- お役立ち記事
- Fundamentals and Applications of Extrusion Molding: A Practical Guide for Town Factories
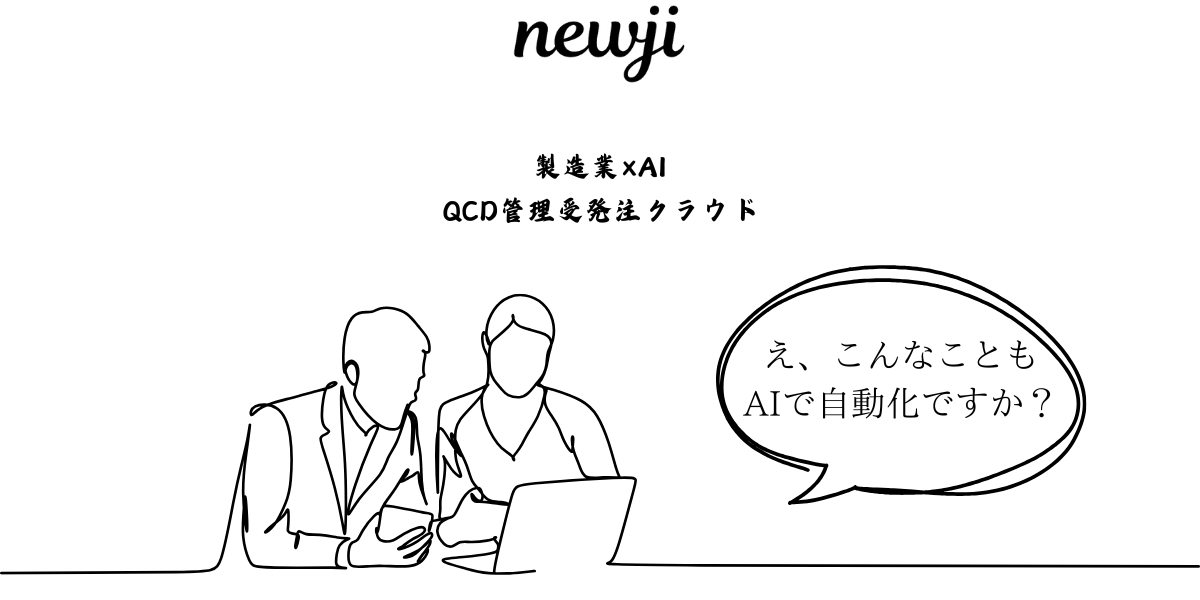
Fundamentals and Applications of Extrusion Molding: A Practical Guide for Town Factories
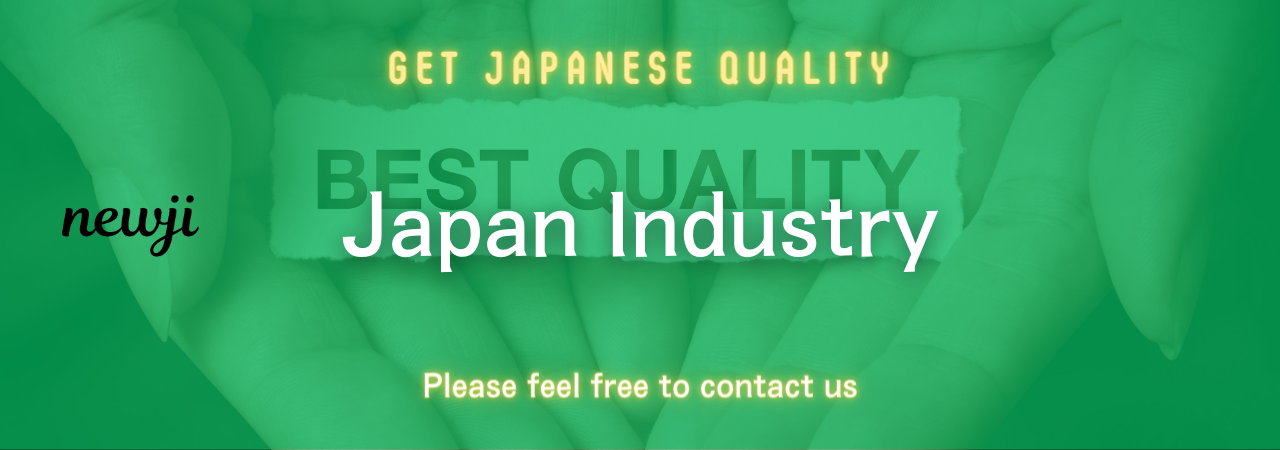
Extrusion molding is a popular manufacturing process known for its versatility and efficiency.
It is particularly beneficial for small-town factories aiming to produce a wide range of products.
This guide delves into the fundamentals and applications of extrusion molding, offering practical insights for small-scale manufacturers.
目次
What is Extrusion Molding?
Extrusion molding is a continuous process where raw material, often in the form of pellets or granules, is melted and forced through a die to create long shapes of a fixed cross-section.
These can be cut into desired lengths or further processed to meet specific needs.
The process is frequently used to produce items like pipes, tubes, sheets, and profiles.
Key Components of Extrusion Molding
Extruder
The extruder is the heart of the operation.
It consists of a cylindrical barrel and a screw that rotates to push the material through the die.
The screw’s design is crucial as it influences the melting and mixing of the material.
Die
The die shapes the molten material into the desired form.
A variety of die types is available, including those for creating hollow, solid, and sheet products.
The shape and size of the die openings directly determine the shape and size of the final product.
Cooling System
After extrusion, the hot material needs to be cooled to harden into its final shape.
