- お役立ち記事
- For quality managers in pharmaceutical manufacturing departments! Risk management and compliance points based on GMP standards
For quality managers in pharmaceutical manufacturing departments! Risk management and compliance points based on GMP standards
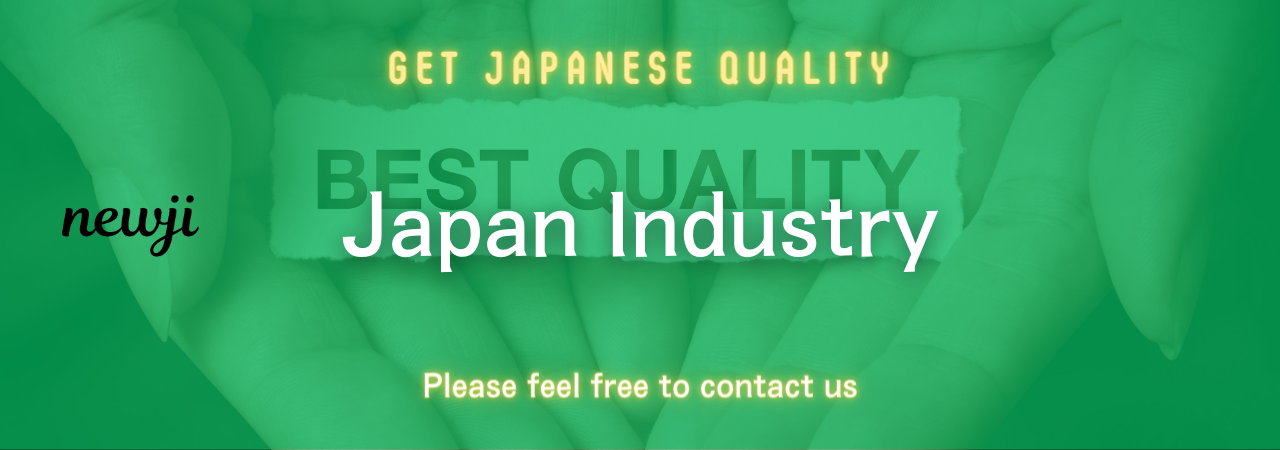
目次
Understanding GMP Standards in Pharmaceutical Manufacturing
GMP, or Good Manufacturing Practice, is a system that ensures products are consistently produced and controlled according to quality standards.
It is designed to minimize the risks involved in any pharmaceutical production that cannot be eliminated through testing the final product.
Compliance with GMP is crucial in the pharmaceutical industry to ensure that products are safe and effective for human consumption.
The Importance of Risk Management in GMP
Risk management is a critical component of GMP.
It involves identifying, assessing, and controlling risks that could potentially impact the quality and safety of pharmaceutical products.
Effective risk management helps to prevent issues that could lead to product recalls, legal consequences, or harm to patients.
In the pharmaceutical manufacturing environment, there are several types of risks that quality managers need to be aware of.
These include contamination risks, supply chain risks, and risks associated with equipment failure.
By anticipating these challenges, quality managers can develop strategies to mitigate them.
Key Compliance Points for Quality Managers
Quality managers in pharmaceutical manufacturing must focus on key compliance points based on GMP standards.
These standards are globally recognized and ensure that pharmaceutical products meet specific quality criteria.
1. Documentation and Record-Keeping
Accurate documentation is a cornerstone of GMP compliance.
Quality managers should ensure that all processes, procedures, and changes are meticulously documented.
This documentation should be accessible and available for audits or inspections.
Proper documentation provides a trail that can help identify the source of any deviations or issues.
2. Personnel Training
Adequate training is essential for all employees involved in the pharmaceutical manufacturing process.
Employees should receive ongoing training on GMP procedures, safety protocols, and any new technologies or processes.
Well-trained personnel are less likely to make errors that could compromise product quality.
