- お役立ち記事
- Fundamentals and Effective Implementation of Manufacturing Line Balancing
月間77,185名の
製造業ご担当者様が閲覧しています*
*2025年2月28日現在のGoogle Analyticsのデータより
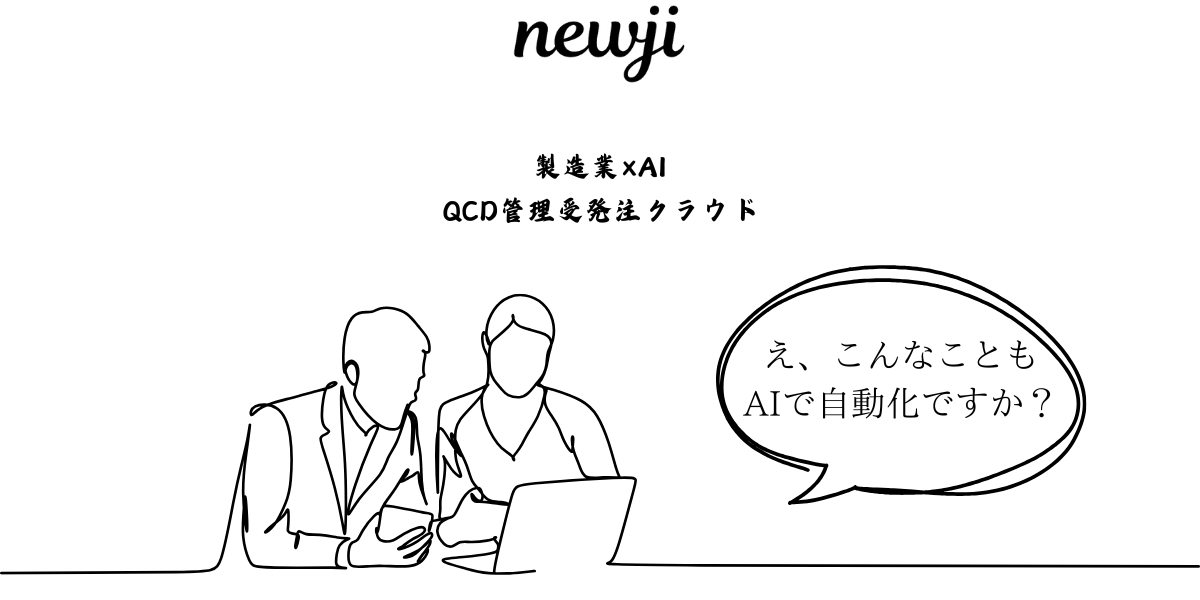
Fundamentals and Effective Implementation of Manufacturing Line Balancing
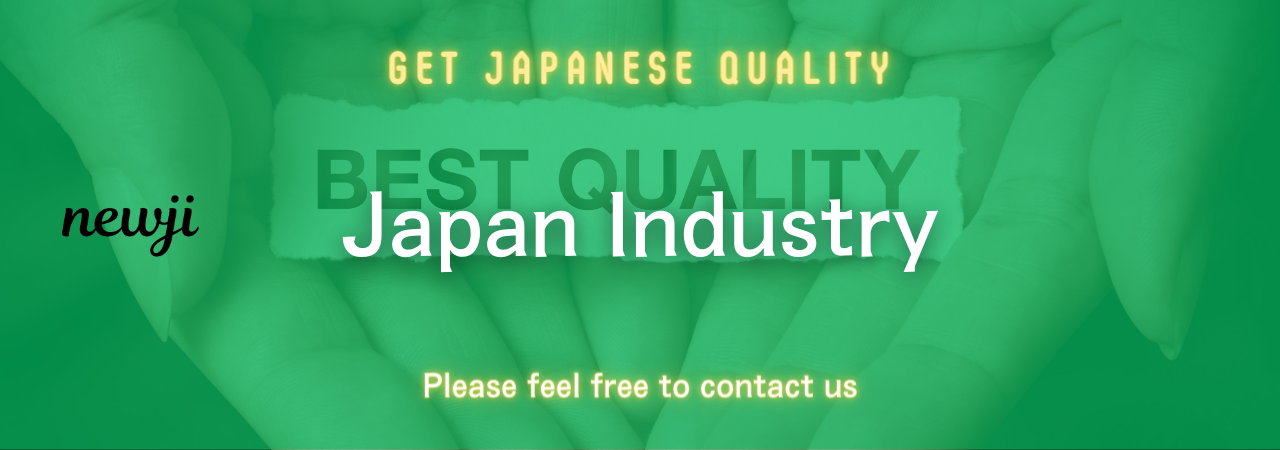
目次
Understanding Manufacturing Line Balancing
Manufacturing line balancing (MLB) is a critical aspect of production efficiency and optimization.
It involves organizing different processes in a production line to achieve maximum efficiency by minimizing idle time and ensuring every workstation is fully utilized.
This ensures smooth workflow, reduces bottlenecks, and can significantly contribute to lowering production costs and increasing output.
Understanding MLB’s fundamentals is essential for anyone involved in manufacturing or production management.
Key Concepts of Line Balancing
1. Task Allocation
In line balancing, tasks are allocated to various workstations along the production line.
It’s important to distribute tasks effectively so that each station can complete its job within the same time frame.
This time frame is often referred to as the cycle time.
Ideally, each workstation should have a balanced workload to avoid delays.
2. Cycle Time
Cycle time is the time taken to complete one unit of production.
