- お役立ち記事
- For production engineers in the precision machinery industry! Points for correcting errors in CNC machines and maintaining machining accuracy
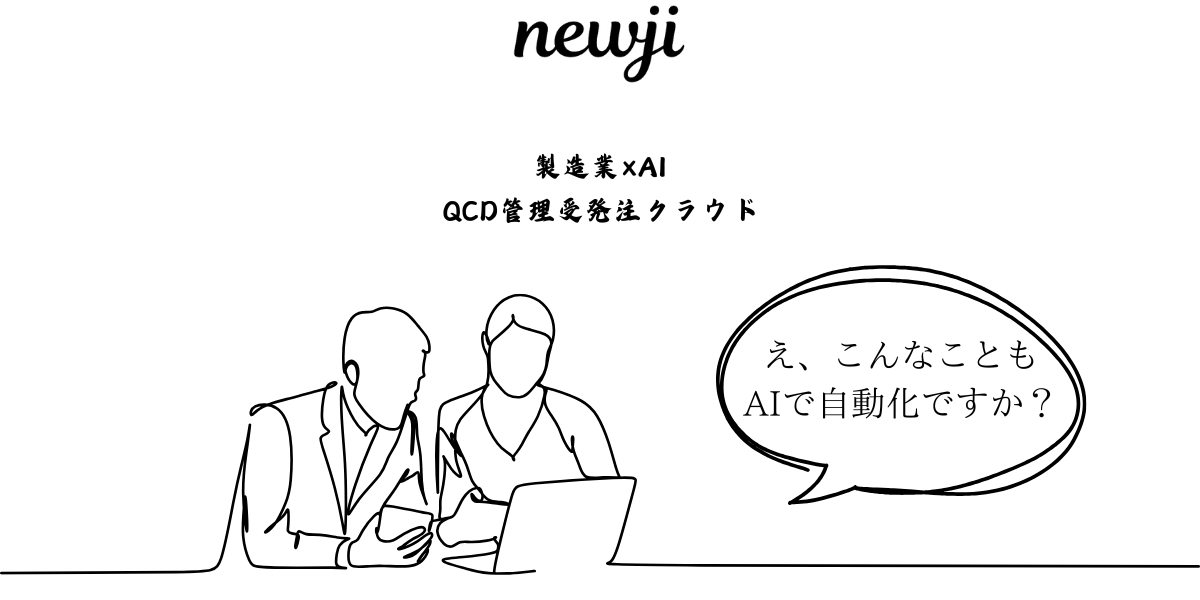
For production engineers in the precision machinery industry! Points for correcting errors in CNC machines and maintaining machining accuracy
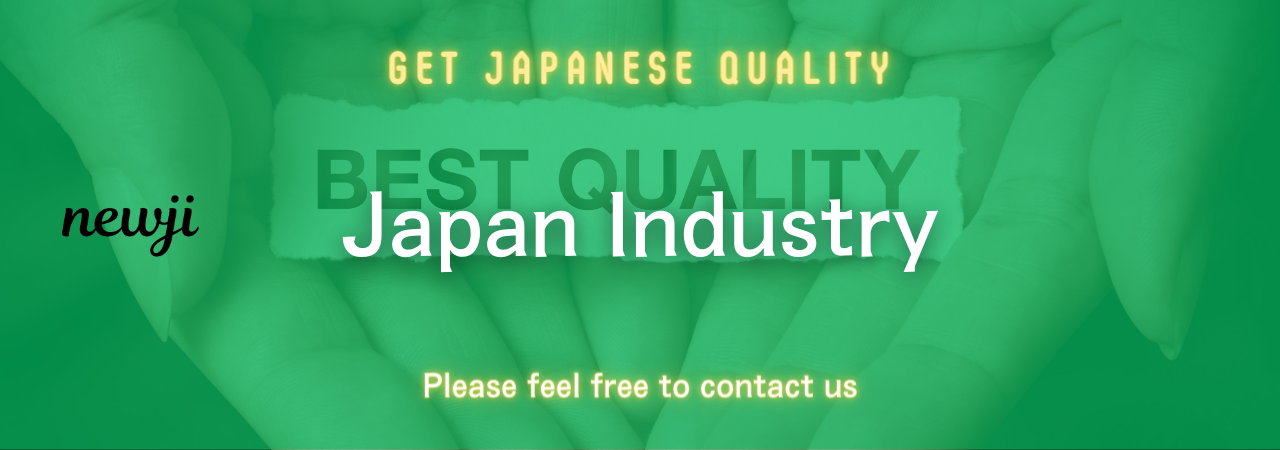
目次
Understanding CNC Machines in Precision Machinery
CNC machines, or Computer Numerical Control machines, are a staple in the precision machinery industry.
They provide high levels of accuracy and efficiency in manufacturing processes.
However, even with advanced technology, errors can occur.
Understanding how to correct these errors and maintain machining accuracy is crucial for production engineers.
