- お役立ち記事
- For project leaders in the feeder guide manufacturing industry for automatic packaging machines! Design techniques that increase efficiency and stability
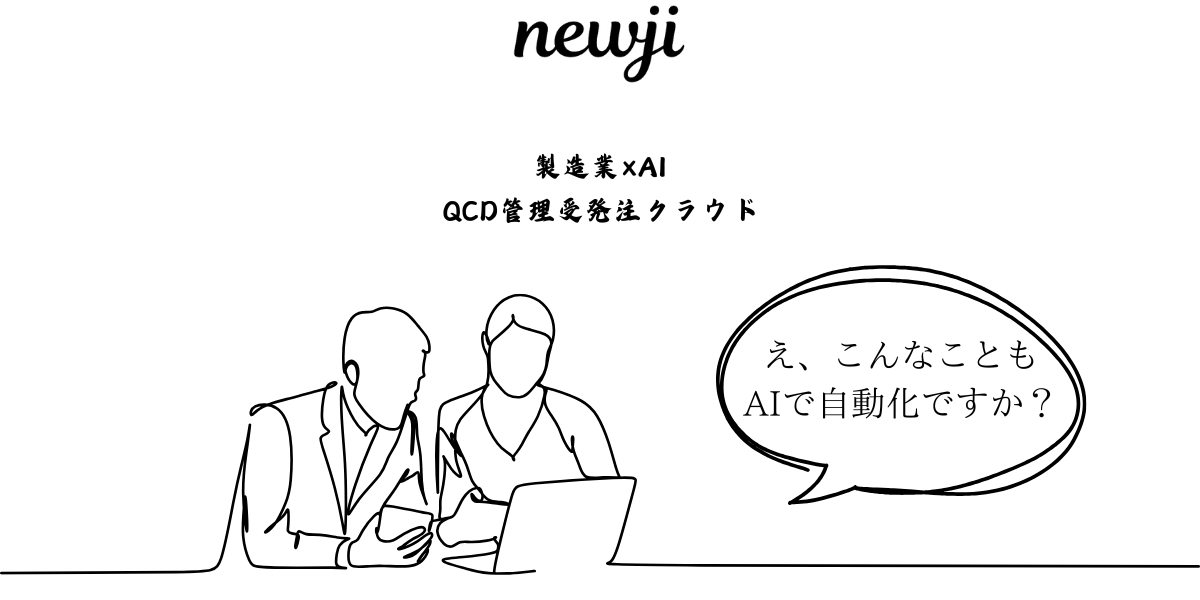
For project leaders in the feeder guide manufacturing industry for automatic packaging machines! Design techniques that increase efficiency and stability
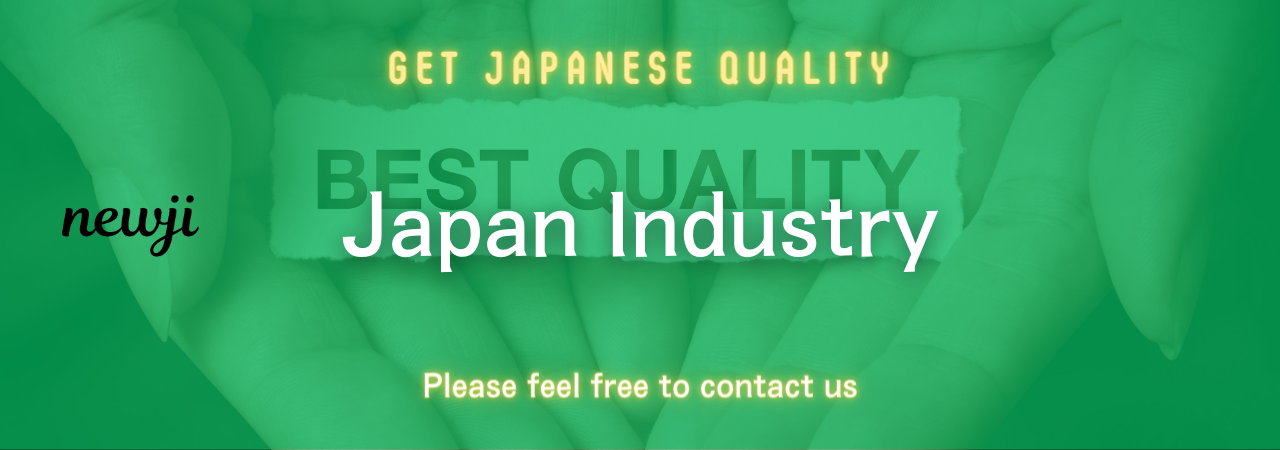
目次
Understanding the Importance of Feeder Guides in Automatic Packaging
In the world of automatic packaging machines, feeder guides play a crucial role in ensuring the efficiency and stability of the entire process.
These components are responsible for directing products smoothly into the packaging line, minimizing disruptions and ensuring consistent output.
As a project leader in the feeder guide manufacturing industry, you are well aware that the design and functionality of these components can significantly impact the overall performance of packaging machines.
Developing effective design techniques is, therefore, essential to optimize both efficiency and stability.
Investing time and resources into improving design strategies can lead to better outcomes, such as reduced downtime, lower maintenance costs, and increased production speed.
