- お役立ち記事
- For project leaders in the liner plate manufacturing industry for crushing equipment! Designed for wear resistance and stability
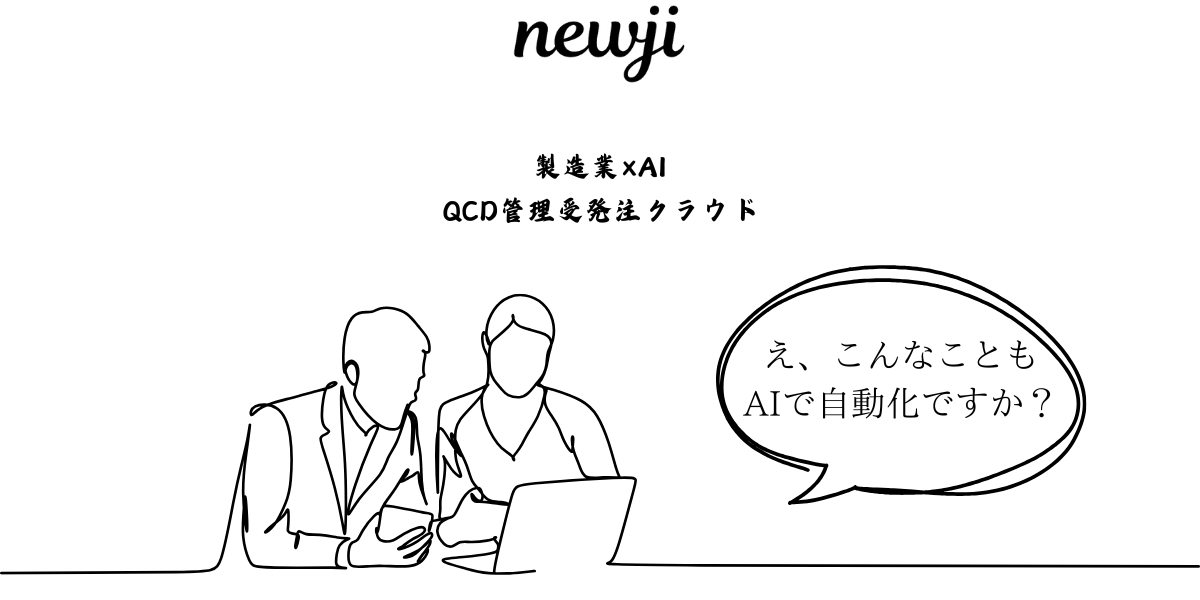
For project leaders in the liner plate manufacturing industry for crushing equipment! Designed for wear resistance and stability
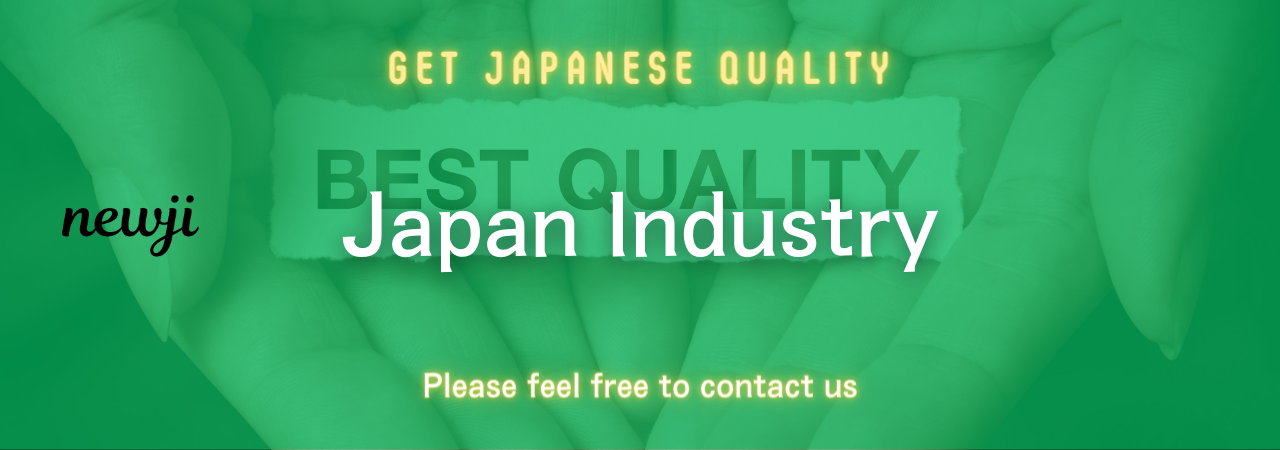
目次
Understanding Liner Plates in Crushing Equipment
Liner plates play a crucial role in crushing equipment, providing the necessary protection and enhancing the machinery’s efficiency.
For project leaders in the liner plate manufacturing industry, understanding the significance of wear resistance and stability is key to improving product performance.
These plates line the interior surfaces of crushers, where they are subjected to harsh abrasive conditions during the crushing process.
The Role of Wear Resistance
Wear resistance is a critical factor affecting the lifespan and performance of liner plates.
During the crushing process, materials such as rocks or minerals erode the surfaces of the liners.
