- お役立ち記事
- For production engineers in the plastic molding industry! Optimize mold flow balance with hot runner system
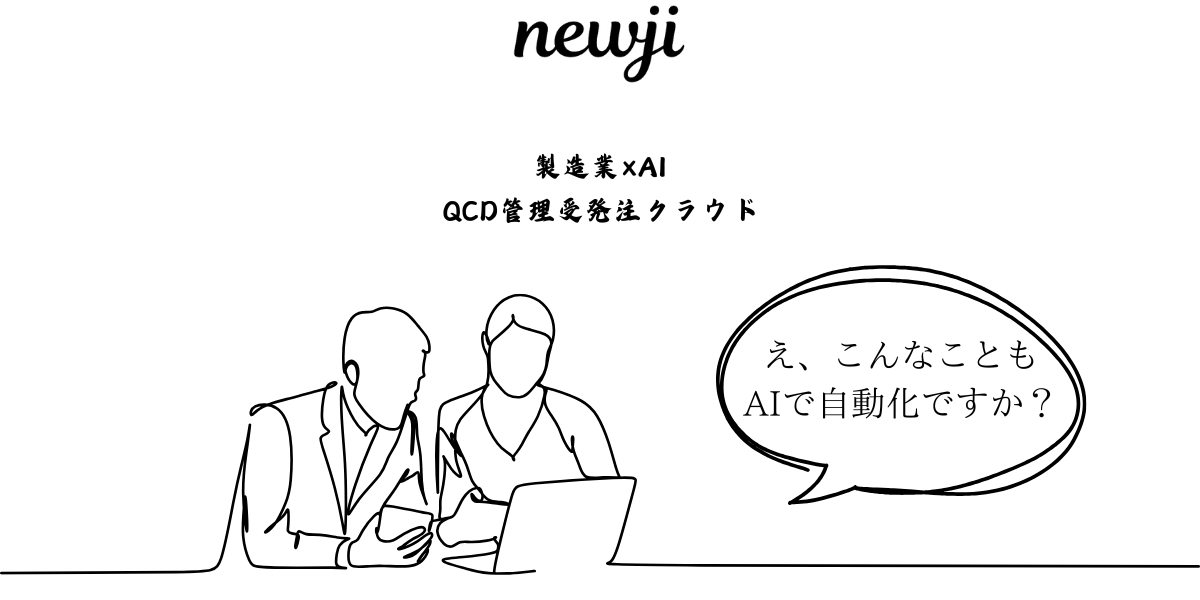
For production engineers in the plastic molding industry! Optimize mold flow balance with hot runner system
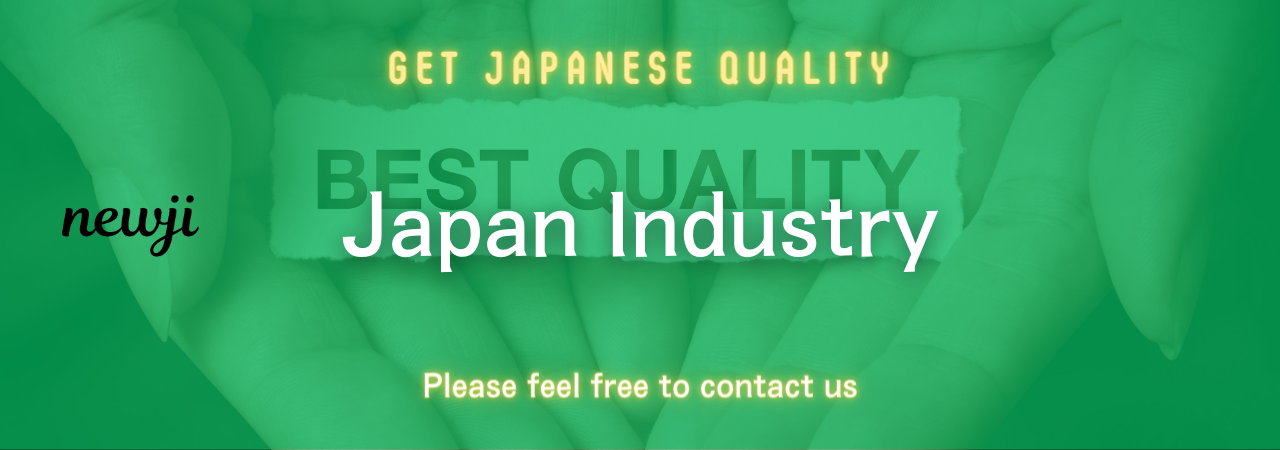
目次
Understanding the Hot Runner System
Plastic molding is an intricate process that requires precision and expertise.
For production engineers in this industry, optimizing the flow of materials through a mold is vital to achieve high-quality finished products.
This is where the hot runner system comes into play.
A hot runner system is a complex assembly used in injection molding to manage the flow of molten plastic.
It consists of heated components that ensure the plastic remains liquid until it reaches the mold cavity.
