- お役立ち記事
- For SMEs: Tips for Avoiding PET Product Troubles and Managing Quality
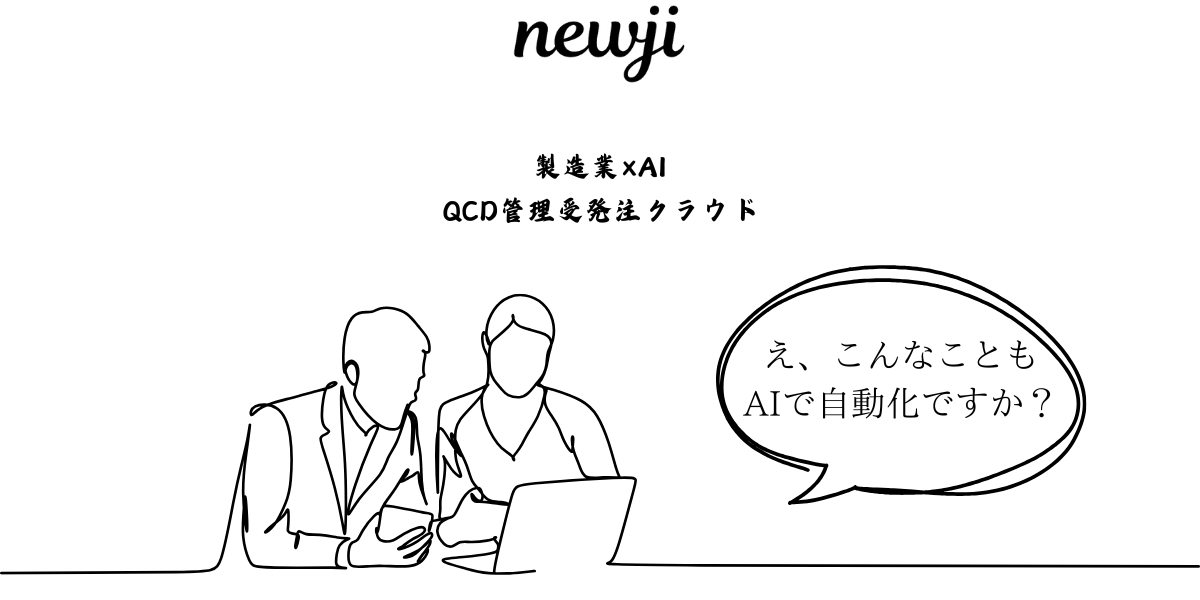
For SMEs: Tips for Avoiding PET Product Troubles and Managing Quality
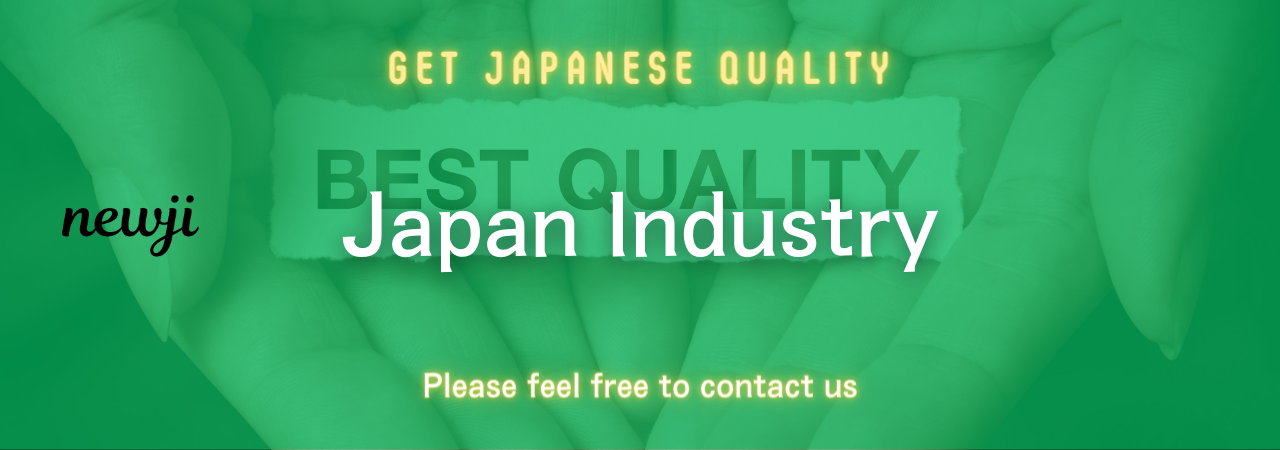
目次
Understanding the Importance of Quality in PET Products
For small and medium-sized enterprises (SMEs), maintaining the quality of PET (polyethylene terephthalate) products is crucial for satisfying customers and ensuring business growth.
PET, a popular plastic material, is widely used in packaging, bottles, and textiles due to its strength, transparency, and recyclability.
However, managing the quality of PET products can be challenging, especially for SMEs with limited resources.
Implementing effective quality control measures can prevent potential product troubles and enhance customer satisfaction.
In this article, we’ll explore some useful tips for avoiding common PET product issues and how to effectively manage quality.
