- お役立ち記事
- For production engineers in the pipe fitting manufacturing industry! Processing and design to achieve both pressure resistance and leak prevention
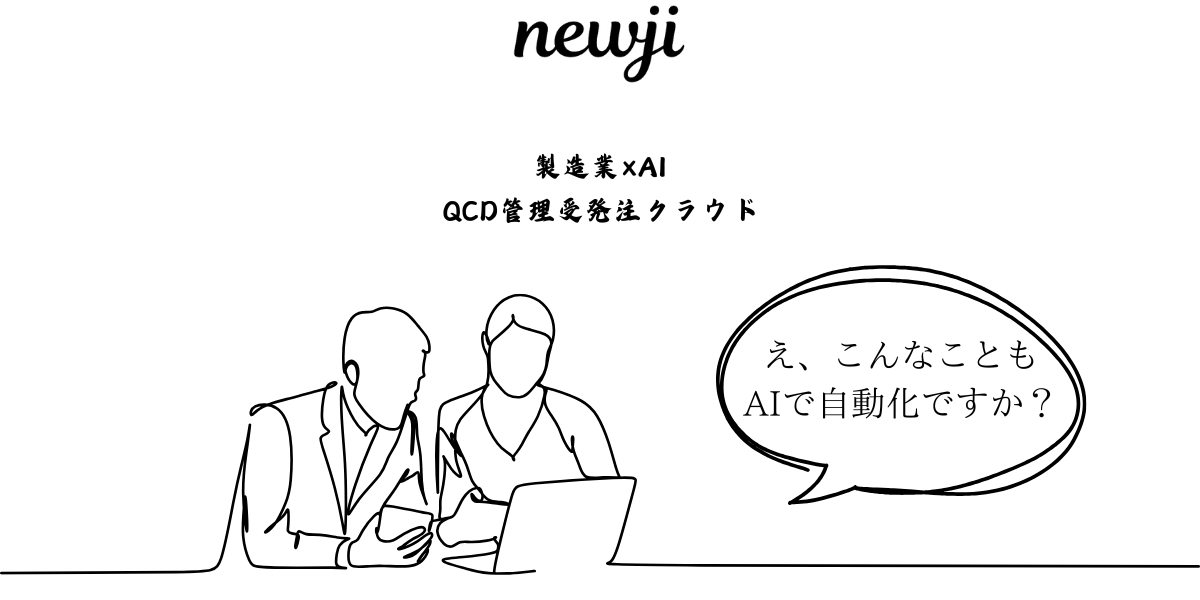
For production engineers in the pipe fitting manufacturing industry! Processing and design to achieve both pressure resistance and leak prevention
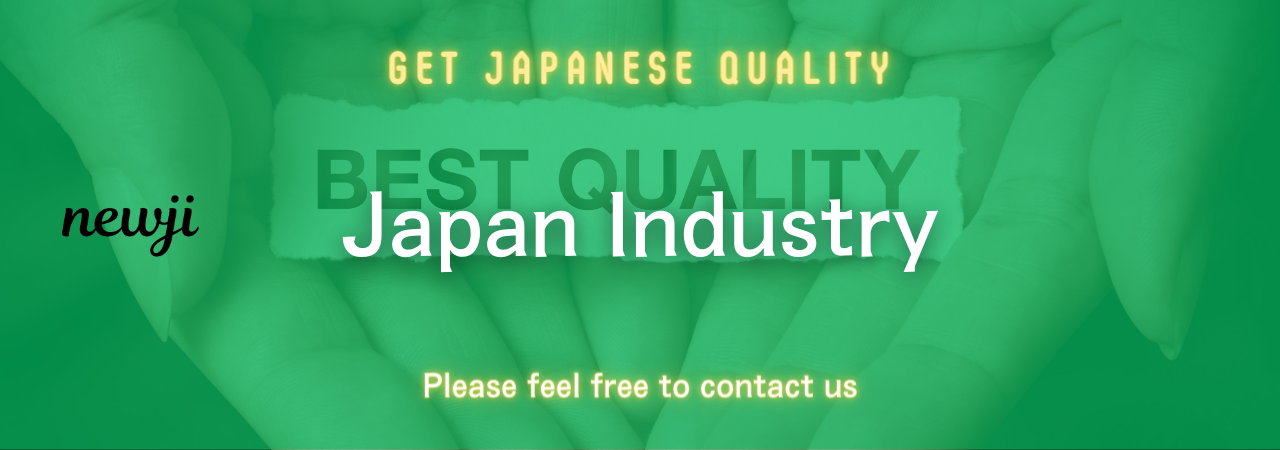
目次
Understanding the Basics of Pipe Fitting Manufacturing
Pipe fitting manufacturing is a critical aspect of various industries, including construction, oil and gas, water treatment, and more.
The primary goal in this industry is to produce components that can withstand high pressure and prevent leaks.
Achieving this requires careful consideration of materials, design, and processing methods.