3. Facility Design and Maintenance
The design and maintenance of pharmaceutical facilities play a vital role in GMP compliance.
Quality managers should ensure that facilities are designed to prevent contamination and allow for easy cleaning and maintenance.
Regular inspections and maintenance are necessary to keep equipment functioning correctly and to address any potential risks promptly.
4. Quality Control and Assurance Processes
Quality control involves testing the final product to ensure it meets all specified requirements.
Quality assurance goes a step further by ensuring that every step of the manufacturing process contributes to the final product’s quality.
Quality managers should implement robust quality control and assurance processes to maintain product integrity.
5. Change Control Management
The pharmaceutical industry is dynamic, with frequent changes in processes, equipment, and regulations.
A structured change control system allows for careful evaluation and documentation of changes, ensuring they do not adversely affect product quality.
Quality managers should oversee this process to assess risks and implement changes smoothly.
Challenges Faced by Quality Managers
Despite the best efforts, quality managers face numerous challenges in maintaining GMP compliance and managing risks.
One common challenge is staying updated with changing regulations and standards.
Pharmaceutical guidelines are continually evolving, and compliance requires staying informed about these changes.
Additionally, managing supply chain risks can be complex.
Suppliers must also comply with GMP standards, and any deviations can impact the final product.
Quality managers must work closely with suppliers to ensure adherence to quality standards.
Finally, fostering a culture of quality within the organization can be challenging.
It requires commitment from all levels of the organization, from the leadership to the operational staff.
Quality managers must encourage this culture through training, communication, and leading by example.
The Benefits of Effective Risk Management and Compliance
When quality managers in pharmaceutical manufacturing effectively manage risks and ensure compliance with GMP standards, they achieve several key benefits for their organization.
Firstly, they improve the safety and efficacy of their products.
This leads to increased trust from healthcare providers and patients, who rely on pharmaceutical products for their health and well-being.
Secondly, effective compliance reduces the likelihood of costly recalls, regulatory penalties, and legal issues.
This not only protects the company’s financial interests but also its reputation within the industry.
Finally, by prioritizing risk management and compliance, quality managers contribute to continuous improvement within the organization.
This can lead to more efficient manufacturing processes, better resource utilization, and an overall competitive advantage in the market.
Conclusion
In conclusion, quality managers in pharmaceutical manufacturing play a crucial role in ensuring compliance with GMP standards.
By focusing on risk management and compliance points such as documentation, training, facility maintenance, quality control, and change management, they safeguard product quality and safety.
The challenges they face are significant, but with the right strategies and commitment, these hurdles can be overcome, resulting in substantial benefits for both the organization and its consumers.
資料ダウンロード
QCD調達購買管理クラウド「newji」は、調達購買部門で必要なQCD管理全てを備えた、現場特化型兼クラウド型の今世紀最高の購買管理システムとなります。
ユーザー登録
調達購買業務の効率化だけでなく、システムを導入することで、コスト削減や製品・資材のステータス可視化のほか、属人化していた購買情報の共有化による内部不正防止や統制にも役立ちます。
NEWJI DX
製造業に特化したデジタルトランスフォーメーション(DX)の実現を目指す請負開発型のコンサルティングサービスです。AI、iPaaS、および先端の技術を駆使して、製造プロセスの効率化、業務効率化、チームワーク強化、コスト削減、品質向上を実現します。このサービスは、製造業の課題を深く理解し、それに対する最適なデジタルソリューションを提供することで、企業が持続的な成長とイノベーションを達成できるようサポートします。
オンライン講座
製造業、主に購買・調達部門にお勤めの方々に向けた情報を配信しております。
新任の方やベテランの方、管理職を対象とした幅広いコンテンツをご用意しております。
お問い合わせ
コストダウンが利益に直結する術だと理解していても、なかなか前に進めることができない状況。そんな時は、newjiのコストダウン自動化機能で大きく利益貢献しよう!
(Β版非公開)