It is determined by the pace needed to meet customer demand.
Cycle time is crucial for setting the rhythm of the entire production line.
3. Takt Time
Takt time is the rate at which a finished product needs to be completed to meet customer demand.
It is calculated by dividing the total available production time by the customer demand.
Matching the cycle time with takt time is crucial for achieving balance in the manufacturing process.
4. Workstation Utilization
Workstation utilization refers to the extent to which each workstation is used.
High utilization means that a workstation is active most of the time, whereas low utilization might indicate inefficiencies.
Effective line balancing maximizes utilization through careful planning and task allocation.
Steps for Implementing Effective Line Balancing
1. Identify and List Tasks
The first step in line balancing is to identify and list all tasks required to complete a unit of production.
This involves breaking down the manufacturing process into smaller, manageable tasks.
2. Determine Task Time
Once all tasks are identified, the time required to complete each task should be measured accurately.
This helps in identifying which tasks might be time-consuming and how to distribute them effectively across workstations.
3. Establish Sequence of Tasks
Determine the sequence in which tasks should be performed.
Some tasks must be completed before others can start.
Creating a sequence ensures a logical and efficient flow of materials and products through the production line.
4. Create Workstations
Divide the production line into different workstations, assigning tasks to each station based on the measured task times and sequence.
Aim to distribute tasks so that each workstation can complete its assigned tasks within the cycle time.
5. Balance the Line
Lastly, adjust the allocation of tasks to ensure that all workstations are balanced.
This may involve redistributing tasks or adding additional resources to certain workstations.
The goal is to have each workstation complete its tasks with minimal wait time and without causing delays in subsequent stations.
Challenges in Manufacturing Line Balancing
1. Variability in Task Times
One of the main challenges in MLB is the variability in task times.
Even with careful planning, there can be differences in how quickly different workers complete the same task.
This can disrupt the balance of the production line.
2. Bottlenecks
Bottlenecks occur when one workstation takes longer than others, causing delays in the entire production process.
Identifying and addressing bottlenecks is essential to maintain a balanced production line.
3. Machine Downtime
Unexpected machine failures or maintenance can halt production at specific workstations.
Regular maintenance and having backup machinery can help mitigate the impact of machine downtime on line balance.
4. Variability in Demand
Fluctuations in customer demand can affect takt time, requiring frequent adjustments to the production line balance.
Maintaining flexibility and being able to quickly adapt to changes in demand is crucial.
Benefits of Effective Line Balancing
1. Increased Efficiency
Effective line balancing ensures that each workstation operates at optimal efficiency, reducing idle time and wasted resources.
This leads to a smoother and faster production process.
2. Reduced Costs
By minimizing delays and reducing bottlenecks, manufacturing costs can be lowered.
Efficient use of labor and machinery reduces the need for overtime and lowers maintenance costs due to consistent operation.
3. Improved Product Quality
A balanced production line can lead to more consistent product quality.
With streamlined processes and well-utilized resources, there is less likelihood of errors or defects, resulting in higher quality finished products.
4. Better Employee Morale
Employees working in a well-balanced production line are likely to experience less stress and frustration.
Balanced workloads create a more pleasant working environment, leading to improved morale and productivity.
Tools and Techniques for Line Balancing
1. Line Balancing Software
Many software solutions are available to help manage and optimize line balancing.
These tools can analyze production data, sequence tasks, and suggest adjustments to maintain balance.
2. Simulation Models
Simulation models can be used to visualize and test different line balancing scenarios without disrupting actual production.
This allows for experimentation and finding the most efficient configuration.
3. Lean Manufacturing Techniques
Lean manufacturing principles, such as Just-in-Time (JIT) and Kaizen, are instrumental in achieving line balance.
These techniques focus on continuous improvement and waste reduction, which are essential for effective line balancing.
Conclusion
Manufacturing line balancing is a vital component of efficient production management.
By understanding key concepts such as task allocation, cycle time, and workstation utilization, and by following a methodical implementation process, manufacturers can achieve a balanced production line that meets demand efficiently and cost-effectively.
Despite challenges like task time variability and machine downtime, the benefits of increased efficiency, reduced costs, improved product quality, and better employee morale make line balancing an essential practice for any manufacturing operation.
資料ダウンロード
QCD管理受発注クラウド「newji」は、受発注部門で必要なQCD管理全てを備えた、現場特化型兼クラウド型の今世紀最高の受発注管理システムとなります。
ユーザー登録
受発注業務の効率化だけでなく、システムを導入することで、コスト削減や製品・資材のステータス可視化のほか、属人化していた受発注情報の共有化による内部不正防止や統制にも役立ちます。
NEWJI DX
製造業に特化したデジタルトランスフォーメーション(DX)の実現を目指す請負開発型のコンサルティングサービスです。AI、iPaaS、および先端の技術を駆使して、製造プロセスの効率化、業務効率化、チームワーク強化、コスト削減、品質向上を実現します。このサービスは、製造業の課題を深く理解し、それに対する最適なデジタルソリューションを提供することで、企業が持続的な成長とイノベーションを達成できるようサポートします。
製造業ニュース解説
製造業、主に購買・調達部門にお勤めの方々に向けた情報を配信しております。
新任の方やベテランの方、管理職を対象とした幅広いコンテンツをご用意しております。
お問い合わせ
コストダウンが利益に直結する術だと理解していても、なかなか前に進めることができない状況。そんな時は、newjiのコストダウン自動化機能で大きく利益貢献しよう!
(β版非公開)