- お役立ち記事
- For project leaders in the gasket manufacturing industry! Material selection to achieve both sealability and durability
For project leaders in the gasket manufacturing industry! Material selection to achieve both sealability and durability
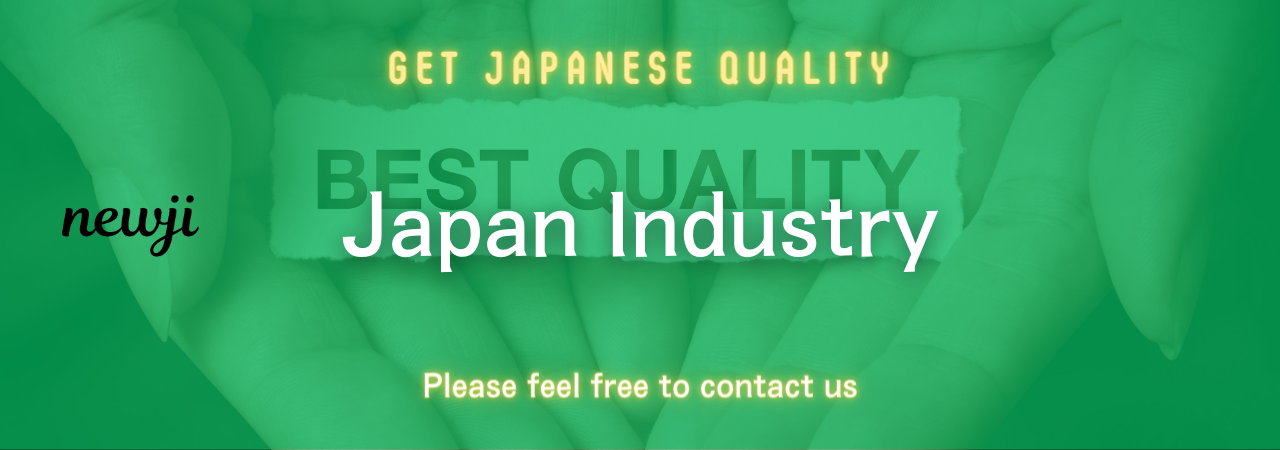
目次
Introduction
When it comes to gasket manufacturing, the importance of choosing the right materials cannot be overstated.
This decision is critical in achieving the balance between sealability and durability, key characteristics necessary for effective gasket performance.
Manufacturers often face challenges juggling these properties, as a material that is highly sealable may not always offer the durability required for long-term use and vice versa.
For project leaders in the gasket manufacturing industry, understanding the criteria for material selection is essential.
Understanding Sealability and Durability
Sealability refers to a material’s ability to prevent fluid or gas from passing through it.
This is crucial in applications where any leakage can compromise the system’s integrity or safety.
Durability, on the other hand, speaks to a material’s longevity and ability to maintain its structural integrity over time.
In the gasket industry, achieving both sealability and durability is essential, as gaskets are often used in demanding environments.
The Challenges of Balancing Sealability and Durability
Finding a material that meets both sealability and durability can be challenging.
Materials that are excellent at forming a tight seal might degrade quickly under high temperatures or pressures.
Conversely, materials designed to withstand harsh conditions may not provide the necessary seal without additional treatment or modification.
Therefore, striking the right balance is a strategic process that demands careful consideration of several factors.
Factors to Consider in Material Selection
Project leaders must consider a multitude of factors when selecting materials for gaskets.
1. Application Environment
The operating environment is the primary consideration.
Gaskets used in automotive engines face different conditions compared to those in aerospace applications.
Temperature fluctuations, exposure to chemicals, and pressure levels are all aspects that influence material choice.
For example, a gasket used in a high-temperature application may require a more heat-resistant material like graphite or metal.
2. Chemical Compatibility
The material must be compatible with the fluids or gases it will contact.
Some materials may react with certain chemicals, leading to degradation or failure.
Choosing a material with chemical resistance is crucial in environments where aggressive substances are present.
3. Mechanical Properties
Mechanical strength is another critical consideration.
A gasket must withstand the mechanical stresses of the application without deforming.
