- お役立ち記事
- For production engineers in the slag groove liner manufacturing industry for steel furnaces! Material technology to achieve both heat resistance and impact resistance
For production engineers in the slag groove liner manufacturing industry for steel furnaces! Material technology to achieve both heat resistance and impact resistance
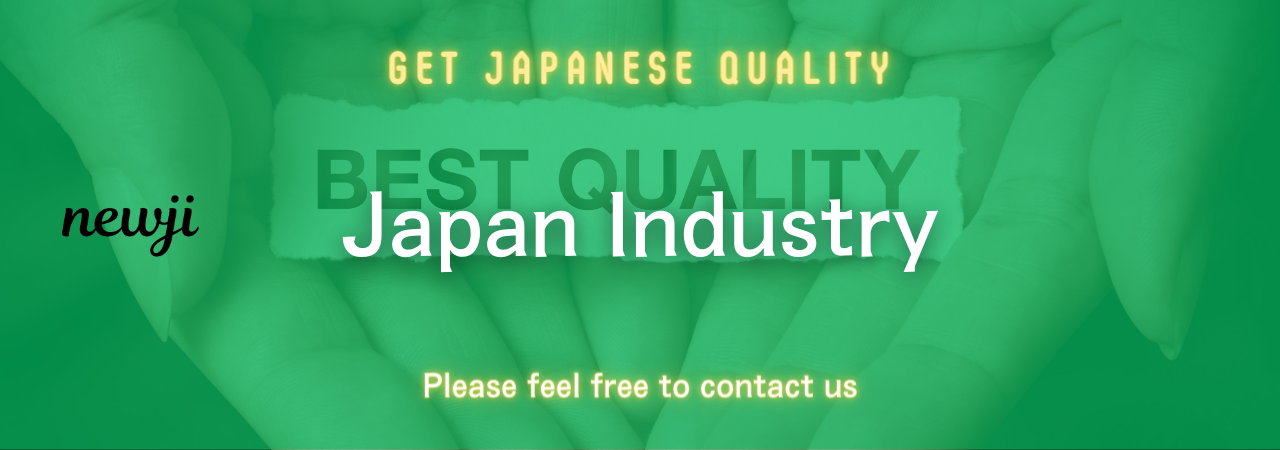
目次
Introduction to Slag Groove Liner Manufacturing
In the world of steel furnace production, slag groove liners play an essential role in ensuring the efficiency and longevity of the furnace operations.
These components must withstand high temperatures and endure significant impacts during processes.
Advanced material technology is required to achieve both heat resistance and impact resistance, which are critical for maintaining production standards and safety.
For production engineers working in the slag groove liner manufacturing industry, understanding material technology is key to innovation and efficiency.
In this article, we will delve into modern materials used for manufacturing slag groove liners and explore how advancements in technology are making production processes more efficient, cost-effective, and reliable.
Understanding Slag Groove Liners
Slag groove liners are a crucial part of steel making facilities.
They help in channeling the waste materials, known as slag, away from the molten metal during production.
This process requires liners to endure extreme conditions, such as elevated temperatures and high mechanical stress from molten slag impact.
Failing to utilize the appropriate materials for these liners can lead to breakdowns, frequent replacements, and costly downtime.
As such, selecting the right material technology is vital for manufacturing robust, durable, and efficient slag groove liners.
Material Technology for Heat Resistance
One of the key challenges facing production engineers is developing materials that offer superior heat resistance.
Slag groove liners are constantly exposed to molten metal and slag at extreme temperatures, often exceeding 1600 degrees Celsius.
Ceramics have long been a popular choice for their high melting points and thermal stability.
Alumina and zirconia ceramics, in particular, offer excellent thermal resistance.
Additionally, certain advanced ceramics, such as silicon carbide (SiC) and silicon nitride (Si3N4), provide even higher thermal performance and are increasingly used in liner production.
Metallic alloys, such as nickel, chromium, and molybdenum-based superalloys, are also excellent choices for high-temperature environments.
These alloys are engineered to withstand the thermal cycles commonly experienced within the steelmaking furnace without degrading.
Innovative Coatings for Enhanced Heat Resistance
In recent years, nanotechnology and advanced coatings have driven major improvements in heat resistance for slag groove liners.
