- お役立ち記事
- “Functional deployment type FMEA” that ensures comprehensiveness and its application to preventing quality problems
月間76,176名の
製造業ご担当者様が閲覧しています*
*2025年3月31日現在のGoogle Analyticsのデータより
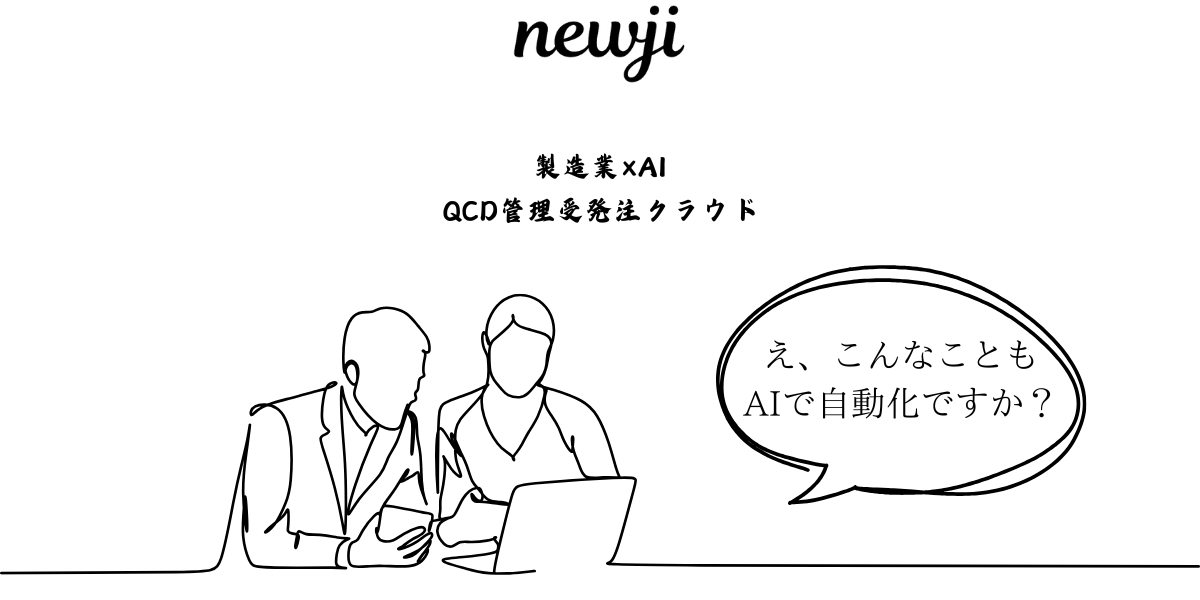
“Functional deployment type FMEA” that ensures comprehensiveness and its application to preventing quality problems
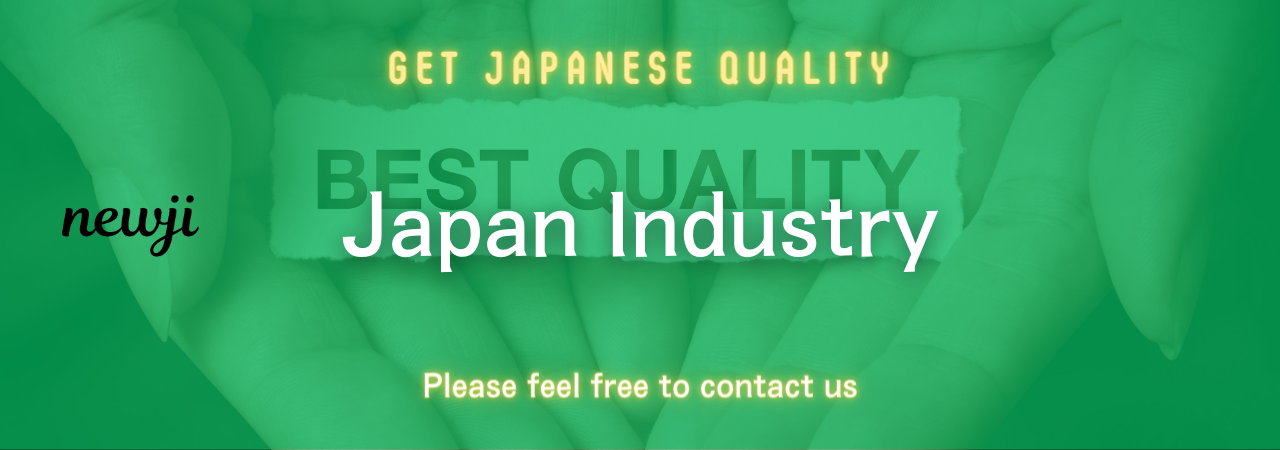
目次
Understanding Functional Deployment Type FMEA
Functional Deployment Type Failure Mode and Effects Analysis (FMEA) is an essential process in engineering and manufacturing used to anticipate and prevent potential quality issues before they arise.
By systematically evaluating components, functions, and processes for possible failure modes, organizations can ensure product quality and reliability.
The ultimate goal of Functional Deployment Type FMEA is to ensure comprehensiveness in the identification and analysis of potential failures.
This analysis aids companies in developing effective solutions that prevent problems and maintain a high standard of quality across their products.
