- お役立ち記事
- For quality managers in the glove holder manufacturing industry! Designed for long-lasting materials and ease of use
For quality managers in the glove holder manufacturing industry! Designed for long-lasting materials and ease of use
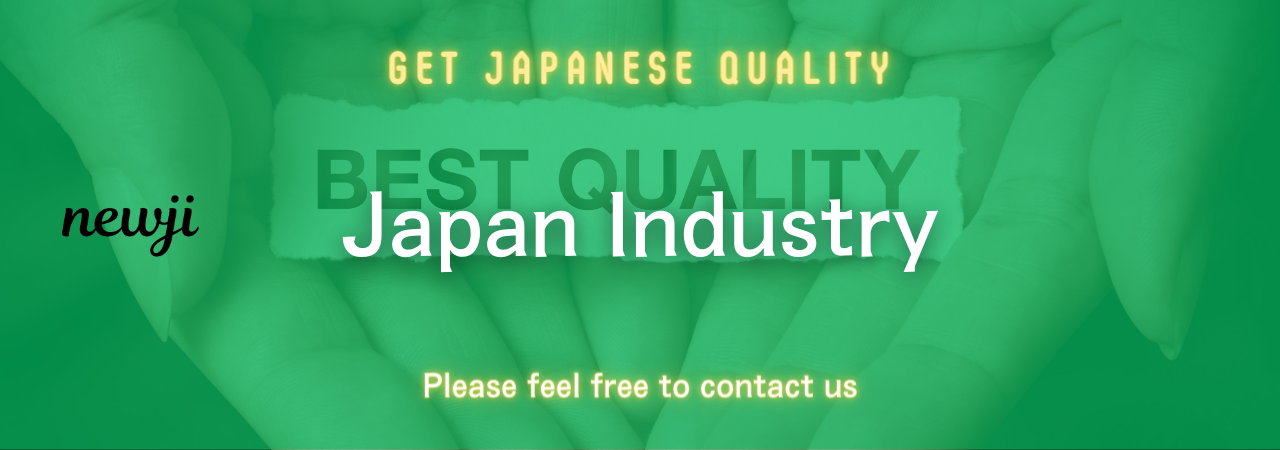
目次
The Importance of Quality in Glove Holder Manufacturing
In the world of manufacturing, quality is a word that holds significant importance.
This is especially true in the glove holder manufacturing industry, where the quality of products can greatly impact their performance and user satisfaction.
Quality managers play a crucial role in ensuring that the final products are not only functional but also meet high standards of durability and ease of use.
Constantly maintaining quality is not a mere option; it’s a necessity.
Glove holders are used in various environments, from industrial settings to medical facilities, where their failure could lead to significant inconvenience or even safety issues.
Understanding Material Selection
One of the primary responsibilities of a quality manager in this field is material selection.
The materials chosen for manufacturing glove holders must be durable, cost-effective, and suitable for various environmental conditions.
Different materials have distinct properties, and understanding these differences is key to producing quality glove holders.
For instance, if the glove holders are intended for industrial use, the selected material should be resistant to chemicals and able to withstand rough handling.
This makes materials like high-grade plastics or stainless steel appealing choices.
On the other hand, for a medical or laboratory setting, the material should be easy to sanitize while remaining robust enough to prevent accidental tearing or breaking.
Designing for Ease of Use
While durability is crucial, ease of use is another pillar of quality in glove holder manufacturing.
The design should ensure that the holders are intuitive and straightforward to use.
An effective glove holder should facilitate the quick and easy retrieval of gloves, reducing time spent on mundane tasks and allowing workers to focus on more critical activities.
Quality managers must work closely with design teams to create prototypes that are user-friendly.
Input from real-world users can be invaluable here, highlighting areas for improvement that may not be obvious in the initial stages of product design.
Field testing is often a critical step in this phase, as it provides insights into practical usability that can refine the final product design.
Implementing Rigorous Testing Protocols
Once a design is finalized, rigorous testing protocols must be put in place.
Testing is an indispensable part of the quality assurance process, helping to identify potential weak points and ensuring that the product meets the expected standards under various conditions.
