- お役立ち記事
- For production engineers in the gas introduction nozzle manufacturing industry for vacuum equipment! Technology that increases uniform flow rate and durability
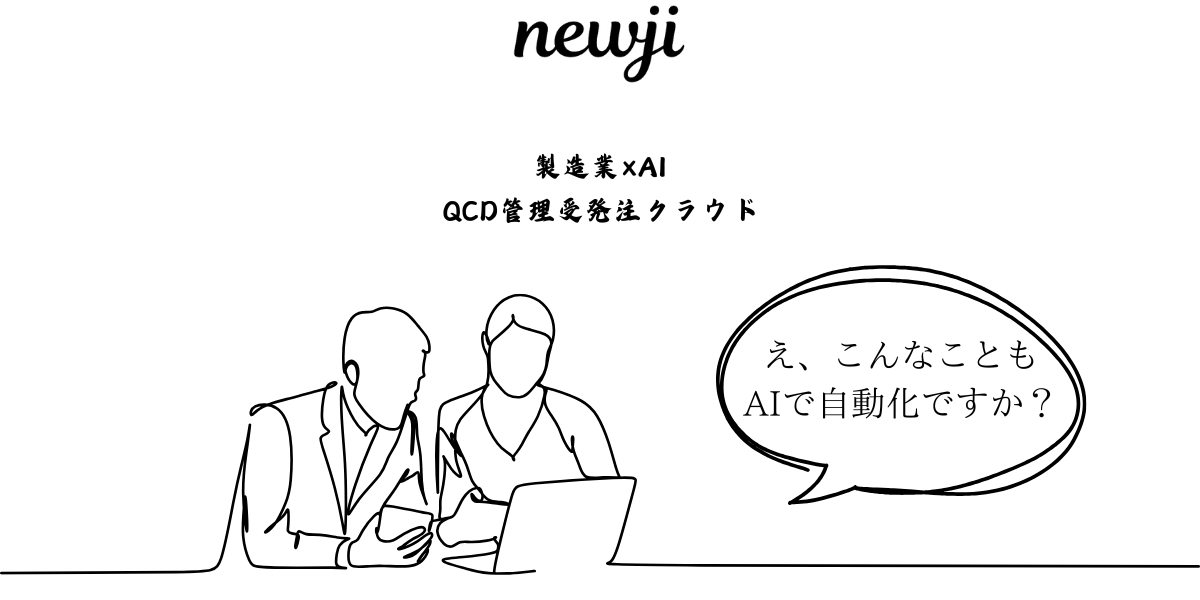
For production engineers in the gas introduction nozzle manufacturing industry for vacuum equipment! Technology that increases uniform flow rate and durability
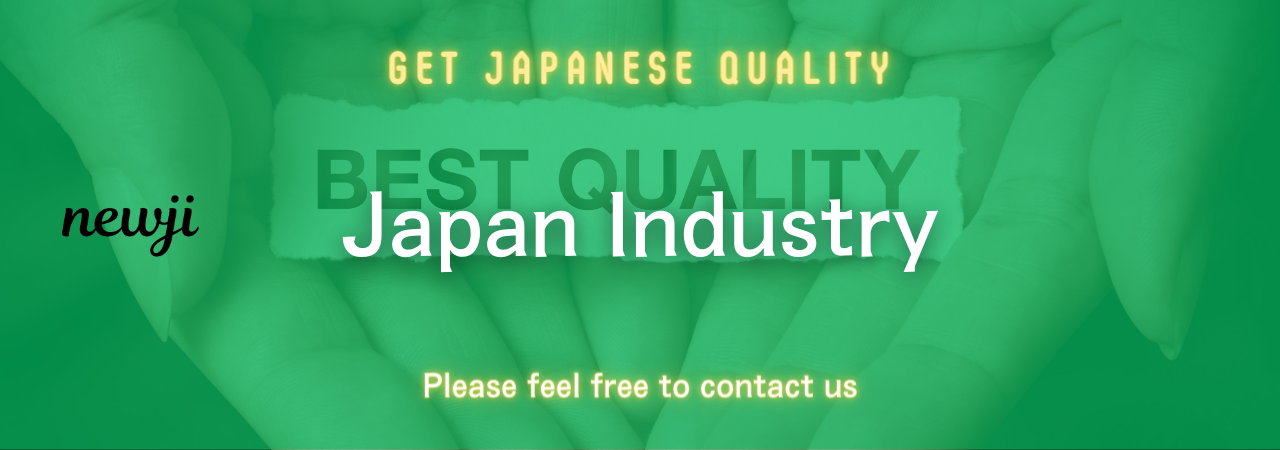
目次
Understanding the Importance of Gas Introduction Nozzles
In the manufacturing of vacuum equipment, one of the most crucial components is the gas introduction nozzle.
These nozzles play a pivotal role in ensuring the precise flow and distribution of gases within the system.
For production engineers, understanding the technology behind these nozzles can significantly impact the efficiency and longevity of the equipment.
