- お役立ち記事
- Forging Principles and Benefits: Forging technology for metal forming and part fabrication
Forging Principles and Benefits: Forging technology for metal forming and part fabrication
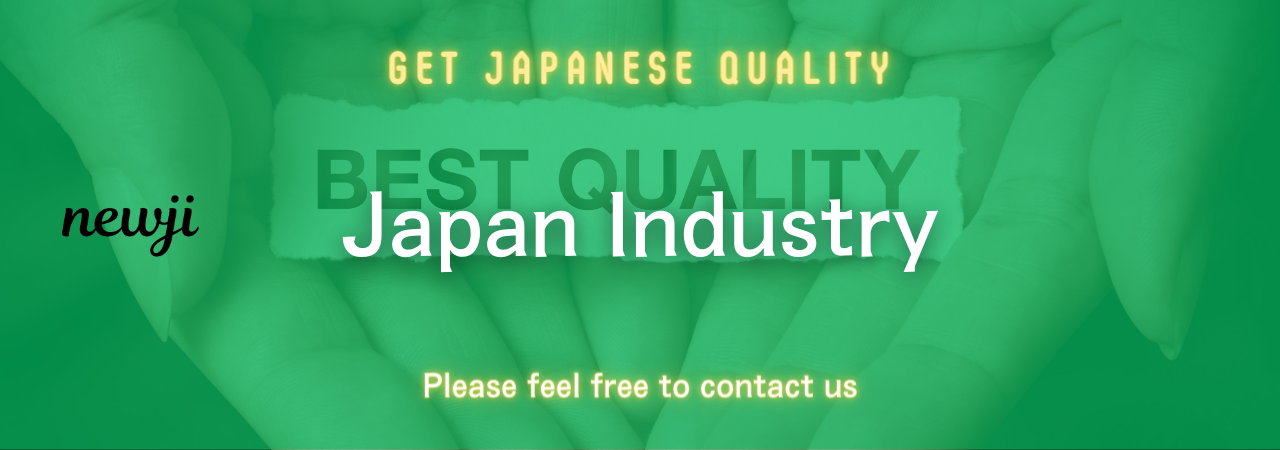
Forging technology has been around for centuries, dating back to the early days of human civilization. From ancient blacksmiths shaping swords and armor to modern-day engineers crafting parts for aerospace and automotive industries, forging has been instrumental in materializing durable and robust metal components.
At its core, forging involves shaping metal using localized compressive forces. This process, which can be done using hammers, presses, or dies, significantly improves the structural integrity and strength of the metal. In this article, we’ll delve into the key principles of forging, explore the different types of forging processes, and outline the benefits that make this age-old technique still relevant in today’s sophisticated manufacturing landscape.
目次
Principles of Forging Technology
Forging is predicated upon several fundamental principles designed to manipulate the metal into the desired shape without compromising its material characteristics. Here are some of the most important aspects:
1. Plastic Deformation
Plastic deformation is the cornerstone of forging. Unlike elastic deformation, where the material returns to its original shape upon removal of the load, plastic deformation involves altering the shape of the metal permanently. This makes the material easier to manipulate and shape into complex forms.
2. Work Hardening
As the metal is deformed under high pressures, its microstructure changes in a way that increases its strength and hardness. This phenomenon is known as work hardening, which benefits the final product by enhancing its durability and resistance to wear and fatigue.
3. Grain Structure Refinement
One of the unique advantages of forging is the ability to refine the grain structure of the metal. Grains become aligned in the direction of the deformation, which optimizes the mechanical properties. This refinement contributes to the metal’s strength, toughness, and fatigue resistance.
Types of Forging Processes
Forging can be classified into several different types based on the temperature, equipment used, and the complexity of the parts being produced. Each type has its specific advantages and applications:
1. Hot Forging
Hot forging is performed at temperatures generally above the recrystallization point of the metal. This type of forging is advantageous because the metal becomes more ductile and less resistant to deformation. Hot forging is widely used for producing components such as crankshafts, gears, and hand tools.
2. Cold Forging
Cold forging is performed at or near room temperature and is typically used for relatively simple shapes. The benefits include better surface finish and tighter dimensional tolerances, but the downside is that more force is required to deform the metal. It is commonly used for producing fasteners, bolts, and rivets.
