- お役立ち記事
- Fostering a Quality Mindset in Quality Management and Ensuring Its Penetration on the Shop Floor
月間76,176名の
製造業ご担当者様が閲覧しています*
*2025年3月31日現在のGoogle Analyticsのデータより
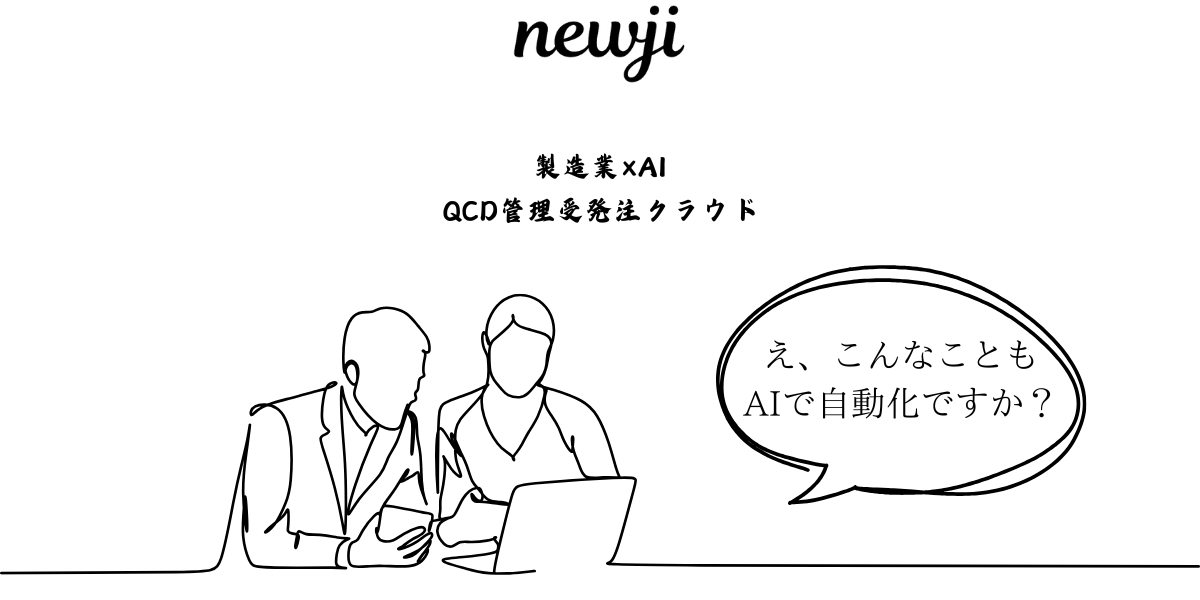
Fostering a Quality Mindset in Quality Management and Ensuring Its Penetration on the Shop Floor
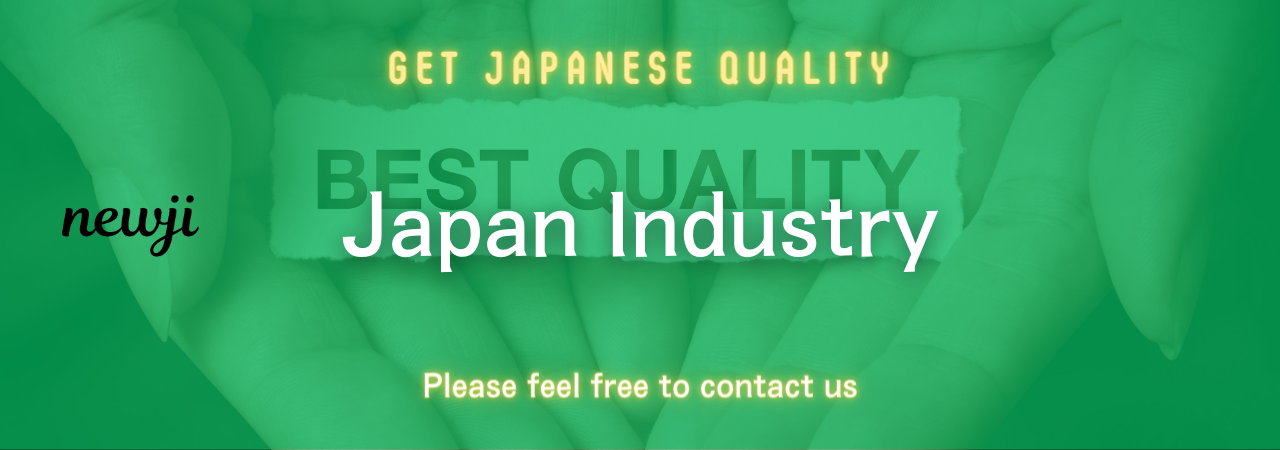
Quality management is an essential aspect of any successful business.
It ensures that products and services meet or exceed customer expectations.
To achieve this, companies must foster a quality mindset within their organization and ensure it penetrates down to the shop floor.
This article will delve into the strategies and practices to help instill a quality mindset and maintain it effectively.
目次
Understanding the Quality Mindset
A quality mindset is a culture that prioritizes quality in every aspect of the business.
It involves a commitment to continuous improvement, customer satisfaction, and employee engagement.
When a company has a quality mindset, every employee understands the importance of their role in maintaining and enhancing product quality.
