- お役立ち記事
- Fundamentals and analysis of impact stress and effective use in strength design
月間77,185名の
製造業ご担当者様が閲覧しています*
*2025年2月28日現在のGoogle Analyticsのデータより
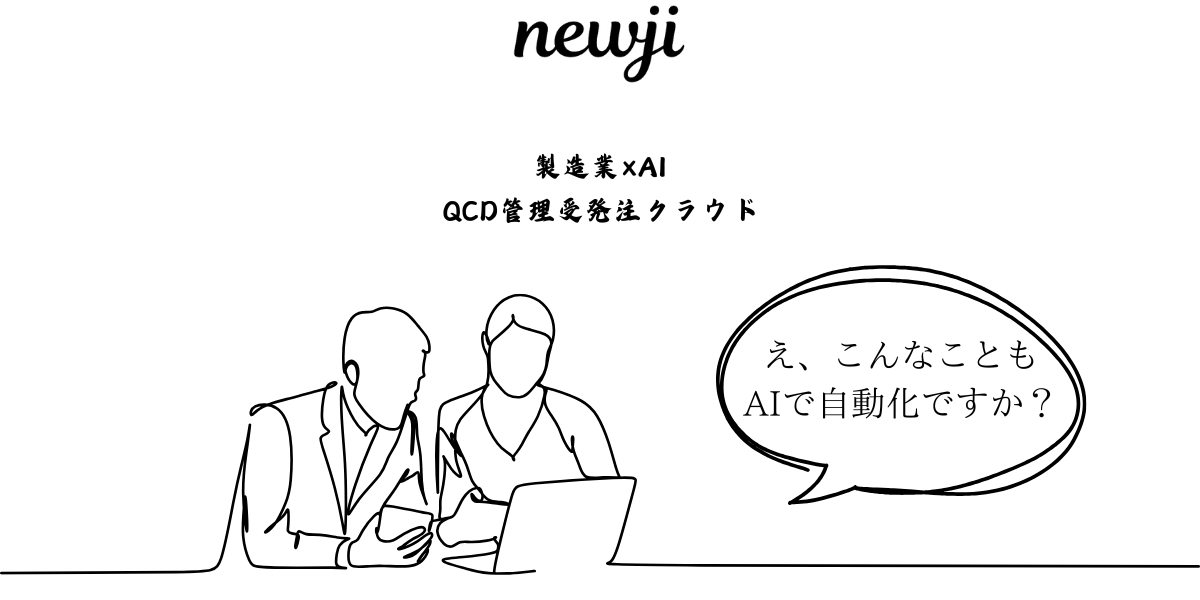
Fundamentals and analysis of impact stress and effective use in strength design
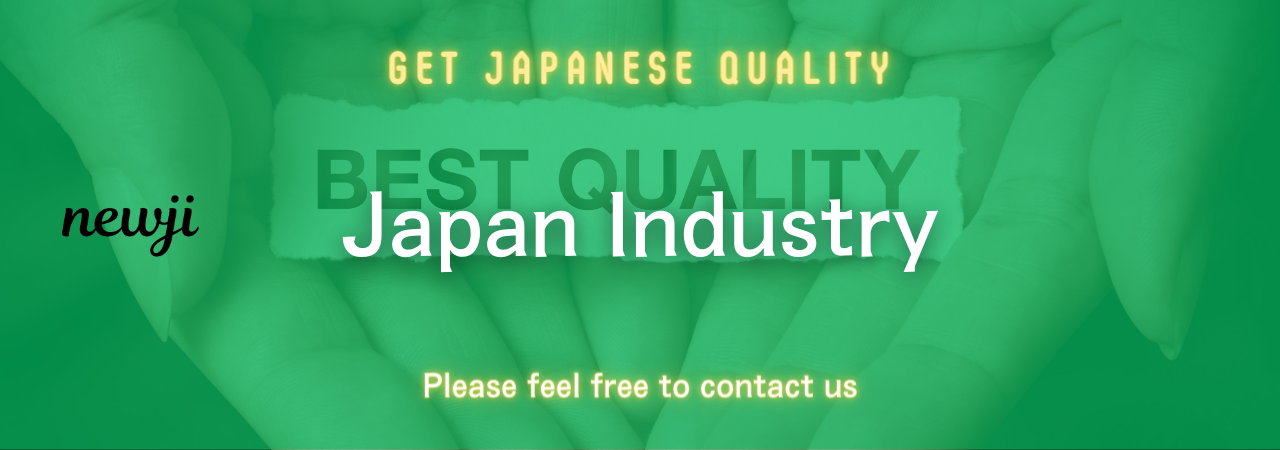
目次
Understanding Impact Stress
Impact stress is a crucial aspect of engineering and design that involves the force exerted on a material when it undergoes a sudden change in momentum.
This force results from a collision or impact, and understanding it is essential to ensuring the durability and safety of structures and materials.
