- お役立ち記事
- For production engineers in the steel industry! How to prevent twisting of steel materials using twist-free processing technology
月間76,176名の
製造業ご担当者様が閲覧しています*
*2025年3月31日現在のGoogle Analyticsのデータより
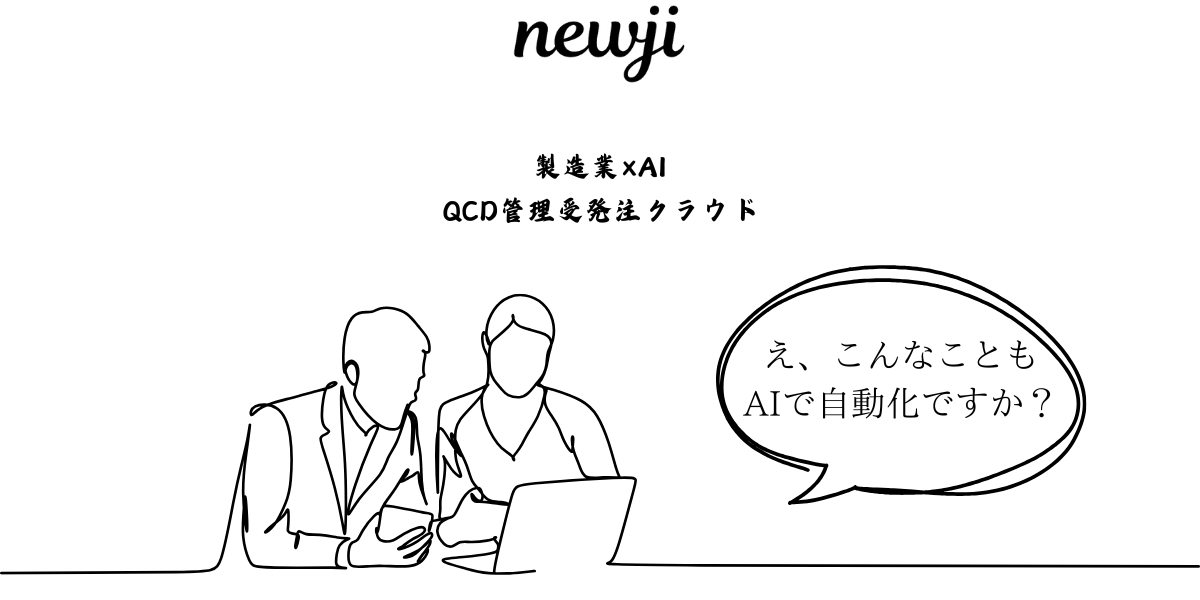
For production engineers in the steel industry! How to prevent twisting of steel materials using twist-free processing technology
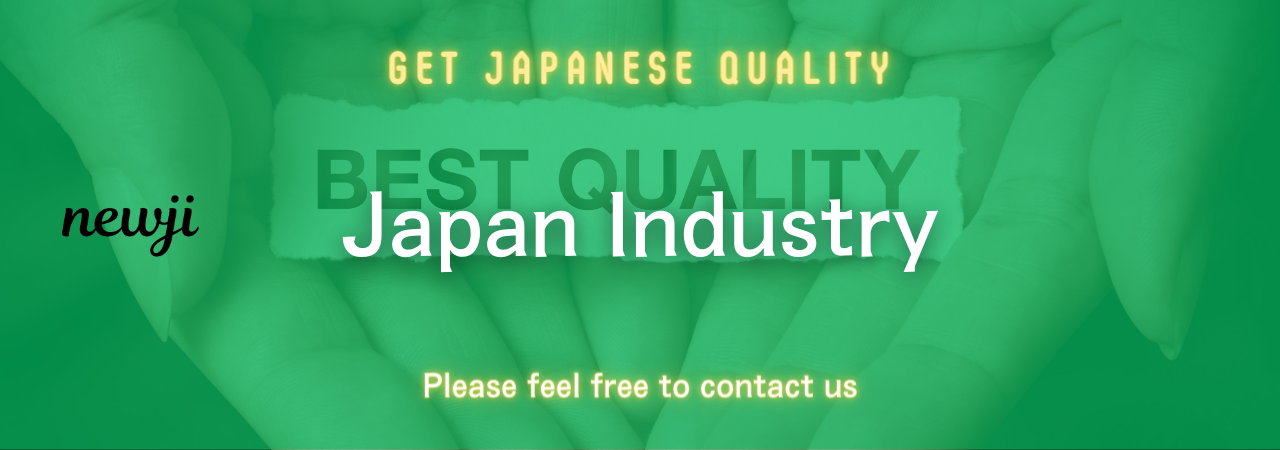
目次
Understanding the Challenge of Twisting in Steel Production
Steel production is an intricate process that involves various stages, from raw material handling to the final shaping and treatment of the product.
One common issue faced by production engineers in the steel industry is the twisting of steel materials.
Twisting can occur during rolling, cooling, or even when the material is being handled or stored.
This can significantly affect the quality and usability of the final product, leading to potential financial losses and negative impacts on a company’s reputation.
Twisting occurs due to uneven temperature distribution, residual stresses within the material, improper handling, or even incorrect machinery settings.
