- お役立ち記事
- Fundamentals and design examples of vector control position sensorless control of permanent magnet synchronous motors
月間76,176名の
製造業ご担当者様が閲覧しています*
*2025年3月31日現在のGoogle Analyticsのデータより
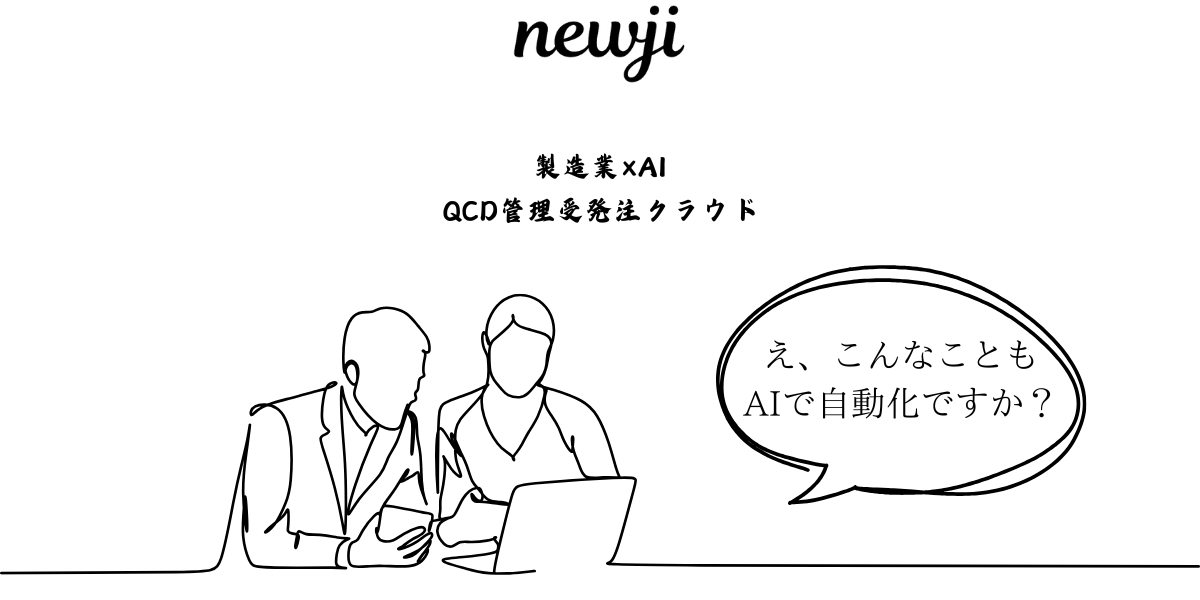
Fundamentals and design examples of vector control position sensorless control of permanent magnet synchronous motors
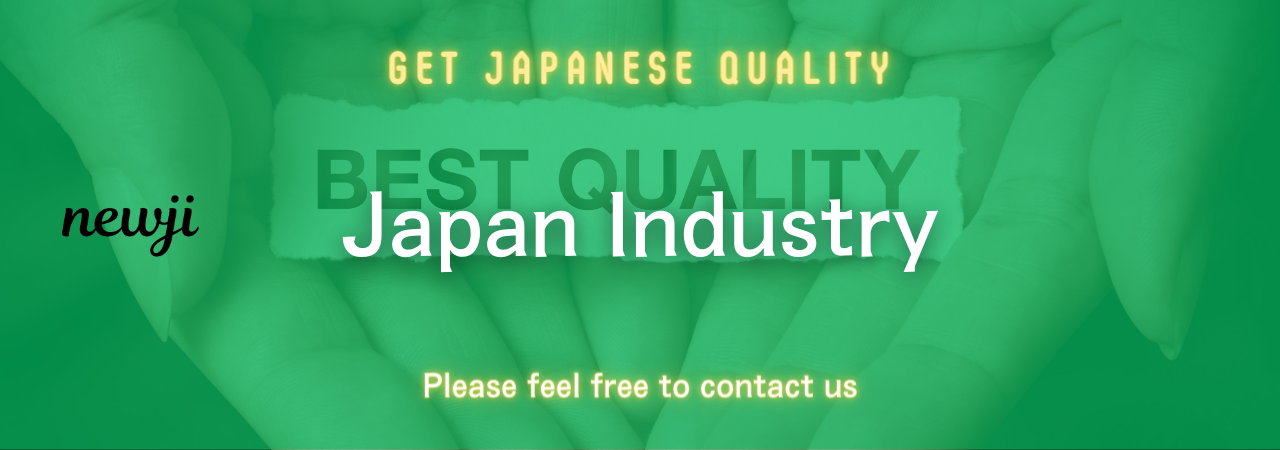
目次
Introduction to Vector Control for Permanent Magnet Synchronous Motors
Permanent Magnet Synchronous Motors (PMSMs) are a popular choice in various applications due to their high efficiency, excellent power-to-weight ratio, and robust performance characteristics.
Vector control, an advanced technique to control these motors efficiently, depends on the precise control of the torque and magnetic flux within the motor.
Although position sensors like encoders or resolvers have traditionally been used, they introduce complexity and additional cost.