When designing objects that are likely to experience impact, such as vehicles, helmets, or building materials, engineers must consider how these forces will affect the integrity of the material.
Failure to adequately account for impact stress can lead to catastrophic failures and safety hazards.
The Basics of Impact Stress
Impact stress occurs when an object strikes another object or surface.
The resulting force is distributed over the area of impact, generating stress within the material.
This stress is often much higher than the stress produced under static conditions, due to the rapid exchange of energy.
The amount of impact stress depends on various factors:
– The mass and velocity of the impacting object
– The angle of impact
– The material properties, such as strength and ductility
– The duration of impact contact
Calculating Impact Stress
To calculate impact stress, engineers utilize formulas that incorporate the object’s mass, velocity, and the material’s properties.
One common method is using the impulse-momentum theorem, which relates force, time, change in momentum, and velocity.
Working through these calculations can provide insights into how a material will behave under specific conditions.
This enables engineers to design structures that can absorb or distribute impact forces more effectively.
The Role of Material Properties
Different materials respond uniquely to impact forces.
Metals, for instance, can deform and bear stress due to their ductility, while brittle materials like glass are more likely to shatter.
Ductile vs. Brittle Materials
Ductile materials, such as certain metals, can absorb a significant amount of energy through plastic deformation.
This allows them to stretch or bend without breaking when subjected to impact stress.
On the other hand, brittle materials tend to fracture when subjected to sudden forces, as they lack the ability to deform plastically.
Understanding these material characteristics helps engineers select appropriate materials for different applications.
For impact-heavy environments, materials that can absorb energy and resist fracture are typically preferable.
Testing for Impact Stress
Various tests help determine how materials behave under impact conditions.
These tests provide valuable data for engineers and designers.
Charpy and Izod Tests
Both the Charpy and Izod tests are popular methods for evaluating a material’s toughness and ability to absorb energy during an impact.
These tests involve striking a material with a swinging pendulum and measuring the energy absorbed in breaking the specimen.
Materials that absorb more energy are generally more resistant to impact damage.
Dynamic Loading Tests
Dynamic loading tests involve subjecting materials to forces that mimic real-world conditions, such as those experienced by automotive components or construction materials during use.
These tests ensure that the materials perform as expected when exposed to varying and unpredictable stresses.
Effective Use of Impact Stress in Design
Understanding impact stress is pivotal not only for safety but also for innovative design solutions.
Incorporating impact stress analysis into design processes helps optimize materials for both performance and cost-effectiveness.
Design for Impact Resistance
When designing for impact resistance, engineers focus on minimizing stress concentration points, which can be potential failure sites.
Round corners, layered construction, and avoiding sharp edges can help distribute stress more evenly.
Additionally, using composite materials can enhance impact resistance without significantly increasing weight.
These materials combine the desirable properties of different substances, offering improved strength, durability, and resistance to impact stress.
Simulation and Modeling
With advancements in technology, simulation and modeling have become indispensable tools for predicting impact behavior.
Software tools allow engineers to simulate various impact scenarios and study the effects on materials and components.
This virtual testing approach reduces the time and cost associated with physical prototypes and testing.
By using computer-aided design (CAD) programs and finite element analysis (FEA), engineers can model the complexities of impact stress on materials.
These models provide valuable insights into potential failure modes, allowing for refinements before physical production.
Conclusion
Understanding and analyzing impact stress is fundamental in designing safe and effective products and structures.
From everyday items like car bumpers to critical infrastructure components like bridges, the principles of impact stress are applied to ensure safety and durability.
By leveraging material science, testing, and modern technology, engineers can create designs that withstand the unpredictable forces of impact while optimizing performance.
資料ダウンロード
QCD管理受発注クラウド「newji」は、受発注部門で必要なQCD管理全てを備えた、現場特化型兼クラウド型の今世紀最高の受発注管理システムとなります。
ユーザー登録
受発注業務の効率化だけでなく、システムを導入することで、コスト削減や製品・資材のステータス可視化のほか、属人化していた受発注情報の共有化による内部不正防止や統制にも役立ちます。
NEWJI DX
製造業に特化したデジタルトランスフォーメーション(DX)の実現を目指す請負開発型のコンサルティングサービスです。AI、iPaaS、および先端の技術を駆使して、製造プロセスの効率化、業務効率化、チームワーク強化、コスト削減、品質向上を実現します。このサービスは、製造業の課題を深く理解し、それに対する最適なデジタルソリューションを提供することで、企業が持続的な成長とイノベーションを達成できるようサポートします。
製造業ニュース解説
製造業、主に購買・調達部門にお勤めの方々に向けた情報を配信しております。
新任の方やベテランの方、管理職を対象とした幅広いコンテンツをご用意しております。
お問い合わせ
コストダウンが利益に直結する術だと理解していても、なかなか前に進めることができない状況。そんな時は、newjiのコストダウン自動化機能で大きく利益貢献しよう!
(β版非公開)