- お役立ち記事
- [From molding to painting] The strength of a small factory that enables one-stop small-lot prototyping
月間76,176名の
製造業ご担当者様が閲覧しています*
*2025年3月31日現在のGoogle Analyticsのデータより
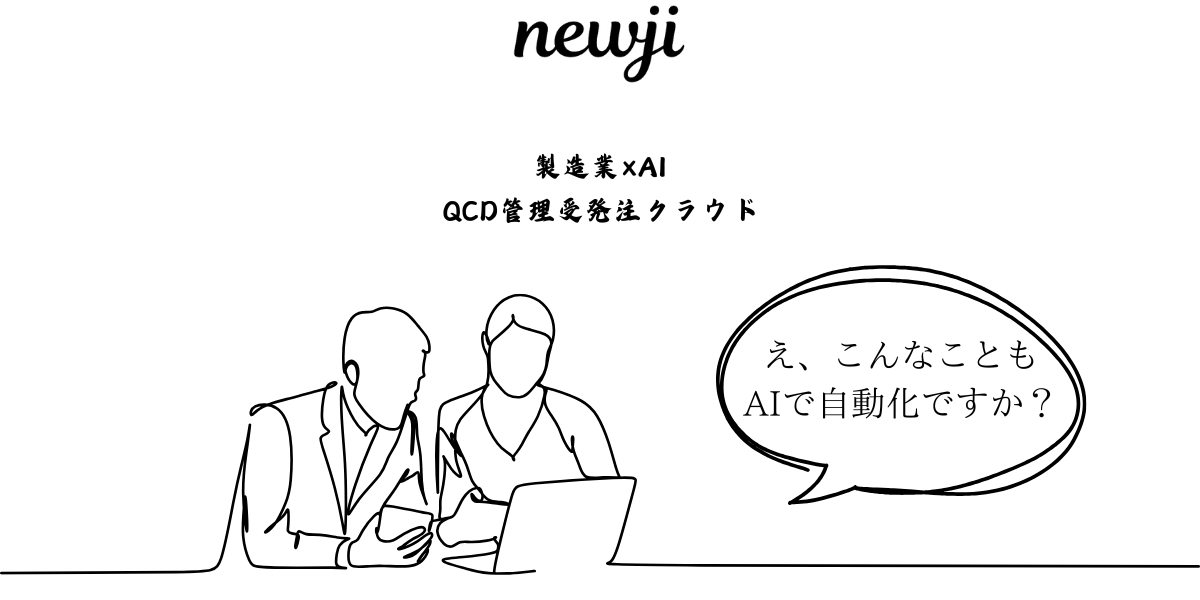
[From molding to painting] The strength of a small factory that enables one-stop small-lot prototyping
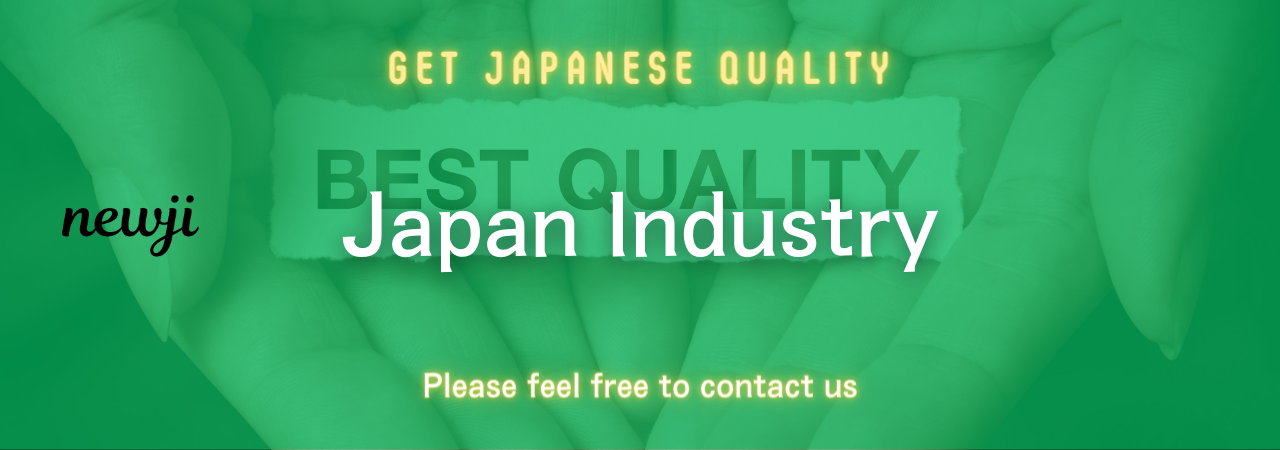
目次
Introduction to Prototyping in Small Factories
In the world of manufacturing, particularly in small factories, the ability to offer one-stop prototyping for small-lot production is a significant advantage.
