- お役立ち記事
- Fracture surface analysis, life prediction, accelerated deterioration testing and prevention of breakage problems in plastics
月間76,176名の
製造業ご担当者様が閲覧しています*
*2025年3月31日現在のGoogle Analyticsのデータより
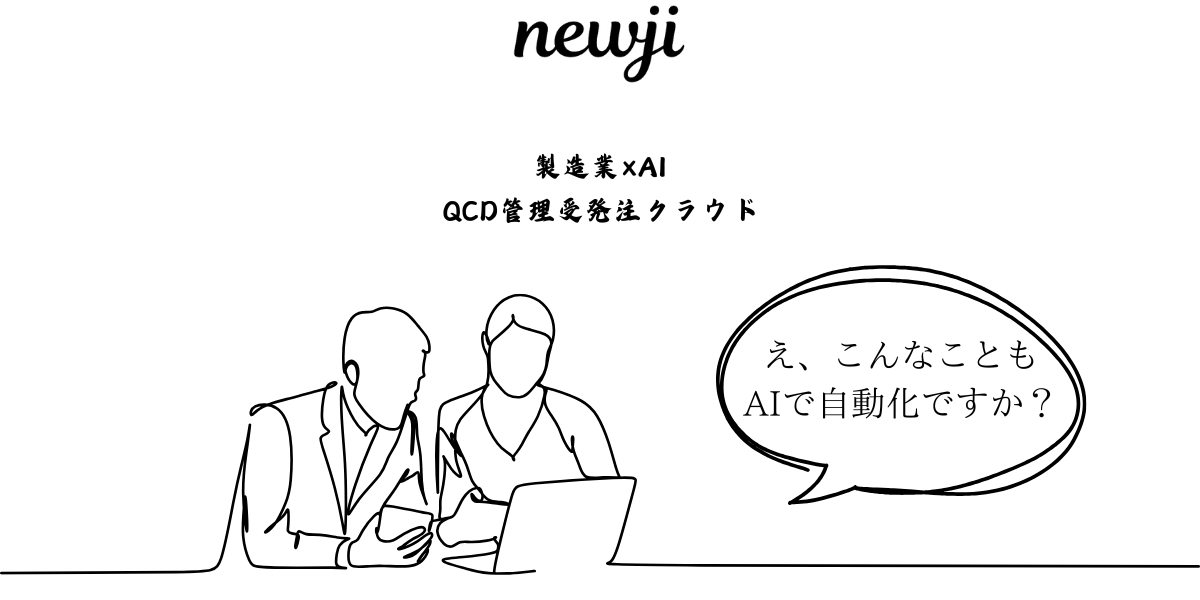
Fracture surface analysis, life prediction, accelerated deterioration testing and prevention of breakage problems in plastics
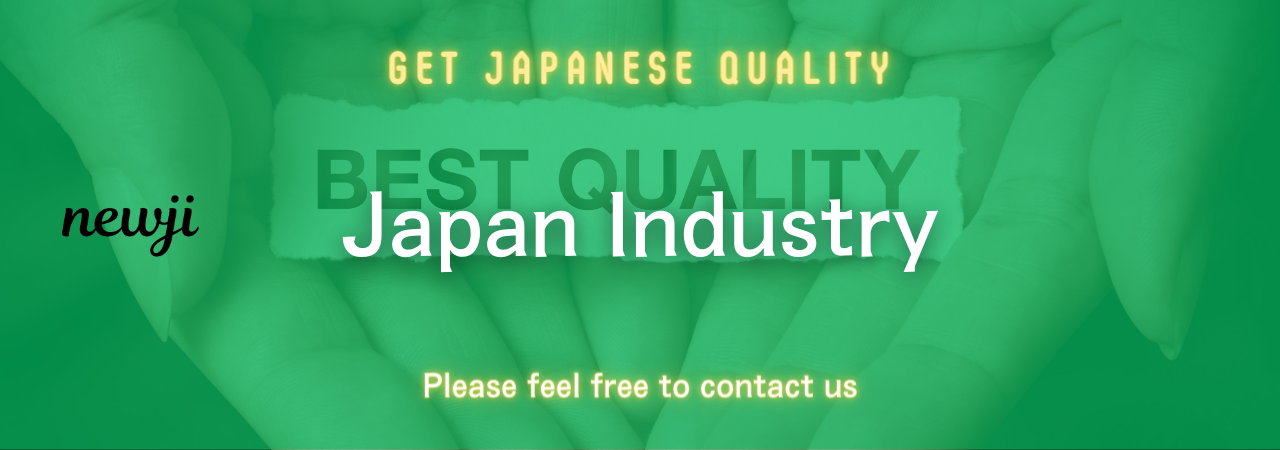
目次
Understanding Fracture Surface Analysis in Plastics
Fracture surface analysis is a critical process used to understand the causes and characteristics of a material’s failure.
When dealing with plastics, this analysis becomes especially important due to their wide range of applications and environmental interactions.
By examining the fracture surfaces, experts can determine whether material failures were caused by inherent weaknesses, external forces, or environmental factors.
In plastics, fractures can appear in various forms, such as brittle, ductile, or mixed-mode fractures.
