- お役立ち記事
- For quality managers in the piping flange manufacturing industry for petrochemical plants! Design technology to achieve both corrosion resistance and strength
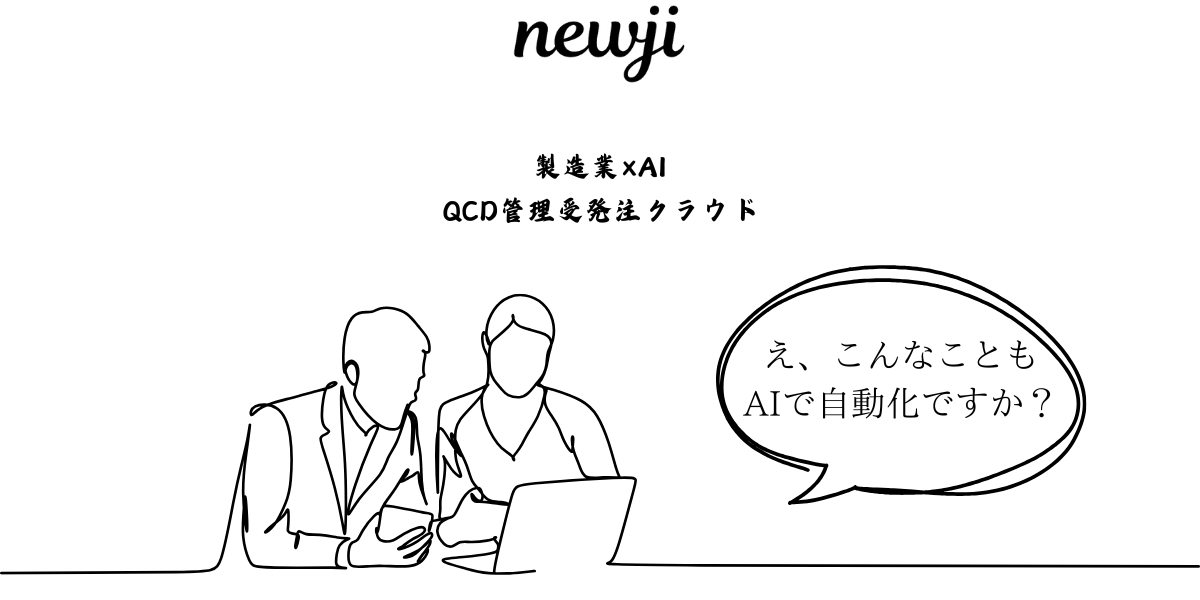
For quality managers in the piping flange manufacturing industry for petrochemical plants! Design technology to achieve both corrosion resistance and strength
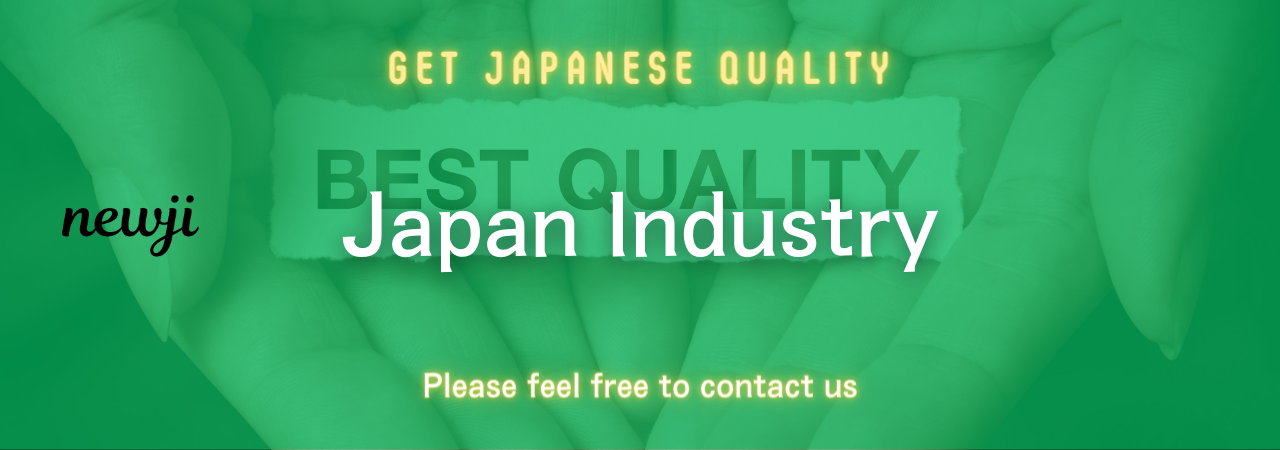
目次
Understanding the Importance of Design Technology in Flange Manufacturing
Design technology plays a crucial role in the piping flange manufacturing industry, especially for petrochemical plants.
Flanges, as critical components in piping systems, must withstand harsh environmental conditions.
The petrochemical industry demands materials that can resist corrosion and maintain strength over time.
Thus, achieving a balance between corrosion resistance and strength is essential for quality managers in this sector.
To meet these requirements, it’s imperative to adopt advanced design technologies.
These technologies not only enhance the performance of flanges but also optimize production processes.
The Role of Corrosion Resistance in Flange Manufacturing
Corrosion resistance is one of the primary considerations in flange manufacturing for petrochemical plants.
