- お役立ち記事
- For quality managers in the peel plate manufacturing industry for automatic labeling machines! Selection of materials that maintain wear resistance and precision
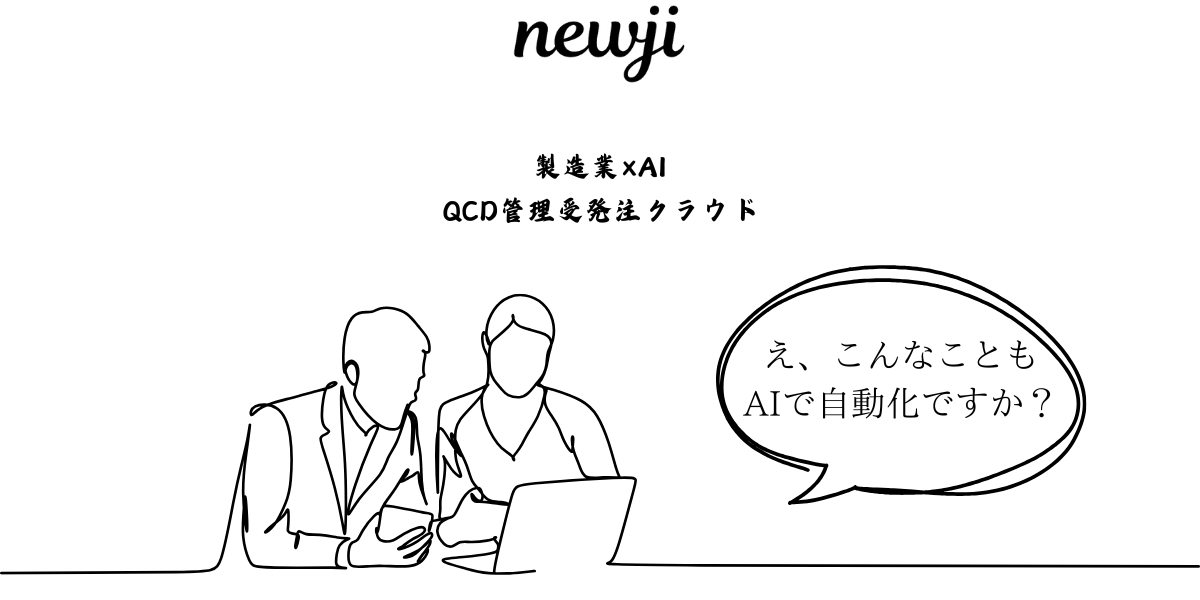
For quality managers in the peel plate manufacturing industry for automatic labeling machines! Selection of materials that maintain wear resistance and precision
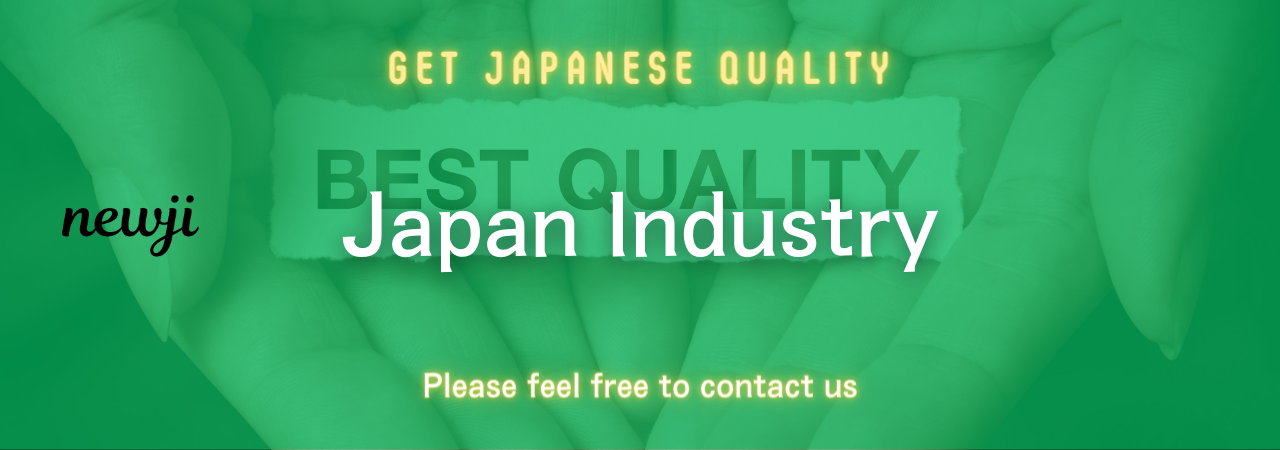
目次
Understanding the Importance of Material Selection
Quality managers in the peel plate manufacturing industry face the crucial task of selecting materials that are integral to the performance and durability of automatic labeling machines.
The right material selection not only ensures wear resistance but also maintains the precision essential for efficient machine operation.
