- お役立ち記事
- For production engineers in the precision machinery industry! Multi-axis machining techniques on multi-axis machining centers
月間76,176名の
製造業ご担当者様が閲覧しています*
*2025年3月31日現在のGoogle Analyticsのデータより
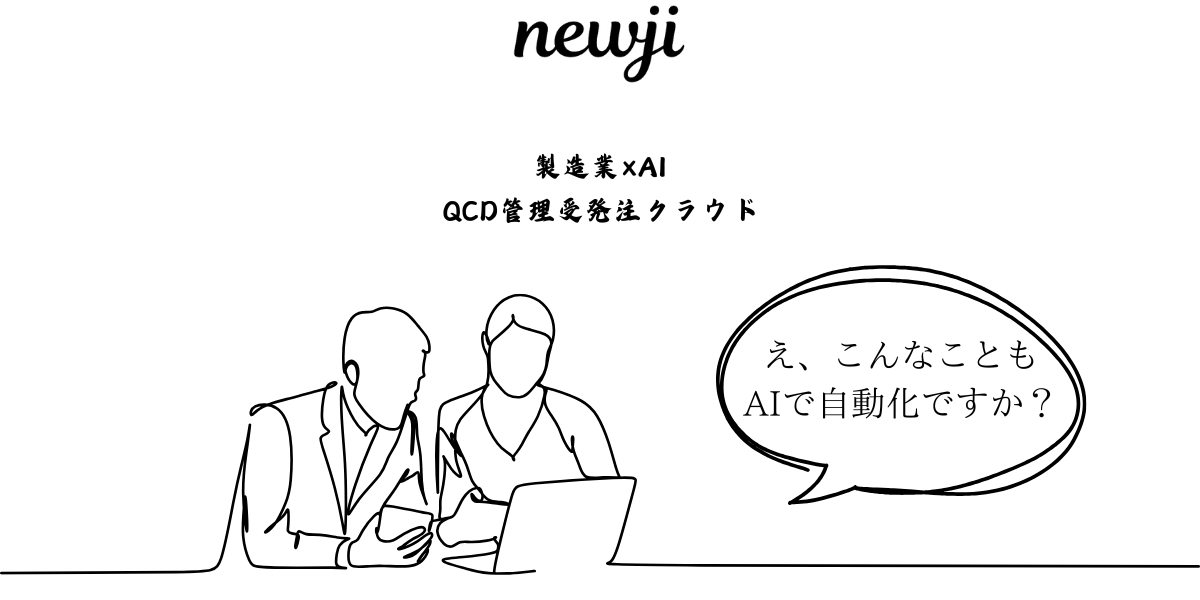
For production engineers in the precision machinery industry! Multi-axis machining techniques on multi-axis machining centers
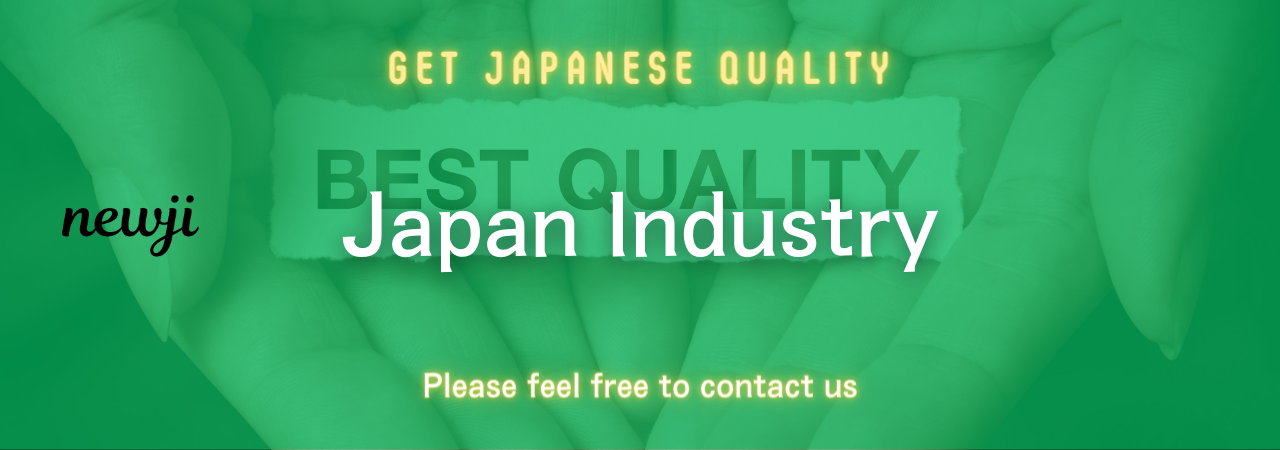
目次
Understanding Multi-Axis Machining
Multi-axis machining involves using computer numerical control (CNC) equipment to manoeuvre a tool around multiple axes simultaneously, allowing for complex shapes and features to be machined with precision.
This advanced technique is essential in the precision machinery industry, where intricate designs and exact specifications are the norm.
Machining centers with more than three axes offer enhanced capabilities by adding rotational freedom, effectively increasing the types of operations that can be completed in one setup.
This reduces the need for multiple fixtures or machine operations, minimizing human error and enhancing the precision of the machined parts.
The Basics of Multi-Axis Machining Centers
In a traditional three-axis machining center, the tool moves linearly along the X (horizontal), Y (horizontal at a different plane), and Z (vertical) axes.
These movements allow the machine to cut into materials from different sides.
