- お役立ち記事
- For production engineers in the sensor manufacturing industry for automatic sorting machines! Design method that achieves both high precision and impact resistance
月間76,176名の
製造業ご担当者様が閲覧しています*
*2025年3月31日現在のGoogle Analyticsのデータより
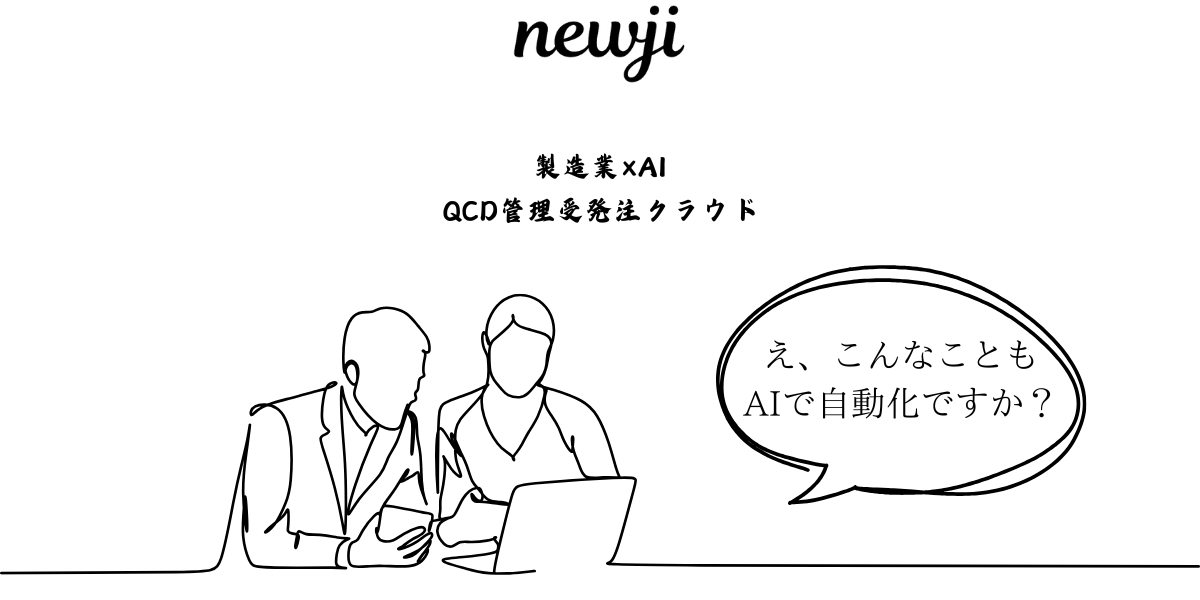
For production engineers in the sensor manufacturing industry for automatic sorting machines! Design method that achieves both high precision and impact resistance
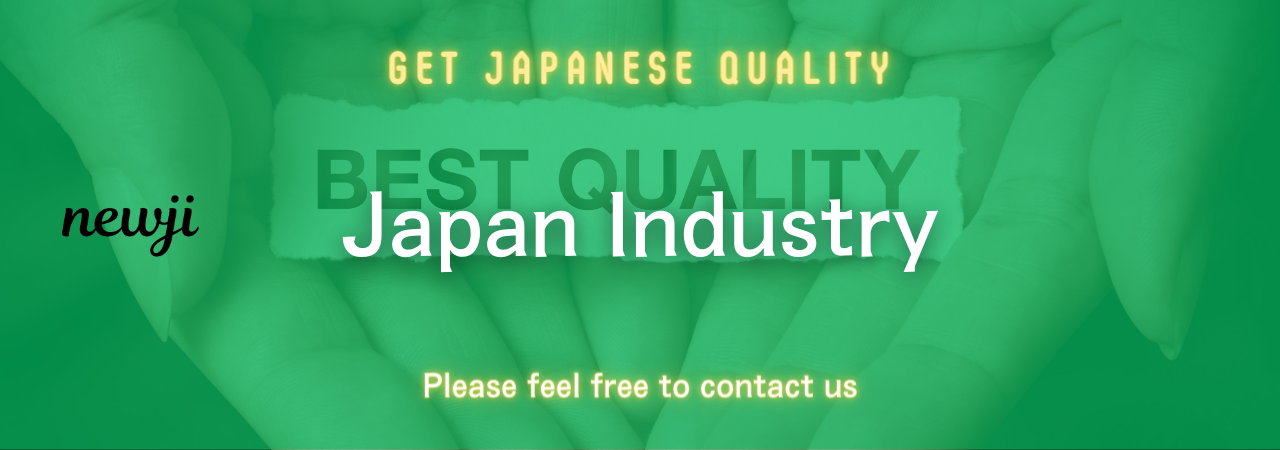
目次
Understanding the Challenges in Sensor Design for Automatic Sorting Machines
In the realm of automatic sorting machines, sensors play a pivotal role in ensuring high precision and reliability during operation.
These machines require sensors that can accurately detect, sort, and classify various objects even at high speeds.
Designing sensors for such applications presents unique challenges, particularly in achieving a balance between high precision and impact resistance.
High precision is crucial for correctly identifying and sorting objects.
However, the sensor’s ability to withstand physical impact and environmental stress is equally important.
This is because sorting machines often operate in harsh environments where sensors may be exposed to vibrations, shocks, and extreme temperatures.
Adapting sensor design to overcome these challenges is critical for production engineers in the sensor manufacturing industry.
The aim is to develop robust sensors that maintain performance without compromising on precision.
Here, we’ll explore various design methods and considerations that engineers can utilize to achieve this delicate balance.
