- お役立ち記事
- Fracture mechanism and fracture surface analysis of solder joints and improvement of strength reliability
月間76,176名の
製造業ご担当者様が閲覧しています*
*2025年3月31日現在のGoogle Analyticsのデータより
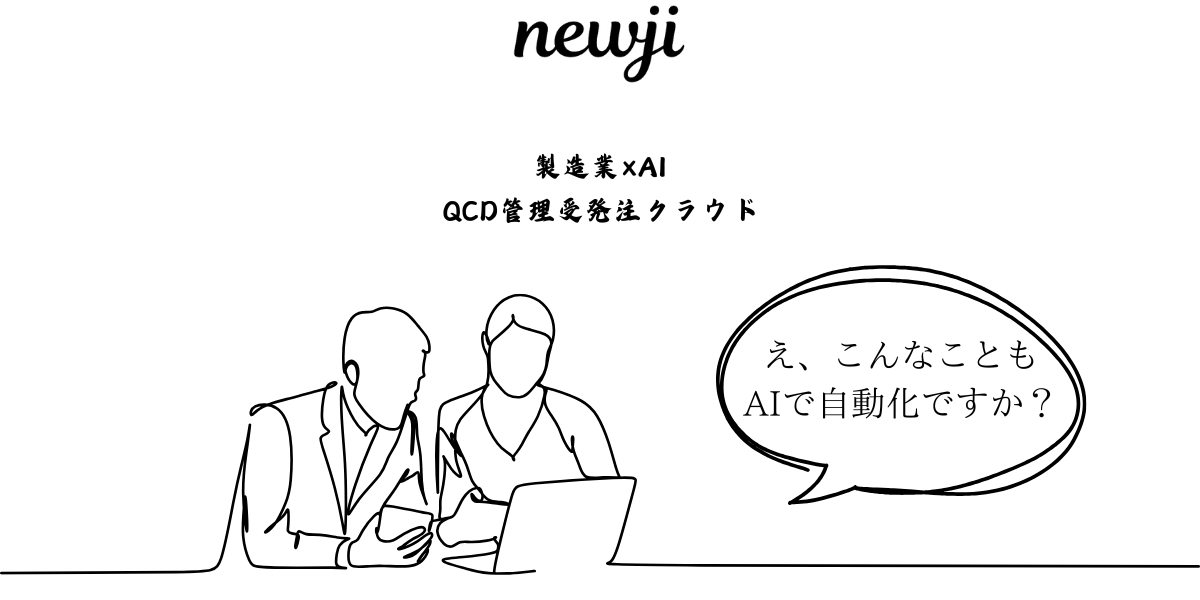
Fracture mechanism and fracture surface analysis of solder joints and improvement of strength reliability
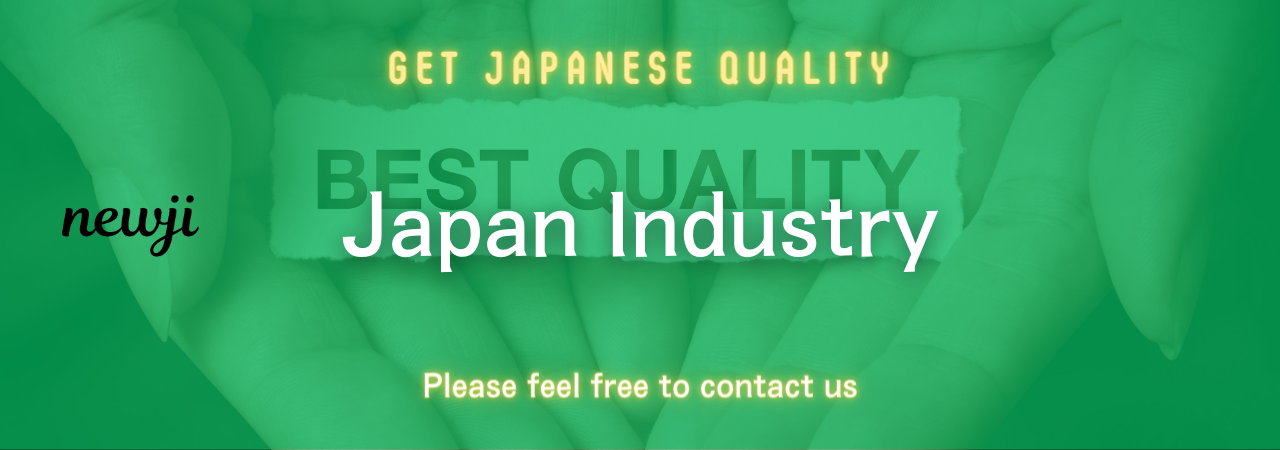
目次
Introduction to Solder Joints
Solder joints play a crucial role in the electronics industry, ensuring the electrical and mechanical connection between components and printed circuit boards (PCBs).
These tiny metal connectors are critical for the performance and longevity of electronic devices.
Understanding how solder joints work can help in improving their strength and reliability.
This article explores the fracture mechanism of solder joints, analyzes their fracture surfaces, and suggests ways to improve their strength and reliability.
Understanding Fracture Mechanism
What is a Fracture Mechanism?
A fracture mechanism refers to the process through which a material breaks or cracks under stress.
For solder joints, this involves understanding how stress and strain affect the joint, ultimately leading to failure.
It is crucial to identify the fracture mechanism to improve the design and integrity of the solder joint.