Position sensorless control, on the other hand, offers a more streamlined and cost-effective solution.
Understanding Vector Control
Before we delve into the sensorless aspect, it’s essential to understand vector control itself.
Vector control, also known as Field-Oriented Control (FOC), is a methodology used for the precise control of the three-phase current supplied to a motor.
By transforming the motor currents to a rotating reference frame, vector control decouples the torque and magnetic flux, enabling independent control over each component.
This control method requires transformation from the three-phase stationary reference frame (abc) to a two-axis rotating reference frame (dq).
The transformation simplifies the dynamic equations of a PMSM, making it easier to manipulate and control.
With the help of this method, the torque performance of the motor can be optimized, enhancing its efficiency and responsiveness.
Key Components of Vector Control
– **Clarke and Park Transformations:** These mathematical transformations convert the stationary reference frame to a rotating one.
– **Proportional-Integral (PI) Controllers:** Used to regulate the d-axis and q-axis currents independently.
– **Pulse Width Modulation (PWM):** Controls the inverter that supplies power to the motor, ensuring the applied voltage matches the calculated requirement.
Position Sensorless Control
Position sensorless control of PMSMs eliminates the need for physical sensors, reducing cost and enhancing system reliability.
This approach estimates rotor position and speed based on the motor’s electrical parameters and operational conditions.
Methods of Sensorless Control
Several techniques can be employed for position sensorless control, each with its unique advantages and challenges.
– **Model Reference Adaptive System (MRAS):** This method utilizes a reference model based on the motor’s equations to estimate the rotor position. By comparing the actual motor response with the reference, it adapts to varying conditions.
– **Extended Kalman Filter (EKF):** An advanced estimation algorithm that considers both measured and estimated states. EKF is particularly useful in noisy environments but can be computationally demanding.
– **Back Electromotive Force (EMF) Method:** Utilizes the relationship between rotor speed and the induced voltage. Simple and effective at higher speeds, but less accurate at low speeds.
Benefits of Sensorless Control
– **Reduced System Complexity:** Eliminates the need for additional wiring and sensors.
– **Lower Costs:** Decreases the overall expenses of the motor control system.
– **Increased Reliability:** With fewer components, the likelihood of mechanical or electrical failure is reduced.
Design Examples of Vector Control Position Sensorless Control
Implementing position sensorless control in a PMSM requires careful consideration of the motor’s characteristics and the application requirements.
Designing such a system involves several critical strategies and techniques.
Example 1: Industrial Robot Arm
In applications like industrial robot arms, precision and reliability are paramount.
The use of vector control with sensorless operation can enhance the performance by providing accurate torque control without additional hardware.
Here, EKF can be used to maintain precise position estimation even with varying load conditions and disturbances.
Example 2: Electric Vehicles
Electric vehicles benefit tremendously from the reduced size and complexity afforded by sensorless control.
In this case, back EMF methods offer a robust solution for high-speed applications where precise position feedback is required.
Paired with a well-tuned PI controller, it ensures efficient torque delivery, optimizing battery life and vehicle performance.
Example 3: Home Appliances
For home appliance motors, minimizing cost is crucial while maintaining performance.
The MRAS method could be an ideal choice due to its balance between computational efficiency and accuracy.
It can handle varying operating speeds effectively, which is often necessary in variable-speed appliances like washing machines.
Challenges and Considerations
Despite the numerous advantages, sensorless control is not without challenges.
Estimating rotor position at very low speeds can be difficult, and additional strategies like injecting high-frequency signals might be needed.
Careful tuning of the control algorithms is required to ensure stability and performance across various operating conditions.
Conclusion
The fundamentals and design of vector control position sensorless control of PMSMs highlight its importance in modern motor applications.
Whether it’s reducing system costs or enhancing motor performance in precision-demanding applications, sensorless control offers a compelling solution.
Future innovations will likely refine these techniques, making them more accessible and effective across an even broader range of applications.
資料ダウンロード
QCD管理受発注クラウド「newji」は、受発注部門で必要なQCD管理全てを備えた、現場特化型兼クラウド型の今世紀最高の受発注管理システムとなります。
ユーザー登録
受発注業務の効率化だけでなく、システムを導入することで、コスト削減や製品・資材のステータス可視化のほか、属人化していた受発注情報の共有化による内部不正防止や統制にも役立ちます。
NEWJI DX
製造業に特化したデジタルトランスフォーメーション(DX)の実現を目指す請負開発型のコンサルティングサービスです。AI、iPaaS、および先端の技術を駆使して、製造プロセスの効率化、業務効率化、チームワーク強化、コスト削減、品質向上を実現します。このサービスは、製造業の課題を深く理解し、それに対する最適なデジタルソリューションを提供することで、企業が持続的な成長とイノベーションを達成できるようサポートします。
製造業ニュース解説
製造業、主に購買・調達部門にお勤めの方々に向けた情報を配信しております。
新任の方やベテランの方、管理職を対象とした幅広いコンテンツをご用意しております。
お問い合わせ
コストダウンが利益に直結する術だと理解していても、なかなか前に進めることができない状況。そんな時は、newjiのコストダウン自動化機能で大きく利益貢献しよう!
(β版非公開)