- お役立ち記事
- For production engineers in the power tool manufacturing industry! Package design method to ensure safety of lithium-ion batteries
For production engineers in the power tool manufacturing industry! Package design method to ensure safety of lithium-ion batteries
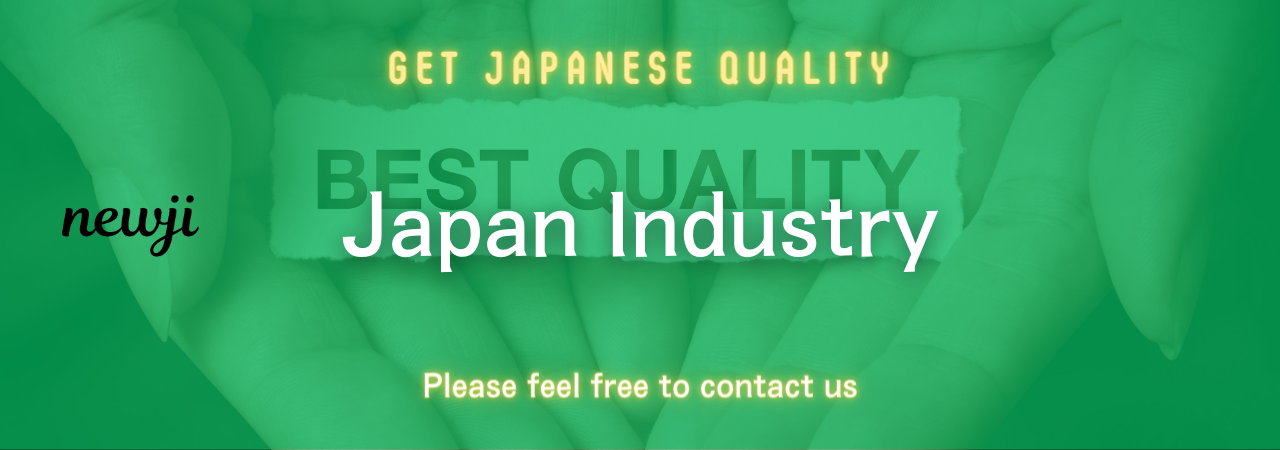
目次
Understanding the Importance of Safe Packaging for Lithium-Ion Batteries
The power tool manufacturing industry heavily relies on lithium-ion batteries due to their efficiency and long-lasting power capabilities.
These batteries have transformed how we use power tools, offering a lightweight and rechargeable power source.
However, alongside these benefits come challenges, particularly regarding safety.
The packaging of lithium-ion batteries plays a crucial role in ensuring they are transported and stored safely, minimizing risks of malfunctions or accidents.
The Key Challenges of Lithium-Ion Battery Packaging
Lithium-ion batteries are susceptible to several safety issues.
The most significant of these is the potential for thermal runaway.
This is a situation where the battery temperature rises uncontrollably, leading to combustion or even explosions.
Mechanical shocks, punctures, or short circuits can trigger thermal runaway.
This potential danger makes effective packaging essential.
Further adding complexity is the movement and transportation of these batteries.
They must be able to withstand various environmental conditions during their journey from manufacturing facilities to their final destination.
This includes resistance against vibrations, temperature variations, and humidity.
Thus, packaging must be robust enough to offer protection under all these conditions.
Components of an Effective Packaging Design
Successful package design for lithium-ion batteries must incorporate several critical components.
Firstly, the package must be made of materials that are flame resistant.
If a battery were to catch fire, the packaging shouldn’t exacerbate the situation by contributing to the flames.
Isolation is another critical factor.
Each battery should be individually sealed to prevent any interaction with others as each could potentially trigger a reaction affecting the rest.
This is often achieved by using individual plastic cladding or compartments made from non-conductive materials.
Additionally, cushioning materials are vital.
They protect the batteries from mechanical shocks and vibrations which could damage the battery cells and potentially cause a safety hazard.
Materials such as foam, rubber, or corrugated cardboard are often used.
Regulatory Compliance in Packaging
Manufacturers must adhere to specific regulations to avoid legal ramifications and ensure customer safety.
The International Air Transport Association (IATA) has laid out stringent rules concerning how lithium-ion batteries should be packed and labeled.
Regulations such as UN 3480 and UN 3481, for instance, specify how standalone and equipment-packed lithium-ion batteries should be handled.
A crucial aspect of compliance is clear labeling, highlighting potential risks and ensuring handlers of the packages are aware of the contents and any special care required.
Furthermore, manufacturers will often need to conduct package performance tests to ensure their packaging meets these international standards.
Innovative Packaging Solutions
As technological advancements evolve, so too do packaging solutions.
Some manufacturers are exploring the use of smart packaging technologies, incorporating sensors and tracking capabilities.
These allow continual monitoring of battery condition, detecting any potential issues such as temperature spikes, and providing real-time data to mitigate risks quickly.
Eco-friendly packaging materials are increasingly in demand.
Solutions that recycle or reuse packaging reduce waste and appeal to environmentally conscious consumers.
By leaning towards biodegradable materials and efficiently designed packages, manufacturers can also cut costs and environmental impacts.
Best Practices for Ensuring Safety
There are several best practices those in the power tool manufacturing industry should adopt to ensure their lithium-ion battery packaging is safe.
First, involve the whole product development team in the packaging process to create a multidisciplinary approach to identifying and solving potential problems before they occur.
Conduct comprehensive testing regularly.
Simulated transportation tests, thermal tests, and impact assessments should be the norm, not the exception.
Collaborating with third-party testing facilities can provide an unbiased view and raise packaging safety standards.
Furthermore, continuous training programs for all stakeholders involved in the packaging process should be implemented.
By staying informed of the newest regulations and technological advances, suppliers, designers, and handlers can ensure they’re doing everything possible to protect the product and, ultimately, the end-user.
Conclusion
In conclusion, designing safe packaging for lithium-ion batteries within the power tool manufacturing industry is a multifaceted challenge.
Balancing safety, compliance, and customer satisfaction demands diligence and innovation.
By understanding the specific requirements and ongoing commitment to best practices, engineers and designers can greatly reduce risks while enhancing product reliability and user trust.
Effective packaging is more than a necessity—it’s a vital component in delivering safe, reliable products to consumers worldwide.
資料ダウンロード
QCD調達購買管理クラウド「newji」は、調達購買部門で必要なQCD管理全てを備えた、現場特化型兼クラウド型の今世紀最高の購買管理システムとなります。
ユーザー登録
調達購買業務の効率化だけでなく、システムを導入することで、コスト削減や製品・資材のステータス可視化のほか、属人化していた購買情報の共有化による内部不正防止や統制にも役立ちます。
NEWJI DX
製造業に特化したデジタルトランスフォーメーション(DX)の実現を目指す請負開発型のコンサルティングサービスです。AI、iPaaS、および先端の技術を駆使して、製造プロセスの効率化、業務効率化、チームワーク強化、コスト削減、品質向上を実現します。このサービスは、製造業の課題を深く理解し、それに対する最適なデジタルソリューションを提供することで、企業が持続的な成長とイノベーションを達成できるようサポートします。
オンライン講座
製造業、主に購買・調達部門にお勤めの方々に向けた情報を配信しております。
新任の方やベテランの方、管理職を対象とした幅広いコンテンツをご用意しております。
お問い合わせ
コストダウンが利益に直結する術だと理解していても、なかなか前に進めることができない状況。そんな時は、newjiのコストダウン自動化機能で大きく利益貢献しよう!
(Β版非公開)