- お役立ち記事
- Fracture mechanism and fracture surface analysis of plastic molded productsFailure analysis technology and troubleshooting
月間77,185名の
製造業ご担当者様が閲覧しています*
*2025年2月28日現在のGoogle Analyticsのデータより
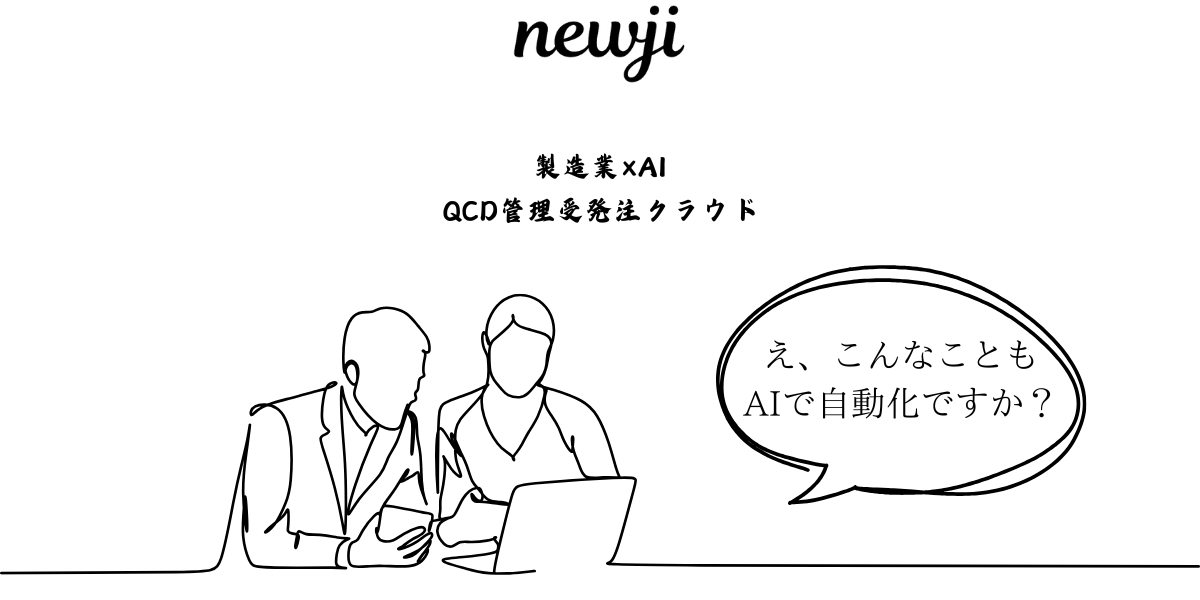
Fracture mechanism and fracture surface analysis of plastic molded productsFailure analysis technology and troubleshooting
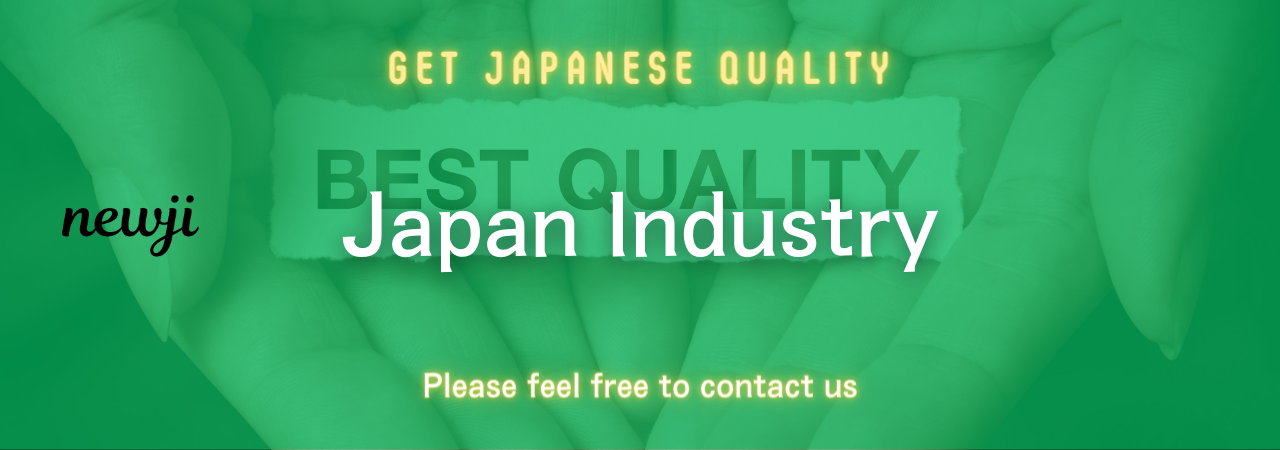
目次
Understanding Fracture Mechanisms in Plastic Molded Products
Plastic molded products are ubiquitous in various industries due to their versatility and durability.
However, like any other material, plastics can experience failure through fractures.
Understanding the fracture mechanism of plastic molded products is crucial for improving their performance and reliability.
