- お役立ち記事
- For project leaders in the pump impeller manufacturing industry! Design technology that achieves both high efficiency and durability
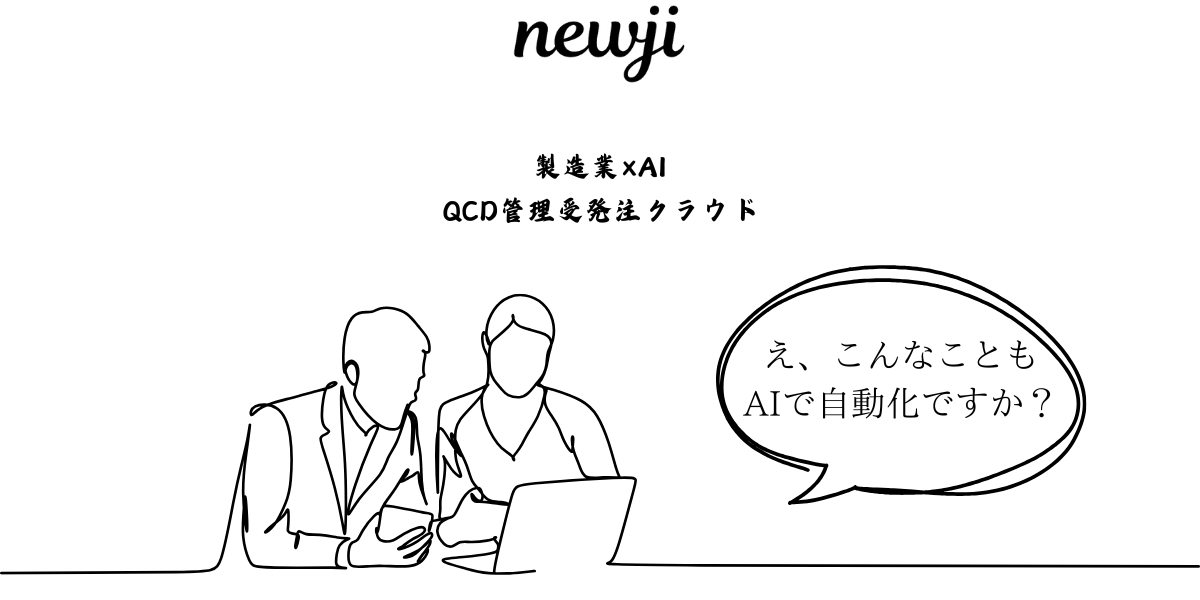
For project leaders in the pump impeller manufacturing industry! Design technology that achieves both high efficiency and durability
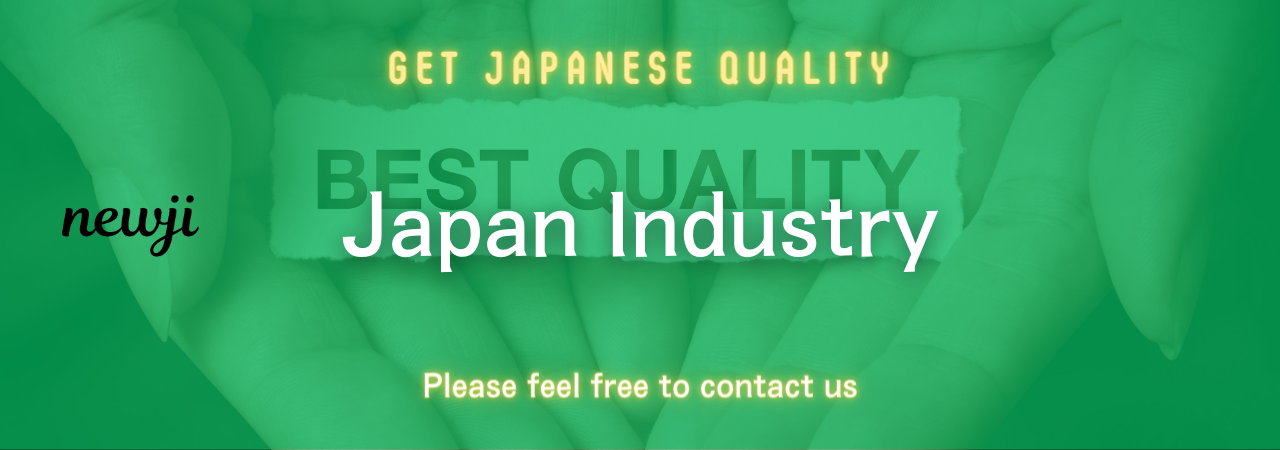
目次
Introduction to Pump Impeller Design
In the pump impeller manufacturing industry, project leaders face the crucial task of balancing efficiency with durability.
The design technology for pump impellers is continually evolving to meet the growing demands for more reliable and efficient pumps.
Understanding the various aspects of this technology is essential for ensuring that your projects not only meet but exceed industry standards.
