- お役立ち記事
- For quality assurance leaders in the cutlery organization tray manufacturing industry! A design method that achieves both durability and storage capacity
月間76,176名の
製造業ご担当者様が閲覧しています*
*2025年3月31日現在のGoogle Analyticsのデータより
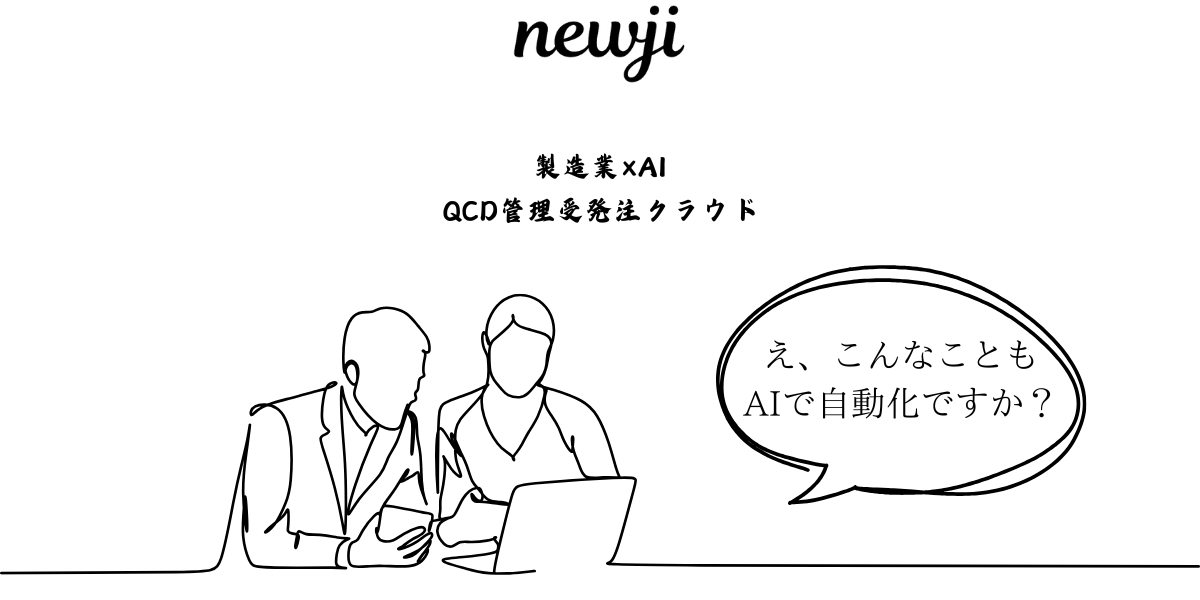
For quality assurance leaders in the cutlery organization tray manufacturing industry! A design method that achieves both durability and storage capacity
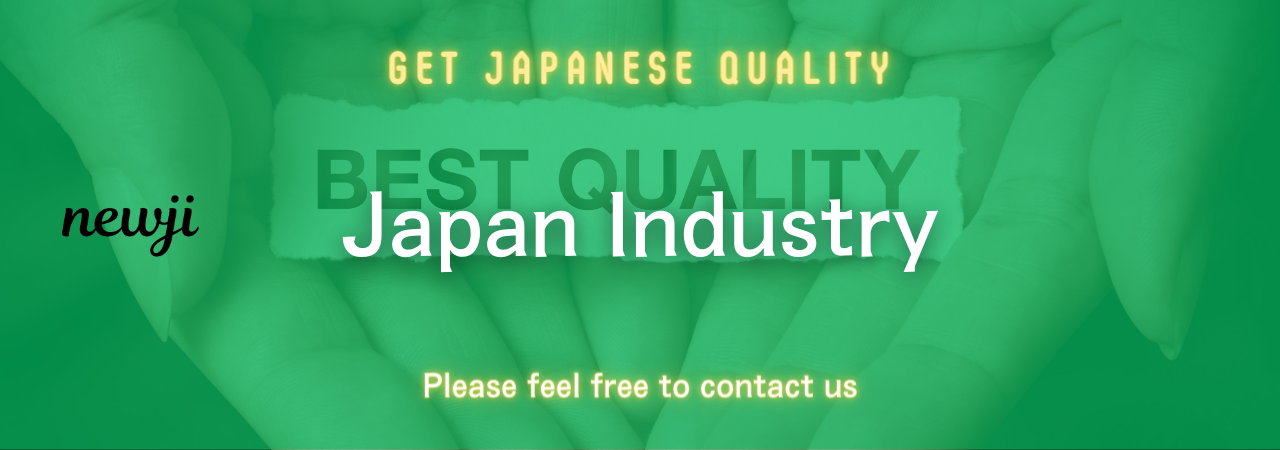
目次
Understanding the Importance of Quality Assurance in Cutlery Organization Tray Manufacturing
In the competitive world of cutlery organization tray manufacturing, quality assurance (QA) is more than just a buzzword.
It is a critical component that ensures the durability and functionality of the product, meeting both consumer expectations and industry standards.
QA processes help in identifying defects, improving product reliability, and enhancing customer satisfaction.
For leaders in this industry, focusing on quality assurance not only improves product quality but also strengthens brand reputation, leading to increased market share.
Challenges in Achieving Durability and Storage Capacity
Manufacturing cutlery organization trays comes with its set of challenges, particularly when trying to balance durability with storage capacity.