In a competitive industry where precision and reliability determine success, understanding how material choice impacts these factors is crucial.
The Role of Peel Plates in Labeling Machines
Peel plates play a vital role in labeling machines by helping to separate labels from their backing.
As each label is applied, the peel plate must maintain precise dimensions to ensure accurate placement.
Wear resistance is also paramount because these components endure constant movement and friction during the labeling process.
A poor material choice could lead to increased machine downtime and additional costs due to frequent replacements.
Factors to Consider in Material Selection
When choosing materials for peel plates, quality managers must consider several key factors to ensure the longevity and effectiveness of the labeling machines.
Wear Resistance
One of the primary considerations is wear resistance.
Materials that can withstand repetitive motion and friction without degrading are ideal.
This property helps maintain consistent operation over long periods, reducing the need for frequent maintenance.
Precision and Stability
Materials must also maintain precision and dimensional stability under various conditions.
Fluctuations in temperature and humidity can cause certain materials to expand or contract, leading to misalignment or errors in labeling.
Choosing materials with stable properties helps prevent these issues, ensuring that the peel plates consistently perform as expected.
Compatibility with Other Machine Parts
Compatibility with other machine components is another critical aspect.
Materials should not cause undue wear or react negatively with other parts of the labeling machine.
Considering how materials interact can prevent mechanical failures and extend the machine’s overall lifespan.
Common Materials Used in Peel Plates
Several materials are commonly used in the manufacturing of peel plates, each with its own advantages and drawbacks.
Stainless Steel
Stainless steel is a popular choice due to its excellent wear resistance and durability.
It can withstand harsh environments and is less likely to corrode, making it ideal for long-term use in labeling machines.
Moreover, stainless steel provides a smooth surface, reducing friction and wear on labels as they pass over the peel plate.
Aluminum
Aluminum offers a balance between strength and weight, making it another common choice.
While not as durable as stainless steel, it is lightweight and easier to machine, which can reduce manufacturing costs.
Aluminum also provides good thermal conductivity, helping to dissipate heat generated during machine operation.
Plastics and Composites
Advanced plastics and composites are increasingly being used for their flexibility and reduced weight.
These materials can be engineered to meet specific wear resistance and precision requirements.
However, they might not offer the same longevity as metals, making them more suitable for applications where frequent replacement is feasible.
Innovations and Future Trends
The peel plate manufacturing industry is evolving with advancements in material science and technology.
New materials and manufacturing techniques are being developed to enhance the wear resistance and precision of peel plates.
Advanced Coatings
Applying advanced coatings to peel plates can significantly improve their wear resistance.
These coatings, such as diamond-like carbon (DLC) or ceramic coatings, provide a hard, low-friction surface that extends the component’s lifespan.
Coatings can be tailored to meet the specific demands of different labeling environments, offering a custom approach to material optimization.
3D Printing
3D printing technology is also making its way into the manufacturing of peel plates.
This innovation allows for the creation of complex geometries and the inclusion of internal features that can enhance performance.
3D printing enables rapid prototyping and testing of different material combinations, helping quality managers find the optimal solution for their machines.
Conclusion
For quality managers in the peel plate manufacturing industry, material selection plays a critical role in ensuring the wear resistance and precision of automatic labeling machines.
By understanding the unique properties and benefits of different materials, and staying informed about new innovations, quality managers can make informed decisions that enhance machine performance and reliability.
Ultimately, the right material choice contributes to fewer machine downtimes, reduced maintenance costs, and consistent labeling accuracy, providing a competitive edge in the dynamic manufacturing landscape.
資料ダウンロード
QCD調達購買管理クラウド「newji」は、調達購買部門で必要なQCD管理全てを備えた、現場特化型兼クラウド型の今世紀最高の購買管理システムとなります。
ユーザー登録
調達購買業務の効率化だけでなく、システムを導入することで、コスト削減や製品・資材のステータス可視化のほか、属人化していた購買情報の共有化による内部不正防止や統制にも役立ちます。
NEWJI DX
製造業に特化したデジタルトランスフォーメーション(DX)の実現を目指す請負開発型のコンサルティングサービスです。AI、iPaaS、および先端の技術を駆使して、製造プロセスの効率化、業務効率化、チームワーク強化、コスト削減、品質向上を実現します。このサービスは、製造業の課題を深く理解し、それに対する最適なデジタルソリューションを提供することで、企業が持続的な成長とイノベーションを達成できるようサポートします。
オンライン講座
製造業、主に購買・調達部門にお勤めの方々に向けた情報を配信しております。
新任の方やベテランの方、管理職を対象とした幅広いコンテンツをご用意しております。
お問い合わせ
コストダウンが利益に直結する術だと理解していても、なかなか前に進めることができない状況。そんな時は、newjiのコストダウン自動化機能で大きく利益貢献しよう!
(Β版非公開)