- お役立ち記事
- Fundamentals and Application Know-How of Hydroforming Technology
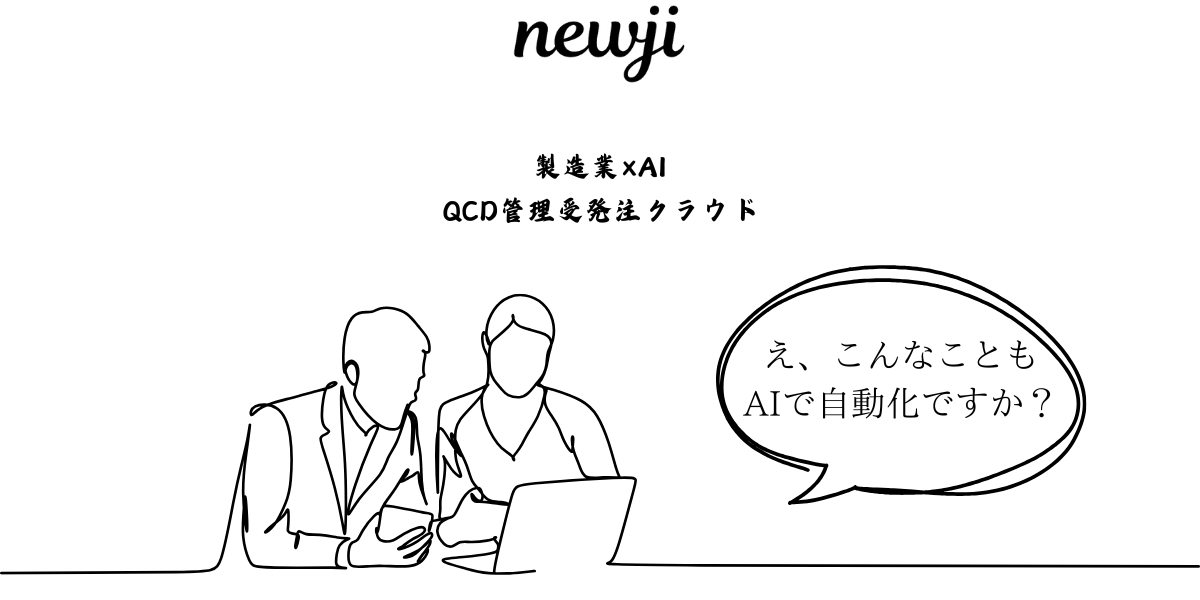
Fundamentals and Application Know-How of Hydroforming Technology
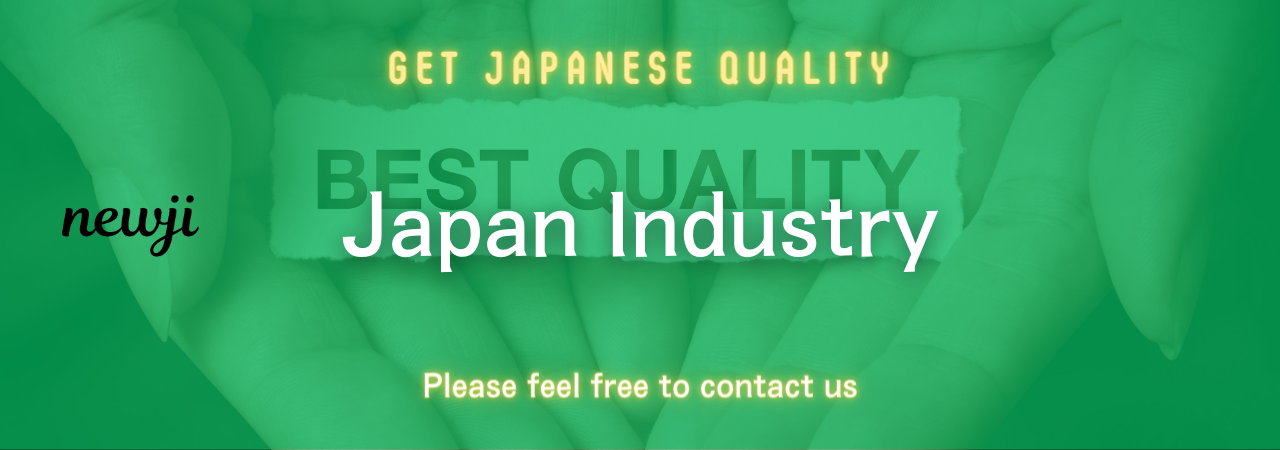
Hydroforming is a manufacturing process used to create complex shapes from malleable materials like metals and composites.