The materials used must resist wear and tear over time, yet still be lightweight and cost-effective.
Additionally, the design must maximize space to accommodate various utensils without compromising the tray’s structural integrity.
Conventional approaches often lead manufacturers to compromise on one aspect in favor of the other.
However, innovative design methods can help overcome these challenges, ensuring both durability and storage efficiency.
Innovative Design Methods for Enhanced Tray Durability
A crucial aspect of cutting-edge tray design is the material selection process.
Engineers need to choose materials known for their strength and durability, such as high-density polyethylene or stainless steel, depending on the desired product attributes.
Incorporating advanced materials like composite plastics also boosts longevity and resistance to environmental factors, such as moisture and heat, which can affect the tray’s performance over time.
Moreover, structural reinforcements can be seamlessly integrated into the tray design.
Utilizing cross-bracing or honeycomb patterns not only distributes weight evenly but also fortifies the tray against possible damage.
These techniques allow for thinner materials without sacrificing strength, thus reducing overall weight and production costs.
Maximizing Storage Capacity Through Smart Design
To optimize storage capacity, manufacturers must innovate beyond traditional layouts.
Utilizing modular design principles, trays can be customized with adjustable compartments to accommodate multiple sizes and shapes of cutlery.
This flexibility is crucial for households with diverse utensil collections and also enhances user satisfaction.
Another approach is to employ vertical layering in the tray design.
By creating stackable segments, manufacturers can increase storage capacity without expanding the tray’s footprint.
This efficient use of space not only caters to consumers with limited kitchen areas but also stands out in the competitive market with its practical utility.
The Role of Technology in Tray Manufacturing
Technology plays a pivotal role in advancing the quality and design of cutlery organization trays.
Computer-aided design (CAD) software empowers designers to simulate stress tests and refine tray architectures before actual production.
This predictive ability ensures that final products are durable and meet quality benchmarks.
Additionally, the use of 3D printing technology in prototyping accelerates the product development process.
Manufacturers can quickly produce models to evaluate design feasibility, allowing for rapid iteration and innovation.
This agility in design and production significantly benefits quality assurance leaders aiming to maintain high standards while responding to market demands swiftly.
Best Practices for Quality Assurance Teams
For quality assurance leaders, establishing a culture of continuous improvement is vital.
Regular training sessions for staff on the latest quality assessment techniques and tools can greatly improve inspection efficiency and accuracy.
Implementing a systematic approach like Six Sigma or Total Quality Management (TQM) can root out inefficiencies and streamline production processes.
Routine product testing at different production stages helps in early detection of defects, ensuring that only high-quality trays reach consumers.
Automation in testing, such as through robotic arms and sensors, offers precise and consistent quality checks without the risk of human error.
Moreover, gathering and analyzing customer feedback systematically enables the drive for improvements based on real-user experiences, thus closing the quality loop.
Achieving Sustainability in Cutlery Tray Manufacturing
As environmental concerns grow, sustainability in manufacturing has become critical.
For cutlery organization tray manufacturers, this means exploring eco-friendly materials such as bio-based plastics or recycled components.
These materials not only reduce the environmental footprint but can also attract environmentally conscious consumers, expanding the market base.
Adopting lean manufacturing principles to minimize waste and optimize resource use further aligns with sustainability goals.
By reducing emissions and ensuring efficient use of materials, manufacturers not only comply with environmental regulations but also achieve cost savings.
For quality assurance leaders, sustaining a balance between high standard compliance and environmental stewardship enhances the company’s corporate responsibility profile.
Conclusion: Leading with Innovation and Quality
In the cutlery organization tray manufacturing industry, utilizing innovative design methods that prioritize durability and storage capacity is essential.
By investing in cutting-edge materials, leveraging technology, and embedding sustainability into operations, quality assurance leaders can provide superior products that meet evolving consumer demands.
Embracing these strategies will not only safeguard the company’s competitive position but also reinforce its commitment to quality excellence and innovation while contributing positively to environmental and economic landscapes.
資料ダウンロード
QCD管理受発注クラウド「newji」は、受発注部門で必要なQCD管理全てを備えた、現場特化型兼クラウド型の今世紀最高の受発注管理システムとなります。
ユーザー登録
受発注業務の効率化だけでなく、システムを導入することで、コスト削減や製品・資材のステータス可視化のほか、属人化していた受発注情報の共有化による内部不正防止や統制にも役立ちます。
NEWJI DX
製造業に特化したデジタルトランスフォーメーション(DX)の実現を目指す請負開発型のコンサルティングサービスです。AI、iPaaS、および先端の技術を駆使して、製造プロセスの効率化、業務効率化、チームワーク強化、コスト削減、品質向上を実現します。このサービスは、製造業の課題を深く理解し、それに対する最適なデジタルソリューションを提供することで、企業が持続的な成長とイノベーションを達成できるようサポートします。
製造業ニュース解説
製造業、主に購買・調達部門にお勤めの方々に向けた情報を配信しております。
新任の方やベテランの方、管理職を対象とした幅広いコンテンツをご用意しております。
お問い合わせ
コストダウンが利益に直結する術だと理解していても、なかなか前に進めることができない状況。そんな時は、newjiのコストダウン自動化機能で大きく利益貢献しよう!
(β版非公開)