Thermal barrier coatings (TBCs), utilizing nanostructured ceramics, are applied to the surface of liners to improve their thermal resistance.
These coatings help insulate the liner material from direct heat exposure, prolonging its lifespan and improving performance.
TBCs are typically made from yttria-stabilized zirconia (YSZ), which is known for its ability to withstand high temperatures.
These coatings are effectively used in various industries, including aerospace and nuclear reactors, making them well-suited for application in slag groove liner manufacturing.
Material Technology for Impact Resistance
Equally important to heat resistance is impact resistance, which ensures that slag groove liners can withstand mechanical stress without fracturing or wearing down rapidly.
To achieve this, manufacturers must consider not only the base material used but also the material’s design and structure.
Steel alloys remain a popular choice due to their excellent impact resistance.
However, advancements in composite materials have opened new avenues for production engineers.
Ceramic matrix composites (CMCs) blend the heat resistance of ceramics with impact resistance, making them a versatile choice for harsh furnace environments.
Polymer-based composites, reinforced with high-strength fibers such as carbon or aramid, also offer significant impact resistance benefits.
These materials are lightweight, durable, and can absorb and dissipate impact energy efficiently, thus reducing wear and tear on the liners.
Design Innovations for Optimal Impact Resistance
In addition to material selection, design innovations play a crucial role in enhancing impact resistance.
Engineers are exploring lattice structures and honeycomb geometries that optimize the material’s natural resistance to impact.
Furthermore, tailoring the grain structure and texture of crystalline materials can enhance their mechanical properties, resulting in improved impact resistance.
Electron beam melting (EBM) and selective laser sintering (SLS) are two advanced additive manufacturing processes that enable engineers to customize liner designs according to their specific requirements.
Balancing Heat and Impact Resistance
Achieving an optimal balance between heat resistance and impact resistance is essential for manufacturing effective slag groove liners.
Understanding the operating conditions of the steel furnace is key to selecting the right material combination.
Engineers often conduct lifecycle analysis and performance testing under simulated working conditions to identify potential weaknesses in liner materials.
This helps in fine-tuning both the material composition and design to meet industrial demands.
Emerging technologies, such as artificial intelligence (AI) and machine learning, are further revolutionizing this process by predicting material behavior under varying thermal and mechanical conditions.
These tools enable production engineers to expedite material testing and optimize their design processes.
Conclusion
In the constantly evolving field of steel furnace production, improving slag groove liners is vital to drive efficiency and reduce operational costs.
The latest advancements in material technology are pushing the boundaries of what was previously considered possible, giving production engineers new tools to enhance both heat and impact resistance in these critical components.
By utilizing modern ceramic and composite materials, integrating innovative coatings, and embracing cutting-edge design technologies, production engineers can manufacture slag groove liners that are ready to face the demanding conditions within steel furnaces.
Through continuous research and development, and by leveraging the power of AI and machine learning, the industry can anticipate even greater breakthroughs in liner performance, helping the steel manufacturing process become more efficient, cost-effective, and sustainable than ever before.
資料ダウンロード
QCD調達購買管理クラウド「newji」は、調達購買部門で必要なQCD管理全てを備えた、現場特化型兼クラウド型の今世紀最高の購買管理システムとなります。
ユーザー登録
調達購買業務の効率化だけでなく、システムを導入することで、コスト削減や製品・資材のステータス可視化のほか、属人化していた購買情報の共有化による内部不正防止や統制にも役立ちます。
NEWJI DX
製造業に特化したデジタルトランスフォーメーション(DX)の実現を目指す請負開発型のコンサルティングサービスです。AI、iPaaS、および先端の技術を駆使して、製造プロセスの効率化、業務効率化、チームワーク強化、コスト削減、品質向上を実現します。このサービスは、製造業の課題を深く理解し、それに対する最適なデジタルソリューションを提供することで、企業が持続的な成長とイノベーションを達成できるようサポートします。
オンライン講座
製造業、主に購買・調達部門にお勤めの方々に向けた情報を配信しております。
新任の方やベテランの方、管理職を対象とした幅広いコンテンツをご用意しております。
お問い合わせ
コストダウンが利益に直結する術だと理解していても、なかなか前に進めることができない状況。そんな時は、newjiのコストダウン自動化機能で大きく利益貢献しよう!
(Β版非公開)