- お役立ち記事
- Fundamentals and applications of plastic welding and points to keep in mind
月間76,176名の
製造業ご担当者様が閲覧しています*
*2025年3月31日現在のGoogle Analyticsのデータより
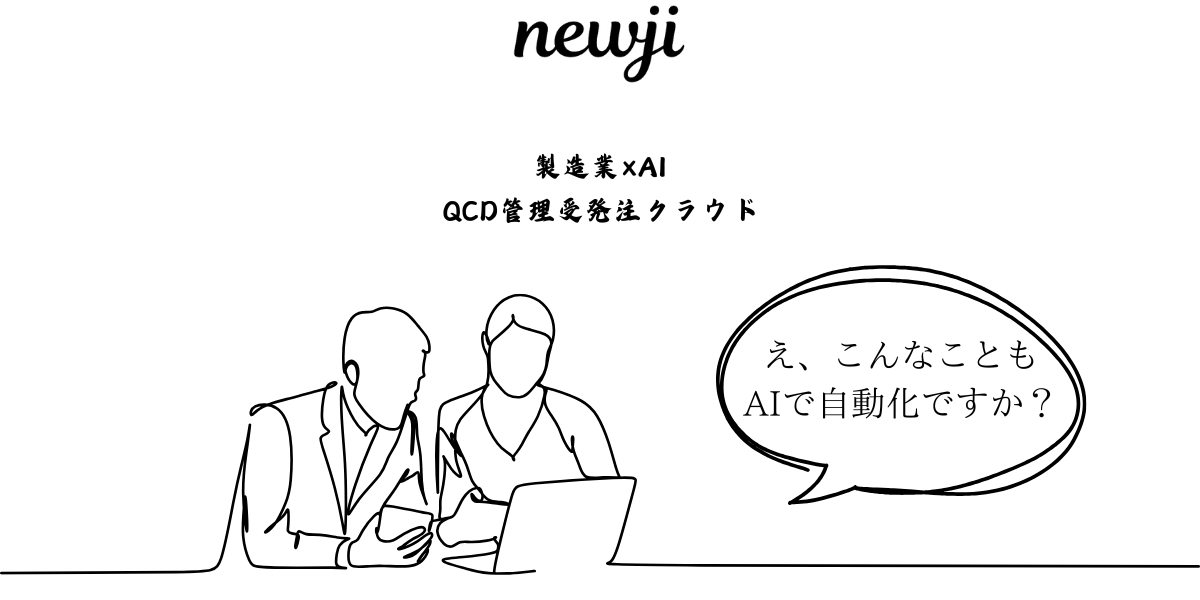
Fundamentals and applications of plastic welding and points to keep in mind
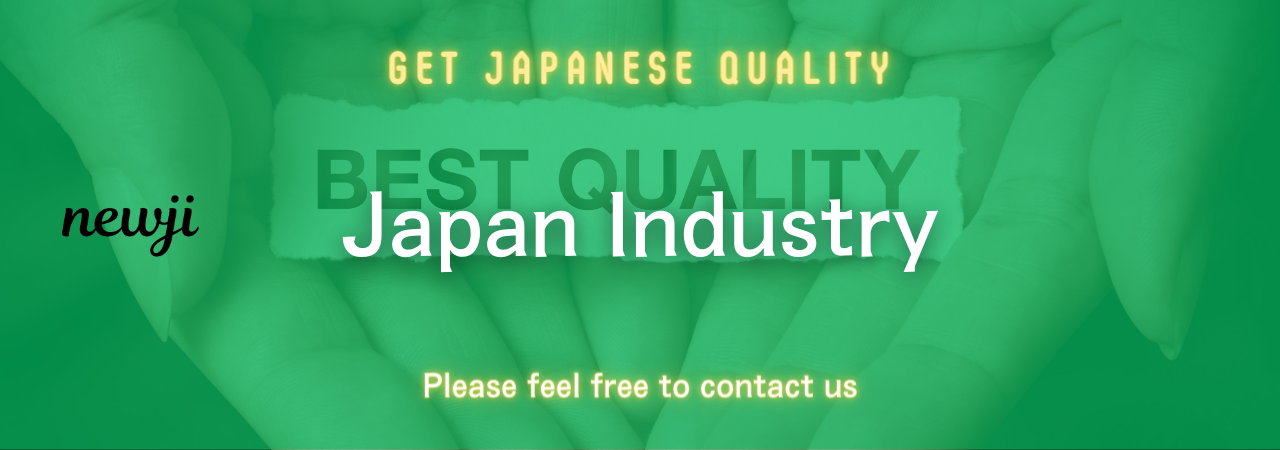
目次
What is Plastic Welding?
Plastic welding is a process of joining two plastic components together using heat, pressure or a combination of both.
This technique resembles metal welding but is specialized for plastic materials.
Plastic welding is widely used in manufacturing and repairing plastic components, ensuring durability and strong bonds without using adhesives.
The method is particularly useful for thermoplastics as their chemical structure allows them to be melted and re-solidified.
Understanding plastic welding involves knowing the different techniques used, the materials that can be welded, and the applications where it is most beneficial.