These facilities have developed a unique strength by managing processes from molding to painting under one roof.
This capability not only streamlines production but also ensures quality and precision in every step.
In this article, we delve into how small factories have optimized their processes and why this approach becomes increasingly valuable in today’s fast-paced production environment.
The Initial Phase: Molding
The first critical phase in small-lot prototyping is molding.
This process involves shaping raw materials into the desired form using various techniques like injection molding, casting, or 3D printing.
Small factories are equipped with versatile machinery that allows them to create intricate designs and accurate dimensional specifications.
The flexibility of these machines enables these facilities to switch between different projects swiftly without compromising on quality.
Advantages of In-House Molding
Having the molding process in-house offers several benefits.
First, it drastically reduces the lead time, as there is no need to wait for third-party services.
Second, direct oversight ensures that any issues in design or execution can be rapidly addressed.
Lastly, it provides cost savings, as outsourcing these tasks usually incurs higher expenses.
Precision in Machining
Following the molding phase, many small factories engage in precision machining.
This step fine-tunes the molded parts to meet the necessary specifications.
Machines such as CNC mills and lathes are commonly used in this stage to achieve micro-level precision and surface finishes.
Ensuring Quality through Machining
Quality control is paramount during machining.
Factories employ skilled machinists to monitor this process closely, ensuring each component meets the exact requirements.
Continuous measurement and inspection are integral, allowing factories to minimize deviations and maintain consistent quality across all components.
The Role of Prototype Testing
Testing prototypes is an essential step before moving to production.
Small factories conduct a series of rigorous tests to identify any flaws or areas for improvement in the prototype.
This ensures that the final product not only meets the client’s expectations but also performs as intended in real-world applications.
Benefits of Extensive Prototype Testing
Thorough testing builds confidence in the product and mitigates the risk of costly recalls or revisions.
It also fosters a deeper understanding of the product’s performance, leading to further optimization and enhanced functionalities.
The feedback obtained during testing is invaluable for refining both the process and the product itself.
Finishing Touches with Painting
The painting process is often the final touch in the prototype journey.
In small factories, this is executed with great precision, using advanced painting booths that ensure uniform color distribution and texture consistency.
Customization through Painting
Painting not only serves an aesthetic purpose but can also be customized to meet specific client needs, such as special finishes or protective coatings.
Small factories often provide a range of options that allow for distinctive designs and features, adding another layer of personalization to the prototype.
The Advantages of One-Stop Prototyping
The strength of a small factory lies in its holistic approach to prototyping.
By handling all production stages internally, these facilities can offer a seamless transition from design to the final product.
Reduced Production Time
One of the most significant advantages is the reduced time to market.
With each stage being overseen by the same team, small factories can drastically cut down on lead times, ensuring faster delivery without sacrificing quality.
Consistent Quality Control
Being able to control each aspect of production allows for tighter quality control, leading to higher client satisfaction.
Continuous oversight ensures that any discrepancies are swiftly corrected, maintaining the product’s integrity throughout its development.
Flexibility and Customization
Small factories thrive on their ability to adapt and customize their processes to meet varied project needs.
They can easily adjust production runs based on client feedback or market changes, offering personalized solutions when larger operations might struggle.
Concluding Thoughts on Prototyping in Small Factories
In conclusion, the strength of small factories in handling one-stop prototyping for small-lot production is evident.
Their ability to manage molding, machining, and painting under one roof not only improves efficiency but also ensures the highest standards of quality and customization.
As markets continue to evolve and demand more personalized solutions, the role of these agile and flexible small factories will become increasingly central to innovative and timely product development.
資料ダウンロード
QCD管理受発注クラウド「newji」は、受発注部門で必要なQCD管理全てを備えた、現場特化型兼クラウド型の今世紀最高の受発注管理システムとなります。
ユーザー登録
受発注業務の効率化だけでなく、システムを導入することで、コスト削減や製品・資材のステータス可視化のほか、属人化していた受発注情報の共有化による内部不正防止や統制にも役立ちます。
NEWJI DX
製造業に特化したデジタルトランスフォーメーション(DX)の実現を目指す請負開発型のコンサルティングサービスです。AI、iPaaS、および先端の技術を駆使して、製造プロセスの効率化、業務効率化、チームワーク強化、コスト削減、品質向上を実現します。このサービスは、製造業の課題を深く理解し、それに対する最適なデジタルソリューションを提供することで、企業が持続的な成長とイノベーションを達成できるようサポートします。
製造業ニュース解説
製造業、主に購買・調達部門にお勤めの方々に向けた情報を配信しております。
新任の方やベテランの方、管理職を対象とした幅広いコンテンツをご用意しております。
お問い合わせ
コストダウンが利益に直結する術だと理解していても、なかなか前に進めることができない状況。そんな時は、newjiのコストダウン自動化機能で大きく利益貢献しよう!
(β版非公開)