- お役立ち記事
- For SMEs: How Injection Speed Affects Product Quality
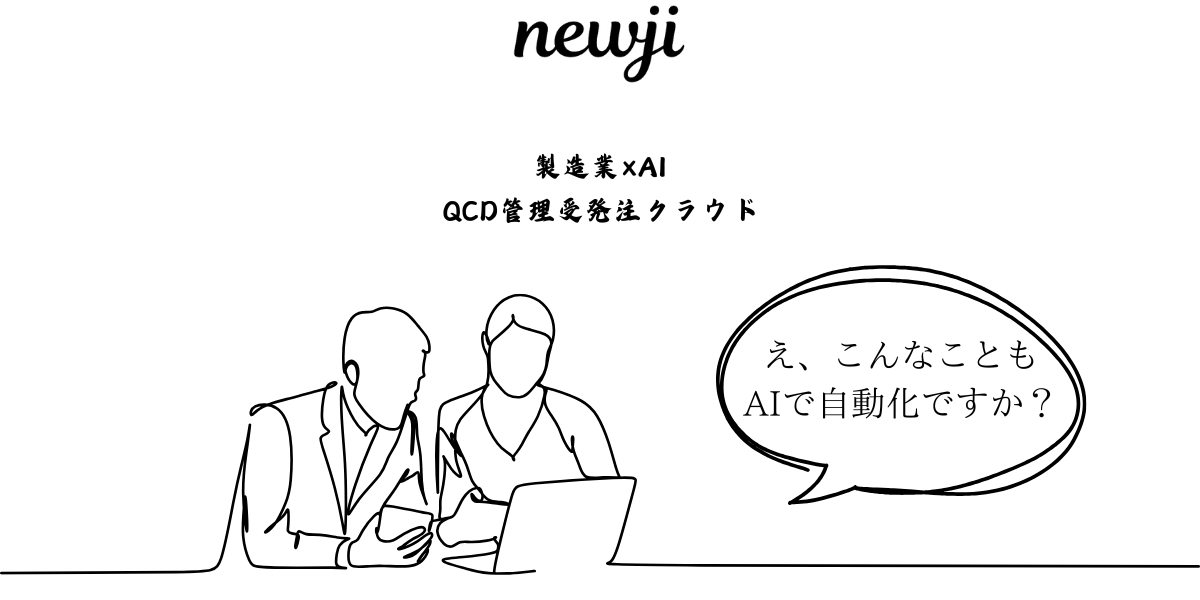
For SMEs: How Injection Speed Affects Product Quality
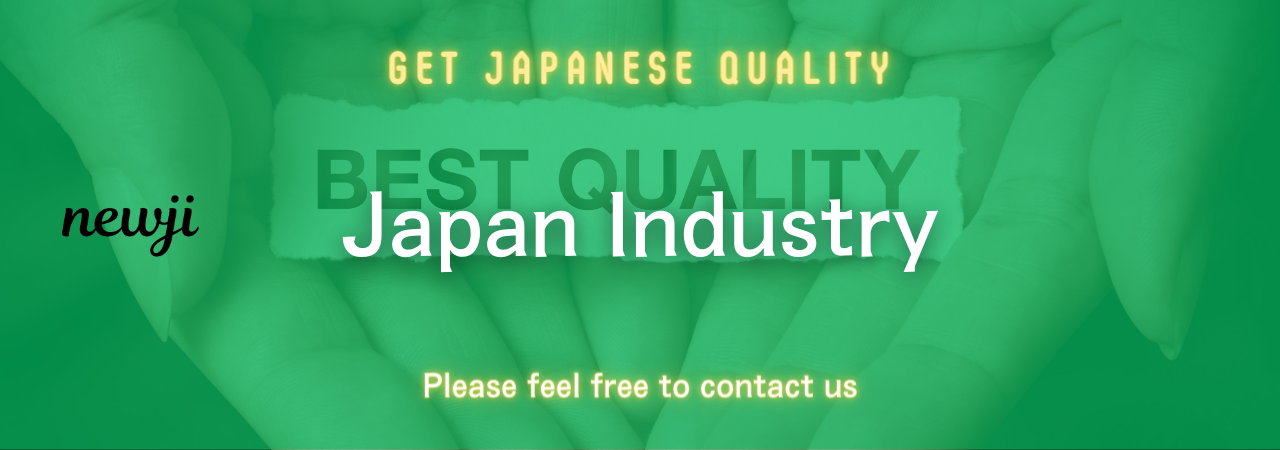
目次
Understanding Injection Molding
Injection molding is a manufacturing process used by many small and medium enterprises (SMEs) to produce a wide variety of parts, from small components to large items.
This process involves injecting molten material, typically plastic, into a mold cavity.
