- お役立ち記事
- For quality assurance departments! The forefront of process quality control using QC process charts
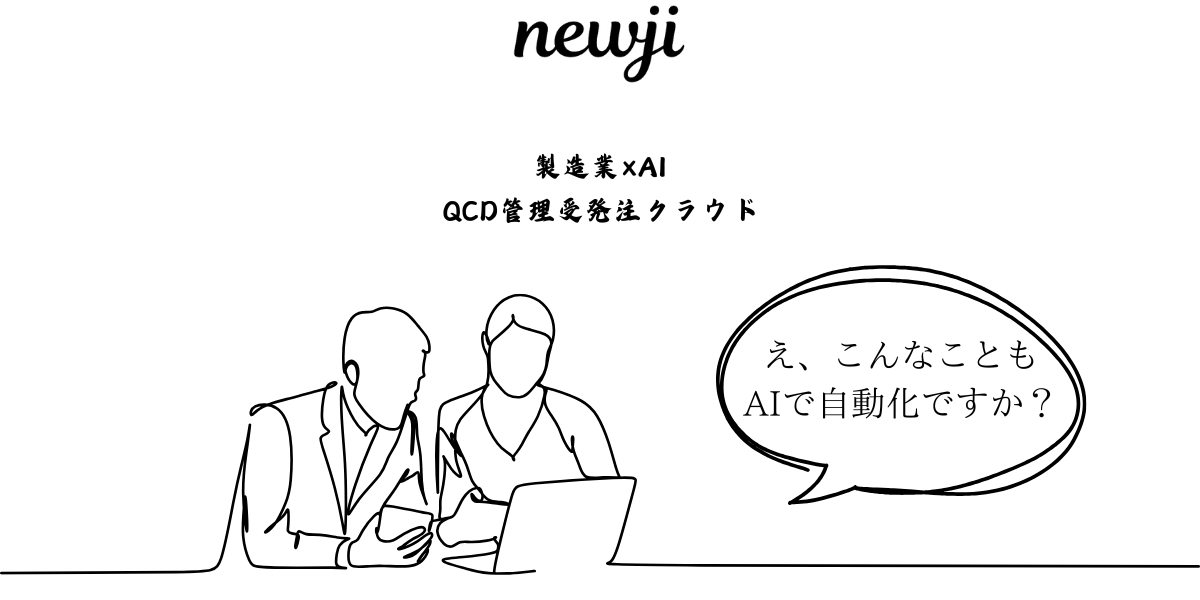
For quality assurance departments! The forefront of process quality control using QC process charts
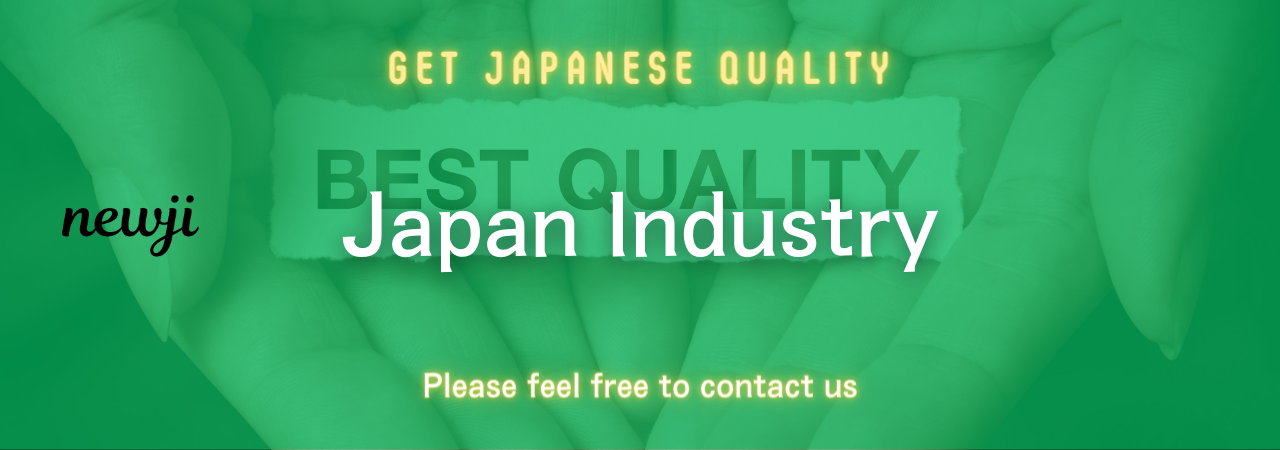
目次
Understanding QC Process Charts
Quality assurance is a crucial aspect of any manufacturing or service industry.
It ensures that products and services meet certain standards and are consistent in quality.
One of the most effective tools used by quality assurance departments is the QC process chart, also known as the quality control chart.
These charts play a pivotal role in process quality control by providing visual representations of data over time, which helps in monitoring and controlling a process.
Understanding QC process charts involves knowing their components, benefits, and applications in various industries.
Components of a QC Process Chart
A QC process chart typically consists of several key elements.
At its core, the chart is a graph with a central line representing the average or desired value, and upper and lower control limits indicating acceptable variations.
