- お役立ち記事
- For production engineers in the toothbrush manufacturing industry! Processing methods to optimize hair hardness and durability
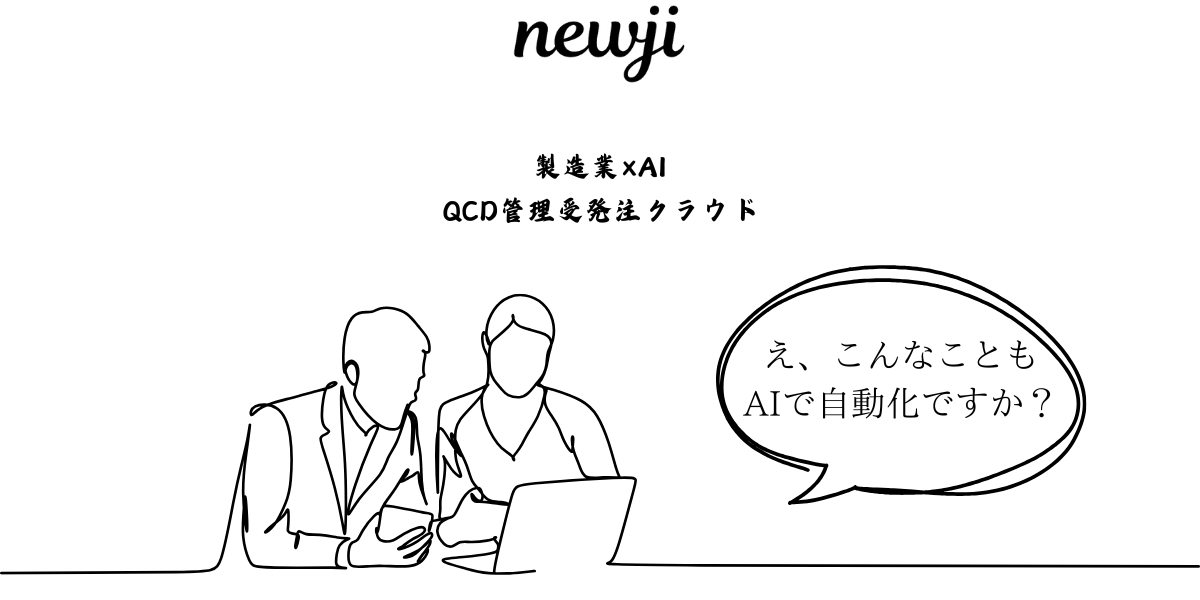
For production engineers in the toothbrush manufacturing industry! Processing methods to optimize hair hardness and durability
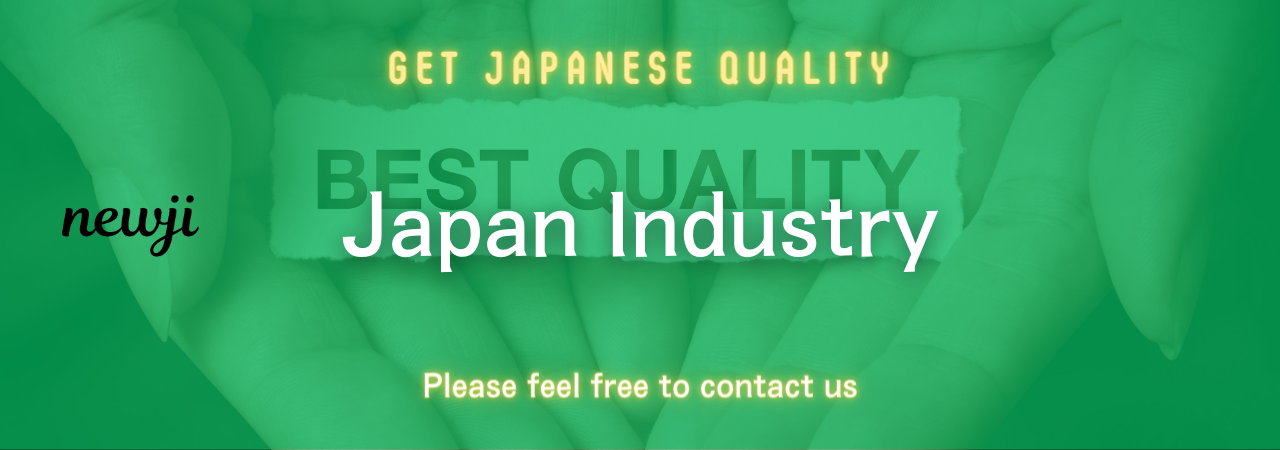
目次
Understanding the Basics of Toothbrush Manufacturing
Toothbrush manufacturing is a fascinating industry that combines art and science.
From ergonomic designs to the intricacies of bristle arrangements, several elements constitute the making of a functional toothbrush.
One crucial aspect that often requires keen attention is the processing methods to optimize the hardness and durability of the toothbrush bristles.
As production engineers, focusing on the technical methodologies to perfect these attributes can lead to superior products that meet consumer demands and expectations.