Techniques in Plastic Welding
Hot Air Welding
Hot air welding, also known as hot gas welding, uses a jet of hot air to melt the plastic surfaces that need to be joined.
Once the plastic reaches its melting point, it fuses with a plastic welding rod of the same material, sealing the join as the material cools.
This method is often used for repairing tanks, liners, and pipes.
Ultrasonic Welding
Ultrasonic welding uses high-frequency ultrasonic acoustic vibrations to create localized heat, allowing the plastics to fuse together without melting the entire surface.
The process is extremely fast, often taking seconds, and is commonly used in the automotive, medical, and consumer electronics industries.
Spin Welding
Spin welding involves rotating one of the plastic parts while pressing it against another stationary part.
Friction generates heat, which melts the surfaces together.
Once desired friction is achieved, the rotation stops and the materials solidify into a strong bond.
This method is typically used for circular welds but is limited to joining round or cylindrical components.
Vibration Welding
Similar to spin welding, vibration welding employs friction to generate heat.
However, instead of rotational movement, the parts are held together and moved laterally with high-frequency vibrations.
When the materials reach their melting point, the vibrations cease and the plastic solidifies, creating the weld.
This technique is advantageous in joining complex or irregular shapes that aren’t suitable for spin welding.
Applications of Plastic Welding
Plastic welding is essential across numerous industries, including automotive, aerospace, medical, and packaging.
In the automotive industry, plastic welding is employed to manufacture dashboards, airflow vents, and fluid reservoirs.
In aerospace, strong joints are crucial for parts that experience considerable stress during operations.
In the medical industry, plastic welding is used to create sterile equipment, such as tubing and fluid bags, while ensuring a reliable bond that prevents leaks and contamination.
Plastic welding in packaging is highly beneficial for creating airtight seals, preserving the integrity of the products inside.
By ensuring that joints are seamless and secure, plastic welding helps enhance product longevity and consumer safety.
Types of Plastics Suitable for Welding
Various types of plastics can be welded, but thermoplastics are best suited due to their ability to be repeatedly melted and solidified.
Some common thermoplastics used in plastic welding include:
Polyethylene (PE)
Polyethylene is highly weldable and often used in products like tank liners, pipes, and geomembranes.
Polypropylene (PP)
Polypropylene’s resilience to chemicals makes it ideal for automotive parts and appliances.
Polyvinyl Chloride (PVC)
Both rigid and flexible PVCs are suitable for welding and find applications in piping, flooring, and medical devices.
Acrylonitrile Butadiene Styrene (ABS)
ABS offers toughness and ease of welding, making it popular in consumer electronics and automotive parts.
Points to Keep in Mind
While plastic welding presents many advantages, there are essential points to consider:
Material Compatibility
Ensure that the materials being welded have compatible melt temperatures and chemical properties to achieve strong welds.
Mixing different plastics can result in weak joints and structural failure.
Safety Precautions
Use appropriate personal protective equipment (PPE), including gloves and eye protection, to safeguard against high temperatures and potential emissions from heated plastics.
Proper ventilation is also critical to avoid inhalation of fumes that might be generated during welding.
Control of Parameters
Managing consistent heat, pressure, and timing is crucial for producing high-quality welds.
This requires proper calibration of welding equipment and understanding material-specific requirements.
Testing and Inspection
Following any welding operation, inspect welds for defects such as voids, inclusions, or weak spots.
Non-destructive testing techniques, like ultrasonic testing, can be employed to ensure the integrity of critical joints without causing damage.
Conclusion
Plastic welding is a versatile technique essential for creating strong, durable joints in various industries.
Understanding the fundamentals of different welding methods, material compatibility, and safety considerations ensures effective application and long-lasting results.
Whether for automotive parts, medical equipment, or consumer goods, plastic welding continues to be an invaluable process that supports modern manufacturing and innovation.
資料ダウンロード
QCD管理受発注クラウド「newji」は、受発注部門で必要なQCD管理全てを備えた、現場特化型兼クラウド型の今世紀最高の受発注管理システムとなります。
ユーザー登録
受発注業務の効率化だけでなく、システムを導入することで、コスト削減や製品・資材のステータス可視化のほか、属人化していた受発注情報の共有化による内部不正防止や統制にも役立ちます。
NEWJI DX
製造業に特化したデジタルトランスフォーメーション(DX)の実現を目指す請負開発型のコンサルティングサービスです。AI、iPaaS、および先端の技術を駆使して、製造プロセスの効率化、業務効率化、チームワーク強化、コスト削減、品質向上を実現します。このサービスは、製造業の課題を深く理解し、それに対する最適なデジタルソリューションを提供することで、企業が持続的な成長とイノベーションを達成できるようサポートします。
製造業ニュース解説
製造業、主に購買・調達部門にお勤めの方々に向けた情報を配信しております。
新任の方やベテランの方、管理職を対象とした幅広いコンテンツをご用意しております。
お問い合わせ
コストダウンが利益に直結する術だと理解していても、なかなか前に進めることができない状況。そんな時は、newjiのコストダウン自動化機能で大きく利益貢献しよう!
(β版非公開)