Once the material cools and solidifies, it takes the shape of the cavity, forming the final product.
Understanding the intricacies of this process is essential for SMEs aiming to produce high-quality products efficiently.
The Role of Injection Speed
Injection speed refers to the rate at which the molten material is injected into the mold cavity.
This parameter is crucial because it influences both the quality of the molded part and the efficiency of the production process.
The speed needs to be precisely controlled to ensure that the material fills the mold completely and that the final product is free from defects.
Injection speed can vary throughout the injection process, starting from a higher speed to quickly fill the mold, followed by a lower speed to pack the material adequately.
This dynamic control helps in achieving optimal product quality and reducing cycle times.
Effects on Product Quality
Several factors are affected by changing the injection speed during the molding process.
Understanding these effects can help SMEs optimize their production lines for better output.
Surface Finish
The surface finish of a molded part is directly influenced by the injection speed.
A higher injection speed can lead to a smoother finish as the molten material enters the mold quickly, reducing the time it has to cool or change state during filling.
However, excessively high speeds can introduce defects like flow marks or burn marks.
Balancing the speed is crucial to achieving the desired finish without compromising on quality.
Dimensional Accuracy
Injection speed also affects the dimensional accuracy of the molded part.
At a slower speed, the material might cool unevenly, causing variations in size and shape.
Conversely, a too-high speed can cause the material to flow too rapidly, potentially leading to underfills or overshoots.
Careful calibration of the injection speed helps ensure that each part maintains consistent dimensions, vital for parts that need precise fits.
Material Properties
Different materials respond to changes in injection speed in various ways.
Some materials may require higher speeds to fill the mold adequately, while others may need a slower speed to avoid degradation.
Understanding the specific material properties is important to align the injection speed with the material’s behavior.
This ensures that the structural integrity and intended properties of the finished product are preserved.
Mold Filling and Air Trapping
Proper mold filling is essential for high-quality products, and injection speed plays a critical role in this aspect.
If the speed is too low, the material may not reach all areas of the mold before starting to solidify, resulting in incomplete parts.
Conversely, too high a speed can trap air within the mold, causing unwanted air pockets or voids in the final product.
Adjusting the speed precisely helps in mitigating these issues and ensures complete mold filling.
Optimizing Injection Speed
For SMEs looking to optimize their production process, understanding how to adjust and control injection speed is key.
Here are some strategies that can be implemented:
Conducting Trials and Tests
Performing trial runs and tests can help determine the optimal injection speed for a specific product.
These trials allow for observation of how different speeds affect the end product in terms of quality and consistency.
With this knowledge, SMEs can fine-tune the process parameters to achieve better outcomes.
Using Advanced Machinery
Investing in advanced injection molding machines equipped with variable speed controls can be beneficial.
These machines offer precise control over the injection speed, allowing adjustments to be made without stopping the production line.
This flexibility enhances the ability to produce high-quality products efficiently and consistently.
Implementing Feedback Systems
Incorporating feedback systems that monitor the quality of the parts during production can provide real-time data on the effects of injection speed.
These systems can detect defects early and allow for immediate adjustments, minimizing waste and ensuring that only top-quality products are produced.
Conclusion
For SMEs engaged in injection molding, understanding how injection speed affects product quality is crucial for maintaining competitiveness and efficiency.
By mastering control over this parameter, businesses can produce reliable, high-quality products, reduce waste, and improve overall operational efficiency.
Continuing to evaluate and refine injection processes will ensure that these enterprises can meet the demands of their markets effectively.
資料ダウンロード
QCD調達購買管理クラウド「newji」は、調達購買部門で必要なQCD管理全てを備えた、現場特化型兼クラウド型の今世紀最高の購買管理システムとなります。
ユーザー登録
調達購買業務の効率化だけでなく、システムを導入することで、コスト削減や製品・資材のステータス可視化のほか、属人化していた購買情報の共有化による内部不正防止や統制にも役立ちます。
NEWJI DX
製造業に特化したデジタルトランスフォーメーション(DX)の実現を目指す請負開発型のコンサルティングサービスです。AI、iPaaS、および先端の技術を駆使して、製造プロセスの効率化、業務効率化、チームワーク強化、コスト削減、品質向上を実現します。このサービスは、製造業の課題を深く理解し、それに対する最適なデジタルソリューションを提供することで、企業が持続的な成長とイノベーションを達成できるようサポートします。
オンライン講座
製造業、主に購買・調達部門にお勤めの方々に向けた情報を配信しております。
新任の方やベテランの方、管理職を対象とした幅広いコンテンツをご用意しております。
お問い合わせ
コストダウンが利益に直結する術だと理解していても、なかなか前に進めることができない状況。そんな時は、newjiのコストダウン自動化機能で大きく利益貢献しよう!
(Β版非公開)