- お役立ち記事
- For purchasing leaders: How to create a procurement plan based on the life cycle of parts
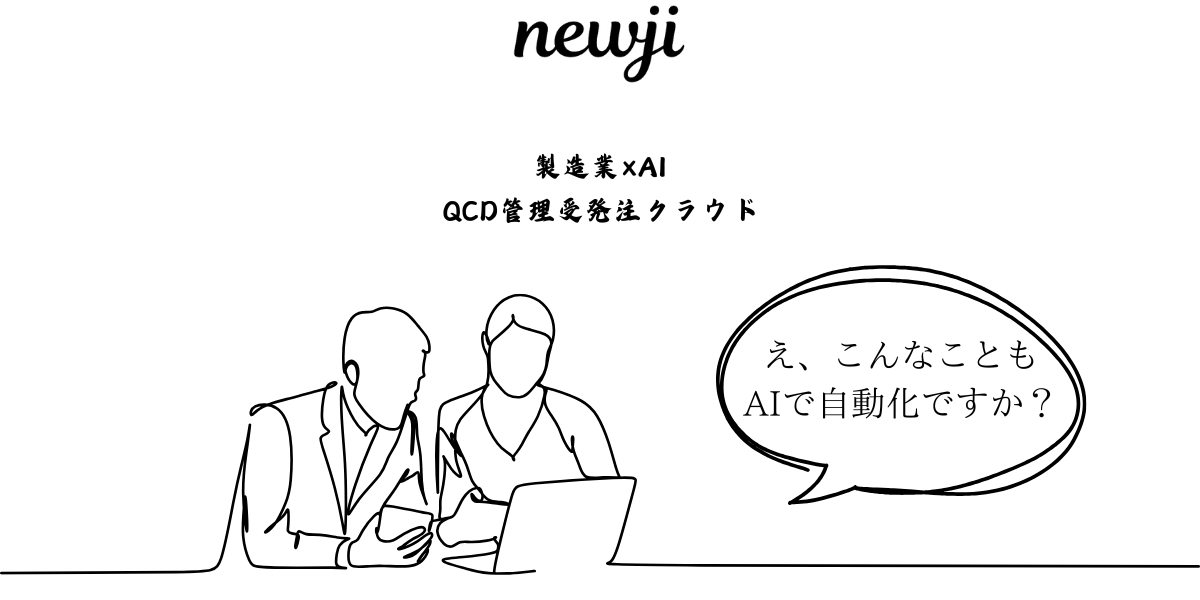
For purchasing leaders: How to create a procurement plan based on the life cycle of parts
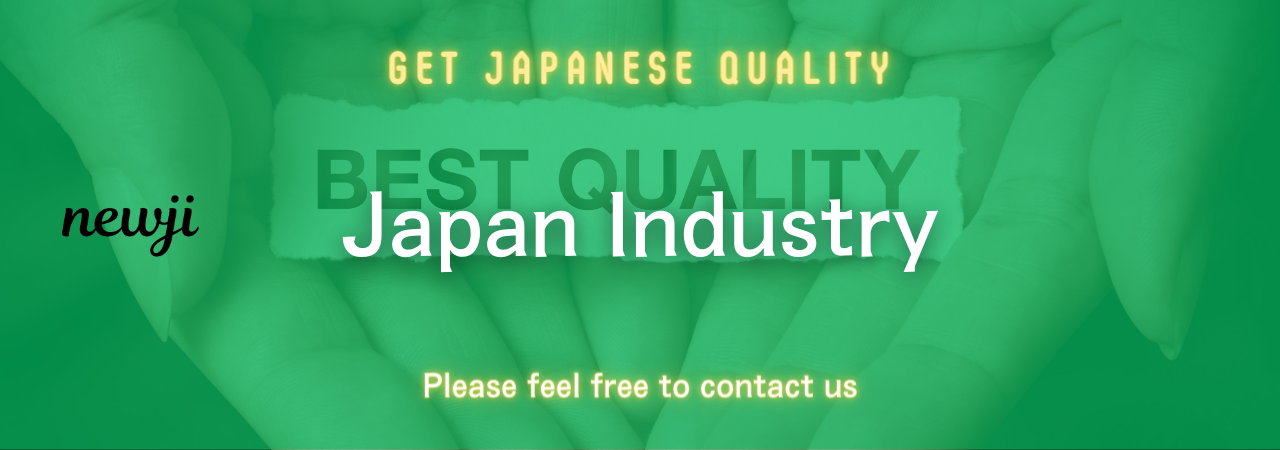
目次
Understanding the Life Cycle of Parts
Before diving into creating a procurement plan, it’s essential to understand the life cycle of parts.
The life cycle of a part usually consists of several stages: introduction, growth, maturity, and decline.
Each stage has distinct characteristics and requires different procurement strategies.
In the introduction stage, parts are newly developed and demand might be low.
As the product gains acceptance, it moves into the growth stage, where demand increases.
The maturity stage sees demand stabilizing, while in the decline stage, demand begins to decrease steadily.
Recognizing which stage a part is in helps procurement leaders tailor their strategies to meet organizational needs while minimizing costs.
Steps to Create a Procurement Plan
1. Assess Current Needs
The first step in creating a procurement plan is to assess the current needs of the organization.
