- お役立ち記事
- Fracture surface analysis and life prediction for plastic products and measures to prevent damage and defects
月間77,185名の
製造業ご担当者様が閲覧しています*
*2025年2月28日現在のGoogle Analyticsのデータより
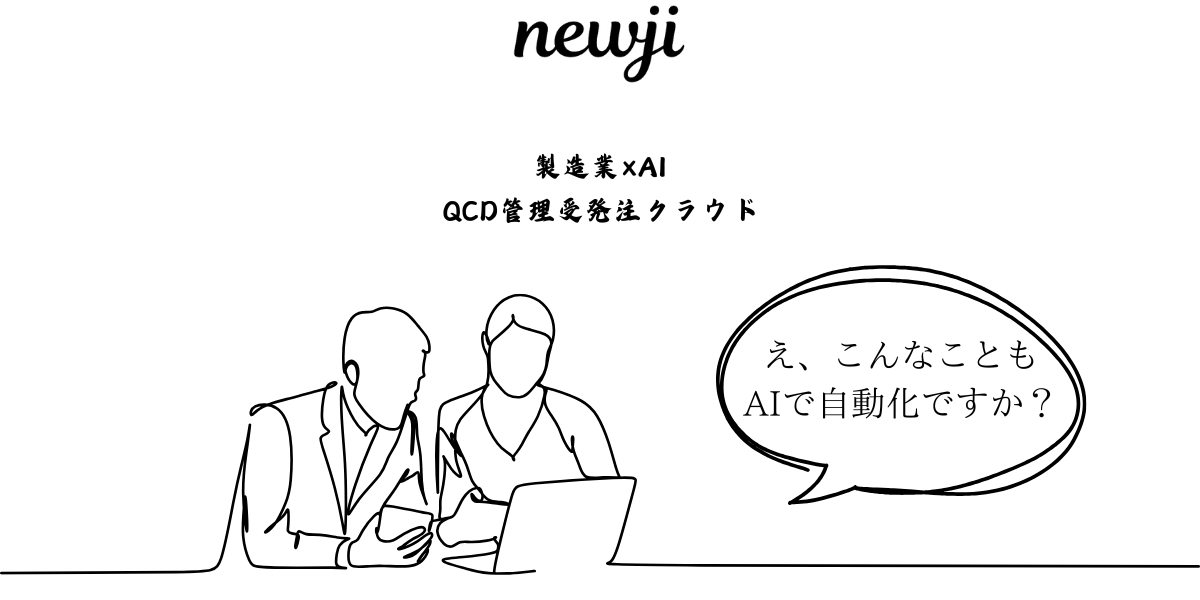
Fracture surface analysis and life prediction for plastic products and measures to prevent damage and defects
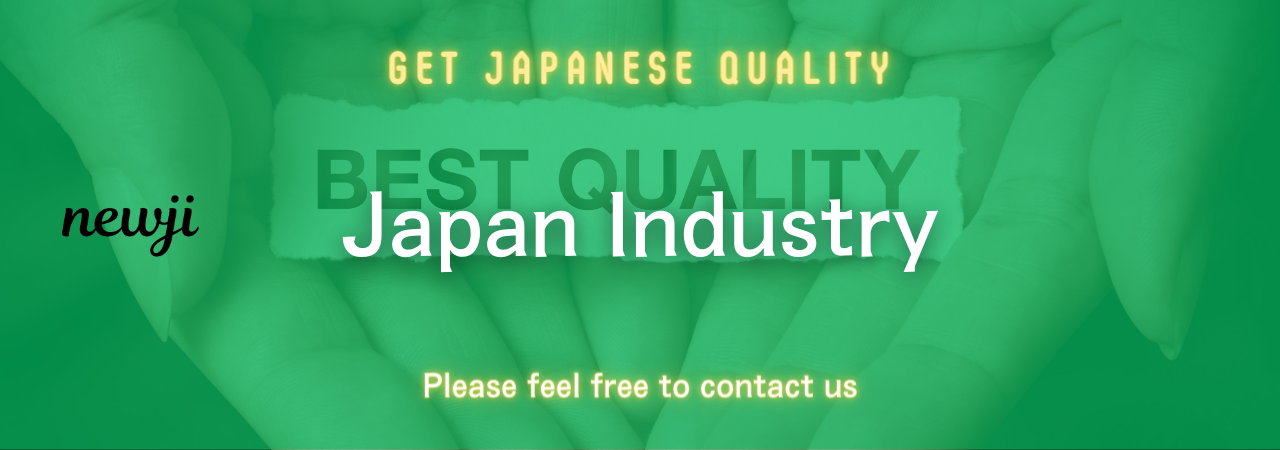
目次
Understanding Fracture Surface Analysis
Fracture surface analysis is a crucial technique used to understand the failure mechanisms in plastic products.
When a plastic component breaks, examining the fracture surface can provide insights into the cause of the failure.
By studying the fracture patterns, one can determine whether the failure was sudden or progressive, enabling targeted improvements in design, material selection, and manufacturing processes.
The Basics of Fracture Surface Analysis
Fracture surface analysis involves examining the broken surfaces of plastic products using microscopes and other analytical tools.
These surfaces often contain telltale marks, such as ridges and dimples, which can indicate specific modes of failure.