Identifying and understanding the causes of twisting is crucial for implementing effective solutions.
By addressing these issues, production engineers can enhance efficiency, reduce waste, and maintain high-quality standards in steel manufacturing.
The Importance of Twist-Free Processing Technology
Twist-free processing technology has become an essential tool in the steel industry.
It offers significant advantages in maintaining the accuracy and integrity of steel products.
This technology helps streamline operations by minimizing defects and optimizing the uniformity of the steel output.
By reducing the instances of twisting, companies can ensure that the steel meets specific dimensional and mechanical properties required by customers.
The importance of twist-free processing technology cannot be overstated.
Not only does it improve the efficiency of production processes, but it also plays a pivotal role in increasing customer satisfaction and trust.
Clients demand high-quality steel products that meet stringent specifications, and employing twist-free technology ensures that these standards are consistently met.
Exploring Twist-Free Processing Techniques
There are several techniques utilized in twist-free processing, each with unique benefits tailored to specific types of steel and production requirements.
Here are some of the most effective methods:
Controlled Cooling
One of the primary causes of twisting is uneven cooling.
By implementing controlled cooling techniques, manufacturers can ensure that the steel is cooled evenly across the entire surface.
This helps in maintaining consistent structure and strength throughout the product.
Techniques such as air-mist cooling or laminar flow cooling systems have been effective in reducing temperature gradients that lead to twisting.
Precision Rolling
Precision rolling is another method used in twist-free processing.
It involves closely monitoring and adjusting the rolling process to ensure uniform thickness and flatness of the steel material.
Precision rolling machinery, equipped with advanced controls, reduces the chances of deviations that result in twisting.
This not only enhances the product’s quality but also improves the efficiency of the production line.
Stress Relieving Processes
Residual stresses in steel can lead to twisting, even after the product has been formed.
Stress-relieving processes, such as annealing or tempering, help reduce these stresses.
By heat-treating the steel at specific temperatures, production engineers can eliminate internal strains, resulting in a more stable and twist-free product.
This is particularly beneficial in applications where precise measurements are critical.
Monitoring and Automation
Advancements in technology have allowed for greater automation and monitoring capabilities in steel production.
Utilizing sensors and analytics, production lines can be equipped with real-time monitoring systems that detect twisting as it occurs.
Automation can then be used to adjust machine settings on-the-fly to correct any deviations, reducing waste and improving production consistency.
Implementing Best Practices in Steel Production
To successfully prevent twisting in steel materials, production engineers should implement a series of best practices focused on optimization and quality control.
Here are several key practices to consider:
Regular Equipment Maintenance
Ensure that all machinery and equipment involved in the production process are regularly maintained and calibrated.
Regular maintenance reduces the risk of mechanical failures that could lead to improper rolling and cooling practices, thus minimizing twisting incidents.
Employee Training and Development
Investing in employee training ensures that your workforce is knowledgeable about the latest twist-free processing technologies and techniques.
Continuous education and skill development will help them effectively recognize and address twisting issues in real-time.
Data-Driven Approaches
Leverage data analytics to assess production line performance and identify areas where twisting might occur.
Data-driven approaches allow engineers to predict potential issues before they arise and implement preventative measures to mitigate risks.
Quality Assurance Protocols
Develop robust quality assurance protocols to regularly inspect and test steel products for twisting.
Ensuring that rigorous testing is part of the production line will help in early detection and correction of defects, maintaining high-quality standards throughout.
Conclusion
Twist-free processing technology is a vital part of modern steel production, offering significant benefits in quality control and production efficiency.
By understanding the causes of twisting and employing effective techniques such as controlled cooling, precision rolling, stress relieving processes, and utilizing advanced monitoring and automation, production engineers can effectively prevent twisting.
Implementing best practices in equipment maintenance, employee training, data analysis, and quality assurance ensures that steel manufacturers can consistently deliver superior products to their clients.
By addressing these critical elements, the steel industry can reduce waste, improve efficiency, and maintain a reputation for excellence in steel production.
資料ダウンロード
QCD管理受発注クラウド「newji」は、受発注部門で必要なQCD管理全てを備えた、現場特化型兼クラウド型の今世紀最高の受発注管理システムとなります。
ユーザー登録
受発注業務の効率化だけでなく、システムを導入することで、コスト削減や製品・資材のステータス可視化のほか、属人化していた受発注情報の共有化による内部不正防止や統制にも役立ちます。
NEWJI DX
製造業に特化したデジタルトランスフォーメーション(DX)の実現を目指す請負開発型のコンサルティングサービスです。AI、iPaaS、および先端の技術を駆使して、製造プロセスの効率化、業務効率化、チームワーク強化、コスト削減、品質向上を実現します。このサービスは、製造業の課題を深く理解し、それに対する最適なデジタルソリューションを提供することで、企業が持続的な成長とイノベーションを達成できるようサポートします。
製造業ニュース解説
製造業、主に購買・調達部門にお勤めの方々に向けた情報を配信しております。
新任の方やベテランの方、管理職を対象とした幅広いコンテンツをご用意しております。
お問い合わせ
コストダウンが利益に直結する術だと理解していても、なかなか前に進めることができない状況。そんな時は、newjiのコストダウン自動化機能で大きく利益貢献しよう!
(β版非公開)