコストダウン自動化機能で大きく利益貢献しよう!
(Β版非公開)