For instance, a rough fracture surface with irregular patterns may suggest a brittle failure.
In contrast, a smooth and shiny surface could point toward ductile failure.
Additionally, understanding the environmental conditions during failure is critical.
Factors such as temperature, humidity, and chemical exposure can significantly affect the way plastics fracture.
By correlating fracture patterns with these conditions, engineers can better predict and prevent future failures.
Microscopic Techniques in Fracture Analysis
Microscopy techniques are essential in providing a detailed view of the fracture surfaces.
Scanning Electron Microscopy (SEM) is often used due to its high resolution and ability to reveal minute details of the cracked surface.
SEM can magnify fracture surfaces by thousands of times, providing insights into microfeatures that could indicate stress concentrations or manufacturing defects.
Other methods, like Optical Microscopy and Atomic Force Microscopy (AFM), also play vital roles.
While optical microscopy offers a quick overview of the fracture surface, AFM can provide three-dimensional imaging, helping to analyze surface roughness and topography.
Life Prediction for Plastic Products
Predicting the life of plastic products involves understanding both the mechanical properties of the materials and the environmental conditions they will face.
By using fracture surface analysis, engineers can gain valuable information necessary for improving life prediction models.
Factors Influencing the Longevity of Plastics
Several factors influence the longevity of plastic products.
Material composition is one such factor.
Different polymers, fillers, and additives have varying resistances to environmental and mechanical stresses.
Therefore, selecting the right material is critical for ensuring product durability.
The manufacturing process can also affect the product’s lifespan.
Processes like injection molding or extrusion can introduce defects such as voids or orientation stress, impacting long-term performance.
By analyzing fracture surfaces, manufacturers can identify and minimize these defects.
Finally, the service environment plays a significant role.
Exposure to UV light, chemicals, high temperatures, or mechanical stress can degrade plastic over time.
Understanding how these factors interact with the material helps in predicting when a product may fail.
Modeling for Life Prediction
Life prediction models integrate fracture surface analysis data with statistical and computational methods to estimate the service life of plastic products.
Models such as the Paris Law can predict crack growth rates under cyclic loads, providing important information for fatigue life estimation.
Similarly, accelerated life testing, combined with fracture analysis, can simulate real-world conditions to forecast product longevity.
These models allow manufacturers to anticipate failure modes and service life, leading to better product designs and increased reliability.
Preventive Measures for Damage and Defects
Preventing damage and defects in plastic products is a multi-faceted approach involving material selection, design optimization, and quality control during manufacturing.
Choosing the Right Materials
Material selection is fundamental to preventing damage in plastic products.
Engineers should choose materials with the appropriate mechanical and thermal properties for their specific applications.
For example, using UV-stabilized plastics can prolong product life in outdoor applications.
Moreover, understanding the chemical interactions between the plastic and its environment can mitigate risks of degradation.
Employing materials resistant to corrosion or chemical attack is essential in certain industrial applications.
Optimizing Product Design
Designing plastic products with failure prevention in mind is another key strategy.
Incorporating features such as radii instead of sharp corners can reduce stress concentrations and potential crack initiation sites.
Additionally, conducting Finite Element Analysis (FEA) during the design phase can help predict how the product will behave under various loads.
By simulating real-world conditions, engineers can identify potential weak spots and make necessary design adjustments.
Implementing Quality Control Measures
Applying rigorous quality control measures during manufacturing ensures that potential defects are identified and rectified early.
Techniques like Non-Destructive Testing (NDT) can detect subsurface defects that are not visible to the naked eye.
Regular monitoring and maintenance of manufacturing equipment can also prevent issues like wear and tear, which can introduce defects into the products.
Conclusion
Fracture surface analysis and life prediction are invaluable tools for understanding and mitigating failures in plastic products.
By studying fracture surfaces, predicting product lifespans, and implementing preventive measures, manufacturers can enhance the reliability and durability of their products.
This proactive approach not only extends product life but also reduces costs associated with failures and recalls, ultimately leading to improved consumer satisfaction.
資料ダウンロード
QCD管理受発注クラウド「newji」は、受発注部門で必要なQCD管理全てを備えた、現場特化型兼クラウド型の今世紀最高の受発注管理システムとなります。
ユーザー登録
受発注業務の効率化だけでなく、システムを導入することで、コスト削減や製品・資材のステータス可視化のほか、属人化していた受発注情報の共有化による内部不正防止や統制にも役立ちます。
NEWJI DX
製造業に特化したデジタルトランスフォーメーション(DX)の実現を目指す請負開発型のコンサルティングサービスです。AI、iPaaS、および先端の技術を駆使して、製造プロセスの効率化、業務効率化、チームワーク強化、コスト削減、品質向上を実現します。このサービスは、製造業の課題を深く理解し、それに対する最適なデジタルソリューションを提供することで、企業が持続的な成長とイノベーションを達成できるようサポートします。
製造業ニュース解説
製造業、主に購買・調達部門にお勤めの方々に向けた情報を配信しております。
新任の方やベテランの方、管理職を対象とした幅広いコンテンツをご用意しております。
お問い合わせ
コストダウンが利益に直結する術だと理解していても、なかなか前に進めることができない状況。そんな時は、newjiのコストダウン自動化機能で大きく利益貢献しよう!
(β版非公開)