However, for more complicated parts, three-axis configurations can be limiting due to the necessity to repeatedly reposition the workpiece.
Multi-axis machining centers, typically involving four, five, or even six axes, allow for the rotation of either the tool or the part itself.
This significantly amplifies the machine’s flexibility.
For instance, in a five-axis machining center, the additional two axes allow the tool to rotate around the X and Y axes, providing more angles and approaches to the workpiece.
Advantages of Multi-Axis Machining
One of the primary advantages of multi-axis machining is its capability to produce complex and high-precision components in shorter production times.
The additional axes reduce the need to transfer parts between different machines or orientations, streamlining operations and reducing lead times.
These machines also improve surface finish quality.
As the tool can approach the material from optimal angles, there is less risk of tool deflection and tool marks, resulting in smoother surfaces.
Reducing the need for repositioning also translates to higher accuracy and quality control.
When using a multi-axis machining center, the part can be machined in a single setup without manual intervention, which minimizes the potential for human error.
Applications in Precision Machinery
The precision machinery industry demands high accuracy and repeatability, areas where multi-axis machining excels.
It’s particularly beneficial for industries such as aerospace, automotive, medical equipment, and any sector that requires complex geometries or materials with intricate details.
In aerospace, for example, multi-axis machining is crucial for producing turbine components, which have complex shapes and need to meet stringent tolerances.
Similarly, in the automotive industry, intricate engine components and precision frame parts are often machined using multi-axis technology.
Key Techniques in Multi-Axis Machining
Several techniques are critical to maximizing the effectiveness of multi-axis machining centers.
Understanding and implementing these techniques is essential for production engineers aiming to optimize their machining processes.
Simultaneous Versus Indexed Machining
Simultaneous machining involves moving all axes at the same time, allowing for the creation of complex shapes in a single operation.
This technique is ideal for intricate parts that require continuous tool engagement with the material, offering superior finishes and precision.
Indexed machining, on the other hand, involves repositioning the part or tool between cuts, similar to a series of static operations.
While less efficient than simultaneous machining, it allows for the completion of more solitary operations which can be beneficial in certain scenarios or with less-complex parts.
Toolpath Optimization
Toolpath optimization is crucial in multi-axis machining to ensure efficient material removal, minimize machining time, and reduce tool wear.
Engineers need to carefully plan the toolpath to avoid collisions, optimize cutting angles, and maintain the quality of the final product.
CAD/CAM software is typically used to simulate the machining process and refine toolpaths before any actual cutting is done.
This tech-focused approach ensures that the machine operates within its limits while achieving the desired final product specifications.
Dynamic Workpiece Positioning
Using dynamic workpiece positioning, engineers can ensure that larger and more complex parts are effectively machined.
This technique involves the real-time adjustment of the workpiece position to maintain optimum tool engagement, often integrated with feedback systems to monitor and adjust the machining process dynamically.
Challenges and Considerations
While multi-axis machining offers numerous advantages, it also presents challenges that production engineers must consider.
The complexity of programming multi-axis machines is higher, necessitating skilled technicians who are proficient in both software and the physical principles of machining.
The cost of multi-axis machinery is another consideration.
These machines are a significant investment and require maintenance to ensure they deliver precise results consistently.
Production engineers need to consider the total cost of ownership, balancing upfront expenses with long-term savings from increased efficiency and reduced error rates.
Training and Skill Development
To fully leverage the benefits of multi-axis machining, it’s crucial for engineers and operators to receive ongoing training.
Understanding the intricacies of toolpath planning, software use, and machine operation will greatly improve their ability to produce accurate and efficient results.
Training programs and certifications are available to help equip engineers with the necessary skills and knowledge to effectively use multi-axis machining centers.
Conclusion
Multi-axis machining centers offer incredible benefits to the precision machinery industry, significantly reducing lead times, improving product quality, and enhancing production efficiency.
By embracing advanced techniques and continual skill enhancement, production engineers can harness these machines’ full potential, pushing the boundaries of what is possible in manufacturing complex and high-precision components.
Adapting to the challenges and considering the strategic investments in multi-axis machining technology and training can spell success for companies in the competitive and ever-evolving landscape of precision machining.
資料ダウンロード
QCD管理受発注クラウド「newji」は、受発注部門で必要なQCD管理全てを備えた、現場特化型兼クラウド型の今世紀最高の受発注管理システムとなります。
ユーザー登録
受発注業務の効率化だけでなく、システムを導入することで、コスト削減や製品・資材のステータス可視化のほか、属人化していた受発注情報の共有化による内部不正防止や統制にも役立ちます。
NEWJI DX
製造業に特化したデジタルトランスフォーメーション(DX)の実現を目指す請負開発型のコンサルティングサービスです。AI、iPaaS、および先端の技術を駆使して、製造プロセスの効率化、業務効率化、チームワーク強化、コスト削減、品質向上を実現します。このサービスは、製造業の課題を深く理解し、それに対する最適なデジタルソリューションを提供することで、企業が持続的な成長とイノベーションを達成できるようサポートします。
製造業ニュース解説
製造業、主に購買・調達部門にお勤めの方々に向けた情報を配信しております。
新任の方やベテランの方、管理職を対象とした幅広いコンテンツをご用意しております。
お問い合わせ
コストダウンが利益に直結する術だと理解していても、なかなか前に進めることができない状況。そんな時は、newjiのコストダウン自動化機能で大きく利益貢献しよう!
(β版非公開)