- お役立ち記事
- For SMEs: Maintenance Guide for Injection Molding Machines
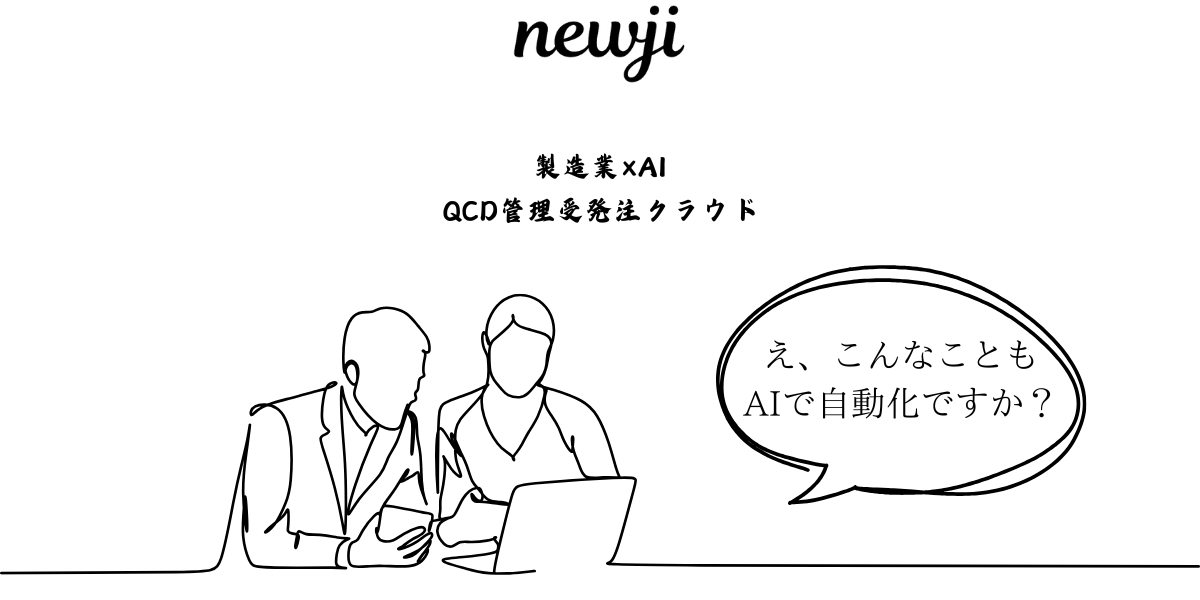
For SMEs: Maintenance Guide for Injection Molding Machines
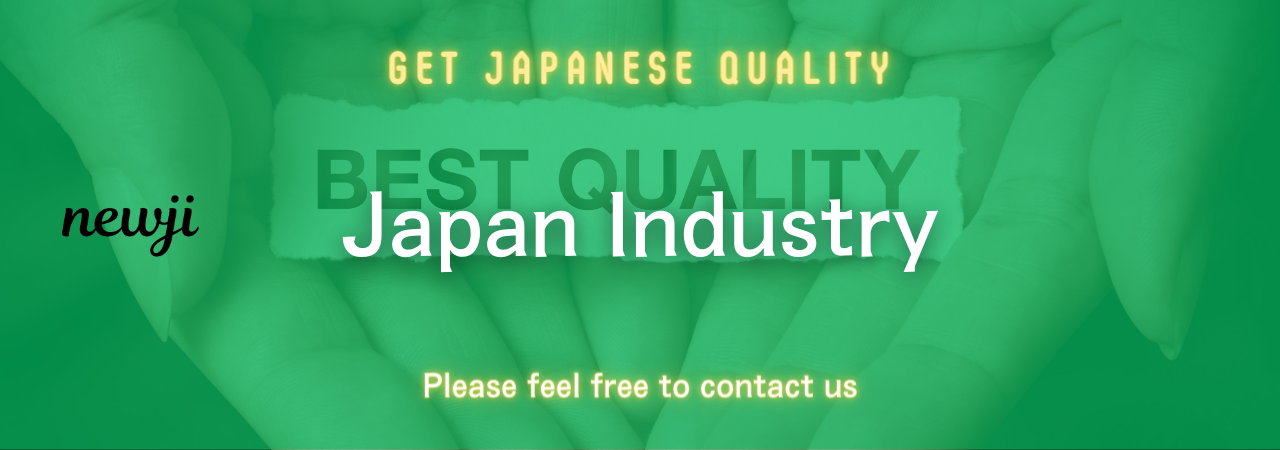
目次
Introduction to Injection Molding Machines
Injection molding machines are essential tools for small and medium-sized enterprises (SMEs) involved in the production of plastic parts.
These machines help in creating detailed and complex components with high precision and efficiency.
Understanding the basics of injection molding machines, including their maintenance, can greatly enhance production capabilities and extend the machinery’s lifespan.
Components of Injection Molding Machines
Injection molding machines consist of two main parts: the injection unit and the clamping unit.
The injection unit is responsible for melting and injecting the plastic material into a mold, while the clamping unit holds the mold in place during the injection and cooling process.