This involves understanding what parts are required, the quantity needed, and when they will be needed.
For this, collaboration with different departments like engineering, production, and maintenance is crucial.
A comprehensive assessment helps in forecasting demand accurately and ensuring that the inventory levels are optimal.
2. Analyze Market and Supplier Trends
Stay informed about market and supplier trends to make educated procurement decisions.
Understanding the global market scenario, potential supply chain disruptions, and any technological advancements is critical.
Relationships with reliable suppliers who are aware of the stages of the parts’ life cycle are vital.
Establishing and maintaining strong relationships with suppliers can lead to better pricing, delivery terms, and service levels.
3. Evaluate Alternative Parts
In certain situations, some parts might be phased out or become too costly.
It’s beneficial to explore alternative parts that can fulfill the same role or function, especially during the maturity and decline stages.
Working closely with engineers and product designers helps identify such alternatives, which might offer better performance or cost benefits.
4. Develop a Budget
Creating a detailed budget is a critical component of any procurement plan.
Factors like part cost, potential savings, and costs associated with delays should be considered.
Budgets should be dynamic and flexible enough to accommodate unexpected changes in part life cycles, like sudden increases in demand or supply chain issues.
Regular budget reviews and updates ensure alignment with the company’s financial goals.
5. Define Procurement Processes and Policies
Establishing clear procurement processes and policies helps in maintaining consistency and efficiency.
Define procedures for supplier selection, contract negotiation, order placement, and quality assurance.
Having documented processes ensures all stakeholders are aligned, and it minimizes risks associated with purchasing decisions.
In the context of the parts’ life cycle, these processes can be adjusted to reflect changes in demand and part availability.
The Importance of Accurate Forecasting
Accurate forecasting is at the heart of an effective procurement plan.
Given the dynamic nature of part life cycles, implementing smart forecasting techniques can minimize risks associated with excess inventory or stockouts.
Adopt advanced tools and technologies like data analytics and AI for more precise forecasting.
These technologies enable procurement professionals to analyze historical data, track market trends, and predict future demand patterns accurately.
Forecasting should be a collaborative effort across departments to ensure that all relevant data is considered, from sales and marketing insights to production schedules.
Maintaining Supplier Relationships
Supplier relationships significantly influence the success of a procurement plan.
Building lasting relationships with key suppliers ensures better reliability, quality, and pricing.
Frequent communication with suppliers allows procurement leaders to stay updated on the latest trends and upcoming changes.
Collaborative relationships with suppliers can also lead to innovative solutions, such as identifying new materials or processes that extend a part’s useful life or enhance its functionality.
Additionally, working closely with suppliers can help mitigate risks related to supply chain disruptions or part shortages.
Managing Part Obsolescence
Managing the obsolescence of parts is an inevitable aspect of the procurement process.
Parts eventually reach the end of their life cycle, requiring procurement leaders to plan for replacements or modifications.
Keeping abreast of new technological developments and maintaining open lines of communication with design and engineering teams is essential.
An effective strategy for managing obsolescence involves proactive planning, allowing time to test and validate potential replacements before they are needed.
This approach minimizes disruptions in production and avoids costly last-minute solutions.
Documentation and Continual Improvement
Documenting the procurement plan and all associated processes ensures transparency and provides a reference for future decision-making.
Regularly reviewing and updating the procurement plan to incorporate lessons learned and market changes is vital for continual improvement.
Feedback from stakeholders involved in the procurement process can provide valuable insights into areas of improvement.
By cultivating a culture of continual improvement, procurement leaders can enhance efficiency, reduce costs, and ensure the seamless operation of the supply chain.
Understanding the life cycle of parts and adopting a strategic approach to procurement allows organizations to optimize their supply chain operations.
A well-formulated procurement plan supports the company’s broader goals by ensuring that the right parts are available at the right time and price.
Such forward-thinking strategies contribute to long-term success and competitive advantage.
資料ダウンロード
QCD調達購買管理クラウド「newji」は、調達購買部門で必要なQCD管理全てを備えた、現場特化型兼クラウド型の今世紀最高の購買管理システムとなります。
ユーザー登録
調達購買業務の効率化だけでなく、システムを導入することで、コスト削減や製品・資材のステータス可視化のほか、属人化していた購買情報の共有化による内部不正防止や統制にも役立ちます。
NEWJI DX
製造業に特化したデジタルトランスフォーメーション(DX)の実現を目指す請負開発型のコンサルティングサービスです。AI、iPaaS、および先端の技術を駆使して、製造プロセスの効率化、業務効率化、チームワーク強化、コスト削減、品質向上を実現します。このサービスは、製造業の課題を深く理解し、それに対する最適なデジタルソリューションを提供することで、企業が持続的な成長とイノベーションを達成できるようサポートします。
オンライン講座
製造業、主に購買・調達部門にお勤めの方々に向けた情報を配信しております。
新任の方やベテランの方、管理職を対象とした幅広いコンテンツをご用意しております。
お問い合わせ
コストダウンが利益に直結する術だと理解していても、なかなか前に進めることができない状況。そんな時は、newjiのコストダウン自動化機能で大きく利益貢献しよう!
(Β版非公開)