- お役立ち記事
- Frisbee Manufacturing Process and Flight Stability Improvement
月間76,176名の
製造業ご担当者様が閲覧しています*
*2025年3月31日現在のGoogle Analyticsのデータより
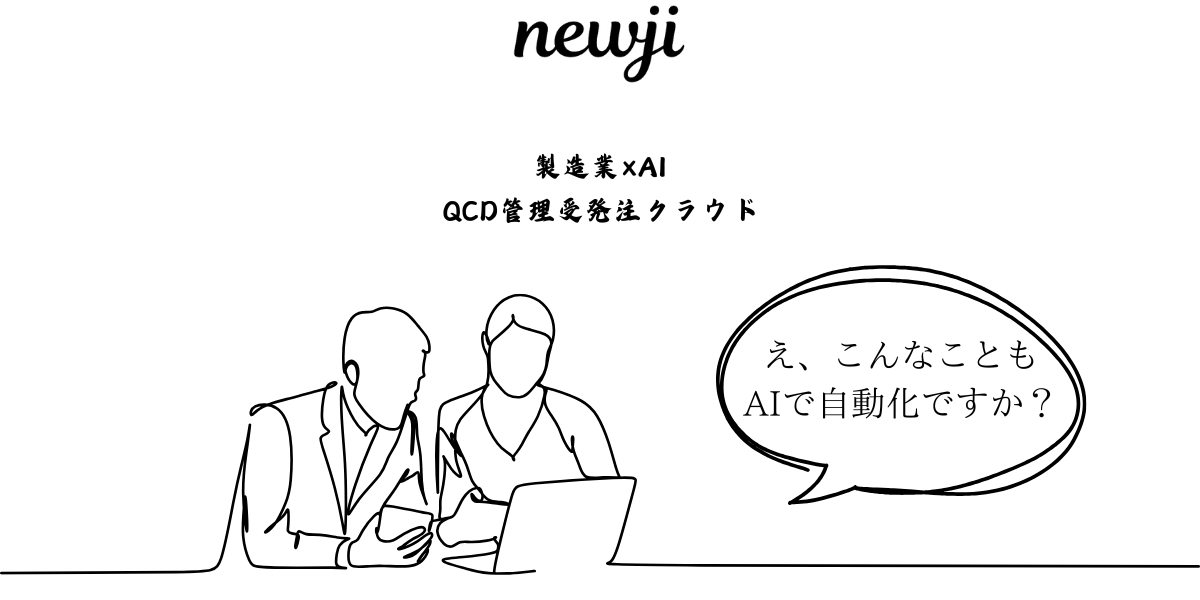
Frisbee Manufacturing Process and Flight Stability Improvement
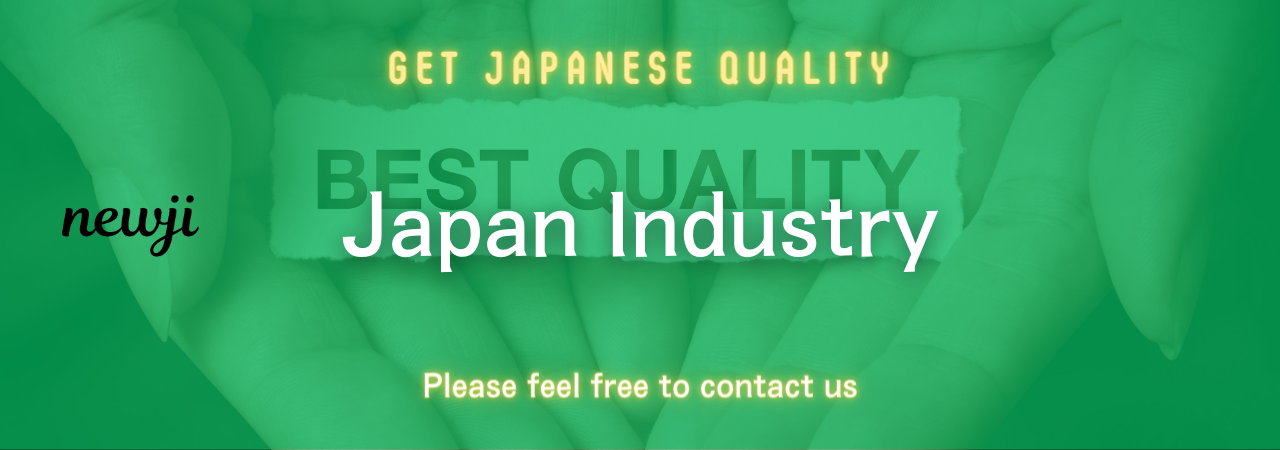
目次
Introduction to Frisbees
Frisbees have long been a popular form of outdoor entertainment for people of all ages.
Their simple design and ease of use make them a favorite in parks, beaches, and backyards.
Despite their simplicity, the manufacturing process of frisbees and their flight stability involves intricate engineering.
