- お役立ち記事
- For quality managers in the vacuum port manufacturing industry for semiconductor manufacturing equipment! Selection of materials that achieve high airtightness and durability
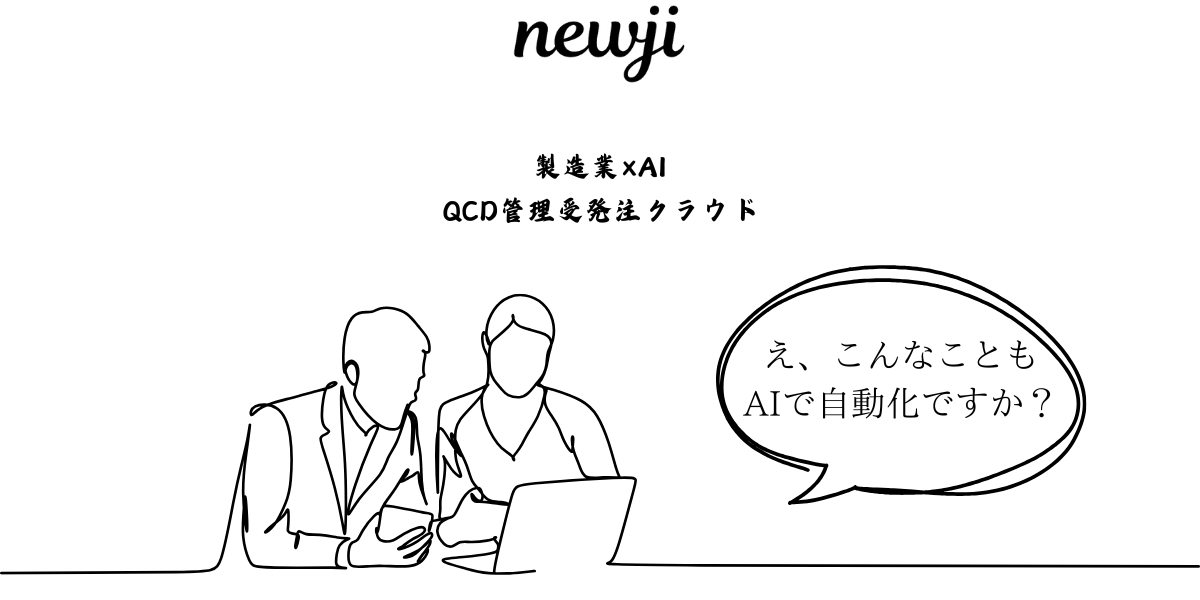
For quality managers in the vacuum port manufacturing industry for semiconductor manufacturing equipment! Selection of materials that achieve high airtightness and durability
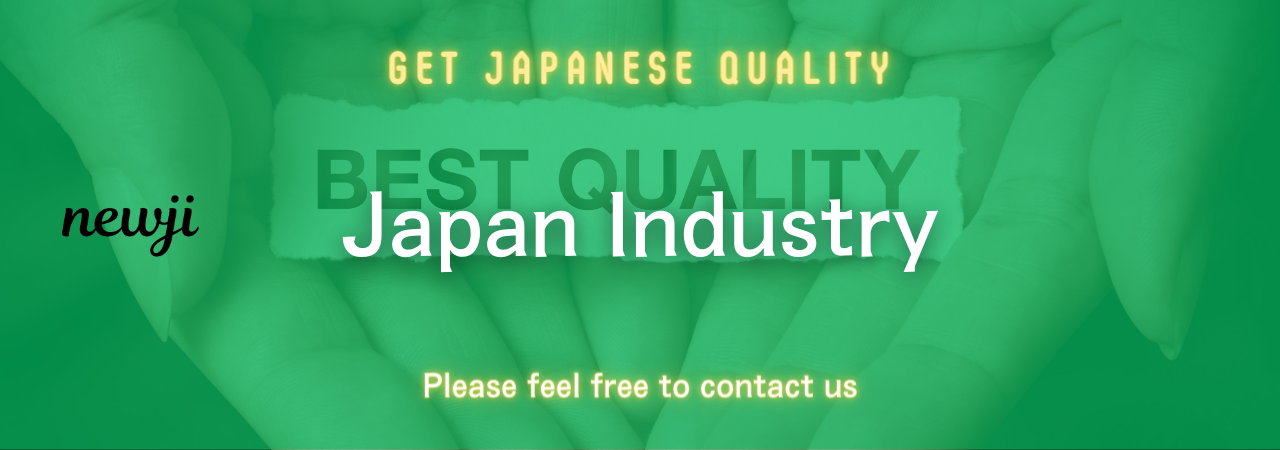
目次
Understanding the Importance of Material Selection
In the vacuum port manufacturing industry, especially for semiconductor manufacturing equipment, selecting the right materials is crucial.
Quality managers must ensure that the materials used achieve high airtightness and durability.
The performance and longevity of semiconductor equipment directly depend on this decision.
Airtightness prevents leaks and maintains the vacuum conditions required for semiconductor processing.
Durability ensures the components withstand the operational and environmental stresses over time.