These limits are usually set at three standard deviations from the mean.
The data points plotted on the chart represent the collected outputs or processes at regular intervals.
When analyzing a QC chart, it’s essential to look for trends or patterns that might suggest a deviation from the standard process.
Benefits of Using QC Process Charts
One of the primary advantages of QC process charts is their ability to provide real-time data analysis.
This allows quality assurance departments to detect and address issues proactively before they escalate into significant problems.
The charts are also instrumental in identifying both common and special causes of variation, helping organizations focus on process improvements.
Moreover, QC process charts facilitate communication and understanding across various levels of an organization.
By visualizing data, these charts make it easier for teams to make informed decisions swiftly.
This enhanced understanding leads to better compliance with industry standards and contributes to delivering high-quality products or services consistently.
Applications in Different Industries
QC process charts are widely utilized across numerous industries, each adapting the tool to their specific needs.
Manufacturing
In manufacturing, QC process charts are indispensable for maintaining product quality.
They help identify variations in product dimensions, weight, or other specifications critical to ensuring consumer satisfaction.
For instance, automotive industries use these charts to monitor the production lines’ performance and maintain stringent safety standards.
Healthcare
In healthcare, QC process charts monitor various processes, such as infection rates, patient wait times, or medication errors.
By analyzing data trends, hospitals and clinics can implement quality improvement measures, resulting in better patient care and safety.
Food and Beverage
The food and beverage industry utilizes QC process charts to ensure that products are safe for consumption.
These charts help monitor processes like cooking temperatures or packaging, ensuring that products meet health regulations without compromising quality.
Software Development
In software development, QC process charts aid in tracking coding errors, testing milestones, or system performance.
They provide software developers and testers with insights to streamline processes, minimize bugs, and enhance user satisfaction.
How to Implement QC Process Charts Effectively
To reap the full benefits of QC process charts, it’s crucial to implement them effectively.
Here are some steps that quality assurance departments can follow:
Define Objectives
Begin by clearly identifying what you want to achieve with the QC process chart.
This could include reducing defects, increasing productivity, or improving customer satisfaction.
Having well-defined objectives ensures that the chart is aligned with the organization’s goals.
Collect Accurate Data
Accurate and consistent data collection is vital for effective QC process charts.
Ensure that the data is gathered systematically and reflects the process being monitored.
The more accurate the data, the more reliable the chart analysis will be.
Select Appropriate Control Limits
Setting the correct upper and lower control limits is crucial for meaningful analysis.
These limits should be realistic and based on historical data or industry standards.
Incorrect limits can lead to false positives or negatives, impacting decision-making.
Analyze and Act on the Data
Analyzing the QC process chart involves understanding trends, shifts, or patterns.
Look for data points outside the control limits, as these indicate potential problems.
Upon identifying issues, implement corrective actions to address the root cause and prevent future occurrences.
Continuously Improve
QC process charts are not a one-time tool but part of an ongoing quality improvement strategy.
Commit to continuous monitoring and refining processes to uphold high standards and adapt to changing needs.
Feedback from the chart should be used to drive ongoing process improvements.
The Future of QC Process Charts
As industries continue to evolve, so do the tools and techniques for quality control.
The future of QC process charts lies in their integration with advanced technologies such as artificial intelligence (AI) and machine learning (ML).
This integration promises more sophisticated data analysis, predictive capabilities, and faster decision-making.
Moreover, digital transformation and automation are set to revolutionize how QC process charts are implemented.
With real-time data capture and automated analysis, quality assurance departments can respond to issues more swiftly, reducing downtime and increasing efficiency.
In conclusion, QC process charts are a powerful asset for quality assurance departments.
By providing a clear, visual representation of data over time, they help organizations maintain process quality control, improve customer satisfaction, and boost operational efficiency.
As technology continues to advance, the potential for even greater insights and improvements through these charts is boundless.
資料ダウンロード
QCD調達購買管理クラウド「newji」は、調達購買部門で必要なQCD管理全てを備えた、現場特化型兼クラウド型の今世紀最高の購買管理システムとなります。
ユーザー登録
調達購買業務の効率化だけでなく、システムを導入することで、コスト削減や製品・資材のステータス可視化のほか、属人化していた購買情報の共有化による内部不正防止や統制にも役立ちます。
NEWJI DX
製造業に特化したデジタルトランスフォーメーション(DX)の実現を目指す請負開発型のコンサルティングサービスです。AI、iPaaS、および先端の技術を駆使して、製造プロセスの効率化、業務効率化、チームワーク強化、コスト削減、品質向上を実現します。このサービスは、製造業の課題を深く理解し、それに対する最適なデジタルソリューションを提供することで、企業が持続的な成長とイノベーションを達成できるようサポートします。
オンライン講座
製造業、主に購買・調達部門にお勤めの方々に向けた情報を配信しております。
新任の方やベテランの方、管理職を対象とした幅広いコンテンツをご用意しております。
お問い合わせ
コストダウンが利益に直結する術だと理解していても、なかなか前に進めることができない状況。そんな時は、newjiのコストダウン自動化機能で大きく利益貢献しよう!
(Β版非公開)