Effective wear-resistant liners can withstand these abrasive forces, minimizing damage and prolonging the life of the crushing equipment.
This resistance not only reduces maintenance costs but also ensures consistent performance over time.
In the manufacturing process, selecting the right materials is essential for achieving optimal wear resistance.
Materials like manganese steel, martensitic steel, and alloy steels are commonly used due to their toughness and ability to absorb impact energy.
Innovations in material technology continue to provide new options for manufacturers aiming to create more durable and high-performance liner plates.
Importance of Stability for Project Success
Stability is another crucial factor for liner plate effectiveness.
In crushing equipment, stability refers to the product’s ability to maintain its structural integrity and optimal alignment under operational stresses.
Stable liner plates ensure that the force distribution within the crusher is even, preventing premature wear or mechanical failure.
Project leaders must focus on the design and installation of liner plates to ensure the machine operates smoothly.
Attention to detail during the installation phase can prevent issues such as misalignment or improper fastening, which can impact the stability of the crushing equipment.
Furthermore, regular inspections and maintenance can help identify potential stability concerns before they become significant problems.
Design Considerations for Liner Plates
When designing liner plates for crushing equipment, several considerations come into play.
The choice of material and its thickness, shape, and configuration will all influence the wear resistance and stability of the liner plate.
In addition to material selection, the design must account for the specific crushing application, as different materials require different types of crushing forces.
Advanced simulation tools can assist project leaders in predicting the wear patterns on liner plates.
By analyzing these patterns, manufacturers can optimize their designs to enhance wear resistance and stability, ensuring the liner plates perform effectively in real-world conditions.
Working with Performance Metrics
Project leaders should set performance metrics to evaluate the success of liner plate designs.
These metrics can include wear rates, maintenance schedules, and the overall cost-effectiveness of the liner plates.
By monitoring these metrics, leaders can make informed decisions about material selection and design improvements.
Moreover, understanding these metrics can help in negotiating with suppliers and collaborating with engineers to develop better solutions.
Latest Trends and Innovations
Innovation in liner plate manufacturing is an ongoing process driven by the need to improve wear resistance and stability.
Recent trends include the development of composite liner plates, which combine different materials to achieve superior performance characteristics.
These composite plates offer enhanced wear resistance, reduced weight, and better impact absorption compared to traditional solid metal liners.
Another trend is the use of advanced coatings that provide a protective barrier against wear and corrosion.
These coatings can significantly extend the lifespan of the liner plates and the associated crushing equipment, offering an attractive option for project leaders focused on longevity and reliability.
Partnerships and Collaboration in the Industry
Collaboration with suppliers, engineers, and end users is essential for project leaders in the liner plate manufacturing industry.
By working closely with stakeholders, manufacturers can better understand the specific needs and challenges faced by those using their products.
This collaborative approach can lead to the development of tailored solutions that meet the unique demands of different crushing applications.
Industry partnerships can also facilitate the sharing of knowledge and best practices, helping companies stay ahead of the competition.
Participating in industry conferences and forums can provide valuable insights into the latest technologies and emerging trends, enabling project leaders to make informed decisions about their liner plate designs.
Future Perspectives in Liner Plate Manufacturing
Looking ahead, the liner plate manufacturing industry is likely to experience continued advancements in material science and manufacturing techniques.
Increasing demand for more efficient and eco-friendly solutions will drive innovation, leading to even more durable and effective liner plates.
Project leaders will need to stay updated on these advancements and be prepared to adopt new technologies that enhance the performance of their crushing equipment.
By focusing on improving wear resistance and stability, the liner plate industry can contribute to more sustainable and cost-effective crushing operations.
In conclusion, project leaders in the liner plate manufacturing industry play a pivotal role in developing products that meet the demands of modern crushing equipment.
By prioritizing wear resistance and stability, they can ensure their liner plates offer maximum protection and performance, ultimately benefiting both manufacturers and users in the industry.
資料ダウンロード
QCD調達購買管理クラウド「newji」は、調達購買部門で必要なQCD管理全てを備えた、現場特化型兼クラウド型の今世紀最高の購買管理システムとなります。
ユーザー登録
調達購買業務の効率化だけでなく、システムを導入することで、コスト削減や製品・資材のステータス可視化のほか、属人化していた購買情報の共有化による内部不正防止や統制にも役立ちます。
NEWJI DX
製造業に特化したデジタルトランスフォーメーション(DX)の実現を目指す請負開発型のコンサルティングサービスです。AI、iPaaS、および先端の技術を駆使して、製造プロセスの効率化、業務効率化、チームワーク強化、コスト削減、品質向上を実現します。このサービスは、製造業の課題を深く理解し、それに対する最適なデジタルソリューションを提供することで、企業が持続的な成長とイノベーションを達成できるようサポートします。
オンライン講座
製造業、主に購買・調達部門にお勤めの方々に向けた情報を配信しております。
新任の方やベテランの方、管理職を対象とした幅広いコンテンツをご用意しております。
お問い合わせ
コストダウンが利益に直結する術だと理解していても、なかなか前に進めることができない状況。そんな時は、newjiのコストダウン自動化機能で大きく利益貢献しよう!
(Β版非公開)