There are several common fracture mechanisms in plastic materials, including brittle fracture, ductile fracture, and fatigue fracture.
Each mechanism depends on multiple factors such as the type of plastic, environmental conditions, and the applied stress.
Brittle fracture in plastics occurs without significant plastic deformation and is usually sudden.
It often results from defects in the material or rapid application of stress.
Polymer chains in the plastic do not align or move to absorb the stress, causing the material to snap.
Ductile fracture, on the other hand, involves significant plastic deformation before failure.
It occurs when the material experiences prolonged stress, allowing polymer chains to stretch and align over time.
Eventually, the material elongates and necks before completely breaking.
Fatigue fracture is caused by repetitive loading cycles, which weaken the material over time.
Even at stress levels below the material’s ultimate tensile strength, repeated loading can result in incremental damage accumulation.
This type of fracture is commonly seen in plastic components used in dynamic applications.
Analyzing Fracture Surfaces
Fracture surface analysis is an essential part of failure analysis as it helps identify the fracture mechanism and root cause of failure.
By examining the fracture surface, engineers can derive insights into the failure process and optimize design and manufacturing processes to enhance material performance.
The visual examination is the first step in fracture surface analysis.
Engineers look for telltale signs that signal the fracture type.
Brittle fractures typically have a shiny, smooth surface with no signs of plastic deformation.
In contrast, ductile fractures exhibit a rough, fibrous surface, indicating significant plastic flow before failure.
Scanning Electron Microscopy (SEM) is another critical tool in fracture analysis.
SEM allows for high-magnification observation of the fracture surfaces, providing detailed images of microstructural features.
By analyzing the fracture morphology, such as the presence of dimples or ridges, engineers can confirm whether the fracture was brittle or ductile.
Energy Dispersive X-ray Spectroscopy (EDS) or Fourier-transform infrared spectroscopy (FTIR) can also be used in conjunction with SEM.
These techniques identify the chemical composition of the fracture surface, which helps determine if there was any contamination or degradation of the material that contributed to the failure.
Troubleshooting and Preventing Fractures
Once the fracture mechanism and contributing factors are identified, engineers can implement preventive measures to reduce the likelihood of future failures.
Troubleshooting involves modifying design, material selection, and manufacturing processes to enhance the product’s performance.
Material selection is often the first consideration in preventing fractures.
Choosing a plastic material with the appropriate mechanical properties for the intended application is crucial.
Factors such as impact strength, toughness, and thermal stability must be evaluated to ensure suitability.
Enhancing the design can also mitigate fracture risks.
Redesigning components to eliminate stress concentration points, providing adequate support, or redistributing loads can all improve product longevity.
Design changes such as adding fillets at sharp corners or increasing wall thickness in high-stress areas can significantly impact performance.
Production process optimization is another critical factor.
Molding conditions, such as temperature, pressure, and cooling rate, play a significant role in the final material properties.
Careful control of these parameters can reduce internal stresses that may lead to fracture.
Post-production enhancements, such as annealing, can further improve fracture resistance.
Annealing involves heating the plastic material to a specific temperature, then cooling it slowly to relieve internal stresses and enhance toughness.
Conclusion: The Importance of Continuous Monitoring and Improvement
Fracture analysis and troubleshooting are ongoing processes.
Even with preventive measures, continuous monitoring of products in service is necessary to identify potential issues early.
Regular inspections, maintenance, and testing can catch signs of degradation before they result in failure.
Engaging in consistent feedback loops with field performance data helps refine designs and processes.
Ultimately, a comprehensive understanding of fracture mechanisms and effective troubleshooting strategies will ensure the reliability and longevity of plastic molded products in various applications.
Engineers and manufacturers must remain proactive in their approach to enhance material performance, reduce failures, and optimize the safety and efficacy of their products.
資料ダウンロード
QCD管理受発注クラウド「newji」は、受発注部門で必要なQCD管理全てを備えた、現場特化型兼クラウド型の今世紀最高の受発注管理システムとなります。
ユーザー登録
受発注業務の効率化だけでなく、システムを導入することで、コスト削減や製品・資材のステータス可視化のほか、属人化していた受発注情報の共有化による内部不正防止や統制にも役立ちます。
NEWJI DX
製造業に特化したデジタルトランスフォーメーション(DX)の実現を目指す請負開発型のコンサルティングサービスです。AI、iPaaS、および先端の技術を駆使して、製造プロセスの効率化、業務効率化、チームワーク強化、コスト削減、品質向上を実現します。このサービスは、製造業の課題を深く理解し、それに対する最適なデジタルソリューションを提供することで、企業が持続的な成長とイノベーションを達成できるようサポートします。
製造業ニュース解説
製造業、主に購買・調達部門にお勤めの方々に向けた情報を配信しております。
新任の方やベテランの方、管理職を対象とした幅広いコンテンツをご用意しております。
お問い合わせ
コストダウンが利益に直結する術だと理解していても、なかなか前に進めることができない状況。そんな時は、newjiのコストダウン自動化機能で大きく利益貢献しよう!
(β版非公開)