- お役立ち記事
- For quality managers in the pressure sensor diaphragm manufacturing industry! Manufacturing technology to achieve both pressure resistance and flexibility
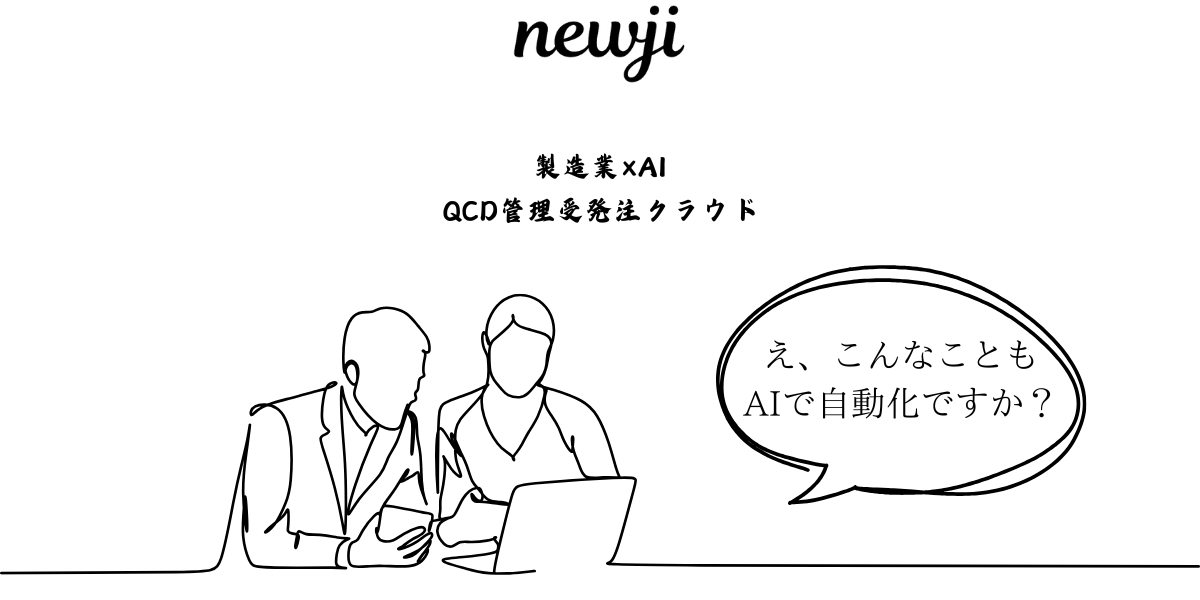
For quality managers in the pressure sensor diaphragm manufacturing industry! Manufacturing technology to achieve both pressure resistance and flexibility
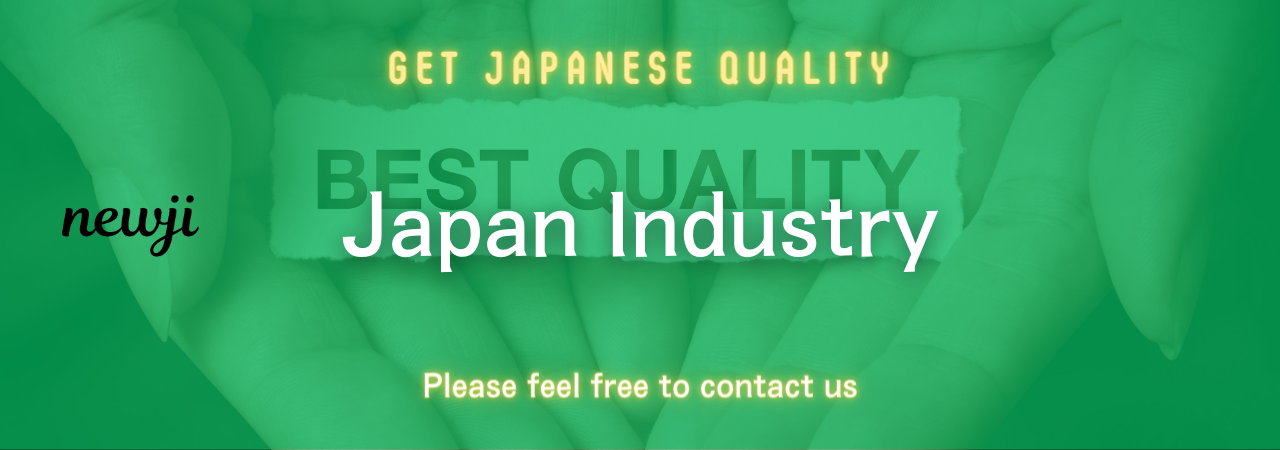
目次
Introduction to Pressure Sensor Diaphragms
Pressure sensors play a crucial role in various industries, from automotive to healthcare.
A key component in these sensors is the diaphragm, which is responsible for detecting pressure changes.
Diaphragms need to be both pressure-resistant and flexible to perform effectively.