Both units work in harmony to produce the final plastic part.
Injection Unit
The injection unit comprises several key components that work together to handle the plastic material.
These include the hopper, which holds the raw plastic pellets, the barrel that heats and melts the plastic, and the screw or plunger that pushes the molten plastic into the mold.
Proper maintenance of these parts is critical for ensuring consistent part quality.
Clamping Unit
The clamping unit, on the other hand, includes the mold and the mechanism for opening and closing it.
It features a movable platen and a fixed platen, between which the mold sits.
This unit provides the necessary force to keep the mold closed during injection and cooling, preventing any defects in the final product.
Importance of Regular Maintenance
Regular maintenance of injection molding machines is crucial to avoid downtime and costly repairs.
Proper upkeep ensures the machines operate smoothly, produce high-quality parts, and maintain efficiency.
Neglecting maintenance can lead to unplanned outages, increased waste, and even damage to equipment.
Planned Maintenance
Planned maintenance involves routine checks and upkeep of machine components.
Scheduling regular inspections can help identify potential issues before they become major problems.
This includes checking for wear and tear on mechanical parts, ensuring electrical systems are functioning properly, and cleaning and lubricating moving parts.
Predictive Maintenance
Predictive maintenance uses data and analytics to predict when a machine or component may fail.
By monitoring machine performance metrics, such as vibration, temperature, and pressure, SMEs can address issues proactively.
This approach minimizes unexpected breakdowns and optimizes machine uptime.
Maintenance Checklist for SMEs
Having a maintenance checklist can help SMEs streamline their maintenance processes and ensure that all necessary tasks are completed regularly.
Below is a helpful guide for a basic maintenance routine:
Daily Maintenance
– Check and top up lubricants to reduce friction and wear on moving parts.
– Inspect hydraulic fluid levels and check for leaks.
– Examine the barrel and screw for any signs of wear or damage.
– Ensure the cooling system is functioning correctly, maintaining optimal temperatures.
Weekly Maintenance
– Clean the hopper and remove any accumulated plastic material or debris.
– Inspect and clean the mold to prevent residue build-up, which can cause defects.
– Check the operation of sensors and switches to ensure consistent performance.
Monthly Maintenance
– Inspect electrical connections for signs of wear, corrosion, or damage.
– Review and calibrate machine settings to ensure accuracy and repeatability.
– Evaluate safety features and mechanisms to maintain a safe working environment.
Common Maintenance Challenges
While regular maintenance is vital, SMEs may face several challenges when keeping up with their injection molding machines.
Resource Limitations
SMEs often have limited resources, including manpower and budget constraints, which can make it difficult to carry out regular maintenance effectively.
It’s important to prioritize critical maintenance tasks and allocate resources efficiently to address these limitations.
Skill Gaps
A shortage of skilled personnel to conduct maintenance may also pose a challenge.
SMEs can address these gaps by investing in training programs to upskill their workforce, ensuring they have the necessary knowledge to maintain and troubleshoot machines.
Documentation and Tracking
Effective documentation and tracking of maintenance activities help in understanding patterns and spotting recurring issues.
Implementing a maintenance tracking system can significantly improve the efficiency and visibility of maintenance operations.
Conclusion: Ensuring Longevity and Efficiency
For SMEs, maintaining injection molding machines is vital for business success.
Efficient upkeep ensures consistent production quality, minimizes downtime, and reduces long-term expenses.
By adhering to regular maintenance schedules, addressing challenges, and leveraging predictive maintenance technologies, SMEs can ensure their injection molding operations run smoothly.
Employing these practices can lead to enhanced productivity, cost savings, and a prolonged lifespan of the equipment, ultimately contributing to the enterprise’s competitive edge in the market.
資料ダウンロード
QCD調達購買管理クラウド「newji」は、調達購買部門で必要なQCD管理全てを備えた、現場特化型兼クラウド型の今世紀最高の購買管理システムとなります。
ユーザー登録
調達購買業務の効率化だけでなく、システムを導入することで、コスト削減や製品・資材のステータス可視化のほか、属人化していた購買情報の共有化による内部不正防止や統制にも役立ちます。
NEWJI DX
製造業に特化したデジタルトランスフォーメーション(DX)の実現を目指す請負開発型のコンサルティングサービスです。AI、iPaaS、および先端の技術を駆使して、製造プロセスの効率化、業務効率化、チームワーク強化、コスト削減、品質向上を実現します。このサービスは、製造業の課題を深く理解し、それに対する最適なデジタルソリューションを提供することで、企業が持続的な成長とイノベーションを達成できるようサポートします。
オンライン講座
製造業、主に購買・調達部門にお勤めの方々に向けた情報を配信しております。
新任の方やベテランの方、管理職を対象とした幅広いコンテンツをご用意しております。
お問い合わせ
コストダウンが利益に直結する術だと理解していても、なかなか前に進めることができない状況。そんな時は、newjiのコストダウン自動化機能で大きく利益貢献しよう!
(Β版非公開)