- お役立ち記事
- Fracture surface analysis and life prediction of plastic materials and measures to prevent recurrence of breakage defects
月間76,176名の
製造業ご担当者様が閲覧しています*
*2025年3月31日現在のGoogle Analyticsのデータより
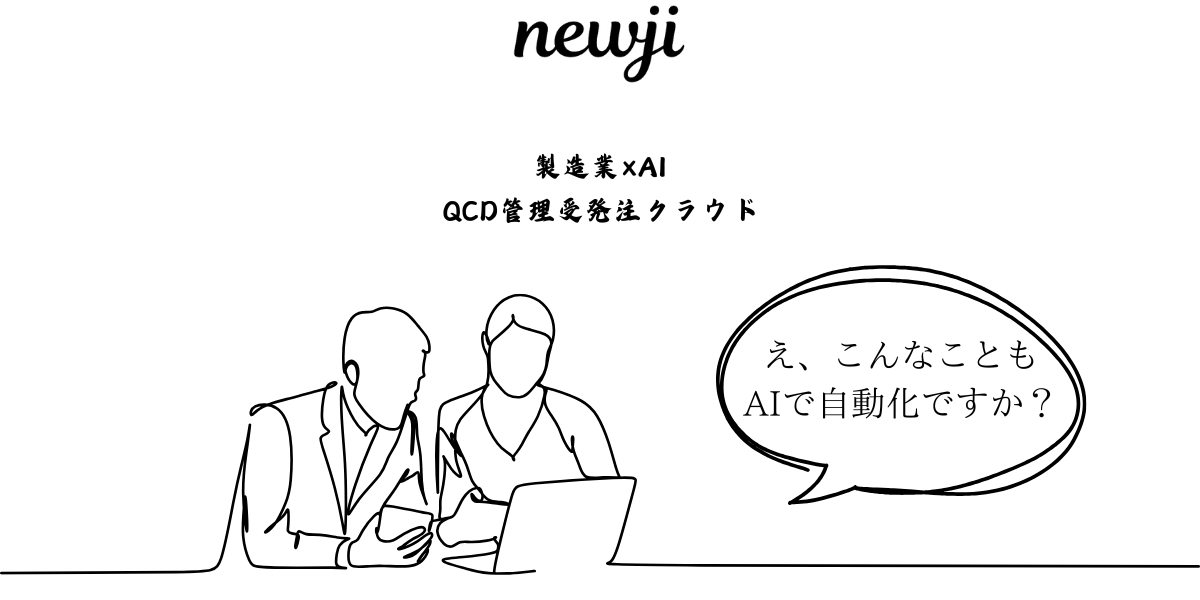
Fracture surface analysis and life prediction of plastic materials and measures to prevent recurrence of breakage defects
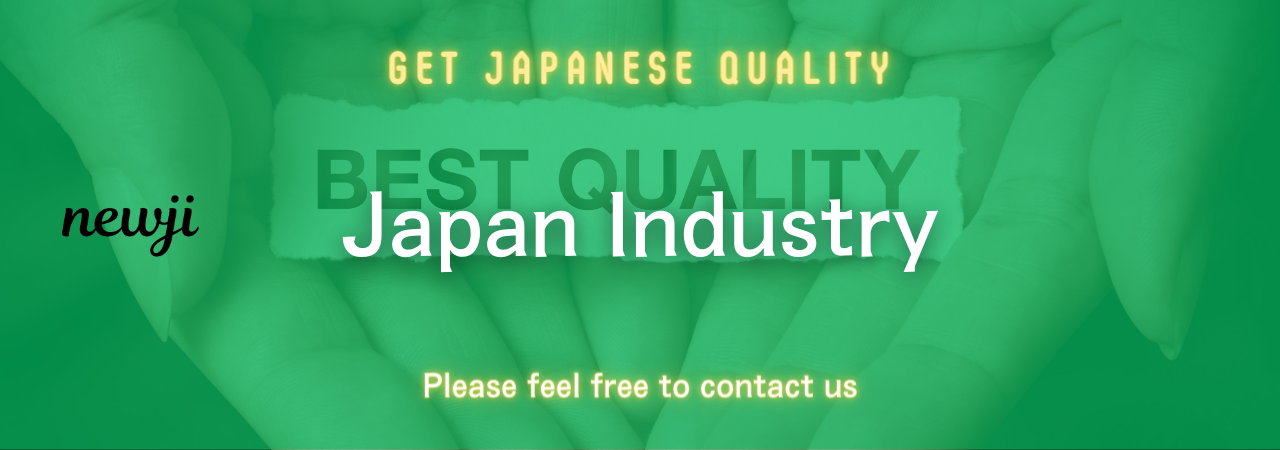
目次
Understanding Fracture Surface Analysis
Fracture surface analysis is a crucial tool in the study of the failure of plastic materials.
It involves examining the characteristics of a fractured surface to determine the reasons behind a material’s failure.
By understanding how a material breaks, researchers and engineers can identify the specific conditions that led to the fracture and take steps to prevent similar issues in the future.
The process typically includes visual examination, scanning electron microscopy, and other advanced analytical techniques.
These methods allow experts to zoom in on the microscopic features of a fracture and gather data about the material’s behavior under stress.
From this analysis, patterns such as crack propagation, stress concentration, and type of fracture (brittle or ductile) can be observed.