This technology stands in contrast to cold runner systems, where material often solidifies before reaching the mold, potentially causing imperfections.
By maintaining the plastic at an ideal temperature throughout the molding process, the hot runner system minimizes waste, reduces cycle times, and enhances product quality.
Understanding and effectively utilizing this system can lead to significant improvements in production efficiency and product consistency.
The Importance of Mold Flow Balance
Balancing mold flow is crucial in plastic molding.
An unbalanced flow can lead to a range of quality issues, such as inconsistent wall thickness, warping, and defects in the final product.
Proper flow balance ensures that the molten plastic fills the mold evenly, resulting in uniformity in the product.
The hot runner system plays a pivotal role in achieving mold flow balance.
It allows for precise control over the temperature and pressure across the manifold, ensuring that each part of the mold receives an equal distribution of material.
This control is particularly important in multi-cavity molds, where different parts of the mold could otherwise experience uneven flow rates.
Mold flow analysis tools, often integrated with hot runner systems, help production engineers visualize and control flow patterns.
Through simulations, engineers can adjust parameters and predict potential issues, allowing for corrective measures before production begins.
Advantages of Using a Hot Runner System
The adoption of a hot runner system offers several advantages that can substantially impact the efficiency of plastic molding operations.
Reduced Cycle Times
One of the most significant benefits of hot runner systems is the reduction in cycle times.
Because the plastic remains in a molten state until it enters the mold, there’s no need for extensive heating and cooling periods that are typical with cold runner systems.
Faster cycle times mean increased productivity and throughput, allowing manufacturers to meet high demands efficiently.
Minimized Material Waste
Material waste is a common concern in plastic molding due to scrap generation and runner material.
With hot runner systems, there’s a drastic reduction in waste since the plastic remains in a molten state until it’s injected into the mold.
This not only reduces costs associated with raw material usage but also contributes to more sustainable manufacturing practices.
Enhanced Product Quality
The consistency and accuracy offered by hot runner systems improve the quality of the manufactured products.
Defects and inconsistencies are greatly reduced, leading to fewer rejected parts and higher customer satisfaction.
Uniform temperature control ensures that the final product meets the desired specifications and performance standards.
Implementing Hot Runner Systems in Production
Integrating hot runner systems into existing molding operations requires careful planning and execution.
Engineers must assess the specific needs of their production line and choose a system that fits those requirements.
Choosing the Right System
Selecting the appropriate hot runner system involves considering factors such as the type of materials being used, the complexity of the mold design, and the desired production volume.
Systems can vary in terms of components and features, so it’s important to consult with experts and manufacturers to identify the best solution.
Installation Considerations
Proper installation is key to maximizing the benefits of a hot runner system.
This includes meticulous attention to the alignment of the nozzles and manifolds and ensuring that the system is correctly integrated with the existing injection molding equipment.
Training for operators and maintenance personnel is also essential to ensure smooth operation and troubleshoot potential issues.
Maintenance Strategies
Regular maintenance of hot runner systems is essential for their long-term performance.
This includes routine inspections, cleaning, and the replacement of worn components.
Preemptive maintenance prevents unexpected downtimes and keeps the production line running efficiently.
Conclusion
For production engineers in the plastic molding industry, optimizing mold flow balance with a hot runner system presents numerous opportunities for improving efficiency and product quality.
While the initial implementation may require investment and effort, the long-term benefits of reduced cycle times, minimized waste, and enhanced product quality are substantial.
By understanding the principles of mold flow and leveraging the technological advantages of hot runner systems, manufacturers can achieve a competitive edge in the increasingly demanding market.
Through careful planning, execution, and maintenance, the transition to utilizing hot runner systems can be a productive and rewarding endeavor.
資料ダウンロード
QCD調達購買管理クラウド「newji」は、調達購買部門で必要なQCD管理全てを備えた、現場特化型兼クラウド型の今世紀最高の購買管理システムとなります。
ユーザー登録
調達購買業務の効率化だけでなく、システムを導入することで、コスト削減や製品・資材のステータス可視化のほか、属人化していた購買情報の共有化による内部不正防止や統制にも役立ちます。
NEWJI DX
製造業に特化したデジタルトランスフォーメーション(DX)の実現を目指す請負開発型のコンサルティングサービスです。AI、iPaaS、および先端の技術を駆使して、製造プロセスの効率化、業務効率化、チームワーク強化、コスト削減、品質向上を実現します。このサービスは、製造業の課題を深く理解し、それに対する最適なデジタルソリューションを提供することで、企業が持続的な成長とイノベーションを達成できるようサポートします。
オンライン講座
製造業、主に購買・調達部門にお勤めの方々に向けた情報を配信しております。
新任の方やベテランの方、管理職を対象とした幅広いコンテンツをご用意しております。
お問い合わせ
コストダウンが利益に直結する術だと理解していても、なかなか前に進めることができない状況。そんな時は、newjiのコストダウン自動化機能で大きく利益貢献しよう!
(Β版非公開)