- お役立ち記事
- For SMEs: A Technical Guide to Preventing Weld Lines
月間76,176名の
製造業ご担当者様が閲覧しています*
*2025年3月31日現在のGoogle Analyticsのデータより
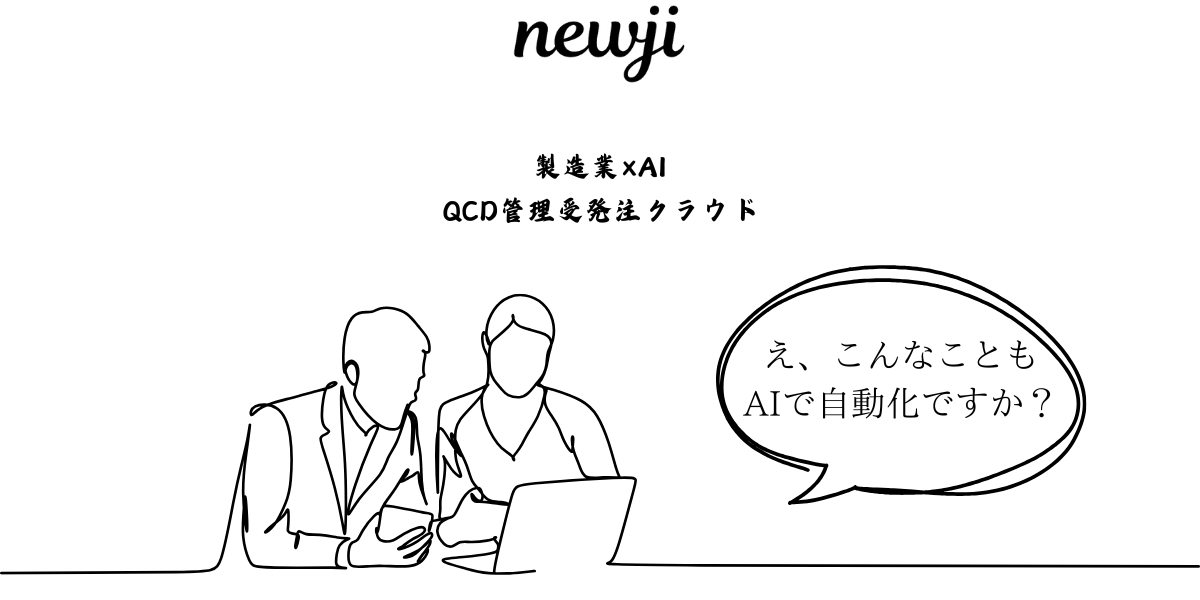
For SMEs: A Technical Guide to Preventing Weld Lines
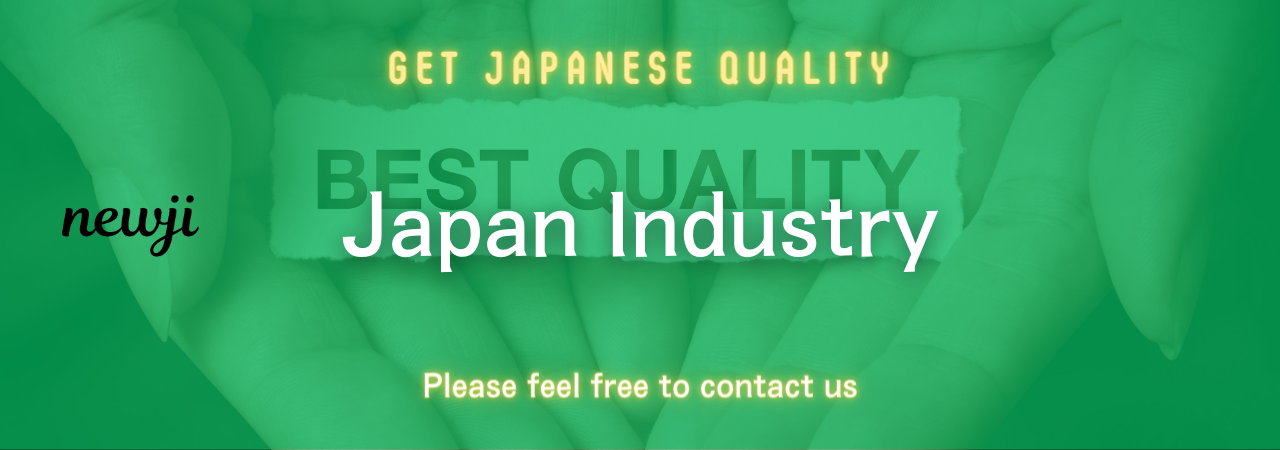
目次
Understanding Weld Lines
Weld lines, often referred to as knit lines, occur when two or more flow fronts of a melted polymer material meet and cool during the injection molding process.
These lines are noticeable defects and can pose challenges in both aesthetics and structural integrity of the molded part.
For small and medium-sized enterprises (SMEs) dealing with injection molding, understanding and preventing weld lines can significantly improve product quality.
Causes of Weld Lines
To effectively prevent weld lines, it is important to first understand their root causes.