Types of Fracture Mechanisms in Solder Joints
Solder joints experience various types of fractures, primarily categorized into ductile and brittle fractures.
– **Ductile Fracture**: This type involves significant deformation before failure.
The material stretches or bends, absorbing a lot of energy.
It’s a slower process, allowing time for visual detection and corrective action.
– **Brittle Fracture**: Unlike ductile fractures, brittle fractures occur with little to no deformation.
They are quick and often produce a clean break.
Brittle fractures are more dangerous as they occur suddenly without prior warning.
– **Fatigue Fracture**: Repeated loading and unloading cycles can lead to fatigue fractures.
This mechanism is prevalent in environments where solder joints face cyclic thermal or mechanical stresses.
Factors Influencing Fracture Mechanisms
Several factors influence the fracture mechanisms in solder joints:
– **Temperature**: High operational temperatures can weaken solder joints, making them more susceptible to ductile fractures.
– **Material Composition**: The metal alloys used in the solder play a significant role in determining the fracture type.
Lead-free solders have different fracture characteristics compared to lead-based solders.
– **Mechanical Load**: The amount and type of mechanical load directly affect the fracture mechanism.
Stresses such as tensile, shear, or compressive forces can initiate fractures.
– **Structural Design**: The design and geometry of the joint can impact how stress distributes across the solder.
Fracture Surface Analysis
Importance of Analyzing Fracture Surfaces
Analyzing fracture surfaces allows engineers to understand the cause of failure in solder joints.
It involves examining the physical appearance of the fracture post-failure.
This analysis helps in diagnosing the fracture mechanism and devising prevention strategies for future failures.
Methods of Fracture Surface Analysis
Fracture surface analysis can be performed using various methods:
– **Microscopic Analysis**: Optical and electron microscopes are used to examine the fracture surfaces in detail.
These tools help identify features like crack propagation paths and failure origins.
– **Chemical Analysis**: Techniques like Energy Dispersive X-ray Spectroscopy (EDS) provide elemental composition details.
Understanding the material makeup helps in inferring fracture causes.
– **X-Ray Diffraction**: This method identifies crystalline structures within the solder, providing insights into stress patterns and potential weak points.
Identifying Features on Fracture Surfaces
Upon analyzing fracture surfaces, several features can guide the identification of fracture mechanisms:
– **Beach Marks**: These semi-circular patterns indicate slow crack growth and are typical in fatigue fractures.
– **Dimples**: Indicative of ductile fractures, dimples show a material has undergone significant plastic deformation before breaking.
– **Cleavage Facets**: These smooth, flat surfaces are characteristic of brittle fractures.
– **Intergranular Fractures**: They occur along the grain boundaries, often linked to corrosion or thermal fatigue.
Improving Strength and Reliability of Solder Joints
Material Selection
Choosing the right solder materials significantly impacts joint reliability.
Opt for materials that offer a balance of strength, ductility, and corrosion resistance.
Consider using lead-free alternatives for environmental safety.
Optimizing Design
Design optimization involves considering the joint’s geometrical configuration.
Ensure even distribution of stress by avoiding sharp corners and incorporating fillets where possible.
Conduct thermal and mechanical simulations during the design phase to predict performance under different conditions.
Process Control
Maintaining a controlled soldering process is vital in preventing defects.
Ensure appropriate soldering temperatures and times to prevent overheating.
Implement thorough inspection protocols post-soldering to detect and rectify early-stage fractures.
Testing and Quality Assurance
Regular testing can help maintain high-quality solder joints.
Utilize thermal cycling and vibration testing for comprehensive assessment.
Implement a robust feedback loop where test results inform future design and process improvements.
Conclusion
Understanding fracture mechanisms and analyzing fracture surfaces are crucial steps in enhancing the strength and reliability of solder joints.
By selecting appropriate materials, optimizing joint designs, and ensuring rigorous process controls, the integrity of solder joints can be significantly improved.
Continuous testing and quality assurance will help in sustaining performance and mitigating failures.
These practices ensure that electrical components remain reliable and robust throughout their operational lifecycle, which is essential for the advancement of modern electronics.
資料ダウンロード
QCD管理受発注クラウド「newji」は、受発注部門で必要なQCD管理全てを備えた、現場特化型兼クラウド型の今世紀最高の受発注管理システムとなります。
ユーザー登録
受発注業務の効率化だけでなく、システムを導入することで、コスト削減や製品・資材のステータス可視化のほか、属人化していた受発注情報の共有化による内部不正防止や統制にも役立ちます。
NEWJI DX
製造業に特化したデジタルトランスフォーメーション(DX)の実現を目指す請負開発型のコンサルティングサービスです。AI、iPaaS、および先端の技術を駆使して、製造プロセスの効率化、業務効率化、チームワーク強化、コスト削減、品質向上を実現します。このサービスは、製造業の課題を深く理解し、それに対する最適なデジタルソリューションを提供することで、企業が持続的な成長とイノベーションを達成できるようサポートします。
製造業ニュース解説
製造業、主に購買・調達部門にお勤めの方々に向けた情報を配信しております。
新任の方やベテランの方、管理職を対象とした幅広いコンテンツをご用意しております。
お問い合わせ
コストダウンが利益に直結する術だと理解していても、なかなか前に進めることができない状況。そんな時は、newjiのコストダウン自動化機能で大きく利益貢献しよう!
(β版非公開)