The Importance of Material Selection
Choosing the right material is fundamental in pipe fitting manufacturing.
Materials must be durable, corrosion-resistant, and must have the right mechanical properties to handle the operating conditions.
Common materials used include stainless steel, carbon steel, copper, aluminum, and certain plastics.
The choice depends on the application’s specific needs, such as resistance to certain chemicals or temperatures.
For instance, stainless steel is often used for its excellent corrosion resistance and strength, making it suitable for high-pressure applications.
On the other hand, plastic fittings might be more appropriate for lower pressure and less corrosive environments.
Design Considerations for Pressure Resistance and Leak Prevention
Ensuring Pressure Resistance
Pressure resistance in pipe fittings is primarily achieved through the design and choice of materials.
Designers must calculate the maximum pressure the fittings will encounter and ensure the selected material and thickness can handle it.
Proper thickness is essential to prevent bursting or deformation under pressure.
Using finite element analysis (FEA) software can aid in simulating and testing different scenarios to ensure the design will hold under maximum pressure conditions.
Strategies for Leak Prevention
Leak prevention is another critical consideration.
Even the smallest leak can lead to significant losses and safety hazards.
Design features like smooth, deburred edges and airtight seals help in preventing leaks.
Using high-quality gaskets and O-rings, which compensate for material expansion or contraction and provide excellent sealing, can be a game-changer.
Moreover, threaded joints must be designed to create a secure fit, and welding should be performed with the utmost precision to eliminate weak points.
Advanced Processing Techniques
Precision Manufacturing
Precision is key in the manufacturing process to ensure fittings meet strict specifications.
Advanced machining processes like CNC machining are commonly used in the industry for their accuracy and consistency.
These technologies produce parts with tight tolerances, essential for ensuring a perfect fit and effective sealing.
Utilizing Heat Treatment
Heat treatment can enhance the properties of metal pipe fittings, improving their strength and durability.
Processes such as annealing, quenching, and tempering help tailor the material properties to the application’s demands.
This step is crucial for fittings that require added strength or resistance to various types of stress.
Quality Assurance in Production
Inspection and Testing
Quality assurance starts with rigorous inspection and testing throughout the manufacturing process.
Non-destructive testing methods, like ultrasonic and radiographic inspection, ensure that no flaws or weaknesses go undetected.
These tests guarantee that each fitting can withstand pressure and function without leaks.
Adhering to Standards and Certifications
Compliance with industry standards and certifications, such as ISO 9001, is essential for maintaining quality and safety.
Standards set by organizations like ASTM and ASME provide guidelines for material properties, design specifications, and testing procedures.
Adhering to these ensures that pipe fittings are of high quality and reliable in application.
Innovations in Pipe Fitting Manufacturing
Embracing New Technologies
With the advancement of technology, new methods are being integrated into pipe fitting manufacturing.
3D printing, for example, allows for the rapid prototyping of new designs, which can be tested and refined with ease.
This technology offers flexibility and reduces lead times significantly.
Sustainable Manufacturing Practices
Sustainability is becoming a priority across all industries, including pipe fitting manufacturing.
Efforts are being made to reduce waste, recycle materials, and improve the energy efficiency of manufacturing processes.
Using eco-friendly materials and processes not only benefits the environment but can also reduce costs and improve a company’s reputation.
Conclusion
For production engineers in the pipe fitting manufacturing industry, achieving a balance between pressure resistance and leak prevention is key to producing reliable and safe products.
Understanding the importance of material selection, embracing advanced processing techniques, and adhering to quality standards are all critical steps in this process.
By staying updated with technological advancements and focusing on sustainable practices, engineers can drive innovation and improve the overall efficiency of their manufacturing operations.
資料ダウンロード
QCD調達購買管理クラウド「newji」は、調達購買部門で必要なQCD管理全てを備えた、現場特化型兼クラウド型の今世紀最高の購買管理システムとなります。
ユーザー登録
調達購買業務の効率化だけでなく、システムを導入することで、コスト削減や製品・資材のステータス可視化のほか、属人化していた購買情報の共有化による内部不正防止や統制にも役立ちます。
NEWJI DX
製造業に特化したデジタルトランスフォーメーション(DX)の実現を目指す請負開発型のコンサルティングサービスです。AI、iPaaS、および先端の技術を駆使して、製造プロセスの効率化、業務効率化、チームワーク強化、コスト削減、品質向上を実現します。このサービスは、製造業の課題を深く理解し、それに対する最適なデジタルソリューションを提供することで、企業が持続的な成長とイノベーションを達成できるようサポートします。
オンライン講座
製造業、主に購買・調達部門にお勤めの方々に向けた情報を配信しております。
新任の方やベテランの方、管理職を対象とした幅広いコンテンツをご用意しております。
お問い合わせ
コストダウンが利益に直結する術だと理解していても、なかなか前に進めることができない状況。そんな時は、newjiのコストダウン自動化機能で大きく利益貢献しよう!
(Β版非公開)