Cooling is typically achieved using air or water, depending on the materials and end-use requirements.
Cutter
For applications requiring specific lengths, a cutter is used to slice the extruded product.
The cutter can be a simple blade or a more complex automated system that coordinates with the extrusion speed.
Materials Used in Extrusion Molding
A wide range of materials can be extruded, including polymers, metals, and ceramics.
Each material has its specific properties and applications.
Polymers
Polymers, especially thermoplastics, are the most commonly used materials in extrusion molding.
Examples include polyethylene, polypropylene, PVC, and nylon.
These materials are known for their flexibility, durability, and ease of extrusion.
Metals
Metal extrusion involves pushing metal billets through a die.
Aluminum, copper, and steel are common choices for metal extrusion.
This process is used to create strong, durable components for automotive, aerospace, and construction industries.
Ceramics
Ceramic extrusion is often used to produce intricate profiles and shapes for applications such as electrical insulators and kiln furniture.
Materials like alumina and zirconia are typical choices.
Types of Extrusion Molding
Extrusion molding can be categorized into several types based on the material and application.
Profile Extrusion
Profile extrusion is used to create products with a uniform cross-section, such as window frames, plastic tubing, and edging.
The die’s design determines the shape of the final product.
Sheet Extrusion
In sheet extrusion, the molten material is forced through a flat die, producing large sheets.
These sheets can be used in packaging, automotive parts, and construction materials.
Blown Film Extrusion
Blown film extrusion involves extruding a tube of molten plastic and then inflating it to form a thin film.
This process is commonly used in making plastic bags and packaging films.
Co-Extrusion
Co-extrusion allows for the combination of multiple materials into a single extruded piece.
This is useful for products requiring different properties on their inner and outer surfaces, such as multilayered packaging films.
Benefits of Extrusion Molding
Extrusion molding offers numerous advantages, making it a preferred method for many manufacturers.
Efficiency
One of the key benefits of extrusion molding is its efficiency.
The continuous operation allows for high-speed production with minimal downtime.
Cost-Effectiveness
Extrusion molding is generally cost-effective, especially for large-scale production.
The initial setup cost is offset by the low per-unit production cost.
Versatility
The process is highly versatile, capable of producing a wide range of shapes and sizes.
This flexibility allows manufacturers to meet diverse market demands.
Material Conservation
Extrusion molding is known for its material efficiency, as it generates minimal waste.
Excess material can often be recycled and reintroduced into the extrusion process.
Applications of Extrusion Molding in Town Factories
Extrusion molding has numerous applications, making it ideal for small-town factories looking to diversify their product lines.
Construction Materials
Extruded products such as pipes, tubing, and window frames are essential components in the construction industry.
Town factories can capitalize on local construction projects by supplying these materials.
Packaging
Extruded sheets and films are commonly used in the packaging industry.
Small factories can produce packaging materials used by local food, beverage, and retail companies.
Automotive Components
Extrusion molding is used to manufacture various automotive components, including seals, hoses, and trim.
This presents an opportunity for town factories to supply parts to local automotive repair shops or manufacturers.
Consumer Goods
Products like garden hoses, kitchen utensils, and toys can be made using extrusion molding.
These consumer goods present a broad market for town factories to explore.
Challenges and Solutions
While extrusion molding offers many benefits, it also presents several challenges.
Understanding these challenges and their solutions can help small factories optimize their operations.
Material Selection
Choosing the right material is crucial for successful extrusion molding.
Different materials have specific melting points, viscosities, and properties.
Collaborating with material suppliers can help town factories make informed decisions.
Quality Control
Maintaining consistent product quality is essential.
Implementing stringent quality control measures, including regular inspections and testing, ensures the final product meets the required standards.
Equipment Maintenance
Regular maintenance of extrusion equipment is vital for smooth operations.
Following a preventive maintenance schedule helps minimize downtime and extend equipment lifespan.
Skilled Workforce
Recruiting and training skilled workers is crucial for efficient extrusion molding operations.
Investing in employee training programs ensures the team is knowledgeable and capable of handling complex tasks.
In conclusion, extrusion molding is a powerful and versatile manufacturing process.
By understanding its fundamentals and applications, town factories can leverage this technique to expand their product offerings and thrive in the competitive market.
With careful planning and execution, even small-scale manufacturers can achieve significant success using extrusion molding.
資料ダウンロード
QCD調達購買管理クラウド「newji」は、調達購買部門で必要なQCD管理全てを備えた、現場特化型兼クラウド型の今世紀最高の購買管理システムとなります。
ユーザー登録
調達購買業務の効率化だけでなく、システムを導入することで、コスト削減や製品・資材のステータス可視化のほか、属人化していた購買情報の共有化による内部不正防止や統制にも役立ちます。
NEWJI DX
製造業に特化したデジタルトランスフォーメーション(DX)の実現を目指す請負開発型のコンサルティングサービスです。AI、iPaaS、および先端の技術を駆使して、製造プロセスの効率化、業務効率化、チームワーク強化、コスト削減、品質向上を実現します。このサービスは、製造業の課題を深く理解し、それに対する最適なデジタルソリューションを提供することで、企業が持続的な成長とイノベーションを達成できるようサポートします。
オンライン講座
製造業、主に購買・調達部門にお勤めの方々に向けた情報を配信しております。
新任の方やベテランの方、管理職を対象とした幅広いコンテンツをご用意しております。
お問い合わせ
コストダウンが利益に直結する術だと理解していても、なかなか前に進めることができない状況。そんな時は、newjiのコストダウン自動化機能で大きく利益貢献しよう!
(Β版非公開)