This innovative technique has revolutionized the way we mold materials by replacing traditional methods such as stamping, welding, and machining.
In this article, we will explore the fundamentals of hydroforming technology and delve into its applications, advantages, and key considerations for implementation.
目次
What is Hydroforming?
Hydroforming is a forming process where a malleable tube or sheet of metal is shaped using a high-pressure hydraulic fluid.
This technique takes advantage of the material’s plasticity, allowing it to be formed into intricate, lightweight, and structurally robust components that would be challenging to achieve using conventional methods.
With hydroforming, manufacturers can produce parts with improved strength-to-weight ratios, exceptional surface finishes, and reduced material wastage.
Types of Hydroforming
There are two primary types of hydroforming processes: sheet hydroforming and tube hydroforming.
Each process is suited to different applications and materials.
Sheet Hydroforming
In sheet hydroforming, a sheet of metal is placed over a die, and a hydraulic fluid applies pressure to the sheet, forcing it into the die’s shape.
This process is often used for creating complex, high-quality metal parts with fine surface finishes, including automotive panels, aerospace components, and appliances.
Sheet hydroforming allows for uniform material thickness and reduces the need for secondary operations such as trimming and welding.
Tube Hydroforming
Tube hydroforming, on the other hand, involves placing a tube inside a die and applying internal hydraulic pressure to expand the tube against the die’s walls.
This method is widely used for manufacturing lightweight structural components such as automotive exhaust systems, bicycle frames, and furniture.
Tube hydroforming enables the production of parts with varying cross-sectional shapes and improved mechanical properties.
Advantages of Hydroforming
Hydroforming offers several key advantages over traditional manufacturing processes, which have contributed to its widespread adoption in various industries.
Cost Efficiency
One of the primary advantages of hydroforming is its cost efficiency.
By eliminating the need for multiple tools and reducing material waste, hydroforming can significantly lower production costs.
Additionally, the process reduces the need for secondary operations like welding, which further minimizes labor and material expenses.
Improved Material Properties
Hydroformed components often exhibit superior material properties compared to those produced using conventional methods.
The high-pressure forming process enhances the material’s strength, ductility, and surface finish, leading to more durable and aesthetically pleasing parts.
This is particularly important in industries where performance and appearance are critical, such as automotive and aerospace.
Design Flexibility
The hydroforming process allows manufacturers to achieve complex shapes and geometries that would be challenging or impossible to create using traditional methods.
This design flexibility enables the production of innovative and optimized components that meet specific performance and aesthetic requirements.
Moreover, the ability to produce parts with varying material thicknesses and integrated features opens up new possibilities for product design and engineering.
Environmental Benefits
Hydroforming is an environmentally friendly manufacturing process that generates less waste compared to traditional methods.
The process’s precision allows for optimal material usage, reducing scrap and conserving raw materials.
Furthermore, hydroformed parts often require fewer secondary operations, which reduces energy consumption and emissions associated with additional processing steps.
Applications of Hydroforming
Hydroforming technology is utilized across various industries due to its ability to produce high-quality, lightweight, and cost-effective components.
Automotive Industry
In the automotive industry, hydroforming is used to manufacture components like exhaust systems, suspension parts, chassis members, and body panels.
The ability to produce lighter yet stronger parts helps improve vehicle performance, fuel efficiency, and safety.
Hydroforming also allows for the integration of multiple functions into a single component, reducing assembly complexity and costs.