This article delves into the innovative design techniques and materials used in pump impeller manufacturing to achieve optimal performance.
The Significance of Pump Impeller Efficiency
Pump efficiency is a vital factor in determining the overall performance of a pump.
High-efficiency impellers ensure that energy consumption is minimized, which is beneficial for both cost and environmental reasons.
Efficiency in pump impellers is achieved through several factors, including the shape and curvature of the blades, the impeller’s size, and the type of materials used in its construction.
Understanding these elements can significantly improve the design process, culminating in a product that is not only effective but also highly efficient.
Blade Shape and Curvature
The shape and curvature of the impeller blades play a critical role in determining its efficiency.
Blades must be designed to maximize fluid flow while minimizing energy loss.
Helicoidal and backward-curved blades are popular choices for their ability to manage flow dynamics effectively, ensuring optimal movement of fluids through the pump.
Project leaders must consider these design aspects to create impellers that deliver superior performance.
Achieving Pump Impeller Durability
While efficiency is critical, durability is equally important in the design of pump impellers.
A durable impeller can withstand harsh conditions and frequent use, reducing maintenance costs and downtime.
To achieve durability, manufacturers must focus on selecting appropriate materials and stress-tested designs that can handle the operational demands placed on pump systems.
Material Selection
The choice of materials in pump impeller manufacturing significantly impacts durability.
Materials like stainless steel, titanium, and high-performance polymers are commonly used due to their strength and resistance to corrosion.
Each material offers distinct advantages, and choosing the right one depends on the specific conditions under which the pump will operate.
For instance, corrosive environments often require corrosion-resistant materials like stainless steel, while lightweight polymers are ideal for systems where weight reduction is paramount.
Innovative Coating Techniques
Coatings can further enhance the durability of pump impellers.
Advanced coating techniques, such as thermal spraying and electroplating, provide an additional layer of protection against wear and corrosion.
These coatings can increase the lifespan of an impeller by mitigating the effects of harsh environmental conditions.
Project leaders should consider incorporating these methods into their designs to improve the overall durability of their products.
Balancing Efficiency and Durability in Design
Finding the right balance between efficiency and durability is a common challenge in impeller design.
It’s essential to consider the trade-offs involved in optimizing these two factors.
While focusing solely on efficiency might lead to thinner, more streamlined blades that could be prone to damage, emphasizing durability might result in heavier, less efficient designs.
The key is to employ advanced design and simulation tools that allow for thorough testing of various configurations to find an optimal balance.
Computational Fluid Dynamics (CFD)
Computational Fluid Dynamics (CFD) is an invaluable tool in pump impeller design.
CFD simulations help project leaders visualize how fluids will interact with the impeller blades, enabling them to make informed decisions about shape and material considerations.
By using CFD, designers can predict performance outcomes and make necessary adjustments early in the design phase, saving time and resources.
Finite Element Analysis (FEA)
Finite Element Analysis (FEA) complements CFD by focusing on the structural integrity of the impeller.
FEA allows designers to assess how impellers will behave under various stress conditions, identifying potential points of failure or weakness.
By applying FEA, project leaders can enhance the durability of their designs, ensuring that impellers can withstand the rigors of daily use.
Conclusion: Advancing Design Technology in Pump Impeller Manufacturing
As the pump impeller manufacturing industry continues to advance, project leaders must stay informed about the latest design technologies and materials.
Balancing efficiency and durability is no simple task, but with the right approach, it is achievable.
By leveraging advanced tools like CFD and FEA, selecting appropriate materials, and incorporating innovative coatings, manufacturers can create impellers that set new standards in performance and longevity.
Staying ahead of technological trends and continually refining design strategies will ensure that your projects not only succeed but also lead the industry in innovation and excellence.
資料ダウンロード
QCD調達購買管理クラウド「newji」は、調達購買部門で必要なQCD管理全てを備えた、現場特化型兼クラウド型の今世紀最高の購買管理システムとなります。
ユーザー登録
調達購買業務の効率化だけでなく、システムを導入することで、コスト削減や製品・資材のステータス可視化のほか、属人化していた購買情報の共有化による内部不正防止や統制にも役立ちます。
NEWJI DX
製造業に特化したデジタルトランスフォーメーション(DX)の実現を目指す請負開発型のコンサルティングサービスです。AI、iPaaS、および先端の技術を駆使して、製造プロセスの効率化、業務効率化、チームワーク強化、コスト削減、品質向上を実現します。このサービスは、製造業の課題を深く理解し、それに対する最適なデジタルソリューションを提供することで、企業が持続的な成長とイノベーションを達成できるようサポートします。
オンライン講座
製造業、主に購買・調達部門にお勤めの方々に向けた情報を配信しております。
新任の方やベテランの方、管理職を対象とした幅広いコンテンツをご用意しております。
お問い合わせ
コストダウンが利益に直結する術だと理解していても、なかなか前に進めることができない状況。そんな時は、newjiのコストダウン自動化機能で大きく利益貢献しよう!
(Β版非公開)