The key objectives in nozzle design are to achieve a uniform flow rate and enhance durability.
This is critical in maintaining the optimal performance of vacuum systems and minimizing downtimes.
The Challenge of Achieving Uniform Flow Rate
Uniform flow rate is essential for maintaining the balance and consistency in vacuum processes.
However, achieving this is not a straightforward task.
Different factors, such as nozzle design, material selection, and manufacturing precision, can influence the flow rate.
Engineers must consider the type of gases in use, as various gases can interact differently with materials and design features.
By optimizing these variables, engineers can ensure a more uniform flow, which translates to better performance and efficiency.
Material Selection for Enhanced Durability
Durability is another critical factor for gas introduction nozzles.
A nozzle that wears out quickly can lead to increased maintenance costs and potential system failures.
To combat this, the selection of material is paramount.
Materials such as stainless steel, ceramics, and specialized alloys offer high resistance to corrosion and wear, improving the longevity of the nozzles.
Moreover, these materials can withstand the high pressures and temperatures typically associated with vacuum systems.
Innovative Design Techniques for Improved Efficiency
Advancements in design techniques have paved the way for significant improvements in nozzle performance.
Computational fluid dynamics (CFD) is one such technique that allows engineers to simulate and analyze gas flow patterns within nozzles.
This technology helps in identifying potential issues and optimizing design parameters before the actual manufacturing process begins.
By utilizing CFD, engineers can predict how changes in nozzle geometry affect flow rate and distribution.
This predictive capability enables the creation of more efficient and effective nozzle designs.
Precision Manufacturing: A Key to Success
Precision in manufacturing is essential to ensuring that the designed specifications are met accurately.
Modern machining technologies, including CNC machining and laser cutting, allow for the production of nozzles with high precision.
These technologies ensure minimal deviations in dimensions, which is critical for maintaining the intended flow characteristics.
Additionally, precision manufacturing reduces the likelihood of defects and inconsistencies, further enhancing the nozzle’s performance and durability.
Quality Assurance and Testing
Once manufactured, it’s crucial to subject gas introduction nozzles to rigorous quality assurance testing.
This ensures that they meet the required performance standards and are free from defects.
Testing includes verifying flow rates, checking for material integrity, and assessing overall durability.
By implementing comprehensive quality control measures, manufacturers can guarantee that their nozzles deliver optimal performance in vacuum equipment.
Trends in Nozzle Technology
The industry is constantly evolving, with new trends emerging to improve nozzle technology further.
One such trend is the integration of smart technologies.
Smart nozzles can provide real-time data on flow rates and system conditions, allowing for instant adjustments and enhancements.
This technology not only increases efficiency but also helps in predictive maintenance, reducing the risk of unexpected downtimes.
Another trend is the use of advanced coatings that improve the wear resistance and chemical stability of nozzles.
These coatings reduce the interaction between gases and nozzle surfaces, enhancing the durability and performance of the nozzles.
Training and Skill Development
For production engineers, staying up-to-date with the latest technologies and methods is crucial.
Continuous training and skill development are essential for understanding and utilizing new design and manufacturing techniques effectively.
Workshops, seminars, and online courses can help engineers stay informed about the latest trends and technologies in nozzle manufacturing.
Conclusion: Innovations for Future Success
In the gas introduction nozzle manufacturing industry for vacuum equipment, enhancing uniform flow rates and durability are critical objectives.
By leveraging new technologies, materials, and manufacturing techniques, engineers can significantly improve nozzle performance.
As the industry advances, staying informed about emerging trends and adopting innovative solutions will be key to maintaining competitiveness and achieving long-term success.
Production engineers who embrace these advancements will be able to create more efficient, reliable, and durable vacuum equipment, greatly benefiting their operations and their customers.
資料ダウンロード
QCD調達購買管理クラウド「newji」は、調達購買部門で必要なQCD管理全てを備えた、現場特化型兼クラウド型の今世紀最高の購買管理システムとなります。
ユーザー登録
調達購買業務の効率化だけでなく、システムを導入することで、コスト削減や製品・資材のステータス可視化のほか、属人化していた購買情報の共有化による内部不正防止や統制にも役立ちます。
NEWJI DX
製造業に特化したデジタルトランスフォーメーション(DX)の実現を目指す請負開発型のコンサルティングサービスです。AI、iPaaS、および先端の技術を駆使して、製造プロセスの効率化、業務効率化、チームワーク強化、コスト削減、品質向上を実現します。このサービスは、製造業の課題を深く理解し、それに対する最適なデジタルソリューションを提供することで、企業が持続的な成長とイノベーションを達成できるようサポートします。
オンライン講座
製造業、主に購買・調達部門にお勤めの方々に向けた情報を配信しております。
新任の方やベテランの方、管理職を対象とした幅広いコンテンツをご用意しております。
お問い合わせ
コストダウンが利益に直結する術だと理解していても、なかなか前に進めることができない状況。そんな時は、newjiのコストダウン自動化機能で大きく利益貢献しよう!
(Β版非公開)