- お役立ち記事
- For the metal materials sector! How to improve product performance by optimizing material design
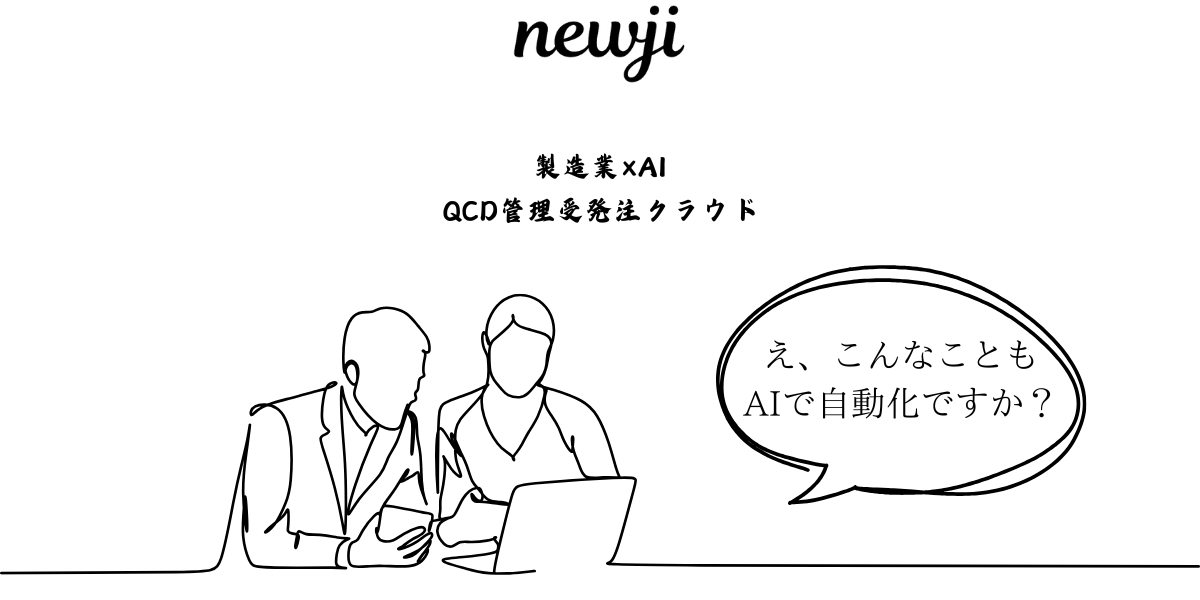
For the metal materials sector! How to improve product performance by optimizing material design
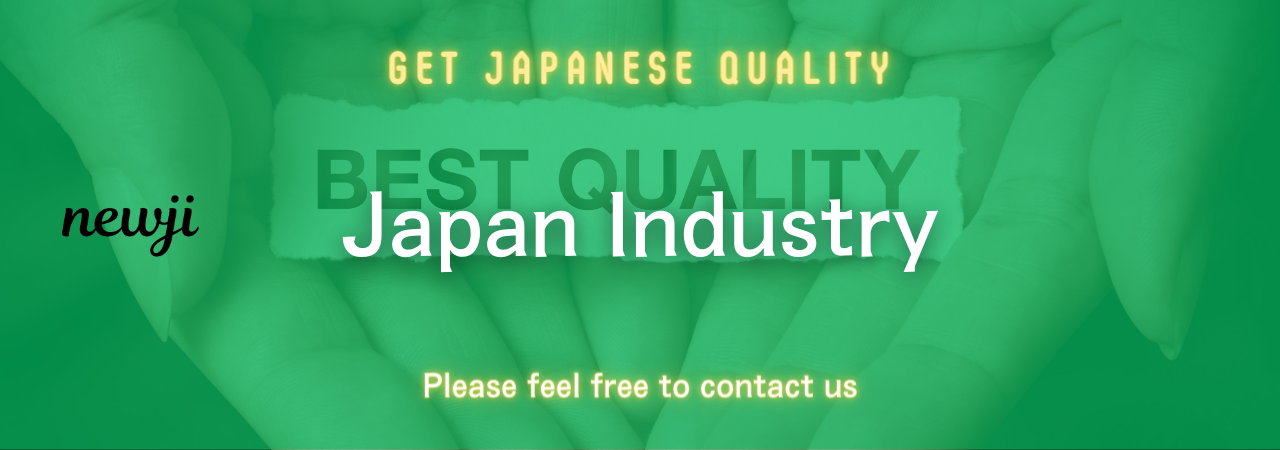
目次
Understanding Material Design in Metals
The metal materials sector plays a critical role in a wide array of industries, including construction, automotive, aerospace, and electronics.
To meet the growing demand for advanced metal products, manufacturers are constantly seeking ways to optimize material design to improve product performance.
By focusing on specific design strategies, they can enhance the strength, durability, and overall quality of metal products while reducing costs and environmental impact.
The Importance of Material Design
Material design involves selecting and configuring materials in a way that meets the desired mechanical, thermal, and chemical properties of a product.
In metal materials, optimizing design is crucial for ensuring that the final product can withstand specific stresses, temperatures, and environmental conditions.
A well-designed metal component will provide consistency in performance and longevity, leading to higher customer satisfaction and a competitive edge in the market.
