- お役立ち記事
- Fracture mechanics and damage tolerance design
月間76,176名の
製造業ご担当者様が閲覧しています*
*2025年3月31日現在のGoogle Analyticsのデータより
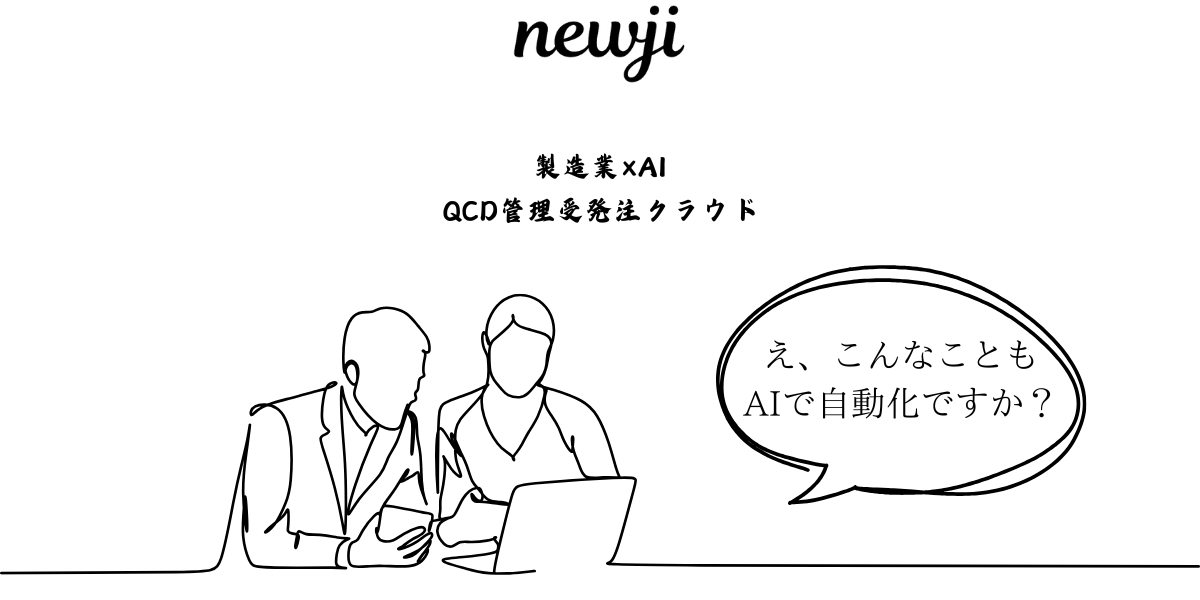
Fracture mechanics and damage tolerance design
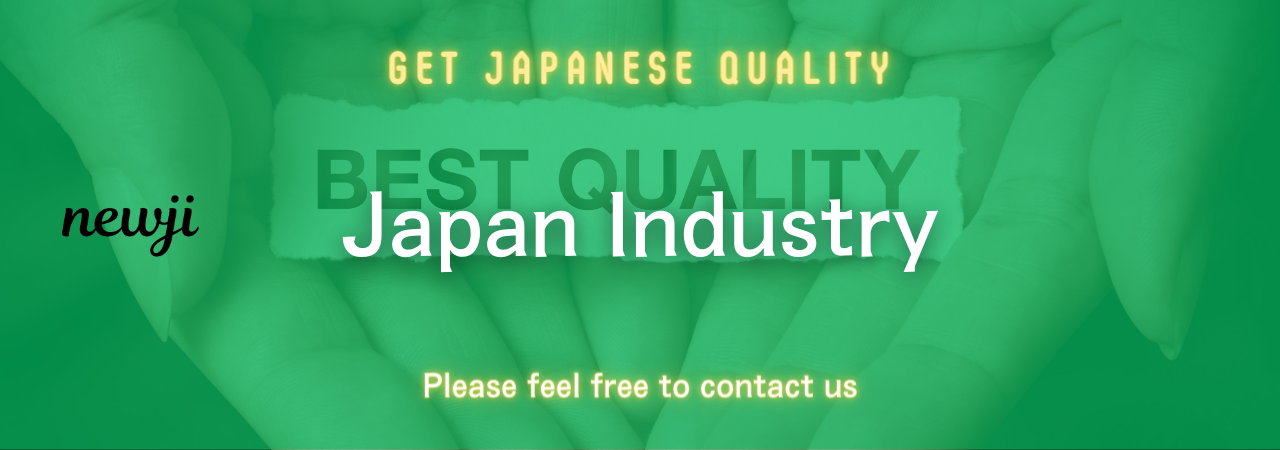
目次
Understanding Fracture Mechanics
Fracture mechanics is a vital area of study in engineering that focuses on the analysis of pre-existing flaws in materials and structures.
It assesses how these flaws can grow into cracks under stress, ultimately leading to the failure of a component.
Understanding fracture mechanics is crucial for designing components that are safe, reliable, and durable.
The primary goal of fracture mechanics is to ensure that materials can resist cracking and breaking under typical service conditions.
It plays a key role in industries like aerospace, automotive, and construction, where material failures can have serious consequences.
By understanding how and why materials fracture, engineers can create designs that prevent catastrophic failures, enhancing the safety and longevity of structures.
Key Concepts in Fracture Mechanics
To comprehend fracture mechanics, it’s essential to be familiar with several fundamental concepts, including stress intensity, crack propagation, and fracture toughness.