Common Quality Issues in PET Products
Before delving into quality management tips, it’s essential to recognize the common issues that SMEs might face with PET products.
These include defects like bubbles or impurities in the plastic, uneven thickness, and improper dimensional stability.
Poor quality PET products can lead to customer complaints, returns, and a damaged reputation.
Therefore, addressing these issues proactively is vital for any SME involved in the production or distribution of PET products.
Bubble Formation
One common issue in PET manufacturing is the formation of bubbles.
These bubbles can occur due to improper heating or cooling during production, leading to weak spots in the material that compromise its strength.
Impurities
Impurities can be introduced at various stages, from raw material handling to the manufacturing process.
These contaminants can affect the appearance and functionality of the final product.
Dimensional Instability
Dimensional instability refers to changes in the size or shape of the PET product.
This can happen during or after production and impacts the product’s fitting and usability.
Tips to Avoid PET Product Troubles
To prevent quality issues in PET products, SMEs should adopt strategies that focus on every aspect of production, from raw material selection to final inspection.
Here are some practical tips:
Select High-Quality Materials
The foundation of any high-quality PET product lies in the raw materials used.
Source your PET resin from reputable suppliers known for their consistent quality.
Ensure to verify the material’s specifications and compatibility with your production needs.
Purchasing high-quality raw materials might come at a higher cost, but it pays off by reducing defects and waste in the long run.
Implement Rigorous Quality Control
Develop a detailed quality control plan that outlines inspection points throughout the production process.
Regularly check for defects such as bubbles, impurities, and dimensional instability.
Ensure your staff is adequately trained to identify defects and understand acceptable quality standards.
Use advanced inspection tools like vision systems or scanners to automate defect detection and reduce human error.
Optimize Manufacturing Processes
Carefully monitor and control the temperature, pressure, and cooling rates during production.
This helps prevent bubble formation and ensures even material distribution.
Regularly maintain and calibrate your machinery to keep it running efficiently.
Process optimization not only enhances product quality but also improves production speed, reducing costs.
Conduct Regular Quality Audits
Regularly audit your entire production process to identify potential areas of improvement.
Quality audits help monitor adherence to standards and offer insights into proactive measures to counteract potential issues.
Consider employing third-party auditors to provide an unbiased assessment of your quality management program.
Effective Quality Management Practices
Incorporating effective quality management practices into your operations can significantly enhance the reliability of PET products.
Here are some strategies that can be useful:
Develop a Quality Management System (QMS)
Implement a QMS tailored to your SME’s needs.
A QMS provides a structured framework for maintaining product quality and ensuring compliance with industry standards.
It also facilitates continuous improvement by documenting and analyzing quality performance over time.
Engage Your Workforce in Quality Initiatives
Encourage your employees to participate in quality improvement initiatives actively.
Conduct regular training sessions to ensure they understand their roles in maintaining product quality.
Create an environment where employees feel comfortable suggesting process improvements.
Build Strong Relationships with Suppliers
Work closely with material and equipment suppliers to ensure they understand your quality expectations.
Building strong partnerships with suppliers can lead to better quality raw materials and support in managing supply chain risks.
Regular communication can also alert you to changes in the supplier’s processes that may impact product quality.
Utilize Technology for Quality Assurance
Leverage technology to enhance quality assurance efforts.
Industry 4.0 solutions like IoT devices, machine learning, and data analytics can provide real-time insights into production processes.
These technologies can help predict potential defects before they occur and enable prompt corrective actions.
Conclusion
For SMEs, avoiding PET product troubles and managing quality is a multifaceted challenge that requires attention to detail and diligence.
By selecting high-quality materials, implementing rigorous quality control, optimizing manufacturing processes, and maintaining an effective quality management system, SMEs can ensure their PET products meet high standards.
Remember, maintaining quality is an ongoing process that requires commitment from every level of the organization.
By focusing on quality, SMEs can not only improve their market position but also build lasting relationships with satisfied customers.
資料ダウンロード
QCD調達購買管理クラウド「newji」は、調達購買部門で必要なQCD管理全てを備えた、現場特化型兼クラウド型の今世紀最高の購買管理システムとなります。
ユーザー登録
調達購買業務の効率化だけでなく、システムを導入することで、コスト削減や製品・資材のステータス可視化のほか、属人化していた購買情報の共有化による内部不正防止や統制にも役立ちます。
NEWJI DX
製造業に特化したデジタルトランスフォーメーション(DX)の実現を目指す請負開発型のコンサルティングサービスです。AI、iPaaS、および先端の技術を駆使して、製造プロセスの効率化、業務効率化、チームワーク強化、コスト削減、品質向上を実現します。このサービスは、製造業の課題を深く理解し、それに対する最適なデジタルソリューションを提供することで、企業が持続的な成長とイノベーションを達成できるようサポートします。
オンライン講座
製造業、主に購買・調達部門にお勤めの方々に向けた情報を配信しております。
新任の方やベテランの方、管理職を対象とした幅広いコンテンツをご用意しております。
お問い合わせ
コストダウンが利益に直結する術だと理解していても、なかなか前に進めることができない状況。そんな時は、newjiのコストダウン自動化機能で大きく利益貢献しよう!
(Β版非公開)