In the coming sections, we will explore various design techniques that project leaders can utilize to enhance feeder guide efficiency and improve machine stability.
Key Design Considerations for Feeder Guides
Material Selection
Choosing the right materials for feeder guides is one of the most critical design decisions.
Feeder guides must withstand wear and tear, friction, and sometimes exposure to harsh environments or chemicals.
Materials like stainless steel, high-grade plastics, or even advanced composites can be considered for different applications.
The selected material should offer durability while being cost-effective and compatible with the machines’ operational environment.
Guide Shape and Configuration
The shape and configuration of feeder guides can significantly influence the flow of products.
Designers should consider the shape of the products being packaged, as well as the type of machine, to create an optimal guide configuration.
Smooth curves and carefully calculated angles can minimize blockages and jams, while adjustable guides can offer flexibility for packaging a variety of products.
This adaptability is particularly valuable in multi-line packaging systems.
Precision Engineering
Ensuring that feeder guides are engineered with precision is paramount for stability.
Precise measurements and tolerances are crucial to ensure that the guides align perfectly with the other components of the packaging machine.
Advanced technologies such as CAD (computer-aided design) and CNC (computer numerical control) machining can help achieve the required precision in manufacturing feeder guides.
Close collaboration with skilled engineers can also lead to innovative solutions tailored to specific machine requirements.
Maintenance-Friendly Designs
Designing feeder guides with maintenance in mind can save valuable time and resources in the long run.
Consider features that allow easy access for cleaning and replacing worn parts without the need to dismantle large sections of the machine.
This not only reduces downtime but also ensures that the guides remain in optimal condition, contributing to the overall stability of the packaging line.
Implementing Innovation in Feeder Guide Design
Incorporating Automation
Automating certain aspects of feeder guide design can lead to higher efficiency and reduced human error.
For instance, automation can be used in the configuration settings of adjustable feeder guides, allowing for quick changes to accommodate different product types.
Project leaders should explore the integration of sensors and actuators that can assist in real-time adjustment and monitoring of the guides.
Leveraging Data and Analytics
Data analytics can provide insights into the performance of packaging machines, including feeder guides.
By analyzing data related to speed, downtime, and product flow, designers can identify patterns and areas for improvement.
Data-driven design decisions can lead to enhancements that optimize guide performance and machine productivity.
It is crucial to keep exploring ways to harness data for continuous improvement.
Collaborative Design Approaches
Designing effective feeder guides is rarely a solo task; it requires collaboration across various teams, including engineers, production staff, and quality assurance experts.
Project leaders can facilitate workshops and brainstorming sessions to gather insights and ideas from different perspectives.
Collaborative efforts can lead to more robust designs that cater to the needs of all stakeholders involved in the packaging process.
Testing and Prototyping for Successful Implementation
Prototype Development
Creating prototypes is an essential step in testing the feasibility of feeder guide designs.
Prototyping allows designers to assess the physical and functional attributes of the guides before mass production.
It also provides an opportunity to identify potential issues and make adjustments to optimize performance.
Rigorous Testing
Once a prototype is developed, rigorous testing must be conducted to verify its effectiveness and stability.
Simulated packaging scenarios can reveal how the feeder guide performs under different conditions and product types.
Comprehensive testing helps ensure that the final product meets all operational requirements and can reliably support the packaging line.
Embracing Continuous Improvement
Designing feeder guides for automatic packaging machines is not a one-time endeavor; it requires a commitment to continuous improvement.
Project leaders must stay informed about emerging industry trends, advanced materials, and new technologies.
Regular feedback loops and performance reviews can help identify areas for further development.
As a project leader in the feeder guide manufacturing industry, adopting a proactive and innovative approach to design can set you apart in a competitive market.
By focusing on efficiency and stability, you can contribute significantly to the success of automatic packaging processes, ultimately benefiting your organization and customers.
資料ダウンロード
QCD調達購買管理クラウド「newji」は、調達購買部門で必要なQCD管理全てを備えた、現場特化型兼クラウド型の今世紀最高の購買管理システムとなります。
ユーザー登録
調達購買業務の効率化だけでなく、システムを導入することで、コスト削減や製品・資材のステータス可視化のほか、属人化していた購買情報の共有化による内部不正防止や統制にも役立ちます。
NEWJI DX
製造業に特化したデジタルトランスフォーメーション(DX)の実現を目指す請負開発型のコンサルティングサービスです。AI、iPaaS、および先端の技術を駆使して、製造プロセスの効率化、業務効率化、チームワーク強化、コスト削減、品質向上を実現します。このサービスは、製造業の課題を深く理解し、それに対する最適なデジタルソリューションを提供することで、企業が持続的な成長とイノベーションを達成できるようサポートします。
オンライン講座
製造業、主に購買・調達部門にお勤めの方々に向けた情報を配信しております。
新任の方やベテランの方、管理職を対象とした幅広いコンテンツをご用意しております。
お問い合わせ
コストダウンが利益に直結する術だと理解していても、なかなか前に進めることができない状況。そんな時は、newjiのコストダウン自動化機能で大きく利益貢献しよう!
(Β版非公開)