- お役立ち記事
- For production engineers in the tissue case manufacturing industry! Manufacturing process that achieves both compact design and durability
For production engineers in the tissue case manufacturing industry! Manufacturing process that achieves both compact design and durability
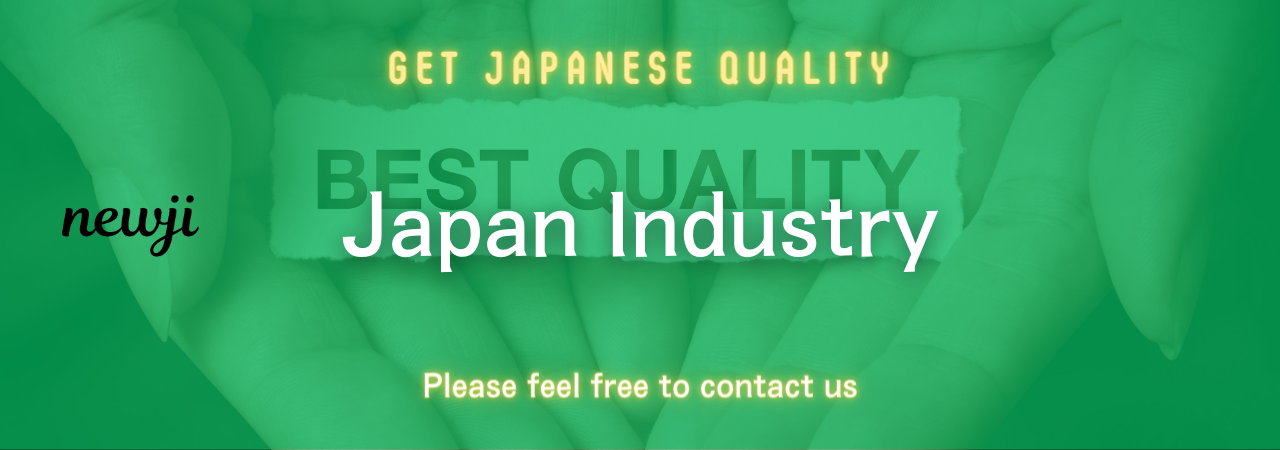
目次
Introduction to Tissue Case Manufacturing
The tissue case manufacturing industry is a specialized sector that combines creativity with functionality to produce essential everyday items.
As production engineers in this field, one of the primary objectives is to create tissue cases that are both compact in design and durable in construction.
The challenge lies in balancing aesthetics and functionality while ensuring cost-efficiency and sustainability.
In this article, we’ll explore the manufacturing process that strikes this balance and discuss strategies to achieve excellence in production.
Understanding the Demand for Compact and Durable Designs
Today’s consumers are increasingly drawn to products that offer convenience without compromising on quality.
Compact tissue cases meet the demand for portability, fitting seamlessly into various spaces, whether in a home, car, or office.
Durability, on the other hand, ensures that these cases can withstand daily use, maintaining their functionality and aesthetic appeal over time.
Thus, manufacturers must focus on innovative materials and designs that fulfill these dual requirements.
Material Selection: The Cornerstone of Durability
Selecting the right materials is critical for achieving durability in tissue case manufacturing.
The choice of material affects not only the lifespan of the product but also its environmental impact and cost.
Common materials include:
Plastics
Plastics are widely used due to their versatility, lightweight nature, and cost-effectiveness.
Advanced polymers can be engineered to offer significant strength, impact resistance, and flexibility.
Engineering-grade plastics like ABS and polycarbonate are popular choices for manufacturers aiming for a balance of these characteristics.
Metals
For premium tissue cases, metals like aluminum and stainless steel provide superior durability and a sleek aesthetic.
These materials are resistant to corrosion and wear, making them ideal for high-end designs.
However, production engineers must consider the weight and cost implications when opting for metal.
Wood and Composites
Wood offers a classic and eco-friendly option, appealing to consumers seeking natural aesthetics.
Composites, which combine natural fibers with resins, provide enhanced durability and moisture resistance.
These materials require careful design and manufacturing processes to prevent warping and ensure long-lasting performance.