The Importance of Functional Deployment in FMEA
Functional Deployment in FMEA refers to the methodical breakdown of processes and systems into their fundamental functions before analyzing each function for potential failures.
This systemic approach ensures that no aspect of a product or process is overlooked, thus providing a comprehensive assessment.
Functional Deployment helps in understanding the intricate relationships between different components and systems, allowing manufacturers to predict how one failure might affect another.
This, in turn, aids in identifying all possible failure modes and understanding their effects on the overall system.
Preventing failures in advance is significant because it allows organizations to save time and resources that would otherwise be spent on troubleshooting and repairs after a failure has occurred.
It also enhances customer satisfaction as the end product is more likely to meet or exceed quality expectations.
Steps in Performing Functional Deployment Type FMEA
Functional Deployment Type FMEA follows a series of methodical steps designed to ensure thoroughness in the analysis of potential failures.
Step 1: Identify and Define the Functions
The first step involves identifying and defining the individual functions within a product or process.
These functions may relate to any component, sub-system, or system.
Each function is specified so that its potential failure modes can be systematically assessed.
Step 2: Determine Potential Failure Modes
The next step is to determine potential failure modes for each of these functions.
Failure Mode refers to the way in which a particular function can fail to perform its required task.
For instance, in a braking system, a potential failure mode could be the inability to generate sufficient stopping force.
Step 3: Assess the Effects of Each Failure Mode
After identifying the potential failure modes, the next step is to assess their effects on the system or product.
This requires evaluating the impact of each failure mode on the functionality, safety, and performance of the overall system.
Step 4: Analyze the Causes
Once the failure modes and their effects are identified, the causes of these failures must be analyzed.
Causes can range from design flaws and material defects to process inconsistencies.
By understanding these causes, organizations can develop strategies to prevent such failures from occurring.
Step 5: Assign Risk Priority
Every failure mode is then assigned a risk priority number (RPN) based on its severity, occurrence, and detectability.
The aim is to prioritize the failure modes that pose the highest risk.
Those with the highest RPN require immediate attention and counteractive measures.
Step 6: Develop and Implement Solutions
The final step involves developing solutions to the high-priority failure modes identified.
These solutions may involve design modifications, material changes, process improvements, or any other corrective action that mitigates the risk.
Application of Functional Deployment Type FMEA in Preventing Quality Problems
The application of Functional Deployment Type FMEA extends beyond theoretical analysis.
It offers tangible benefits in preventing quality problems in real-world engineering and manufacturing scenarios.
Identifying Potential Quality Problems Early
By using Functional Deployment Type FMEA, organizations can identify potential quality problems early in the design and development stages.
This early identification allows companies to take corrective action before a product reaches the production stage, ensuring that only high-quality products are manufactured.
Continuous Improvement
Functional Deployment Type FMEA promotes continuous improvement by encouraging organizations to regularly assess and refine their processes.
With each cycle, companies can refine their analysis, update their risk priorities, and implement more effective solutions, thus continually improving product quality and reliability.
Reducing Costs Associated with Failures
By preventing potential failures before they occur, Functional Deployment Type FMEA helps organizations reduce costs associated with post-production troubleshooting, product recalls, and warranty claims.
This not only saves money but also preserves the brand’s reputation.
Enhancing Product Reliability and Customer Satisfaction
Through thorough analysis and prevention of failure modes, products developed using Functional Deployment Type FMEA are typically more reliable.
This reliability enhances customer satisfaction because consumers receive durable products with fewer defects.
Conclusion
Functional Deployment Type FMEA stands as a pivotal practice in the engineering and manufacturing industries, providing a structured framework for identifying and preventing potential failures.
By ensuring comprehensiveness in functional analysis, organizations can significantly enhance product quality, reduce production costs, and improve customer satisfaction.
In a world where product excellence and reliability are paramount, adopting Functional Deployment Type FMEA becomes not only beneficial but vital for success.
資料ダウンロード
QCD管理受発注クラウド「newji」は、受発注部門で必要なQCD管理全てを備えた、現場特化型兼クラウド型の今世紀最高の受発注管理システムとなります。
ユーザー登録
受発注業務の効率化だけでなく、システムを導入することで、コスト削減や製品・資材のステータス可視化のほか、属人化していた受発注情報の共有化による内部不正防止や統制にも役立ちます。
NEWJI DX
製造業に特化したデジタルトランスフォーメーション(DX)の実現を目指す請負開発型のコンサルティングサービスです。AI、iPaaS、および先端の技術を駆使して、製造プロセスの効率化、業務効率化、チームワーク強化、コスト削減、品質向上を実現します。このサービスは、製造業の課題を深く理解し、それに対する最適なデジタルソリューションを提供することで、企業が持続的な成長とイノベーションを達成できるようサポートします。
製造業ニュース解説
製造業、主に購買・調達部門にお勤めの方々に向けた情報を配信しております。
新任の方やベテランの方、管理職を対象とした幅広いコンテンツをご用意しております。
お問い合わせ
コストダウンが利益に直結する術だと理解していても、なかなか前に進めることができない状況。そんな時は、newjiのコストダウン自動化機能で大きく利益貢献しよう!
(β版非公開)