3. Closed-Die Forging
Also known as impression-die forging, this process involves placing a heated metal billet in a die that contains an impression of the desired shape. The metal is then forced to fill the die cavities. This method is ideal for producing complex shapes with high dimensional accuracy. Examples of parts made using closed-die forging include turbine blades and connecting rods.
4. Open-Die Forging
In open-die forging, the metal is not confined entirely within the dies, allowing for a broader range of shapes and sizes. This process is generally used for larger components such as shafts, discs, and rings. It offers greater flexibility but requires more skill to achieve the desired dimensions and shape.
Benefits of Forging Technology
Forging technology offers several significant benefits that have sustained its relevance in various industries. Below are some of the key advantages.
1. Enhanced Strength and Durability
The consolidation and alignment of the grains during the forging process result in a product that has higher tensile strength and toughness compared to those produced through other manufacturing methods. This makes forged components highly reliable, even in demanding applications.
2. Superior Fatigue Resistance
Forged components exhibit excellent fatigue resistance due to the refined microstructure and work hardening effects. This is particularly crucial for parts subjected to cyclic loads, such as aircraft landing gear, automotive crankshafts, and industrial machinery.
3. Consistency and Repeatability
The forging process ensures that each part is dimensionally consistent and repeatable. This is essential for mass production scenarios where maintaining high standards of quality is imperative.
4. Material Efficiency
Forging can produce components with minimum waste material. The precision and control over the material flow reduce the need for excess metal, making forging a cost-effective and resource-efficient process.
5. Versatility
The forging process is highly adaptable, allowing for the production of a wide range of shapes and sizes. Whether it’s a small bolt or a large industrial gear, forging can handle it all. This versatility is unmatched by many other manufacturing methods.
Application Areas of Forging
The advantages of forging technology make it suitable for various industries. Here are some practical applications:
– Automotive Industry:Forged components such as crankshafts, gears, and connecting rods are vital for the performance and durability of vehicles.
– Aerospace: The aerospace industry relies heavily on forged parts for landing gear, engine components, and structural frames due to their strength and reliability.
– Oil and Gas:Forged valves, pipelines, and drilling components are crucial for the robust and fail-safe operation of oil and gas extraction and processing systems.
– Military:The military sector uses forged parts for weaponry, vehicles, and equipment, demanding high durability and reliability under extreme conditions.
Future Prospects and Innovations
While forging technology is deeply rooted in tradition, modern advancements continue to evolve the process. Innovations such as computer-aided design (CAD) and simulation technologies have revolutionized the planning and execution of forging operations. Additionally, the development of new forging materials and hybrid processes that combine forging with other techniques ensures that this technology remains at the forefront of manufacturing.
In conclusion, forging technology’s principles and benefits prove it to be an indispensable method for metal forming and part fabrication. Its ability to produce high-strength, reliable, and cost-effective components keeps it vital for various industrial applications. As technology progresses, the forging process is set to become even more efficient and versatile, paving the way for new possibilities in manufacturing.
資料ダウンロード
QCD調達購買管理クラウド「newji」は、調達購買部門で必要なQCD管理全てを備えた、現場特化型兼クラウド型の今世紀最高の購買管理システムとなります。
ユーザー登録
調達購買業務の効率化だけでなく、システムを導入することで、コスト削減や製品・資材のステータス可視化のほか、属人化していた購買情報の共有化による内部不正防止や統制にも役立ちます。
NEWJI DX
製造業に特化したデジタルトランスフォーメーション(DX)の実現を目指す請負開発型のコンサルティングサービスです。AI、iPaaS、および先端の技術を駆使して、製造プロセスの効率化、業務効率化、チームワーク強化、コスト削減、品質向上を実現します。このサービスは、製造業の課題を深く理解し、それに対する最適なデジタルソリューションを提供することで、企業が持続的な成長とイノベーションを達成できるようサポートします。
オンライン講座
製造業、主に購買・調達部門にお勤めの方々に向けた情報を配信しております。
新任の方やベテランの方、管理職を対象とした幅広いコンテンツをご用意しております。
お問い合わせ
コストダウンが利益に直結する術だと理解していても、なかなか前に進めることができない状況。そんな時は、newjiのコストダウン自動化機能で大きく利益貢献しよう!
(Β版非公開)