They are motivated to identify and solve problems, resulting in a more efficient and effective production process.
The Importance of Leadership
Leading by Example
Leaders play a crucial role in fostering a quality mindset.
They set the tone for the entire organization.
By demonstrating a commitment to quality, leaders can influence their teams to follow suit.
It is vital for leaders to actively participate in quality initiatives, show enthusiasm for continuous improvement, and recognize employees’ efforts in achieving high standards.
Training and Development
Continuous training is essential for maintaining a quality mindset.
Investing in employee development helps to ensure that everyone is equipped with the necessary skills and knowledge to perform their tasks effectively.
Leaders should prioritize quality management training programs and encourage employees to pursue further education and certifications.
Creating a Culture of Quality
Open Communication
Communication is key to building a quality-focused culture.
Encouraging open dialogue between employees at all levels helps to create an environment where everyone feels comfortable sharing their ideas and concerns.
Regular team meetings and feedback sessions can facilitate this process.
By addressing issues promptly and collectively, companies can prevent defects and improve overall quality.
Employee Empowerment
Empowering employees to take ownership of their work is crucial for maintaining a quality mindset.
When employees feel responsible for the quality of their output, they are more likely to take pride in their work and strive for excellence.
Giving employees the authority to make decisions and solve problems fosters a sense of ownership and accountability.
Implementing Quality Management Systems
Effective quality management systems (QMS) are essential for ensuring that a quality mindset is embedded throughout the organization.
These systems provide a structured approach to managing processes, monitoring performance, and implementing improvements.
Standard Operating Procedures
Developing and maintaining standard operating procedures (SOPs) is a fundamental aspect of a QMS.
SOPs ensure consistency and uniformity in the production process.
They provide clear guidelines for employees to follow, reducing the likelihood of errors and deviations from quality standards.
Regular Audits and Inspections
Conducting regular audits and inspections helps to identify areas for improvement and ensure compliance with quality standards.
These assessments can be internal or external and should cover all aspects of the production process.
By regularly reviewing and updating procedures, companies can maintain high standards and continuously improve their operations.
Corrective and Preventive Actions
Implementing corrective and preventive actions (CAPAs) is essential for addressing quality issues and preventing them from recurring.
When a problem is identified, a CAPA process should be initiated to investigate the root cause and implement appropriate measures to rectify and prevent future occurrences.
This proactive approach to quality management helps to minimize defects and enhance overall product quality.
Ensuring Penetration on the Shop Floor
Visual Management
Visual management tools, such as charts, graphs, and dashboards, can help to communicate quality performance metrics to shop floor employees.
These tools provide real-time visibility into key performance indicators (KPIs) and enable employees to monitor progress and identify areas for improvement.
By making quality metrics easily accessible, companies can keep employees informed and engaged in quality initiatives.
Kaizen and Continuous Improvement
The concept of kaizen, or continuous improvement, is integral to fostering a quality mindset on the shop floor.
Kaizen encourages employees to constantly look for ways to improve processes and eliminate waste.
Implementing small, incremental changes can lead to significant improvements in quality and efficiency over time.
By fostering a culture of continuous improvement, companies can ensure that quality remains a top priority.
Team-Based Problem Solving
Collaborative problem-solving is an effective way to address quality issues and implement improvements on the shop floor.
Creating cross-functional teams that include employees from different departments can help to identify and solve problems more effectively.
Encouraging teamwork and collaboration fosters a sense of shared responsibility for quality and drives collective efforts toward achieving high standards.
Conclusion
Fostering a quality mindset in quality management and ensuring its penetration on the shop floor is crucial for achieving long-term success.
By prioritizing leadership, creating a culture of quality, implementing effective quality management systems, and engaging shop floor employees, companies can establish and maintain high standards.
Continuous improvement, open communication, and employee empowerment are key elements in building a sustainable quality-focused culture.
By investing in these practices, businesses can enhance customer satisfaction, improve efficiency, and achieve excellence in their products and services.
資料ダウンロード
QCD管理受発注クラウド「newji」は、受発注部門で必要なQCD管理全てを備えた、現場特化型兼クラウド型の今世紀最高の受発注管理システムとなります。
ユーザー登録
受発注業務の効率化だけでなく、システムを導入することで、コスト削減や製品・資材のステータス可視化のほか、属人化していた受発注情報の共有化による内部不正防止や統制にも役立ちます。
NEWJI DX
製造業に特化したデジタルトランスフォーメーション(DX)の実現を目指す請負開発型のコンサルティングサービスです。AI、iPaaS、および先端の技術を駆使して、製造プロセスの効率化、業務効率化、チームワーク強化、コスト削減、品質向上を実現します。このサービスは、製造業の課題を深く理解し、それに対する最適なデジタルソリューションを提供することで、企業が持続的な成長とイノベーションを達成できるようサポートします。
製造業ニュース解説
製造業、主に購買・調達部門にお勤めの方々に向けた情報を配信しております。
新任の方やベテランの方、管理職を対象とした幅広いコンテンツをご用意しております。
お問い合わせ
コストダウンが利益に直結する術だと理解していても、なかなか前に進めることができない状況。そんな時は、newjiのコストダウン自動化機能で大きく利益貢献しよう!
(β版非公開)