Common Errors in CNC Machines
Before tackling the solutions, it is vital to identify the common errors that can occur in CNC machines.
These errors might arise due to various factors such as mechanical issues, programming mistakes, or external disturbances.
1. **Mechanical Errors**: These include misalignment of machine components, wear and tear of machine parts, or issues with the machine’s drive systems.
2. **Programming Errors**: Inaccurate coding can lead to incorrect tool paths or command functions, resulting in faulty production.
3. **Tool Wear and Breakage**: Tools may become dull or break due to excessive use, improper handling, or incorrect material selection.
4. **Thermal Expansion**: Heat generated from machine operations might cause components to expand, affecting the precision of machining.
5. **External Factors**: Vibrations, power fluctuations, or environmental conditions can lead to deviations in performance.
Strategies for Correcting CNC Machine Errors
Addressing errors in CNC machines promptly is crucial to minimize downtimes and maintain production quality.
Regular Maintenance and Calibration
One of the foremost strategies is to establish a routine for regular maintenance and calibration of machines.
This involves checking machine alignment, tightening loose components, and ensuring that the calibration is set to the manufacturer’s specifications.
Routine checks help in identifying potential issues before they turn into significant problems.
Optimize Programming Techniques
By ensuring that all programming inputs are accurate and well-understood, you can avoid many common errors.
Training sessions for machine operators on the latest CNC programming standards and providing them with up-to-date manuals can enhance their skills.
Additionally, utilizing simulation software to test programs before actual execution helps prevent costly mistakes.
Monitor Tool Conditions
Regular inspection of tools is necessary to prevent wear-related errors.
Use high-quality tooling materials and replace them as needed.
Integrating tool break detection systems can also aid in minimizing disruptions due to tool failure.
Heat Management
Implementing efficient cooling systems can help manage the thermal expansion of machine parts.
Ensure that there is adequate ventilation in the workspace and consider using coolant systems during operations to mitigate the heat generated.
Addressing External Factors
Minimize environmental limitations by setting machines on stable surfaces and in locations that are less susceptible to vibrations and temperature changes.
Install power stabilizers to protect against voltage fluctuations.
Maintaining Precision in Machining
Aside from correcting errors, maintaining machining accuracy is a proactive approach that ensures ongoing precision in production.
Implement Precision Control Systems
Modern CNC machines come equipped with precision control systems that enhance machining accuracy.
These systems include advanced motion controllers and feedback mechanisms that continuously monitor and adjust tool positions.
Use High-Quality Raw Materials
The quality of raw materials significantly impacts the final product’s precision.
Choose high-grade materials that suit your production requirements and ensure they meet industry standards.
Adopt Best Practices in Setup
Consistency in setup processes reduces the variability in production.
Standardizing machine setup protocols ensures that all operators follow the same procedures, reducing the risk of setup errors.
Staff Training and Development
Investing in comprehensive training programs for machinists and production staff can enhance their understanding of CNC machines.
Focus on practical skills and problem-solving techniques that can aid in recognizing and addressing potential issues quickly.
Regular Performance Audits
Conduct regular audits of the machines and production processes to ensure everything aligns with set performance standards.
This can help catch deviations early on and implement corrective measures efficiently.
Conclusion
For production engineers in the precision machinery industry, mastering the art of correcting errors in CNC machines and maintaining machining accuracy is vital.
It ensures the production of high-quality components and minimizes downtime.
By understanding common errors, applying effective strategies, and continuously improving practices, businesses can optimize their CNC machine operations for sustained success.
Remember, staying proactive and informed about the latest advancements in CNC technologies will keep your processes efficient and precise.
資料ダウンロード
QCD調達購買管理クラウド「newji」は、調達購買部門で必要なQCD管理全てを備えた、現場特化型兼クラウド型の今世紀最高の購買管理システムとなります。
ユーザー登録
調達購買業務の効率化だけでなく、システムを導入することで、コスト削減や製品・資材のステータス可視化のほか、属人化していた購買情報の共有化による内部不正防止や統制にも役立ちます。
NEWJI DX
製造業に特化したデジタルトランスフォーメーション(DX)の実現を目指す請負開発型のコンサルティングサービスです。AI、iPaaS、および先端の技術を駆使して、製造プロセスの効率化、業務効率化、チームワーク強化、コスト削減、品質向上を実現します。このサービスは、製造業の課題を深く理解し、それに対する最適なデジタルソリューションを提供することで、企業が持続的な成長とイノベーションを達成できるようサポートします。
オンライン講座
製造業、主に購買・調達部門にお勤めの方々に向けた情報を配信しております。
新任の方やベテランの方、管理職を対象とした幅広いコンテンツをご用意しております。
お問い合わせ
コストダウンが利益に直結する術だと理解していても、なかなか前に進めることができない状況。そんな時は、newjiのコストダウン自動化機能で大きく利益貢献しよう!
(Β版非公開)