This involves considering the material’s tensile strength, compressibility, and flexibility.
Materials like PTFE offer an excellent balance of chemical resistance and mechanical properties, making them a popular choice.
4. Cost and Availability
While the ideal material may exist, it might be prohibitively expensive or difficult to source.
Project leaders need to find materials that fit within budgetary constraints and are readily available.
This often requires a compromise, balancing performance needs with cost-effectiveness.
Common Materials Used in Gasket Manufacturing
Several materials are commonly used in gasket manufacturing, each with advantages and disadvantages.
1. Rubber
Rubber is a flexible, cost-effective option for many gasket applications.
Materials like nitrile, silicone, and EPDM are widely used due to their excellent sealability and adaptability to dynamic sealing environments.
However, they may not perform well under extreme temperatures or prolonged chemical exposure.
2. PTFE (Polytetrafluoroethylene)
PTFE, commonly known as Teflon, is highly resistant to chemicals and can withstand a broad temperature range.
This makes it highly durable and suitable for demanding applications.
While excellent in sealing performance, PTFE gaskets can be expensive and may require reinforcement to prevent deformation under pressure.
3. Metal
Metal gaskets, including those made from stainless steel, copper, and other alloys, provide exceptional durability and heat resistance.
They are often used in high-pressure applications, such as in the oil and gas industry.
Their sealability can be a concern if not properly designed, but they are effective when combined with a soft material to enhance sealing capabilities.
4. Graphite
Graphite gaskets excel in high-temperature applications due to their excellent thermal stability.
They offer good sealing properties and are often used in environments where other materials might fail.
However, they can be brittle and may require careful handling.
Innovative Approaches to Material Selection
Advancements in materials science have led to the development of composite and multi-material gaskets that aim to combine the best properties of different materials.
By using a combination of materials, manufacturers can create gaskets that achieve both sealability and durability in challenging environments.
This multi-material approach allows for more customized solutions tailored to specific applications.
1. Composite Gaskets
Composite gaskets integrate multiple material layers to enhance performance.
For example, a metal core can be coated with PTFE to provide chemical resistance while maintaining structural strength.
These gaskets can meet the demands of various industrial applications by offering a tailored balance of properties.
2. Custom Material Formulations
Recent innovations have led to the development of custom material formulations optimized for specific applications.
These formulations can be designed to counteract the limitations of traditional materials, such as improved temperature tolerance or enhanced chemical resistance.
Conclusion
For project leaders in the gasket manufacturing industry, material selection is a pivotal decision that affects the product’s success.
Balancing sealability and durability requires a thorough understanding of the application’s demands and the materials available.
By considering the operating environment, chemical compatibility, mechanical properties, and cost constraints, manufacturers can make informed choices.
Innovations in material science open new opportunities to create gaskets that meet both sealability and durability needs, ensuring reliability in even the most demanding applications.
資料ダウンロード
QCD調達購買管理クラウド「newji」は、調達購買部門で必要なQCD管理全てを備えた、現場特化型兼クラウド型の今世紀最高の購買管理システムとなります。
ユーザー登録
調達購買業務の効率化だけでなく、システムを導入することで、コスト削減や製品・資材のステータス可視化のほか、属人化していた購買情報の共有化による内部不正防止や統制にも役立ちます。
NEWJI DX
製造業に特化したデジタルトランスフォーメーション(DX)の実現を目指す請負開発型のコンサルティングサービスです。AI、iPaaS、および先端の技術を駆使して、製造プロセスの効率化、業務効率化、チームワーク強化、コスト削減、品質向上を実現します。このサービスは、製造業の課題を深く理解し、それに対する最適なデジタルソリューションを提供することで、企業が持続的な成長とイノベーションを達成できるようサポートします。
オンライン講座
製造業、主に購買・調達部門にお勤めの方々に向けた情報を配信しております。
新任の方やベテランの方、管理職を対象とした幅広いコンテンツをご用意しております。
お問い合わせ
コストダウンが利益に直結する術だと理解していても、なかなか前に進めることができない状況。そんな時は、newjiのコストダウン自動化機能で大きく利益貢献しよう!
(Β版非公開)