Common testing practices include stress testing, where glove holders are subjected to extreme conditions to evaluate their resilience.
Flexibility and load-bearing assessments are also essential, ensuring the glove holder performs optimally without deformation.
Furthermore, testing should also account for the long-term usability of the product.
This means simulating wear and tear over extended periods to guarantee the glove holder remains functional and dependable throughout its lifespan.
Leveraging Technology for Quality Control
Modern technology can greatly enhance the quality assurance processes in glove holder manufacturing.
Advanced machinery and software solutions enable precision crafting, allowing for tighter control over production tolerances.
This means that each piece manufactured is almost identical to the next, minimizing variability and ensuring consistent quality.
Automated systems can also take over repetitive quality checks, reducing human error and freeing up human resources for more analytical tasks.
By using technology for quality control, manufacturers can increase efficiency, reduce waste, and maintain high standards consistently.
Continuous Improvement and Feedback Loops
To maintain high quality standards, it’s essential to establish a continuous feedback loop with customers and within the manufacturing team.
Customer feedback can offer valuable insights into how glove holders perform in real-world situations, revealing potential areas for improvement.
Internally, implementing regular reviews and team discussions can foster a culture of continuous improvement.
Encouraging employees at all levels to share ideas and feedback on the manufacturing process can lead to innovative solutions that enhance product quality.
Environmental and Regulatory Compliance
Today’s consumers are more environmentally conscious than ever, and this is influencing how products are made.
Quality managers must ensure that their production processes adhere to environmental guidelines and comply with regulations.
This means selecting recyclable or sustainable materials when possible and ensuring that manufacturing techniques are environmentally friendly.
Compliance with industry regulations and standards is also critical.
These regulations exist to protect both workers and consumers, ensuring that products are safe and reliable.
Future Trends in Glove Holder Manufacturing
As technology and materials science advance, new trends are expected to emerge in glove holder manufacturing.
Smart materials that can adapt to their environment are on the horizon, offering even greater resilience and versatility.
Furthermore, the integration of IoT (Internet of Things) technology could allow for smarter inventory management, where glove holders with embedded sensors signal when glove stocks are low or require replenishment.
Quality managers need to stay ahead of these trends to ensure they can implement such innovations effectively without compromising quality.
Conclusion
Being a quality manager in the glove holder manufacturing industry involves a wide range of responsibilities, all centered around maintaining high standards of product quality.
From material selection and design to rigorous testing and continuous improvement, every aspect of production must be scrutinized for excellence.
By focusing on durability and ease of use, quality managers can help their companies produce glove holders that are reliable, efficient, and satisfy the needs of various industries.
The commitment to quality ensures not only the longevity of the product but also bolsters the reputation of the manufacturing firm, paving the way for continued success and innovation.
資料ダウンロード
QCD調達購買管理クラウド「newji」は、調達購買部門で必要なQCD管理全てを備えた、現場特化型兼クラウド型の今世紀最高の購買管理システムとなります。
ユーザー登録
調達購買業務の効率化だけでなく、システムを導入することで、コスト削減や製品・資材のステータス可視化のほか、属人化していた購買情報の共有化による内部不正防止や統制にも役立ちます。
NEWJI DX
製造業に特化したデジタルトランスフォーメーション(DX)の実現を目指す請負開発型のコンサルティングサービスです。AI、iPaaS、および先端の技術を駆使して、製造プロセスの効率化、業務効率化、チームワーク強化、コスト削減、品質向上を実現します。このサービスは、製造業の課題を深く理解し、それに対する最適なデジタルソリューションを提供することで、企業が持続的な成長とイノベーションを達成できるようサポートします。
オンライン講座
製造業、主に購買・調達部門にお勤めの方々に向けた情報を配信しております。
新任の方やベテランの方、管理職を対象とした幅広いコンテンツをご用意しております。
お問い合わせ
コストダウンが利益に直結する術だと理解していても、なかなか前に進めることができない状況。そんな時は、newjiのコストダウン自動化機能で大きく利益貢献しよう!
(Β版非公開)