Factors Influencing Metal Material Design
Several factors play a role in the design and optimization of metal materials:
1. **Chemical Composition**: The combination of elements in an alloy directly impacts its properties.
For example, adding elements like chromium and nickel can increase corrosion resistance, making them ideal for stainless steels used in harsh environments.
2. **Microstructure**: The arrangement of microscopic particles within a metal determines its mechanical properties.
Through processes like heat treatment and alloying, manufacturers can manipulate the microstructure to enhance characteristics such as hardness and ductility.
3. **Manufacturing Processes**: Techniques such as casting, forging, and extrusion influence the final properties of metal products.
Each method offers unique benefits, such as improved strength or precision, and must be carefully selected based on the intended application.
4. **Environmental Conditions**: Metals must be designed to withstand different environments, such as high temperatures, pressure, or exposure to corrosive substances.
Tailoring material design to these conditions ensures reliability and safety.
Techniques for Optimizing Material Design
To improve product performance through material design, manufacturers can employ several techniques:
Advanced Alloy Development
By experimenting with different combinations of elements, manufacturers can develop new alloys with enhanced properties.
Advanced computational tools and simulation software allow researchers to predict the behavior of new alloys before they are produced, saving time and resources in the development process.
These innovations can lead to stronger, lighter, and more durable metal products that meet the demands of current and future applications.
Heat Treatment Optimization
Heat treatment processes such as annealing, quenching, and tempering are critical to shaping the microstructure of metals.
By carefully controlling the temperature and cooling rates, manufacturers can achieve desired mechanical properties, such as improved toughness or reduced brittleness.
Using refined heat treatment techniques, companies can enhance the performance of metal materials while minimizing energy consumption.
Surface Engineering
Coating and surface treatments can significantly improve the durability and performance of metal products.
Methods such as galvanizing, anodizing, or applying protective coatings help protect metals from corrosion, wear, and fatigue.
These surface treatments are especially important in sectors where metals are exposed to harsh environments, extending the life of components and reducing maintenance costs.
Testing and Validation
Once a new design has been developed, rigorous testing and validation processes are essential to ensure that metal products meet quality and safety standards.
This includes conducting mechanical tests, such as tensile strength and impact resistance assessments, as well as environmental testing under simulated conditions.
Feedback from these tests allows for further refinement and optimization, leading to continuous improvement of metal designs.
The Role of Data and Technology
In today’s rapidly evolving manufacturing landscape, data and technology play a crucial role in optimizing material design for metals.
With the advent of Industry 4.0, manufacturers now have access to vast amounts of data generated by smart sensors and IoT devices throughout the production process.
This data provides valuable insights into material performance, enabling more informed decision-making and efficient design processes.
Machine Learning and AI
Machine learning and artificial intelligence are transforming the way manufacturers approach material design.
These technologies can analyze large datasets to identify patterns and predict outcomes, helping researchers develop new materials with desired properties quicker than traditional methods.
AI-driven solutions streamline the optimization process and inspire innovative approaches to complex material challenges.
Simulation and Modeling Tools
Advanced simulation and modeling software allow manufacturers to test different design scenarios virtually.
By replicating real-world conditions, these tools help predict the performance of metal products under various stresses and temperatures.
Simulations reduce the reliance on physical prototypes, leading to faster development cycles and lower production costs, while ensuring high-quality designs.
Conclusion
Optimizing material design in the metal materials sector is crucial to creating high-performance, reliable products across industries.
By focusing on factors such as chemical composition, microstructure, and environmental conditions, manufacturers can enhance product quality and efficiency.
The integration of technology and data analytics into the design process unlocks new opportunities for innovation and continuous improvement.
As the demand for sophisticated metal products increases, companies that prioritize material design optimization will be well-equipped to meet the challenges of the future.
Staying at the forefront of these advancements not only ensures competitive advantages but also contributes to sustainable practices and innovative solutions that drive progress across the industry.
資料ダウンロード
QCD調達購買管理クラウド「newji」は、調達購買部門で必要なQCD管理全てを備えた、現場特化型兼クラウド型の今世紀最高の購買管理システムとなります。
ユーザー登録
調達購買業務の効率化だけでなく、システムを導入することで、コスト削減や製品・資材のステータス可視化のほか、属人化していた購買情報の共有化による内部不正防止や統制にも役立ちます。
NEWJI DX
製造業に特化したデジタルトランスフォーメーション(DX)の実現を目指す請負開発型のコンサルティングサービスです。AI、iPaaS、および先端の技術を駆使して、製造プロセスの効率化、業務効率化、チームワーク強化、コスト削減、品質向上を実現します。このサービスは、製造業の課題を深く理解し、それに対する最適なデジタルソリューションを提供することで、企業が持続的な成長とイノベーションを達成できるようサポートします。
オンライン講座
製造業、主に購買・調達部門にお勤めの方々に向けた情報を配信しております。
新任の方やベテランの方、管理職を対象とした幅広いコンテンツをご用意しております。
お問い合わせ
コストダウンが利益に直結する術だと理解していても、なかなか前に進めることができない状況。そんな時は、newjiのコストダウン自動化機能で大きく利益貢献しよう!
(Β版非公開)