Aerospace Industry
The aerospace industry benefits from hydroforming technology due to its ability to produce intricate and lightweight components with excellent structural integrity.
Hydroforming is used to manufacture parts such as wing sections, fuselage panels, and engine components.
The precision and quality of hydroformed parts meet the rigorous standards required in aerospace applications, contributing to safer and more efficient aircraft.
Medical Industry
In the medical industry, hydroforming is used to produce high-precision components for medical devices and equipment.
The process allows for the creation of complex shapes with tight tolerances, essential for devices such as surgical instruments, implants, and diagnostic equipment.
Material versatility and biocompatibility also make hydroforming an attractive option for medical applications.
Consumer Goods
Hydroforming is also employed in the production of various consumer goods, including bicycles, furniture, and appliances.
The process enables the creation of lightweight, durable, and aesthetically pleasing products that meet consumer demands for quality and design.
Hydroformed components in bicycles, for instance, contribute to improved performance and reduced weight.
Key Considerations for Hydroforming Implementation
When considering implementing hydroforming technology in a manufacturing process, several factors need to be taken into account to ensure successful integration and optimal results.
Material Selection
The choice of material is crucial to the success of the hydroforming process.
Materials must have suitable plasticity and ductility to withstand the high-pressure forming process without cracking or deforming.
Common materials used in hydroforming include aluminum, stainless steel, and various alloys.
The material’s properties, such as strength, corrosion resistance, and surface finish, should align with the application’s requirements.
Tooling and Equipment
Investing in high-quality tooling and equipment is essential for achieving precise and consistent results in hydroforming.
The die design must accurately reflect the desired part geometry and account for material flow and expansion.
Hydraulic systems should be capable of delivering the necessary pressure levels with precision and control.
Regular maintenance and calibration of tooling and equipment are critical to ensure optimal performance and longevity.
Process Control
Effective process control is vital to achieving consistent and high-quality hydroformed parts.
This involves monitoring and adjusting parameters such as fluid pressure, material feed, and die alignment throughout the forming process.
Implementing advanced control systems and quality assurance measures can help identify and address any deviations or issues promptly, ensuring consistent product quality.
Conclusion
Hydroforming technology has transformed manufacturing by enabling the production of complex, lightweight, and high-quality components across various industries.
With its cost efficiency, improved material properties, design flexibility, and environmental benefits, hydroforming presents a compelling alternative to traditional manufacturing methods.
By understanding the fundamentals, advantages, and applications of hydroforming, manufacturers can leverage this innovative technology to achieve superior product performance and efficiency.
As industry demands continue to evolve, hydroforming will undoubtedly play a crucial role in shaping the future of manufacturing.
資料ダウンロード
QCD調達購買管理クラウド「newji」は、調達購買部門で必要なQCD管理全てを備えた、現場特化型兼クラウド型の今世紀最高の購買管理システムとなります。
ユーザー登録
調達購買業務の効率化だけでなく、システムを導入することで、コスト削減や製品・資材のステータス可視化のほか、属人化していた購買情報の共有化による内部不正防止や統制にも役立ちます。
NEWJI DX
製造業に特化したデジタルトランスフォーメーション(DX)の実現を目指す請負開発型のコンサルティングサービスです。AI、iPaaS、および先端の技術を駆使して、製造プロセスの効率化、業務効率化、チームワーク強化、コスト削減、品質向上を実現します。このサービスは、製造業の課題を深く理解し、それに対する最適なデジタルソリューションを提供することで、企業が持続的な成長とイノベーションを達成できるようサポートします。
オンライン講座
製造業、主に購買・調達部門にお勤めの方々に向けた情報を配信しております。
新任の方やベテランの方、管理職を対象とした幅広いコンテンツをご用意しております。
お問い合わせ
コストダウンが利益に直結する術だと理解していても、なかなか前に進めることができない状況。そんな時は、newjiのコストダウン自動化機能で大きく利益貢献しよう!
(Β版非公開)