- お役立ち記事
- Fundamentals and Applications of Compounding in Manufacturing
Fundamentals and Applications of Compounding in Manufacturing
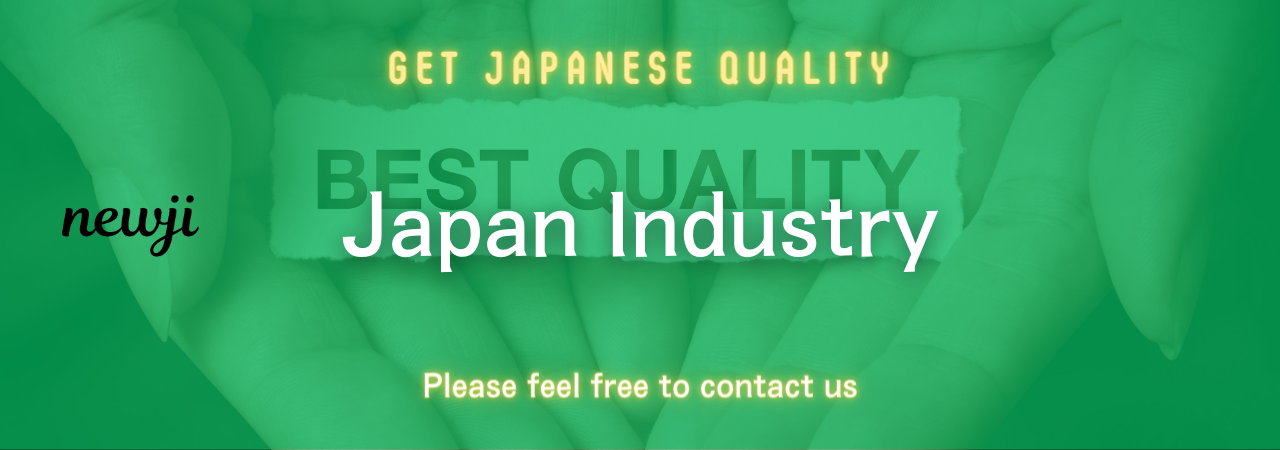
In the world of manufacturing, the term “compounding” often arises as a critical process. But what exactly does it mean, and how does it apply across different industries? Let’s dive into the fundamentals of compounding in manufacturing, exploring its various applications and importance.
目次
Understanding the Basics of Compounding
Compounding in a manufacturing context refers to the process of blending or combining multiple substances to create a new material with specific desired properties. This can involve a range of ingredients, including polymers, resins, fillers, additives, and pigments. The goal is to produce a material that meets precise engineering requirements for strength, flexibility, durability, or other characteristics.
The Importance of Compounding
Compounding is vital for several reasons:
1. Customization: Manufacturers can tailor materials to meet exact specifications, enhancing performance for particular applications.
2. Cost-Efficiency: Optimizing material properties can reduce the need for multiple separate components, thereby cutting costs.
3. Performance: Custom compounds often outperform off-the-shelf materials in terms of durability, functionality, and safety.
4. Innovation: Compounding enables the creation of unique materials that can lead to advancements in various fields, from automotive to medical devices.
The Compounding Process
The process of compounding typically involves three main steps:
1. Selection of Ingredients: Choosing the right polymers, fillers, and additives based on the required properties of the final product.
2. Mixing and Blending: Combining the ingredients in a controlled environment to ensure uniform distribution and interaction at the molecular level.
3. Extrusion or Molding: Forming the compounded material into the desired shape using extrusion, molding, or other techniques.
Common Methods of Compounding
Several techniques can be employed during the compounding process, each suited to different materials and applications:
1. Melt Compounding: This involves heating a polymer until it melts and then mixing it with other ingredients. The mixture is then cooled and solidified into the final product.
2. Solution Compounding: In this method, the materials are dissolved in a solvent, mixed thoroughly, and then the solvent is evaporated to leave a homogeneous material.
3. Dry Blending: This technique involves mixing powders without using a solvent or heat, relying on mechanical agitation to achieve uniformity.