By mastering the techniques to control bristle hardness and enhance their longevity, manufacturers can create toothbrushes that maintain oral hygiene effectively.
The Importance of Bristle Hardness and Durability
When consumers choose a toothbrush, they often look for the balance between bristle firmness and longevity.
Hardness impacts how efficiently the bristles clean the teeth, while durability assures prolonged use without significant wear and tear.
Bristles that are too soft may not clean effectively, while overly hard bristles can damage gums and enamel.
Therefore, optimizing this attribute ensures that the user receives a toothbrush that is both safe and effective.
Why Durability Matters
The durability of toothbrush bristles is a key factor determining the product’s lifespan.
Frequent fracturing or flattening of bristles leads to ineffective cleaning, necessitating frequent replacements that deter consumers.
Enhanced durability means longevity for the toothbrush and consistent performance over several months of regular use, which is an attractive feature for consumers looking for reliability and value for money.
Materials Used in Toothbrush Bristles
Materials play a significant role in determining the hardness and durability of toothbrush bristles.
Typically, toothbrush bristles are made from synthetic materials such as nylon, due to its excellent balance between flexibility, resistance to wear, and affordability.
Nylon Bristles
Nylon is the most commonly used material due to its superior properties.
It can be adjusted during production to create desired hardness levels by controlling the diameter and density of the bristles.
Alternatives to Nylon
While nylon dominates, there are efforts to explore other materials, including biodegradable plastics and bamboo fibers, in pursuit of environmentally friendly solutions.
However, these alternatives often require innovative processing to approach the reliability and effectiveness of traditional nylon bristles.
Processing Methods to Optimize Bristle Hardness
Once you understand your material options, the next step is to explore how to manipulate them to achieve the desired hardness.
This often involves a combination of mechanical and chemical processes.
Diameter and Density Control
To change the hardness, you can adjust the diameter of individual bristles.
Thicker diameters tend to produce stiffer, harder bristles, while thinner diameters yield softer results.
Controlling the density, or pack, of the bristles on the toothbrush head can also influence the overall hardness.
Higher density can make bristles feel firmer due to increased support.
Heat Treatment
Applying heat can influence the mechanical properties of the bristles.
By carefully managing the temperature and duration of heat exposure during manufacturing, you can increase the stiffness of the bristle fibers.
It’s vital to ensure uniform heating to avoid weaknesses that could impact durability.
Techniques to Enhance Bristle Durability
Beyond hardness, enhancing bristle durability involves strategies to prevent fraying, breakage, and wear over time.
Surface Coatings
Applying specialized coatings to the bristle surfaces can help reduce friction and protect against abrasion.
Coatings can also impart antimicrobial properties, which add to longevity by maintaining hygiene and preventing growth that could degrade bristle integrity.
Anchoring Methods
The way bristles are anchored into the toothbrush head is crucial for durability.
Using advanced anchoring techniques such as tapering or interweaving ensures that the bristles stay in place longer.
Cheaper anchoring methods might seem cost-effective in production but can lead to early failure.
Innovative Design
Finally, innovative designs that incorporate varying brushing angles or multi-layer bristle lengths can distribute the pressure more evenly during use.
This reduces stress on any single bristle, preserving the integrity of the set.
Final Thoughts on Optimizing Toothbrush Manufacturing
For production engineers in the toothbrush manufacturing industry, focusing on bristle hardness and durability is a pathway to creating superior products.
Understanding the intricate balance of materials and processing methods can lead to making toothbrushes that stand out in the market for their efficacy and longevity.
The goal should always be to satisfy consumer needs while incorporating sustainable practices that account for future advances in materials science and environmental considerations.
The win-win of a well-optimized toothbrush is a happier consumer and a cleaner planet.
資料ダウンロード
QCD調達購買管理クラウド「newji」は、調達購買部門で必要なQCD管理全てを備えた、現場特化型兼クラウド型の今世紀最高の購買管理システムとなります。
ユーザー登録
調達購買業務の効率化だけでなく、システムを導入することで、コスト削減や製品・資材のステータス可視化のほか、属人化していた購買情報の共有化による内部不正防止や統制にも役立ちます。
NEWJI DX
製造業に特化したデジタルトランスフォーメーション(DX)の実現を目指す請負開発型のコンサルティングサービスです。AI、iPaaS、および先端の技術を駆使して、製造プロセスの効率化、業務効率化、チームワーク強化、コスト削減、品質向上を実現します。このサービスは、製造業の課題を深く理解し、それに対する最適なデジタルソリューションを提供することで、企業が持続的な成長とイノベーションを達成できるようサポートします。
オンライン講座
製造業、主に購買・調達部門にお勤めの方々に向けた情報を配信しております。
新任の方やベテランの方、管理職を対象とした幅広いコンテンツをご用意しております。
お問い合わせ
コストダウンが利益に直結する術だと理解していても、なかなか前に進めることができない状況。そんな時は、newjiのコストダウン自動化機能で大きく利益貢献しよう!
(Β版非公開)