- お役立ち記事
- For project leaders in the CNC lathe tool holder manufacturing industry! Technology that achieves both high holding power and ease of use
For project leaders in the CNC lathe tool holder manufacturing industry! Technology that achieves both high holding power and ease of use
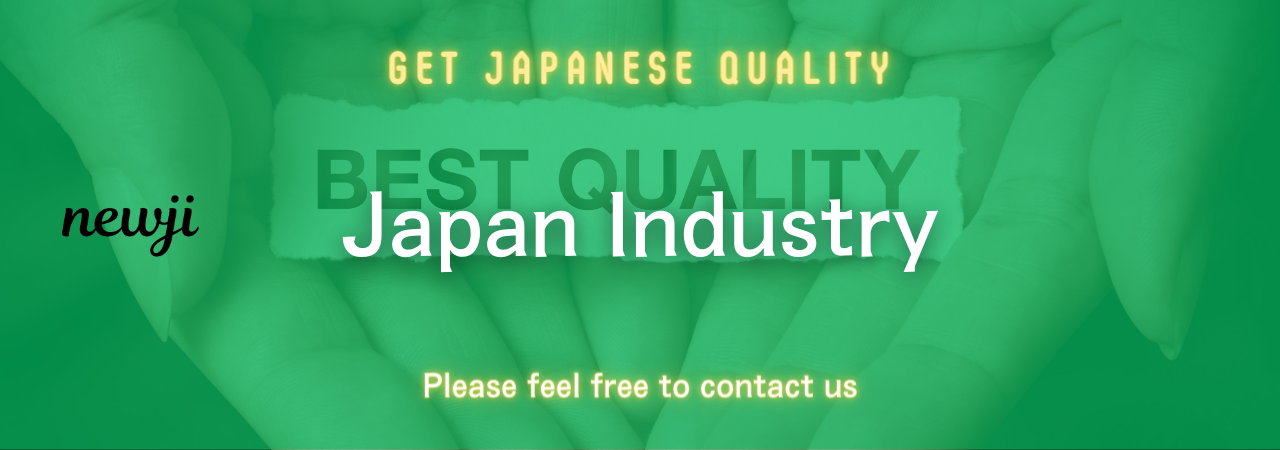
目次
Introduction
In the dynamic world of CNC lathe tool holder manufacturing, project leaders face the ongoing challenge of developing products that not only exhibit high holding power but are also easy to use.
This dual focus is critical as it directly influences productivity and user satisfaction.
In this article, we’ll delve into the cutting-edge technology that makes it possible to achieve both these objectives, ensuring that you stay ahead in the competitive marketplace.
Understanding CNC Lathe Tool Holders
To appreciate the advancements in tool holder technology, it’s essential to first understand what a CNC lathe tool holder does.
These devices secure cutting tools in CNC lathes, facilitating precise and efficient material removal during machining processes.
The key attributes of a high-performing tool holder include stability, accuracy, and the ability to withstand high operational loads.
However, the ease of handling and setup is equally important to enhance efficiency and reduce downtime.
The Importance of Holding Power
Holding power is a critical factor when it comes to CNC tool holders.
It determines the stability and rigidity of the cutting tool, which directly impacts the quality of the machined part.
A tool holder with optimal holding power minimizes vibrations and tool deflection, leading to precise dimensions and smooth finishes on the workpiece.
These attributes are vital for ensuring consistency and meeting stringent quality standards in manufacturing.
The Role of Ease of Use
While holding power is crucial, it should not come at the expense of ease of use.
Tool holders that are difficult to set up or adjust can lead to increased downtime, affecting production schedules.
Therefore, innovations that enhance usability without compromising on performance are invaluable.
A balance between these two aspects ensures that operators can quickly switch tools, adapt to different machining requirements, and maintain continuous production flow.
Innovations in Tool Holder Design
Over the years, advancements in technology have led to the development of innovative tool holder designs that cater to both high holding power and ease of use.
Enhanced Clamping Mechanisms
Recent innovations in clamping mechanisms have significantly improved the holding power of tool holders.
Advanced designs like hydraulic and pneumatic clamping allow for greater stability by distributing clamping force evenly across the tool shank.