Applications of Compounding in Manufacturing
Compounding finds applications across a wide range of industries, each leveraging the process to meet their specific material needs.
1. Automotive Industry
The automotive industry extensively uses compounded materials to improve vehicle performance and safety. For instance, thermoplastic elastomers (TPE) are compounded to produce car interiors and under-the-hood components. These materials provide excellent heat resistance, flexibility, and durability.
2. Construction Sector
In construction, compounded materials like polyvinyl chloride (PVC) are essential for pipes, windows, and flooring. These materials offer robustness, ease of installation, and long-term durability, making them ideal for infrastructure projects.
3. Electronics and Electrical
Compounded polymers are crucial in the electronics industry for making casings, connectors, and insulating materials. Flame-retardant compounds ensure safety and compliance with stringent industry standards.
4. Medical Devices
The medical field relies on compounded materials for items like tubing, connectors, and even implants. Medical-grade polymers must be biocompatible, ensuring they do not adversely react with the human body.
Tailoring Compounded Materials for Specific Needs
The beauty of compounding lies in its versatility. By adjusting the types and amounts of ingredients, manufacturers can create materials tailored for specific applications. This level of customization is achieved through careful consideration of:
1. Mechanical Properties: The strength, elasticity, and toughness of materials can be fine-tuned.
2. Thermal Properties: Adjusting the melting point and heat resistance for applications exposed to varying temperatures.
3. Chemical Resistance: Ensuring materials can withstand exposure to harsh chemicals without degrading.
4. Aesthetic Qualities: Adding pigments and stabilizers to achieve the desired appearance and colorfastness.
Quality Control in Compounding
Ensuring the consistency and quality of compounded materials is crucial. Manufacturers employ rigorous quality control measures, including:
1. Material Testing: Regular testing for tensile strength, impact resistance, and other physical properties.
2. Process Monitoring: Continuous monitoring of the compounding process to maintain ingredient proportions and mixing conditions.
3. Batch Verification: Conducting batch-by-batch checks to confirm uniformity and compliance with specifications.
The Future of Compounding
The advancements in materials science are paving the way for even more sophisticated and high-performance compounded materials. Innovations such as nanocomposites, which incorporate nanoparticles into polymers, are unlocking new possibilities in strength, lightness, and functionality. Additionally, sustainable compounding practices using bio-based and recycled materials are gaining traction, aligning with global environmental goals.
Compounding in manufacturing is a foundational process that enables the creation of tailored, high-performance materials across a multitude of industries. From enhancing vehicle safety to improving medical devices, compounding provides the flexibility and precision needed to meet ever-evolving technological and regulatory demands. As material science continues to advance, the potential for compounding to drive innovation and efficiency in manufacturing remains boundless.
資料ダウンロード
QCD調達購買管理クラウド「newji」は、調達購買部門で必要なQCD管理全てを備えた、現場特化型兼クラウド型の今世紀最高の購買管理システムとなります。
ユーザー登録
調達購買業務の効率化だけでなく、システムを導入することで、コスト削減や製品・資材のステータス可視化のほか、属人化していた購買情報の共有化による内部不正防止や統制にも役立ちます。
NEWJI DX
製造業に特化したデジタルトランスフォーメーション(DX)の実現を目指す請負開発型のコンサルティングサービスです。AI、iPaaS、および先端の技術を駆使して、製造プロセスの効率化、業務効率化、チームワーク強化、コスト削減、品質向上を実現します。このサービスは、製造業の課題を深く理解し、それに対する最適なデジタルソリューションを提供することで、企業が持続的な成長とイノベーションを達成できるようサポートします。
オンライン講座
製造業、主に購買・調達部門にお勤めの方々に向けた情報を配信しております。
新任の方やベテランの方、管理職を対象とした幅広いコンテンツをご用意しております。
お問い合わせ
コストダウンが利益に直結する術だと理解していても、なかなか前に進めることができない状況。そんな時は、newjiのコストダウン自動化機能で大きく利益貢献しよう!
(Β版非公開)