Weld lines form due to inadequate fusion of hot plastic streams coming together.
This typically happens because of:
1. **Material Flow**: When polymer resin flows into a mold, it can split and converge around cores, inserts, or holes.
The points where the material joins are potential weld line locations.
2. **Temperature Variations**: Different temperature zones in the mold can lead to uneven cooling speeds.
If the plastic cools too quickly before the converging streams fully melt together, a weld line is formed.
3. **Pressure Levels**: Insufficient injection pressure can also result in weak material flow, leading to improper fusion and formation of weld lines.
4. **Mold Design**: Complex mold designs with intricate details or multiple gates can contribute to weld line issues.
Inaccurately balanced or symmetrically flawed designs may promote weld line formation.
Strategies to Prevent Weld Lines
Preventing weld lines requires a carefully strategized approach that encompasses the selection of materials, design customization, and process optimization.
Optimize Material Selection
The choice of material plays a critical role in weld line formation.
Certain polymers are more prone to weld lines than others.
To reduce the risk, consider these options:
– **Use Low Viscosity Materials**: Low viscosity polymers flow better and fuse more effectively, reducing the chance of weld lines.
– **Enhance Thermal Properties**: Utilizing materials with superior thermal conductivity can help maintain even temperature distributions throughout the mold.
– **Select Additives Carefully**: Additives can often change the thermal or mechanical properties of the polymer.
Additives that increase flow and fusion characteristics can be beneficial.
Improve Mold Design
Mold design adjustments can significantly reduce the incidence of weld lines.
– **Streamline Mold Paths**: Simplify flow paths by reducing obstacles and part complexities wherever possible.
Ensure smooth transitions to ease material flow.
– **Adjust Gate Design**: Properly positioning gates to support uniform and convergent flow can help minimize weld lines.
Gates should be located where they promote simultaneous and smooth filling of the mold.
– **Balance Temperature Zones**: Ensure that the mold maintains a consistent temperature to prevent localized cooling, which can result in weld lines.
Hot and cold zones should be minimized.
Refine Process Parameters
The following process modifications can aid in reducing weld lines:
– **Increase Injection Speed**: Higher injection speeds can help maintain the temperature of the polymer flow, promoting better fusion at the join line.
– **Raise Mold Temperature**: Higher mold temperatures allow for a more extended phase of plastic fusion, reducing the likelihood of premature solidification that results in weld lines.
– **Utilize Proper Cooling Techniques**: Balancing cooling times and methods can diminish premature solidification at the junction of flow fronts.
– **Adjust Injection Pressure**: Optimize injection pressure to ensure proper material flow and fusion for seamless mold filling.
Technological Solutions
For SMEs, leveraging technological advancements can bring excellent results against weld lines.
Simulation Software
Simulation tools can predict where weld lines are likely to occur, allowing engineers to make preemptive changes to the mold or process flow before actual production.
This can save time and resources on trial-and-error methods.
Advanced Molding Techniques
The employment of advanced injection molding techniques, such as gas-assisted injection and foaming technologies, can aid in minimizing the occurrence of weld lines by facilitating improved material flow and fusion.
Use of Cameras and Sensors
In-line cameras and temperature sensors can provide real-time feedback about the molding process, enabling quick adjustments to parameters in response to potential weld line issues.
Measuring Success
Implement regular quality checks and establish metrics for evaluating success in weld line reduction.
Periodic testing such as visual inspection, tensile strength tests, and surface finish evaluation should be conducted to ensure consistent quality of the molded parts.
Conclusion
Preventing weld lines is crucial for maintaining the quality and durability of injection molded products.
By understanding the root causes, optimizing material choice, refining design, and maximizing process efficiency, SMEs can greatly reduce weld line formation.
Additionally, leveraging new technologies and regularly measuring production outcomes ensures continuous improvement in the quality of plastic components.
資料ダウンロード
QCD管理受発注クラウド「newji」は、受発注部門で必要なQCD管理全てを備えた、現場特化型兼クラウド型の今世紀最高の受発注管理システムとなります。
ユーザー登録
受発注業務の効率化だけでなく、システムを導入することで、コスト削減や製品・資材のステータス可視化のほか、属人化していた受発注情報の共有化による内部不正防止や統制にも役立ちます。
NEWJI DX
製造業に特化したデジタルトランスフォーメーション(DX)の実現を目指す請負開発型のコンサルティングサービスです。AI、iPaaS、および先端の技術を駆使して、製造プロセスの効率化、業務効率化、チームワーク強化、コスト削減、品質向上を実現します。このサービスは、製造業の課題を深く理解し、それに対する最適なデジタルソリューションを提供することで、企業が持続的な成長とイノベーションを達成できるようサポートします。
製造業ニュース解説
製造業、主に購買・調達部門にお勤めの方々に向けた情報を配信しております。
新任の方やベテランの方、管理職を対象とした幅広いコンテンツをご用意しております。
お問い合わせ
コストダウンが利益に直結する術だと理解していても、なかなか前に進めることができない状況。そんな時は、newjiのコストダウン自動化機能で大きく利益貢献しよう!
(β版非公開)