Each type of fracture provides unique insights into the behavior and properties of the polymer material.
Through microscopic examination and other advanced techniques, analysts learn vital information about how, and why, a failure occurred.
Life Prediction of Plastics
Life prediction is a crucial aspect of ensuring the reliability and safety of plastic products.
Understanding the expected service life of a plastic material involves analyzing its behavior under different conditions over time.
This process typically involves a combination of mathematical modeling, material testing, and historical data analysis.
Several factors influence the lifespan of plastics, including exposure to UV light, thermal cycling, mechanical stress, and chemical interactions.
Each element can degrade the polymer chains, leading to reduced strength and eventual failure.
Predictive models incorporate these factors to estimate the material’s enduring capacity, guiding manufacturers to choose the right materials and design for specific applications.
Advanced Testing Techniques
A variety of testing techniques are employed to better understand the durability and longevity of plastics.
These include mechanical testing, chemical resistance assessments, and environmental simulations.
Mechanical tests like tensile strength and impact resistance provide fundamental insights into the material’s performance under expected loads and conditions.
Chemical resistance tests expose plastics to different solvents and chemicals to observe any changes in properties.
Environmental simulations replicate long-term exposure to UV radiation, moisture, and temperature fluctuations, helping to approximate real-world conditions.
Together, these tests form a comprehensive picture that supports life prediction models.
Accelerated Deterioration Testing
Accelerated deterioration testing is a method used to expedite the aging process of plastics in a controlled environment.
This approach helps manufacturers and researchers simulate years of wear and tear in a shorter time frame.
By understanding how plastics will behave under accelerated conditions, companies can quickly identify potential weaknesses and improve material formulations.
Common techniques include exposing plastics to intensified UV light, applying cyclic loading, and using elevated temperatures.
Test data allows for the precise recreation of the environmental factors that affect plastic products, revealing not only when but how materials will fail.
Benefits and Challenges
Accelerated testing offers substantial benefits, such as fast-tracked product development and cost savings.
However, it poses challenges as well, primarily ensuring that the accelerated conditions equitably represent real-world scenarios.
Accurate models must correctly scale the effects observed in accelerated tests to predict the material’s behavior in actual applications.
Collaborations between technical teams, experienced material scientists, and industry partners help to ensure the testing aligns with real usage patterns.
The quality of the accelerated deterioration testing directly influences the reliability of life predictions and informs strategic decisions in design and materials engineering.
Preventing Breakage Problems in Plastics
Preventing breakage in plastic components requires a proactive approach combining solid design practices, material selection, and regular quality checks.
Understanding the failure mechanisms is essential in creating materials that meet both user expectations and safety standards.
Manufacturers should focus on identifying and obstacles and enhancing their designs to reduce failure risks.
Material Selection and Design Considerations
Selecting the right material is fundamental to preventing failures.
Engineers must consider the intended environment, loads, and potential stressors when choosing a plastic resin.
The selection process involves evaluating material datasheets and leveraging empirical data to ensure the choice aligns with the application’s demands.
Design considerations should focus on minimizing stress concentrations, aligning fibers, and reducing thickness variations.
Effective packaging strategies can also mitigate impact forces during transport and handling.
Additional simulations using computer-aided design (CAD) tools help designers optimize geometries capable of absorbing stress effectively.
Regular Quality Checks and Maintenance
Continuous quality control processes are essential in maintaining standards and preventing unexpected failures.
Incorporating non-destructive testing (NDT) techniques in production, such as ultrasonic scanning or thermal imaging, helps detect defects before they become problems.
Regular maintenance protocols, especially in applications like piping or mechanical gears, ensure issues can be addressed before causing significant damage.
In conclusion, integrating fracture surface analysis, life prediction, and accelerated deterioration testing bolsters the entire lifecycle management of plastic products.
By prioritizing these elements, manufacturers can produce plastics that ensure safety, reliability, and performance, meeting the ever-evolving demands of consumers and industries alike.
資料ダウンロード
QCD管理受発注クラウド「newji」は、受発注部門で必要なQCD管理全てを備えた、現場特化型兼クラウド型の今世紀最高の受発注管理システムとなります。
ユーザー登録
受発注業務の効率化だけでなく、システムを導入することで、コスト削減や製品・資材のステータス可視化のほか、属人化していた受発注情報の共有化による内部不正防止や統制にも役立ちます。
NEWJI DX
製造業に特化したデジタルトランスフォーメーション(DX)の実現を目指す請負開発型のコンサルティングサービスです。AI、iPaaS、および先端の技術を駆使して、製造プロセスの効率化、業務効率化、チームワーク強化、コスト削減、品質向上を実現します。このサービスは、製造業の課題を深く理解し、それに対する最適なデジタルソリューションを提供することで、企業が持続的な成長とイノベーションを達成できるようサポートします。
製造業ニュース解説
製造業、主に購買・調達部門にお勤めの方々に向けた情報を配信しております。
新任の方やベテランの方、管理職を対象とした幅広いコンテンツをご用意しております。
お問い合わせ
コストダウンが利益に直結する術だと理解していても、なかなか前に進めることができない状況。そんな時は、newjiのコストダウン自動化機能で大きく利益貢献しよう!
(β版非公開)