Stress Intensity
Stress intensity is a measure of the concentration of stress around a flaw or crack in a material.
It’s a crucial factor in determining whether a crack will grow or remain stable.
The stress intensity factor helps engineers predict the likelihood of crack growth under various loading conditions.
If the stress intensity exceeds a material’s fracture toughness, the crack is likely to propagate, leading to failure.
Crack Propagation
Crack propagation refers to the growth of a crack within a material over time.
This process can be influenced by various factors, such as the material’s properties, environmental conditions, and the type and magnitude of loads applied.
Understanding how cracks propagate is critical for predicting the life expectancy of a component and taking necessary measures to prevent failure.
Fracture Toughness
Fracture toughness is a material property that describes a material’s ability to resist crack propagation.
It’s an intrinsic quality that varies among different materials and can be affected by temperature, loading rate, and environmental conditions.
Materials with high fracture toughness can withstand higher stress intensities before breaking, making them more resilient to fracture failure.
Introduction to Damage Tolerance Design
Damage tolerance design is a systematic approach that aims to ensure structures can sustain some level of damage without catastrophic failure.
This design philosophy acknowledges that no material is perfect and that flaws and imperfections are inevitable during manufacturing and service life.
By incorporating damage tolerance, engineers can create safer and more reliable structures.
The primary objective of damage tolerance design is to prevent sudden and unexpected failures by allowing for detection and repair of damage before it becomes critical.
This approach is particularly important in the aerospace industry, where safety is paramount, and the consequences of failure are severe.
Principles of Damage Tolerance Design
Damage tolerance design relies on several principles to ensure the ongoing safety and functionality of structures.
These principles include redundancy, load path diversity, and periodic inspections.
Redundancy
Redundancy involves incorporating additional components or pathways in a design to create backups in case of failure.
By having multiple load-carrying members, a structure can continue to function even if one component fails.
This principle helps ensure that damage does not lead to an immediate catastrophic failure, providing time for detection and repair.
Load Path Diversity
Load path diversity refers to designing structures in such a way that loads can be distributed along different paths.
This diversification reduces the likelihood of single-point failures, enhancing the overall robustness of the structure.
As a result, if damage occurs in one part of the structure, it won’t compromise the entire system.
Periodic Inspections
Regular inspections are a critical aspect of damage tolerance design.
By routinely examining structures for signs of wear, corrosion, and fatigue cracks, it’s possible to detect damage early and address it before it leads to failure.
These inspections are crucial for maintaining the safety and integrity of systems over their operational life.
The Synergy Between Fracture Mechanics and Damage Tolerance Design
Fracture mechanics and damage tolerance design are closely intertwined in engineering practices.
While fracture mechanics provides the necessary tools and understanding to predict and analyze crack growth, damage tolerance design allows engineers to mitigate the risks associated with material flaws.
By integrating these disciplines, engineers can better anticipate potential issues and address them proactively.
This synergy leads to the development of safer and more durable structures across various industries.
Applications in Different Industries
Fracture mechanics and damage tolerance design have significant applications across multiple sectors.
Aerospace Industry
In the aerospace industry, these disciplines are crucial for the safety and performance of aircraft.
Engineers design airframes and engine components using damage tolerance principles, ensuring that any damage that occurs during service is detected and addressed promptly to maintain passenger safety.
Automotive Industry
In the automotive sector, fracture mechanics and damage tolerance design help create crash-resistant vehicles.
By understanding how materials behave under stress and incorporating redundancy and inspections into designs, automotive engineers can enhance vehicle durability and passenger protection.
Construction Industry
In construction, these principles ensure the safety and longevity of buildings and infrastructure.
Engineers use fracture mechanics to evaluate and predict potential weaknesses in structures, while damage tolerance design allows for regular inspections and maintenance to prevent failures over time.
Conclusion
Fracture mechanics and damage tolerance design are indispensable tools in the field of engineering.
By offering insights into crack behavior and strategies to cope with damage, they help create safer, more reliable, and longer-lasting structures.
Their applications span various industries, emphasizing the need for continued research and development to further enhance their effectiveness.
Understanding and integrating these disciplines is essential for engineers tasked with designing the critical infrastructure of tomorrow.
資料ダウンロード
QCD管理受発注クラウド「newji」は、受発注部門で必要なQCD管理全てを備えた、現場特化型兼クラウド型の今世紀最高の受発注管理システムとなります。
ユーザー登録
受発注業務の効率化だけでなく、システムを導入することで、コスト削減や製品・資材のステータス可視化のほか、属人化していた受発注情報の共有化による内部不正防止や統制にも役立ちます。
NEWJI DX
製造業に特化したデジタルトランスフォーメーション(DX)の実現を目指す請負開発型のコンサルティングサービスです。AI、iPaaS、および先端の技術を駆使して、製造プロセスの効率化、業務効率化、チームワーク強化、コスト削減、品質向上を実現します。このサービスは、製造業の課題を深く理解し、それに対する最適なデジタルソリューションを提供することで、企業が持続的な成長とイノベーションを達成できるようサポートします。
製造業ニュース解説
製造業、主に購買・調達部門にお勤めの方々に向けた情報を配信しております。
新任の方やベテランの方、管理職を対象とした幅広いコンテンツをご用意しております。
お問い合わせ
コストダウンが利益に直結する術だと理解していても、なかなか前に進めることができない状況。そんな時は、newjiのコストダウン自動化機能で大きく利益貢献しよう!
(β版非公開)