Each fracture surface tells a story about the inherent properties of the material and the external forces that led to its failure.
The insights gained can help refine material selection and enhance design strategies in manufacturing, ultimately leading to more durable and reliable plastic products.
Factors Contributing to Fracture in Plastics
Several factors can cause plastic materials to fracture.
Understanding these factors is essential for effective life prediction and prevention of breakage defects.
1. Material Composition
The composition of plastic materials greatly affects their mechanical properties.
For instance, additives and fillers can enhance flexibility or rigidity but might also introduce weaknesses under certain conditions.
Poorly distributed fillers or improper curing can result in uneven strength distribution, leading to fracture.
2. Environmental Conditions
Exposure to environmental elements like UV light, temperature fluctuations, and chemicals can degrade plastics.
UV radiation, in particular, can cause photo-oxidative damage, making plastics brittle.
Extreme temperatures can also alter the molecular structure, leading to both thermal expansion and contraction stress within the material.
3. Mechanical Stress
Repeated mechanical stress or overloading can cause fatigue in plastic materials.
Fatigue refers to the progressive and localized structural damage that occurs when a material is subjected to cyclic loading.
Over time, even minor stresses can accumulate, forming microcracks that eventually lead to fractures.
4. Manufacturing Defects
Defects arising from the manufacturing process, like air bubbles or weld lines, are another cause of fractures.
These defects serve as stress concentrators, weakening the material at those points.
Quality control in manufacturing practices is critical to reducing such defects.
Life Prediction of Plastic Materials
Predicting the life span of plastic materials is a complex process involving several methodologies.
The goal is to estimate how long a material can perform its function before it fails, allowing manufacturers to make informed decisions regarding replacement and maintenance schedules.
Creep Analysis
Creep analysis evaluates how the material will deform over an extended period under constant stress.
By conducting tests at various stress levels and temperatures, engineers can model the long-term behavior of the material, providing a basis for predicting its useful lifetime.
Fatigue Testing
Fatigue testing is used to determine the endurance limit and the number of cycles a material can withstand before failure.
This involves subjecting a sample to cyclic loading to simulate real-world conditions.
Fatigue data helps in understanding the threshold of material performance under repetitive stress.
Accelerated Aging Tests
Accelerated aging tests expose materials to environmental conditions that simulate long-term exposure in a condensed timeframe.
By subjecting plastics to heat, UV light, and moisture in controlled settings, engineers can predict how they will behave over the years.
The results from these tests are crucial for assessing the durability and expected lifespan of plastic components.
Preventing Recurrence of Breakage Defects
Preventing recurrence of breakage defects in plastic materials requires a multi-pronged approach that addresses both design and processing aspects.
1. Material Selection
Choosing the right material is the first step in preventing defects.
Engineers must consider the application’s specific requirements, including environmental factors and load conditions.
Selecting materials with higher resistance to UV degradation, better mechanical properties, or enhanced chemical resistance can substantially reduce the risk of fractures.
2. Design Improvements
Optimized design can significantly mitigate stress concentrations and prevent fractures.
Design enhancements might include adding radii to corners, reducing sharp edges, and evenly distributing material thickness.
Using simulation tools can help identify potential weak points and allow for design adjustments before production.
3. Quality Control in Manufacturing
Implementing rigorous quality control measures throughout the manufacturing process is vital.
This includes regular inspections and tests to identify and correct defects such as voids, weld lines, or improper curing.
Automation and real-time monitoring technologies can aid in maintaining consistent production quality.
4. Regular Maintenance and Monitoring
Maintaining and monitoring equipment used in the production and end-use environments can prevent defects.
Regular checks and preventive maintenance can identify any emerging issues, reducing the risk of sudden failures.
In conclusion, analyzing fracture surfaces provides vital insights into the failure mechanisms of plastic materials.
By understanding the causes and conditions leading to fractures, engineers can accurately predict material life spans and implement measures to prevent defects.
Through careful material selection, design optimization, rigorous quality control, and ongoing maintenance, the recurrence of breakage can be minimized, ensuring safer and longer-lasting plastic products.
資料ダウンロード
QCD管理受発注クラウド「newji」は、受発注部門で必要なQCD管理全てを備えた、現場特化型兼クラウド型の今世紀最高の受発注管理システムとなります。
ユーザー登録
受発注業務の効率化だけでなく、システムを導入することで、コスト削減や製品・資材のステータス可視化のほか、属人化していた受発注情報の共有化による内部不正防止や統制にも役立ちます。
NEWJI DX
製造業に特化したデジタルトランスフォーメーション(DX)の実現を目指す請負開発型のコンサルティングサービスです。AI、iPaaS、および先端の技術を駆使して、製造プロセスの効率化、業務効率化、チームワーク強化、コスト削減、品質向上を実現します。このサービスは、製造業の課題を深く理解し、それに対する最適なデジタルソリューションを提供することで、企業が持続的な成長とイノベーションを達成できるようサポートします。
製造業ニュース解説
製造業、主に購買・調達部門にお勤めの方々に向けた情報を配信しております。
新任の方やベテランの方、管理職を対象とした幅広いコンテンツをご用意しております。
お問い合わせ
コストダウンが利益に直結する術だと理解していても、なかなか前に進めることができない状況。そんな時は、newjiのコストダウン自動化機能で大きく利益貢献しよう!
(β版非公開)