Balancing these properties is essential for quality managers in the manufacturing industry who aim to produce high-quality sensors.
The Importance of Pressure Resistance and Flexibility
The pressure sensor diaphragm must withstand high-pressure environments without deforming or breaking.
Pressure resistance ensures durability and reliability over a long period.
Simultaneously, flexibility allows the diaphragm to respond accurately to pressure changes.
This dual requirement is what makes the manufacturing process challenging yet fascinating.
Why Pressure Resistance Matters
In industrial settings, pressure sensors are often exposed to extreme conditions.
A diaphragm that lacks sufficient pressure resistance can lead to sensor failure, causing inaccurate readings.
This can be detrimental, especially in critical applications such as monitoring hydraulic systems or controlling environmental conditions in chemical processing plants.
The Role of Flexibility
While pressure resistance is important, flexibility is equally critical.
A diaphragm must be able to bend and return to its original shape as pressure conditions vary.
This ensures that the sensor provides precise measurements needed for proper functionality in applications like medical devices and automotive systems.
Materials Used for Diaphragms
The choice of materials is crucial in achieving the required balance between pressure resistance and flexibility.
Quality managers must understand the properties of different materials to make informed decisions.
Common Materials in Use
1. **Metals**: Stainless steel, titanium, and other alloys are popular due to their high strength and durability.
They provide excellent pressure resistance but can be less flexible unless engineered specifically for that purpose.
2. **Polymers**: These materials offer greater flexibility and are lightweight.
Rubber and plastics are common in applications where moderate pressure conditions are expected.
3. **Composites**: Combining metals with polymers can create diaphragms that offer both flexibility and strength.
These composites are tailored to specific performance requirements.
Manufacturing Techniques for Optimized Diaphragms
To achieve the desired balance, various manufacturing techniques are employed.
These not only affect the physical properties of the diaphragm but also its performance and longevity.
Precision Machining
Precision machining involves crafting diaphragms with intricate designs that can enhance both pressure resistance and flexibility.
Using computer-aided design (CAD) technology, manufacturers can produce diaphragms with finely-tuned thickness variations that offer enhanced performance.
Heat Treatment Processes
Heat treatment is a common method to improve the mechanical properties of diaphragm materials.
By altering the material’s structure through controlled heating and cooling, its strength and flexibility can be optimized.
Advanced Coatings
Applying coatings such as anti-corrosive or wear-resistant layers can extend the life of diaphragms.
These coatings can also provide additional flexibility and protection, making the diaphragms more robust in harsh operating environments.
Quality Control in Diaphragm Manufacturing
Maintaining high standards of manufacturing quality is essential to ensure diaphragms meet industry requirements.
Quality managers play a pivotal role in implementing rigorous inspection processes from material selection to final product assessment.
Material Testing
Before production, raw materials undergo stringent testing to verify their strength, elasticity, and other properties.
These tests confirm that the materials used will consistently meet the sensory requirements of pressure resistance and flexibility.
Performance Evaluation
During and after production, the diaphragms are subjected to performance evaluation tests.
Simulating real-life conditions, these tests check for responsiveness, durability, and overall functionality.
Inspection Techniques
Using advanced inspection techniques like ultrasonic testing and X-ray imaging allows manufacturers to detect defects that are not visible to the naked eye.
These methods help ensure only diaphragms meeting the highest quality standards reach the market.
Conclusion
Balancing pressure resistance and flexibility in pressure sensor diaphragms is a complex but achievable task.
By selecting appropriate materials and employing advanced manufacturing techniques, quality managers can produce high-performance diaphragms.
Through strict quality control measures, they ensure these components meet or exceed industry requirements, providing reliable performance across various applications.
In a competitive industry, mastering these aspects of diaphragm production is key to success.
資料ダウンロード
QCD調達購買管理クラウド「newji」は、調達購買部門で必要なQCD管理全てを備えた、現場特化型兼クラウド型の今世紀最高の購買管理システムとなります。
ユーザー登録
調達購買業務の効率化だけでなく、システムを導入することで、コスト削減や製品・資材のステータス可視化のほか、属人化していた購買情報の共有化による内部不正防止や統制にも役立ちます。
NEWJI DX
製造業に特化したデジタルトランスフォーメーション(DX)の実現を目指す請負開発型のコンサルティングサービスです。AI、iPaaS、および先端の技術を駆使して、製造プロセスの効率化、業務効率化、チームワーク強化、コスト削減、品質向上を実現します。このサービスは、製造業の課題を深く理解し、それに対する最適なデジタルソリューションを提供することで、企業が持続的な成長とイノベーションを達成できるようサポートします。
オンライン講座
製造業、主に購買・調達部門にお勤めの方々に向けた情報を配信しております。
新任の方やベテランの方、管理職を対象とした幅広いコンテンツをご用意しております。
お問い合わせ
コストダウンが利益に直結する術だと理解していても、なかなか前に進めることができない状況。そんな時は、newjiのコストダウン自動化機能で大きく利益貢献しよう!
(Β版非公開)