A solid understanding of these factors is essential for quality managers aiming to maintain and improve manufacturing standards.
Key Factors to Consider in Material Selection
Material Composition
The composition of materials used in vacuum port manufacturing significantly impacts the performance and reliability of the equipment.
Commonly used materials include stainless steel, aluminum, and various alloys.
Each has distinct properties that influence their suitability for different applications.
For instance, stainless steel is known for its high resistance to corrosion and excellent structural integrity.
This makes it a popular choice for vacuum ports that require a strong and stable material.
Thermal Conductivity
Thermal conductivity is another critical factor.
During semiconductor manufacturing, equipment is subjected to varying temperature conditions.
The materials selected should be able to handle these changes without compromising the vacuum environment or the device’s functionality.
Materials with high thermal conductivity can quickly dissipate heat, reducing the risk of thermal damage.
This is particularly important in high-precision manufacturing processes where temperature control is paramount.
Chemical Resistance
Semiconductor manufacturing involves the use of various chemicals, from cleaning agents to etching solutions.
The materials used in vacuum ports must be able to resist these chemicals to prevent degradation and maintain airtightness.
Quality managers should prioritize materials that offer strong chemical resistance.
This safeguards the integrity of the vacuum environment and prevents contamination of delicate semiconductor wafers.
The Role of Testing and Validation
Before finalizing material choices, rigorous testing and validation processes are essential.
These processes ensure that the selected materials meet the required specification for airtightness and durability.
Leak Testing
Leak testing is a critical component of the validation process.
It determines the material’s capability to maintain a vacuum seal under operational conditions.
This test involves subjecting materials to pressure differentials and checking for any leaks.
Successful leak testing confirms that the material can deliver the high level of airtightness needed in semiconductor manufacturing.
Fatigue Testing
Fatigue testing evaluates a material’s ability to withstand repeated stress and strain over time.
Vacuum ports experience continuous use in dynamic environments, making durability a crucial property.
By conducting fatigue tests, manufacturers can predict the material’s lifespan and avoid unexpected failures.
Innovative Materials for Enhanced Performance
The search for materials that deliver superior performance is ongoing.
Innovations in material science are leading to the development of advanced materials tailored for vacuum port manufacturing.
Composite Materials
Composite materials are gaining traction due to their customizable properties.
By combining different materials, manufacturers can create composites that offer enhanced strength, lightweight characteristics, and improved thermal management.
These materials can be engineered to meet specific needs, providing a competitive edge in semiconductor equipment manufacturing.
Carbon-Based Materials
Carbon-based materials, such as carbon fiber and graphene, are also emerging as promising options.
They offer exceptional strength-to-weight ratios and excellent thermal and chemical resistance.
These properties make them suitable candidates for parts subjected to rigorous conditions in vacuum environments.
Balancing Cost and Performance
While the properties of materials are of utmost importance, cost considerations cannot be overlooked.
Quality managers need to find a balance between performance and affordability.
Cost-Benefit Analysis
Conducting a cost-benefit analysis helps in assessing the long-term value of material choices.
Sometimes, investing in a more expensive high-performance material can lead to reduced maintenance costs and longer equipment life.
Supplier Reliability
The reliability and reputation of material suppliers also play a pivotal role.
Choosing suppliers with a track record of delivering consistent, high-quality materials can prevent issues down the line.
Long-term partnerships with reputable suppliers ensure a steady supply of materials and can sometimes offer cost advantages in bulk purchases.
Conclusion
The role of quality managers in the vacuum port manufacturing industry is crucial for the advancement of semiconductor manufacturing equipment.
Careful material selection based on airtightness and durability can significantly improve equipment performance and longevity.
Understanding the material properties, conducting thorough testing, exploring innovative options, and balancing costs are all vital steps in this process.
As technology advances, the importance of selecting the right materials will continue to grow, pushing the boundaries of what is possible in semiconductor manufacturing.
資料ダウンロード
QCD調達購買管理クラウド「newji」は、調達購買部門で必要なQCD管理全てを備えた、現場特化型兼クラウド型の今世紀最高の購買管理システムとなります。
ユーザー登録
調達購買業務の効率化だけでなく、システムを導入することで、コスト削減や製品・資材のステータス可視化のほか、属人化していた購買情報の共有化による内部不正防止や統制にも役立ちます。
NEWJI DX
製造業に特化したデジタルトランスフォーメーション(DX)の実現を目指す請負開発型のコンサルティングサービスです。AI、iPaaS、および先端の技術を駆使して、製造プロセスの効率化、業務効率化、チームワーク強化、コスト削減、品質向上を実現します。このサービスは、製造業の課題を深く理解し、それに対する最適なデジタルソリューションを提供することで、企業が持続的な成長とイノベーションを達成できるようサポートします。
オンライン講座
製造業、主に購買・調達部門にお勤めの方々に向けた情報を配信しております。
新任の方やベテランの方、管理職を対象とした幅広いコンテンツをご用意しております。
お問い合わせ
コストダウンが利益に直結する術だと理解していても、なかなか前に進めることができない状況。そんな時は、newjiのコストダウン自動化機能で大きく利益貢献しよう!
(Β版非公開)