This ensures a firm grip, reducing the chances of tool displacement during high-speed operations.
Moreover, these mechanisms often feature quick-release systems that enable rapid tool changes, contributing to increased efficiency and reduced machine downtime.
Modular Tool Holder Systems
Modular tool holder systems have gained popularity due to their versatility and ease of use.
These systems allow manufacturers to customize tool holders according to specific machining tasks by simply swapping out components.
This flexibility not only enhances productivity but also extends the life of the tool holders by allowing for easy maintenance and part replacement.
Furthermore, modular systems are often designed with intuitive interfaces that enable quick adjustments, making them user-friendly and ideal for various machining environments.
Material Innovations
Advancements in material science have played a vital role in enhancing tool holder performance.
The use of premium alloys and composite materials has led to the development of tool holders that offer both durability and reduced weight.
Lightweight materials make handling easier and reduce operator fatigue, while advanced alloys provide the necessary strength and rigidity for reliable holding power.
These materials also contribute to the overall longevity of the tool holders, making them a cost-effective choice for manufacturers looking to maximize ROI.
Impact of Technology on Manufacturing Efficiency
Integrating these technological advancements into CNC lathe tool holders has a profound impact on manufacturing efficiency.
The dual emphasis on holding power and ease of use translates to several tangible benefits.
Improved Operational Stability
Stable tool holders mean that machining operations can be executed at higher speeds without compromising on dimensional accuracy.
This improvement not only increases the throughput but also enhances the quality of the final product.
Manufacturers can achieve tighter tolerances and better surface finishes, thereby reducing the need for secondary operations.
Reduced Setup Times
User-friendly tool holder designs with features like quick-change mechanisms significantly reduce setup times.
Operators spend less time on tool adjustments and can focus more on actual machining processes.
This reduction in downtime directly correlates with higher productivity and efficient use of resources.
Enhanced Operator Safety and Comfort
With ergonomically designed tool holders and lightweight materials, operators experience less fatigue and reduced risk of strain injuries.
Safety features integrated into the tool holders, such as secure clamping systems, further protect operators from potential accidents during tool changes.
This focus on operator well-being translates to a healthier and more efficient work environment.
Conclusion
For project leaders in the CNC lathe tool holder manufacturing industry, staying ahead requires embracing innovations that deliver both high holding power and ease of use.
The latest tool holder technologies, including enhanced clamping mechanisms, modular systems, and advanced materials, provide the perfect balance between performance and usability.
By integrating these innovations into your operations, you can achieve greater efficiency, improved product quality, and an overall competitive advantage in the market.
Continued investment in research and development, alongside an understanding of industry trends, will ensure that your company remains at the forefront of tool holder technology.
As you seek to enhance your product offerings, remember that the end goal is a seamless, efficient, and productive machining process that benefits both operators and manufacturers alike.
資料ダウンロード
QCD調達購買管理クラウド「newji」は、調達購買部門で必要なQCD管理全てを備えた、現場特化型兼クラウド型の今世紀最高の購買管理システムとなります。
ユーザー登録
調達購買業務の効率化だけでなく、システムを導入することで、コスト削減や製品・資材のステータス可視化のほか、属人化していた購買情報の共有化による内部不正防止や統制にも役立ちます。
NEWJI DX
製造業に特化したデジタルトランスフォーメーション(DX)の実現を目指す請負開発型のコンサルティングサービスです。AI、iPaaS、および先端の技術を駆使して、製造プロセスの効率化、業務効率化、チームワーク強化、コスト削減、品質向上を実現します。このサービスは、製造業の課題を深く理解し、それに対する最適なデジタルソリューションを提供することで、企業が持続的な成長とイノベーションを達成できるようサポートします。
オンライン講座
製造業、主に購買・調達部門にお勤めの方々に向けた情報を配信しております。
新任の方やベテランの方、管理職を対象とした幅広いコンテンツをご用意しております。
お問い合わせ
コストダウンが利益に直結する術だと理解していても、なかなか前に進めることができない状況。そんな時は、newjiのコストダウン自動化機能で大きく利益貢献しよう!
(Β版非公開)