Key Design Considerations for High Precision Sensors
In designing sensors for automatic sorting machines, ensuring high precision is paramount.
Precision affects not only the accuracy of the sorted output but also the efficiency of the entire operation.
Below are some of the primary considerations for achieving high precision in sensor design.
Choice of Sensing Technology
The type of sensing technology employed greatly influences the precision of a sensor.
Different technologies, such as optical, inductive, capacitive, or ultrasonic sensors, offer varying levels of precision and reliability.
Optical sensors, for example, provide high accuracy and fast response times, making them suitable for identifying small objects.
Production engineers must evaluate the requirements of the sorting machine and select the appropriate technology that best suits the application’s needs.
Sensitivity and Resolution
Sensitivity refers to the sensor’s ability to detect minute changes in the object being sorted.
Increased sensitivity can lead to higher resolution, allowing the sensor to distinguish finer variations between similar objects.
When designing sensors, engineers should consider integrating components that enhance sensitivity without causing false readings.
Calibration and Error Correction
High precision sensors benefit significantly from calibration and error correction mechanisms.
Implementing self-calibration features can help maintain accuracy over time, compensating for any drift or degradation in sensor performance.
Error correction algorithms can also be embedded to resolve inaccuracies, further enhancing precision.
Design Methods for Enhanced Impact Resistance
While high precision is essential, impact resistance is critical to ensuring sensor longevity and reliability, particularly in demanding environments.
Impact resistance prevents damage from physical shocks, vibrations, and temperature fluctuations.
Here are several methods to enhance the impact resistance of sensors.
Robust Material Selection
The choice of materials used in sensor construction massively influences their durability and impact resistance.
Materials such as high-grade silicone, toughened glass, and stainless steel can provide enhanced protection and resistance to physical damage.
Additionally, coating techniques can be applied to create an extra protective layer around the sensor’s sensitive components.
Mechanical Design Features
Incorporating specific mechanical design features can significantly boost the impact resistance of sensors.
Structural enhancements such as shock absorbers, dampening mounts, and flexible joints can reduce the transmission of vibrations and shocks to the sensor’s core.
Innovative casing designs can also help dissipate kinetic energy away from critical components.
Environmental Sealing and Protection
Sensors operating in automatic sorting machines need protection against environmental factors such as dust, moisture, and temperature extremes.
Sealing techniques, including gaskets and O-rings, protect the sensor from ingress of unwanted particles and liquids.
Temperature-resistant materials and thermal management systems ensure sensor stability even in fluctuating temperature conditions.
Balancing Precision and Impact Resistance
Achieving a balance between high precision and impact resistance requires a holistic design approach.
Production engineers should focus on a comprehensive understanding of both the application’s operational requirements and the limitations of available technologies.
Integrated System Approach
A systems approach involves integration and collaboration between various sensor components and the sorting machine as a whole.
Engineers should aim for seamless compatibility, ensuring that the sensor design is optimized for the entire system rather than as an isolated component.
Iterative Testing and Feedback
Continuous testing and feedback loops are vital in refining sensor design.
Prototype sensors should be subjected to rigorous testing under realistic conditions to evaluate both precision and impact resistance.
Feedback from these tests can inform design improvements and adjustments.
Future Trends in Sensor Design for Automatic Sorting Machines
The field of sensor design continues to evolve, with technological advancements opening up new possibilities for improving precision and impact resistance.
Here are some promising trends to watch in the future.
Smart Sensors and IoT Integration
The integration of smart sensors with IoT technologies allows for real-time data analysis and performance monitoring.
This advancement enables more accurate and dynamic precision control, as well as predictive maintenance strategies for enhanced impact resistance.
Advanced Materials and Nanotechnology
Research into advanced materials, including nanotechnology, presents opportunities to create sensors with superior properties.
These materials promise to deliver enhanced sensitivity and durability, pushing the boundaries of what is currently achievable.
Machine Learning and AI
The incorporation of machine learning and AI can lead to more intelligent sensor systems capable of self-optimization.
These technologies can improve both precision and impact resistance by enabling the sensor to adapt to varying conditions.
In conclusion, designing sensors for automatic sorting machines that achieve high precision and impact resistance is a complex challenge for production engineers.
By leveraging advances in technology, material science, and design methodology, engineers can develop sensors that excel in both performance and durability.
資料ダウンロード
QCD管理受発注クラウド「newji」は、受発注部門で必要なQCD管理全てを備えた、現場特化型兼クラウド型の今世紀最高の受発注管理システムとなります。
ユーザー登録
受発注業務の効率化だけでなく、システムを導入することで、コスト削減や製品・資材のステータス可視化のほか、属人化していた受発注情報の共有化による内部不正防止や統制にも役立ちます。
NEWJI DX
製造業に特化したデジタルトランスフォーメーション(DX)の実現を目指す請負開発型のコンサルティングサービスです。AI、iPaaS、および先端の技術を駆使して、製造プロセスの効率化、業務効率化、チームワーク強化、コスト削減、品質向上を実現します。このサービスは、製造業の課題を深く理解し、それに対する最適なデジタルソリューションを提供することで、企業が持続的な成長とイノベーションを達成できるようサポートします。
製造業ニュース解説
製造業、主に購買・調達部門にお勤めの方々に向けた情報を配信しております。
新任の方やベテランの方、管理職を対象とした幅広いコンテンツをご用意しております。
お問い合わせ
コストダウンが利益に直結する術だと理解していても、なかなか前に進めることができない状況。そんな時は、newjiのコストダウン自動化機能で大きく利益貢献しよう!
(β版非公開)