Innovative Design for Compact Solutions
Creating a compact design without sacrificing durability involves innovative engineering and smart design choices.
Production engineers can incorporate features that optimize space and enhance usability.
Foldable and Collapsible Designs
Incorporating foldable or collapsible mechanisms can dramatically reduce the storage footprint of tissue cases.
These designs are particularly useful for portable or travel-sized products, allowing consumers to pack them easily when on the move.
Integrated Storage Compartments
Designing tissue cases with additional compartments can enhance functionality.
These compartments can store small items such as wet wipes or hand sanitizers, adding value to the product while maintaining its compact size.
Minimalist Aesthetics
Adopting a minimalist design approach can help reduce material usage and production costs.
Simple, sleek lines not only appeal to modern consumer tastes but also streamline manufacturing processes, contributing to overall efficiency.
Sustainable Manufacturing Practices
Sustainability is a growing concern for production engineers and consumers alike.
Implementing eco-friendly practices in tissue case manufacturing can reduce environmental impact and appeal to environmentally conscious buyers.
Recycling and Reusing Materials
Utilizing recycled materials not only conserves resources but also aligns with consumer demand for green products.
Production engineers can work to source recycled plastics or metals, incorporating them into new designs while maintaining quality and durability.
Energy-Efficient Production
Optimizing production processes to minimize energy consumption can lead to significant cost savings and environmental benefits.
Implementing energy-efficient machinery and adopting lean manufacturing principles help reduce waste and emissions.
Innovative Finishing Techniques
Exploring sustainable finishing techniques, such as water-based coatings or low-VOC paints, can minimize the ecological footprint of manufacturing.
Such practices not only protect the environment but also ensure safe indoor air quality for users.
Quality Control and Testing
To ensure that tissue cases meet the desired standards of compactness and durability, rigorous quality control procedures must be in place.
These processes ensure consistency, reliability, and customer satisfaction.
Stress and Durability Testing
Conducting stress tests simulates real-world conditions to evaluate the product’s durability.
These tests can identify potential weaknesses in the design or material choice, allowing production engineers to make necessary adjustments before mass production.
User Feedback Integration
Gathering and incorporating user feedback can provide valuable insights into design improvements and functional enhancements.
Production engineers should establish mechanisms for collecting and analyzing this data to drive continuous product development.
Conclusion: Achieving Excellence in Tissue Case Manufacturing
Manufacturing tissue cases that combine compact design with durability requires a harmonious blend of material science, innovative design, and sustainable practices.
Production engineers play a pivotal role in guiding the development process, ensuring each product meets market demands while maintaining profitability and environmental responsibility.
By adhering to best practices in material selection, design innovation, sustainable manufacturing, and quality control, manufacturers can produce tissue cases that satisfy consumer needs and stand the test of time.
As the industry continues to evolve, production engineers will be at the forefront, crafting solutions that marry form with function in the most efficient and eco-friendly ways possible.
資料ダウンロード
QCD調達購買管理クラウド「newji」は、調達購買部門で必要なQCD管理全てを備えた、現場特化型兼クラウド型の今世紀最高の購買管理システムとなります。
ユーザー登録
調達購買業務の効率化だけでなく、システムを導入することで、コスト削減や製品・資材のステータス可視化のほか、属人化していた購買情報の共有化による内部不正防止や統制にも役立ちます。
NEWJI DX
製造業に特化したデジタルトランスフォーメーション(DX)の実現を目指す請負開発型のコンサルティングサービスです。AI、iPaaS、および先端の技術を駆使して、製造プロセスの効率化、業務効率化、チームワーク強化、コスト削減、品質向上を実現します。このサービスは、製造業の課題を深く理解し、それに対する最適なデジタルソリューションを提供することで、企業が持続的な成長とイノベーションを達成できるようサポートします。
オンライン講座
製造業、主に購買・調達部門にお勤めの方々に向けた情報を配信しております。
新任の方やベテランの方、管理職を対象とした幅広いコンテンツをご用意しております。
お問い合わせ
コストダウンが利益に直結する術だと理解していても、なかなか前に進めることができない状況。そんな時は、newjiのコストダウン自動化機能で大きく利益貢献しよう!
(Β版非公開)