In this article, we delve into how frisbees are made and what makes their flight stable.
The Manufacturing Process of Frisbees
Material Selection
The process begins with the selection of materials.
Frisbees are typically made from a plastic known as polyethylene.
This material is chosen because of its balance between flexibility and durability, which is essential for absorbing impact during play without breaking.
Polyethylene also has the advantage of being lightweight, allowing frisbees to fly smoothly through the air.
Molding the Frisbee
Once the material is selected, it undergoes injection molding.
This process involves melting the plastic and injecting it into a mold that forms the frisbee’s shape.
The mold is usually composed of two parts: the top and the bottom.
After the molten plastic is injected, the mold is cooled to let the frisbee solidify.
The cooling process is crucial as it impacts the frisbee’s final structure, ensuring it is not prone to warping.
Trimming and Smoothing
After the frisbee is removed from the mold, it goes through a trimming process.
This step involves removing any excess plastic known as ‘flash’ that may have seeped out during molding.
Careful trimming is essential to maintain the aerodynamics of the frisbee.
Once trimmed, the edges are smoothed to ensure a comfortable grip and reduce air resistance during flight.
Adding Design and Color
The aesthetic appeal of frisbees plays a vital role in their marketability.
Color is added to the polyethylene during the molding process, allowing for vibrant and long-lasting hues.
Designs such as logos or patterns are often applied using screen printing techniques.
This not only customizes the frisbee but can also help identify a specific brand or purpose.
Improving Flight Stability
Aerodynamic Design
The primary factor that influences frisbee flight is its aerodynamic design.
Frisbees are shaped like a disc with a rounded edge, allowing them to cut through the air smoothly.
This design creates lift, similar to an airplane wing, contributing to stability and distance.
The center of the frisbee is slightly elevated to reduce drag and provide a lifting surface for the air to move over.
Spin Mechanics
Spin is crucial for frisbee flight.
When you throw a frisbee, spinning it helps stabilize its flight path.
The spin prevents the frisbee from tumbling through the air by distributing centrifugal force evenly across the disc.
This stability allows for longer flights and better accuracy.
Weight Distribution
The weight distribution in a frisbee is another critical factor.
Manufacturers strive to balance the weight evenly over the entire disc.
Some features like a thicker rim help maintain inertia, providing more control to the user.
This balance ensures that the frisbee doesn’t wobble during flight, allowing for precision throwing and catching.
Testing and Quality Control
Before hitting the market, frisbees undergo rigorous testing.
Manufacturers test different prototypes to assess their flight capabilities.
They use wind tunnels and real-world experiments to observe how changes in design and materials affect performance.
These tests help improve accuracy, stability, and distance, ensuring that only the best product reaches consumers.
Innovations in Frisbee Technology
Innovations continue to emerge in the frisbee market.
Technological advancements have led to new designs that enhance flight performance.
Some of the latest innovations focus on materials that provide better grip even when wet, allowing players to enjoy the game in various conditions.
Others experiment with designs that can accommodate different throwing techniques and tricks.
Furthermore, eco-friendly materials are gaining popularity.
Manufacturers are exploring biodegradable and recycled plastics to lessen the environmental impact, making the play not only fun but sustainable.
Conclusion
The process of manufacturing frisbees and improving their flight stability is a blend of science, engineering, and creativity.
From selecting durable materials, detailed design molds to quality control testing, each step plays a pivotal role in the final product.
Understanding these elements gives us a greater appreciation of this simple yet elegant flying disc.
As technology continues to advance, it will be fascinating to see how frisbee manufacturers bring new innovations to our beloved summer pastime.
資料ダウンロード
QCD管理受発注クラウド「newji」は、受発注部門で必要なQCD管理全てを備えた、現場特化型兼クラウド型の今世紀最高の受発注管理システムとなります。
ユーザー登録
受発注業務の効率化だけでなく、システムを導入することで、コスト削減や製品・資材のステータス可視化のほか、属人化していた受発注情報の共有化による内部不正防止や統制にも役立ちます。
NEWJI DX
製造業に特化したデジタルトランスフォーメーション(DX)の実現を目指す請負開発型のコンサルティングサービスです。AI、iPaaS、および先端の技術を駆使して、製造プロセスの効率化、業務効率化、チームワーク強化、コスト削減、品質向上を実現します。このサービスは、製造業の課題を深く理解し、それに対する最適なデジタルソリューションを提供することで、企業が持続的な成長とイノベーションを達成できるようサポートします。
製造業ニュース解説
製造業、主に購買・調達部門にお勤めの方々に向けた情報を配信しております。
新任の方やベテランの方、管理職を対象とした幅広いコンテンツをご用意しております。
お問い合わせ
コストダウンが利益に直結する術だと理解していても、なかなか前に進めることができない状況。そんな時は、newjiのコストダウン自動化機能で大きく利益貢献しよう!
(β版非公開)