The substances flowing through these pipes are often corrosive, which can compromise the integrity of the entire system.
If the flanges are not corrosion-resistant, they can deteriorate, leading to leaks or even catastrophic failures.
Materials used in manufacturing should, therefore, possess high corrosion resistance.
Super alloys and stainless steel are popular choices for their ability to withstand corrosive substances.
Innovative coatings and treatments can also enhance corrosion resistance, providing an extra layer of protection.
For quality managers, understanding the interplay between material properties and environmental conditions is essential.
By doing so, they can select and design flanges that perform optimally in diverse environments.
The Need for Strength in Piping Flanges
While corrosion resistance is vital, strength is equally important when designing piping flanges.
These components must endure high pressure, temperature fluctuations, and mechanical stress.
Ensuring that flanges have the necessary structural integrity involves selecting materials that offer both robustness and flexibility.
Quality managers should focus on material selection, specific to the pressure and temperature they will face in application.
Metals like carbon steel, alloy steel, and duplex stainless steel are typically chosen for their strength and durability.
In addition to material selection, precision in manufacturing processes such as forging and machining is critical.
These ensure that the flanges deliver consistent performance under demanding conditions.
Innovative Design Technologies in Flange Manufacturing
Modern manufacturing technologies significantly enhance the capability to design flanges that meet both corrosion resistance and strength requirements.
Computer-Aided Design (CAD) Systems
The use of CAD systems has revolutionized the design process in flange manufacturing.
These systems enable engineers to create precise geometric models and simulate various conditions flanges might endure.
CAD software helps in visualizing design complexities, enabling engineers to refine and optimize designs before moving to production.
By simulating real-world conditions within CAD, manufacturers can foresee potential issues, improving both the design’s quality and the lifespan of the product.
Finite Element Analysis (FEA)
Finite Element Analysis (FEA) is another groundbreaking design technology.
It allows manufacturers to simulate physical phenomena such as stress, heat transfer, and fluid dynamics.
FEA helps in predicting how flanges will behave under different loads and conditions.
Through FEA, designers can pinpoint weaknesses in a design and make informed adjustments.
This process ensures that the final product adheres to stringent safety and performance standards, which are crucial in the petrochemical industry.
3D Printing and Rapid Prototyping
3D printing and rapid prototyping are game-changers for testing and refining flange designs.
These technologies allow for the production of prototype components quickly and cost-effectively.
Rapid prototyping helps manufacturers to experiment with different design concepts without incurring high costs.
It accelerates the development process by enabling fast feedback and iteration, ensuring that the final design meets all specified requirements.
Implementing Best Practices for Optimal Flange Design
Quality managers must adopt best practices to ensure the manufacturing process aligns with both corrosion resistance and strength goals.
Material Selection Criteria
Selecting the right material is foundational to achieving a desirable balance of properties.
Considerations include the specific chemicals flanges will encounter, operating temperatures, and pressure ratings.
Consulting with material scientists and metallurgists can provide deeper insights into selecting optimal materials.
Regular Testing and Validation
Ongoing testing throughout the design and manufacturing processes is critical.
Regular destructive and non-destructive testing validates that the flanges meet all required specifications.
Such testing should mimic service conditions as closely as possible, ensuring that products are reliable.
Collaboration and Communication
Collaboration between design, manufacturing, and quality assurance teams is essential.
Open communication ensures everyone is aligned with the project’s objectives and technical requirements are fully understood.
Interdisciplinary teams bring diverse perspectives, which can lead to innovative solutions.
The Future of Flange Manufacturing
As the demand for safer and more efficient petrochemical plants grows, the flange manufacturing industry must continue evolving.
Emerging technologies like artificial intelligence and machine learning offer new avenues for innovation.
These technologies can optimize production processes, reduce waste, and enhance precision in both design and manufacturing.
In conclusion, quality managers in the piping flange manufacturing industry must leverage design technology to meet the dual demands of corrosion resistance and strength.
By staying ahead of technological advancements and implementing best practices, manufacturers can ensure the production of high-quality flanges that stand the test of time.
資料ダウンロード
QCD調達購買管理クラウド「newji」は、調達購買部門で必要なQCD管理全てを備えた、現場特化型兼クラウド型の今世紀最高の購買管理システムとなります。
ユーザー登録
調達購買業務の効率化だけでなく、システムを導入することで、コスト削減や製品・資材のステータス可視化のほか、属人化していた購買情報の共有化による内部不正防止や統制にも役立ちます。
NEWJI DX
製造業に特化したデジタルトランスフォーメーション(DX)の実現を目指す請負開発型のコンサルティングサービスです。AI、iPaaS、および先端の技術を駆使して、製造プロセスの効率化、業務効率化、チームワーク強化、コスト削減、品質向上を実現します。このサービスは、製造業の課題を深く理解し、それに対する最適なデジタルソリューションを提供することで、企業が持続的な成長とイノベーションを達成できるようサポートします。
オンライン講座
製造業、主に購買・調達部門にお勤めの方々に向けた情報を配信しております。
新任の方やベテランの方、管理職を対象とした幅広いコンテンツをご用意しております。
お問い合わせ
コストダウンが利益に直結する術だと理解していても、なかなか前に進めることができない状況。そんな時は、newjiのコストダウン自動化機能で大きく利益貢献しよう!
(Β版非公開)